Damn! Car in for #6 cyl scoring. Which way to go?
#76
Former Vendor

The issue with the steel cylinder is dissimilar expansion characteristics. You no longer have an all aluminum engine.I've recently seen an increase in the engines that we are seeing sent to us that have been previously built with steel cylinders, and are seeing issues from dissimilar metal corrosion. Once these engines are fitted with steel cylinders, the block is compromised, and can never be fitted with LN Nickies cylinders in the future.
All of my engines utilize billet aluminum LN Engineering Nickies cylinders, with Nikisil plating.
All builders have different thoughts on this. Some are monetarily driven, and others aren't willing to accept compromise for any amount of money.
All of my engines utilize billet aluminum LN Engineering Nickies cylinders, with Nikisil plating.
All builders have different thoughts on this. Some are monetarily driven, and others aren't willing to accept compromise for any amount of money.
#77
Nordschleife Master
Join Date: Mar 2003
Location: Destin, Nashville, In a 458 Challenge
Posts: 5,128
Received 904 Likes
on
532 Posts

Seems like Porsche has always payed games by holding back and cutting costs/corners on the NAs to keep the GTs and turbos marketable at the price differences. Until my very recent purchase of a 997.2 C4S, I have always purchased turbos and GTXs and throughout the years observed those with the NAs experiencing issues, some serious, while mine were bullet proof and accumulating miles, trouble free miles . . .
10-15 years ago, I built 2 NA 3.6 engines out to 3.8s and built them like they should have been from the factory. The NAs came alive and candidly, were more exciting to drive than my new daily driver turbos at the time. Porsche won't do that because they cannot charge their huge premiums for turbos/GTs if they make the NAs they way they should be made.
#78

Haven't bothered to confirm the statement from Dwain that Porsche is building the new twin turbo motor with pressed in cromoly bores. Very similar to how he does his conversion. Let's assume for sake of argument it's true. I'm curious what your take is on the idea Porsche has gone to this method of dissimilar material? Maybe the design of the new case is substantially different rendering dissimilar material meaningless?
I'm in the information gathering phase of my rebuild and really hoping to make the best informed decision I can regarding the method I choose. Appreciate all the insight.
I'm in the information gathering phase of my rebuild and really hoping to make the best informed decision I can regarding the method I choose. Appreciate all the insight.
The issue with the steel cylinder is dissimilar expansion characteristics. You no longer have an all aluminum engine.I've recently seen an increase in the engines that we are seeing sent to us that have been previously built with steel cylinders, and are seeing issues from dissimilar metal corrosion. Once these engines are fitted with steel cylinders, the block is compromised, and can never be fitted with LN Nickies cylinders in the future.
All of my engines utilize billet aluminum LN Engineering Nickies cylinders, with Nikisil plating.
All builders have different thoughts on this. Some are monetarily driven, and others aren't willing to accept compromise for any amount of money.
All of my engines utilize billet aluminum LN Engineering Nickies cylinders, with Nikisil plating.
All builders have different thoughts on this. Some are monetarily driven, and others aren't willing to accept compromise for any amount of money.
#79

We have been prominent in Europe for repairing M96/7 engines with bore issues (first "D" chunking then bore scoring) using a similar solution to Jake Raby (an aerospace alloy Nikasil plated cylinder) with well over 2000 fitted reliably - but have also come across several engines previously fitted with ferrous dry liners that have failed - so his post is both relevant and I can confirm his experiences.
The main problem we have found is with the deck height slipping (due to poor machining accuracy of the step location and/or incorrect fitting).
Several businesses were persuaded to move to iron dry liners to save a few pounds in cost but then had to pay for the engines to be rebuilt again properly and came back to our supply over here in the UK.
However it is well established that fitting a tube inside a tube is not as stiff or strong as the same overall inside and external diameter tube in one homogeneous tube.
We have found that when the ferrous liner is thin it often rotates when the differential expansion makes it become loose or sinks in the cylinder - whereas we have never had any problem fitting alloy into alloy. If the ferrous liner is thicker it results in the remaining alloy sleeve holding it being too thin and allowing the pressure from the piston loading to push the ferrous cylinder in the thrust direction until it stretches the alloy bore and becomes lose again.
In all cases it takes a little while for ferrous liners to move and cause a problem so often exceeds the warranty the building company may have applied - so I would always recommend using an alloy Nikasil liner or cylinder and not a ferrous one for long life reliability.
The very reliable cylinders in the GT and turbo variants are very similar to ours - being alloy Nikasil plated supported by a precision machined top hat section that fits inside a precision machined recess in the top of the cylinder block and converts the open deck M96/7 construction to a closed deck design - like the GT3 and Turbo - bullet proof but a little more expensive to produce and create.
We usually see iron liners over here but have also seen steel dry ones (which despite not being located at the top in a machined recess do seem better but like iron liners have to run with greater cold clearances and sometimes give rise to smoking and oil consumption).
The original 2.5, 2.7 and 3.2 Boxster versions had thicker cylinder tubes cast into the open deck design and less piston force and were acceptably reliable. The 996 3.4 used the same casting but bored out an additional 3mm making the cylinder wall thinner while the piston forces on it increased - leading to ovality and "D" chunking.
We think a change in the Lokasil specification adding more silicon made the later 3.4, 3.6 and 3.8 engines a bit stronger but they were not made with thicker cylinder walls so with increased piston forces they also migrate oval and sometimes crack or "D" chunk.
Because we machine away all of the original upper cylinder (to enable us to fit a thicker ribbed wet liner) we have had no problems retrofitting our alloy "cylinders" (as they should be more properly named not "liners") to engines previously fitted with ferrous liners that have failed.
You can see why in either of our videos accessed via www.hartech.org Porsche specialists UK
Baz
The main problem we have found is with the deck height slipping (due to poor machining accuracy of the step location and/or incorrect fitting).
Several businesses were persuaded to move to iron dry liners to save a few pounds in cost but then had to pay for the engines to be rebuilt again properly and came back to our supply over here in the UK.
However it is well established that fitting a tube inside a tube is not as stiff or strong as the same overall inside and external diameter tube in one homogeneous tube.
We have found that when the ferrous liner is thin it often rotates when the differential expansion makes it become loose or sinks in the cylinder - whereas we have never had any problem fitting alloy into alloy. If the ferrous liner is thicker it results in the remaining alloy sleeve holding it being too thin and allowing the pressure from the piston loading to push the ferrous cylinder in the thrust direction until it stretches the alloy bore and becomes lose again.
In all cases it takes a little while for ferrous liners to move and cause a problem so often exceeds the warranty the building company may have applied - so I would always recommend using an alloy Nikasil liner or cylinder and not a ferrous one for long life reliability.
The very reliable cylinders in the GT and turbo variants are very similar to ours - being alloy Nikasil plated supported by a precision machined top hat section that fits inside a precision machined recess in the top of the cylinder block and converts the open deck M96/7 construction to a closed deck design - like the GT3 and Turbo - bullet proof but a little more expensive to produce and create.
We usually see iron liners over here but have also seen steel dry ones (which despite not being located at the top in a machined recess do seem better but like iron liners have to run with greater cold clearances and sometimes give rise to smoking and oil consumption).
The original 2.5, 2.7 and 3.2 Boxster versions had thicker cylinder tubes cast into the open deck design and less piston force and were acceptably reliable. The 996 3.4 used the same casting but bored out an additional 3mm making the cylinder wall thinner while the piston forces on it increased - leading to ovality and "D" chunking.
We think a change in the Lokasil specification adding more silicon made the later 3.4, 3.6 and 3.8 engines a bit stronger but they were not made with thicker cylinder walls so with increased piston forces they also migrate oval and sometimes crack or "D" chunk.
Because we machine away all of the original upper cylinder (to enable us to fit a thicker ribbed wet liner) we have had no problems retrofitting our alloy "cylinders" (as they should be more properly named not "liners") to engines previously fitted with ferrous liners that have failed.
You can see why in either of our videos accessed via www.hartech.org Porsche specialists UK
Baz
Last edited by bazhart; 01-12-2017 at 06:42 AM. Reason: spelling mistake
#80

Good info however the Vision solution I'm referring to cannot be described as a "liner" and neither are the many motors Porsche has produced using some form of steel as a "stand alone" cylinder as you point out below (italics). Big difference between a thin liner and stand alone bore. Vision creates a "closed deck" solution just as you describe and yes is more expensive to produce. I suppose this is why Porsche did not produce the M/96 - M/97 motors this way in the first place. Take a closer look at the photos In my previous post of the before and after case half and you'll see the first third of bore is completely machined out of the case. The new cylinder is then pressed into place with an oring at it's base just the same as the GT3 cup motors produced by Porsche.
As I've said I'm still in the info gathering phase of my rebuild plan with a goal of first learning all the viable solutions available. I have no idea which solution I'll use at this point. To that end I appreciate the info you've posted.
The very reliable cylinders in the GT and turbo variants are very similar to ours - being alloy Nikasil plated supported by a precision machined top hat section that fits inside a precision machined recess in the top of the cylinder block and converts the open deck M96/7 construction to a closed deck design - like the GT3 and Turbo - bullet proof but a little more expensive to produce and create.
As I've said I'm still in the info gathering phase of my rebuild plan with a goal of first learning all the viable solutions available. I have no idea which solution I'll use at this point. To that end I appreciate the info you've posted.
The very reliable cylinders in the GT and turbo variants are very similar to ours - being alloy Nikasil plated supported by a precision machined top hat section that fits inside a precision machined recess in the top of the cylinder block and converts the open deck M96/7 construction to a closed deck design - like the GT3 and Turbo - bullet proof but a little more expensive to produce and create.
We have been prominent in Europe for repairing M96/7 engines with bore issues (first "D" chunking then bore scoring) using a similar solution to Jake Raby (an aerospace alloy Nikasil plated cylinder) with well over 2000 fitted reliably - but have also come across several engines previously fitted with ferrous dry liners that have failed - so his post is both relevant and I can confirm his experiences.
The main problem we have found is with the deck height slipping (due to poor machining accuracy of the step location and/or incorrect fitting).
Several businesses were persuaded to move to iron dry liners to save a few pounds in cost but then had to pay for the engines to be rebuilt again properly and came back to our supply over here in the UK.
However it is well established that fitting a tube inside a tube is not as stiff or strong as the same overall inside and external diameter tube in one homogeneous tube.
We have found that when the ferrous liner is thin it often rotates when the differential expansion makes it become loose or sinks in the cylinder - whereas we have never had any problem fitting alloy into alloy. If the ferrous liner is thicker it results in the remaining alloy sleeve holding it being too thin and allowing the pressure from the piston loading to push the ferrous cylinder in the thrust direction until it stretches the alloy bore and becomes lose again.
In all cases it takes a little while for ferrous liners to move and cause a problem so often exceeds the warranty the building company may have applied - so I would always recommend using an alloy Nikasil liner or cylinder and not a ferrous one for long life reliability.
The very reliable cylinders in the GT and turbo variants are very similar to ours - being alloy Nikasil plated supported by a precision machined top hat section that fits inside a precision machined recess in the top of the cylinder block and converts the open deck M96/7 construction to a closed deck design - like the GT3 and Turbo - bullet proof but a little more expensive to produce and create.
We usually see iron liners over here but have also seen steel dry ones (which despite not being located at the top in a machined recess do seem better but like iron liners have to run with greater cold clearances and sometimes give rise to smoking and oil consumption).
The original 2.5, 2.7 and 3.2 Boxster versions had thicker cylinder tubes cast into the open deck design and less piston force and were acceptably reliable. The 996 3.4 used the same casting but bored out an additional 3mm making the cylinder wall thinner while the piston forces on it increased - leading to ovality and "D" chunking.
We think a change in the Lokasil specification adding more silicon made the later 3.4, 3.6 and 3.8 engines a bit stronger but they were not made with thicker cylinder walls so with increased piston forces they also migrate oval and sometimes crack or "D" chunk.
Because we machine away all of the original upper cylinder (to enable us to fit a thicker ribbed wet liner) we have had no problems retrofitting our alloy "cylinders" (as they should be more properly named not "liners") to engines previously fitted with ferrous liners that have failed.
You can see why in either of our videos accessed via www.hartech.org Porsche specialists UK
Baz
The main problem we have found is with the deck height slipping (due to poor machining accuracy of the step location and/or incorrect fitting).
Several businesses were persuaded to move to iron dry liners to save a few pounds in cost but then had to pay for the engines to be rebuilt again properly and came back to our supply over here in the UK.
However it is well established that fitting a tube inside a tube is not as stiff or strong as the same overall inside and external diameter tube in one homogeneous tube.
We have found that when the ferrous liner is thin it often rotates when the differential expansion makes it become loose or sinks in the cylinder - whereas we have never had any problem fitting alloy into alloy. If the ferrous liner is thicker it results in the remaining alloy sleeve holding it being too thin and allowing the pressure from the piston loading to push the ferrous cylinder in the thrust direction until it stretches the alloy bore and becomes lose again.
In all cases it takes a little while for ferrous liners to move and cause a problem so often exceeds the warranty the building company may have applied - so I would always recommend using an alloy Nikasil liner or cylinder and not a ferrous one for long life reliability.
The very reliable cylinders in the GT and turbo variants are very similar to ours - being alloy Nikasil plated supported by a precision machined top hat section that fits inside a precision machined recess in the top of the cylinder block and converts the open deck M96/7 construction to a closed deck design - like the GT3 and Turbo - bullet proof but a little more expensive to produce and create.
We usually see iron liners over here but have also seen steel dry ones (which despite not being located at the top in a machined recess do seem better but like iron liners have to run with greater cold clearances and sometimes give rise to smoking and oil consumption).
The original 2.5, 2.7 and 3.2 Boxster versions had thicker cylinder tubes cast into the open deck design and less piston force and were acceptably reliable. The 996 3.4 used the same casting but bored out an additional 3mm making the cylinder wall thinner while the piston forces on it increased - leading to ovality and "D" chunking.
We think a change in the Lokasil specification adding more silicon made the later 3.4, 3.6 and 3.8 engines a bit stronger but they were not made with thicker cylinder walls so with increased piston forces they also migrate oval and sometimes crack or "D" chunk.
Because we machine away all of the original upper cylinder (to enable us to fit a thicker ribbed wet liner) we have had no problems retrofitting our alloy "cylinders" (as they should be more properly named not "liners") to engines previously fitted with ferrous liners that have failed.
You can see why in either of our videos accessed via www.hartech.org Porsche specialists UK
Baz
#81
Rennlist Member

Fast, Good or Cheap. Pick two.
The only shops who don't use our processes is because they want it done quick and cheap.
No one has the experience we have. We do an average of 125 engines a year.
We won't re-sleeve any block previously sleeved by other shops. Just keep that in mind when you have to rebuild the engine again.
The only shops who don't use our processes is because they want it done quick and cheap.
No one has the experience we have. We do an average of 125 engines a year.
We won't re-sleeve any block previously sleeved by other shops. Just keep that in mind when you have to rebuild the engine again.
The following users liked this post:
jlert (11-04-2022)
#82
Rennlist Member

We have been prominent in Europe for repairing M96/7 engines with bore issues (first "D" chunking then bore scoring) using a similar solution to Jake Raby (an aerospace alloy Nikasil plated cylinder) with well over 2000 fitted reliably - but have also come across several engines previously fitted with ferrous dry liners that have failed - so his post is both relevant and I can confirm his experiences.
The main problem we have found is with the deck height slipping (due to poor machining accuracy of the step location and/or incorrect fitting).
Several businesses were persuaded to move to iron dry liners to save a few pounds in cost but then had to pay for the engines to be rebuilt again properly and came back to our supply over here in the UK.
However it is well established that fitting a tube inside a tube is not as stiff or strong as the same overall inside and external diameter tube in one homogeneous tube.
We have found that when the ferrous liner is thin it often rotates when the differential expansion makes it become loose or sinks in the cylinder - whereas we have never had any problem fitting alloy into alloy. If the ferrous liner is thicker it results in the remaining alloy sleeve holding it being too thin and allowing the pressure from the piston loading to push the ferrous cylinder in the thrust direction until it stretches the alloy bore and becomes lose again.
In all cases it takes a little while for ferrous liners to move and cause a problem so often exceeds the warranty the building company may have applied - so I would always recommend using an alloy Nikasil liner or cylinder and not a ferrous one for long life reliability.
The very reliable cylinders in the GT and turbo variants are very similar to ours - being alloy Nikasil plated supported by a precision machined top hat section that fits inside a precision machined recess in the top of the cylinder block and converts the open deck M96/7 construction to a closed deck design - like the GT3 and Turbo - bullet proof but a little more expensive to produce and create.
We usually see iron liners over here but have also seen steel dry ones (which despite not being located at the top in a machined recess do seem better but like iron liners have to run with greater cold clearances and sometimes give rise to smoking and oil consumption).
The original 2.5, 2.7 and 3.2 Boxster versions had thicker cylinder tubes cast into the open deck design and less piston force and were acceptably reliable. The 996 3.4 used the same casting but bored out an additional 3mm making the cylinder wall thinner while the piston forces on it increased - leading to ovality and "D" chunking.
We think a change in the Lokasil specification adding more silicon made the later 3.4, 3.6 and 3.8 engines a bit stronger but they were not made with thicker cylinder walls so with increased piston forces they also migrate oval and sometimes crack or "D" chunk.
Because we machine away all of the original upper cylinder (to enable us to fit a thicker ribbed wet liner) we have had no problems retrofitting our alloy "cylinders" (as they should be more properly named not "liners") to engines previously fitted with ferrous liners that have failed.
You can see why in either of our videos accessed via www.hartech.org Porsche specialists UK
Baz
The main problem we have found is with the deck height slipping (due to poor machining accuracy of the step location and/or incorrect fitting).
Several businesses were persuaded to move to iron dry liners to save a few pounds in cost but then had to pay for the engines to be rebuilt again properly and came back to our supply over here in the UK.
However it is well established that fitting a tube inside a tube is not as stiff or strong as the same overall inside and external diameter tube in one homogeneous tube.
We have found that when the ferrous liner is thin it often rotates when the differential expansion makes it become loose or sinks in the cylinder - whereas we have never had any problem fitting alloy into alloy. If the ferrous liner is thicker it results in the remaining alloy sleeve holding it being too thin and allowing the pressure from the piston loading to push the ferrous cylinder in the thrust direction until it stretches the alloy bore and becomes lose again.
In all cases it takes a little while for ferrous liners to move and cause a problem so often exceeds the warranty the building company may have applied - so I would always recommend using an alloy Nikasil liner or cylinder and not a ferrous one for long life reliability.
The very reliable cylinders in the GT and turbo variants are very similar to ours - being alloy Nikasil plated supported by a precision machined top hat section that fits inside a precision machined recess in the top of the cylinder block and converts the open deck M96/7 construction to a closed deck design - like the GT3 and Turbo - bullet proof but a little more expensive to produce and create.
We usually see iron liners over here but have also seen steel dry ones (which despite not being located at the top in a machined recess do seem better but like iron liners have to run with greater cold clearances and sometimes give rise to smoking and oil consumption).
The original 2.5, 2.7 and 3.2 Boxster versions had thicker cylinder tubes cast into the open deck design and less piston force and were acceptably reliable. The 996 3.4 used the same casting but bored out an additional 3mm making the cylinder wall thinner while the piston forces on it increased - leading to ovality and "D" chunking.
We think a change in the Lokasil specification adding more silicon made the later 3.4, 3.6 and 3.8 engines a bit stronger but they were not made with thicker cylinder walls so with increased piston forces they also migrate oval and sometimes crack or "D" chunk.
Because we machine away all of the original upper cylinder (to enable us to fit a thicker ribbed wet liner) we have had no problems retrofitting our alloy "cylinders" (as they should be more properly named not "liners") to engines previously fitted with ferrous liners that have failed.
You can see why in either of our videos accessed via www.hartech.org Porsche specialists UK
Baz
#83
Former Vendor

There's are reason why a few of "those other Guys" have attended my classes on these engines. When they showed up, I learned more about them, than they learned from me about these engines. This includes knowing their experience level with the M9X platform, and how long they'd been working with them.
That said, Nickies have been constantly used in my facility since 1999. We didn't start building these engines 3-4 years ago, nor do the processes that we use only have a couple years of application under their belts. Baz at Hartech shares the same sort of experiences, and has been working with these engines just as long, just across the Atlantic.
That said, Nickies have been constantly used in my facility since 1999. We didn't start building these engines 3-4 years ago, nor do the processes that we use only have a couple years of application under their belts. Baz at Hartech shares the same sort of experiences, and has been working with these engines just as long, just across the Atlantic.
#84

I agree the Nickies sleeve is great way to go but it sounds like your saying Hartech and Flat 6 are the only game in town and all others are not worth considering?
If this is the case I have to say my reaction to this sort of dogmatic thinking is to run the other way fast. No one has a lock down on knowledge. Knowledge comes from experience.
Other builders have also taken the time to learn this engines shortcomings and come up with a process which from my view fully address the issues and offer a great long term reliable solution. Some of those solutions include using "Nickies" and others do not. Most are in the $20K range which is not cheap.
As far as the lead times are concerned 5-6 weeks is the norm which is more than enough time to perform a complete rebuild. I consider lead time to be time spent working on the motor on a daily basis. Any more than that is ridiculous IMHO.
If this is the case I have to say my reaction to this sort of dogmatic thinking is to run the other way fast. No one has a lock down on knowledge. Knowledge comes from experience.
Other builders have also taken the time to learn this engines shortcomings and come up with a process which from my view fully address the issues and offer a great long term reliable solution. Some of those solutions include using "Nickies" and others do not. Most are in the $20K range which is not cheap.
As far as the lead times are concerned 5-6 weeks is the norm which is more than enough time to perform a complete rebuild. I consider lead time to be time spent working on the motor on a daily basis. Any more than that is ridiculous IMHO.
#85

Can I just say t hat it is absolutely not my intention to get into a competition about rebuilding these engines. We have been involved since the first set of rebuild gaskets and seals was available and now build 1/day - but are stuck at that because we cannot just increase output in one place (without shift working) but everywhere and we didn't start Hartech to dominate everything - just to provide a good quality affordable engineered based service to Porsche owners.
The unexpected engine problems just happened to fit into a sphere of my education, previous experience and familiarity and that is probably why we are managing very well rebuilding them our way over here but it is unlikely to go on for decades when Gen 2 engines and eventually plasma coated alloy cylinder blocks take the stage and reduce failure rates.
I also don't want to criticise others - because there are always different ways to do things and - properly engineered - it is in my experience - often the case that several different solutions all work.
Good engineers and specialists recognise each other and similarly quickly realise who provides a less than reliable and cheaper solution for more commercial reasons - but in our opinion it is not good practice to expose that directly - just to instead explain why we do things our way and leave it to the consumer to make up their own minds where to go.
Because we cannot easily expand anymore in the UK but have developed such a reliable solution - and because of the transport cost for cylinders and timing delays - we are assisting a Canadian specialist in setting up to replicate our system and production over there and they are doing a great job setting it all up with considerable investment in machinery and tooling - but in the States there seem to already be many quite large operations doing OK - so it is not my intention to compare our differences for any reason other than to support those that understand how to do things properly and explain why some other solutions may not in my opinion (for what it is worth) be quite as good.
However - unless I miss-understand the photo on page 5 - it seems that ours is still the only wet cylinder where the top hat section fits into a precision machined locations to support the cylinder - preventing it from tipping or stretching the locating bore - and creating a true closed deck. That is not to say other systems are necessarily inferior - just different. The GT3 and Turbo variants also have a similar top hat precision location to ours and of course are also alloy Nikasil plated.
If you view either of the 2 short videos available from us on www.hartech.org you will clearly see the machined recess in the block and the flat on the sides of the cylinder necessary because the top diameter is larger to fit the machined block top recess.
It is having to manufacture the cylinder from a bigger billet and to machine out the top diameter and cylinder flats - that increases our costs - so I would like to claim that no other solution we have seen is better and in our case we compensated for the extra costs by setting up our own IN HOUSE machine shop to carry out all the work within our own premises and under our total control reducing the number of margins added on by each sub-contractor and speeding up deliveries.
In situations where racing is the requirement it is not so important to use alloy instead of steel because the clearances are only ever going to be used flat out (and for relatively low overall mileages) but for road use with an engine that has to perform well at very low and high speeds and has relatively large diameter pistons - it is better to match the cylinder and piston expansion coefficients as much as possible (which is why Porsche and others have gone to such lengths to do just that).
If the diameter of a bigger than standard piston results in there being little clearance for the coolant it is possible to make a steel wet liner a little thinner (for racing) or to drill coolant holes along its height to compensate for the lower thermal cooling coefficient and this has often been used for special low volume racing applications but is more expensive yet again.
Fitting alloy wet liners is a special procedure and requires a lot more "engineering" and extremely close tolerances to make it reliable. In our experience - in applications where the original cylinder block is recognised as weak - it is usually better to machine it all away in the area of the coolant but then essential to support the top (as we do). We are lucky that Porsche's original design allowed for that by making the inside of the top of each cylinder coolant area circular!
In our experience over here - very thin alloy dry liners can twist and work loose over time and distort whereas a thicker wet liner is much more stable.
It seems from my occasional reading of the International forums (that generally record different solutions in the USA) that a lot of different methods are all working well and providing a satisfactory outcome for our cousins over there!
Baz
The unexpected engine problems just happened to fit into a sphere of my education, previous experience and familiarity and that is probably why we are managing very well rebuilding them our way over here but it is unlikely to go on for decades when Gen 2 engines and eventually plasma coated alloy cylinder blocks take the stage and reduce failure rates.
I also don't want to criticise others - because there are always different ways to do things and - properly engineered - it is in my experience - often the case that several different solutions all work.
Good engineers and specialists recognise each other and similarly quickly realise who provides a less than reliable and cheaper solution for more commercial reasons - but in our opinion it is not good practice to expose that directly - just to instead explain why we do things our way and leave it to the consumer to make up their own minds where to go.
Because we cannot easily expand anymore in the UK but have developed such a reliable solution - and because of the transport cost for cylinders and timing delays - we are assisting a Canadian specialist in setting up to replicate our system and production over there and they are doing a great job setting it all up with considerable investment in machinery and tooling - but in the States there seem to already be many quite large operations doing OK - so it is not my intention to compare our differences for any reason other than to support those that understand how to do things properly and explain why some other solutions may not in my opinion (for what it is worth) be quite as good.
However - unless I miss-understand the photo on page 5 - it seems that ours is still the only wet cylinder where the top hat section fits into a precision machined locations to support the cylinder - preventing it from tipping or stretching the locating bore - and creating a true closed deck. That is not to say other systems are necessarily inferior - just different. The GT3 and Turbo variants also have a similar top hat precision location to ours and of course are also alloy Nikasil plated.
If you view either of the 2 short videos available from us on www.hartech.org you will clearly see the machined recess in the block and the flat on the sides of the cylinder necessary because the top diameter is larger to fit the machined block top recess.
It is having to manufacture the cylinder from a bigger billet and to machine out the top diameter and cylinder flats - that increases our costs - so I would like to claim that no other solution we have seen is better and in our case we compensated for the extra costs by setting up our own IN HOUSE machine shop to carry out all the work within our own premises and under our total control reducing the number of margins added on by each sub-contractor and speeding up deliveries.
In situations where racing is the requirement it is not so important to use alloy instead of steel because the clearances are only ever going to be used flat out (and for relatively low overall mileages) but for road use with an engine that has to perform well at very low and high speeds and has relatively large diameter pistons - it is better to match the cylinder and piston expansion coefficients as much as possible (which is why Porsche and others have gone to such lengths to do just that).
If the diameter of a bigger than standard piston results in there being little clearance for the coolant it is possible to make a steel wet liner a little thinner (for racing) or to drill coolant holes along its height to compensate for the lower thermal cooling coefficient and this has often been used for special low volume racing applications but is more expensive yet again.
Fitting alloy wet liners is a special procedure and requires a lot more "engineering" and extremely close tolerances to make it reliable. In our experience - in applications where the original cylinder block is recognised as weak - it is usually better to machine it all away in the area of the coolant but then essential to support the top (as we do). We are lucky that Porsche's original design allowed for that by making the inside of the top of each cylinder coolant area circular!
In our experience over here - very thin alloy dry liners can twist and work loose over time and distort whereas a thicker wet liner is much more stable.
It seems from my occasional reading of the International forums (that generally record different solutions in the USA) that a lot of different methods are all working well and providing a satisfactory outcome for our cousins over there!
Baz
#86
Former Vendor

I agree the Nickies sleeve is great way to go but it sounds like your saying Hartech and Flat 6 are the only game in town and all others are not worth considering?
If this is the case I have to say my reaction to this sort of dogmatic thinking is to run the other way fast. No one has a lock down on knowledge. Knowledge comes from experience.
As the
Other builders have also taken the time to learn this engines shortcomings and come up with a process which from my view fully address the issues and offer a great long term reliable solution. Some of those solutions include using "Nickies" and others do not. Most are in the $20K range which is not cheap.
As far as the lead times are concerned 5-6 weeks is the norm which is more than enough time to perform a complete rebuild. I consider lead time to be time spent working on the motor on a daily basis. Any more than that is ridiculous IMHO.
If this is the case I have to say my reaction to this sort of dogmatic thinking is to run the other way fast. No one has a lock down on knowledge. Knowledge comes from experience.
As the
Other builders have also taken the time to learn this engines shortcomings and come up with a process which from my view fully address the issues and offer a great long term reliable solution. Some of those solutions include using "Nickies" and others do not. Most are in the $20K range which is not cheap.
As far as the lead times are concerned 5-6 weeks is the norm which is more than enough time to perform a complete rebuild. I consider lead time to be time spent working on the motor on a daily basis. Any more than that is ridiculous IMHO.
We only hope, and expect that others put as much into their programs as we do, and that they offer a product without compromise.
That said, it's. It how fast or ski an engine is built. You won't find a clock in my facility- it takes as long as it takes. I have maintained a 9 month backlog with these engines since 2007, and the last 5 years have been at 1 year to 14 months. We don't rush, and we don't accept every job that knocks on our door. Maybe 3-4 times a year we lose a job (that I'd accept) because someone has the necessity for instant gratification- so be it. I will not rush, and I will not expedite; because haste makes waste, and all that can be rushed is failure- not success.
My process has been proven for over a decade. We have a 64 step process that creates the experience that our customers experience. You won't read of any disappointment.
It's pretty clear that you are going to Vision for the build, and that's probably what you should do. Under no circumstance will I "sell" anyone on anything, or persuade them. I probably send more business to Vision than his marketing creates, 3 people have been sent that way this week alone, and you make 4.
#87

fair enough. Sounds like you leave room for others the play which was my only concern. I have no doubt about your proven process which I stated early on.
Not even close to making my decision on who to use at this point but if one doesn't take the time to learn facts and debate different ideas then it becomes a blind $20K decision. As a business owner I've learned not to make blind $20K decisions.
Dwain was very complimentary towards you BTW. Nothing but good things to say. My main reason for reaching out to him has more to do with a recommendation from a fellow PCA member and the fact that his shop is a 40 minute drive from where my wife kids vacation each year.
I think it would be a great resource and help others who are facing the possibility to have a rebuild thread photo essay style. Whomever I do end up using I'm hoping will go along with the idea. Obviously being mindful of protecting proprietary processes etc...
Not even close to making my decision on who to use at this point but if one doesn't take the time to learn facts and debate different ideas then it becomes a blind $20K decision. As a business owner I've learned not to make blind $20K decisions.
Dwain was very complimentary towards you BTW. Nothing but good things to say. My main reason for reaching out to him has more to do with a recommendation from a fellow PCA member and the fact that his shop is a 40 minute drive from where my wife kids vacation each year.
I think it would be a great resource and help others who are facing the possibility to have a rebuild thread photo essay style. Whomever I do end up using I'm hoping will go along with the idea. Obviously being mindful of protecting proprietary processes etc...
Not at all. We've welcomed others into this game, and many of them utilize the components that we have developed to build their engines. If we were the only game in town, we'd not be offering to sell these components. This is one reason that I have had over 1,400 technicians attend my classes over the last decade. It's also the reason why I've written the book on these engines. So, any thought you had is completely off base, considering these facts I have just shared.
We only hope, and expect that others put as much into their programs as we do, and that they offer a product without compromise.
That said, it's. It how fast or ski an engine is built. You won't find a clock in my facility- it takes as long as it takes. I have maintained a 9 month backlog with these engines since 2007, and the last 5 years have been at 1 year to 14 months. We don't rush, and we don't accept every job that knocks on our door. Maybe 3-4 times a year we lose a job (that I'd accept) because someone has the necessity for instant gratification- so be it. I will not rush, and I will not expedite; because haste makes waste, and all that can be rushed is failure- not success.
My process has been proven for over a decade. We have a 64 step process that creates the experience that our customers experience. You won't read of any disappointment.
It's pretty clear that you are going to Vision for the build, and that's probably what you should do. Under no circumstance will I "sell" anyone on anything, or persuade them. I probably send more business to Vision than his marketing creates, 3 people have been sent that way this week alone, and you make 4.
We only hope, and expect that others put as much into their programs as we do, and that they offer a product without compromise.
That said, it's. It how fast or ski an engine is built. You won't find a clock in my facility- it takes as long as it takes. I have maintained a 9 month backlog with these engines since 2007, and the last 5 years have been at 1 year to 14 months. We don't rush, and we don't accept every job that knocks on our door. Maybe 3-4 times a year we lose a job (that I'd accept) because someone has the necessity for instant gratification- so be it. I will not rush, and I will not expedite; because haste makes waste, and all that can be rushed is failure- not success.
My process has been proven for over a decade. We have a 64 step process that creates the experience that our customers experience. You won't read of any disappointment.
It's pretty clear that you are going to Vision for the build, and that's probably what you should do. Under no circumstance will I "sell" anyone on anything, or persuade them. I probably send more business to Vision than his marketing creates, 3 people have been sent that way this week alone, and you make 4.
#88
Former Vendor

We post a few dozen assembly photos on our Facebook page from every build. Photos are no problem, at least 80 photos are taken to document our assembly process as a standard procedure here.
I have nothing bad to say about Dwain. Others have came into this arena and created a price war between themselves, which is creating a bunch of junk to be built. Those are the guys that don't want to meet me. I don't play that game. I do more than build these engines, and my prices are only going up as the engine is developed more and more- not down.
Anytime someone starts asking about other builders I go quiet and won't say anything, good or bad. I don't care what they do.
choose carefully. Location matters to some, but I ship cars cross country weekly and o we 1/2 my USA business is from California. Shipping cost less than local sales taxes. I have sold one engine in my own state in the last 2 years.
I have nothing bad to say about Dwain. Others have came into this arena and created a price war between themselves, which is creating a bunch of junk to be built. Those are the guys that don't want to meet me. I don't play that game. I do more than build these engines, and my prices are only going up as the engine is developed more and more- not down.
Anytime someone starts asking about other builders I go quiet and won't say anything, good or bad. I don't care what they do.
choose carefully. Location matters to some, but I ship cars cross country weekly and o we 1/2 my USA business is from California. Shipping cost less than local sales taxes. I have sold one engine in my own state in the last 2 years.
#89

I appreciate the well thought out response. This is the reason I've learned to come to forums. We all benefit massively from experts such as yourself and others.
I have watched your videos and also read the lengthy white paper you published on the issue. Great resource.
Vision machines the case half I would say very very similar to yours based on photo evidence. I know they do use an autoclave to heat the case half prior to pressing in the room temp cylinder which also has an oring at it's base for proper oil/water sealing.
Analyzing 4130 cromoly cylinder (no coating) vs Alloy cylinder w/Nikasil coating vs Nickie liner for daily street use. One of these must naturally be a better material solution given the application however, doesn't the water cooled affect to a large degree render the dissimilar material a non issue? I assume your alloy cylinder is made of billet? The case we know is cast so isn't that technically also a dissimilar material?
Thanks again for engaging in the process!
I have watched your videos and also read the lengthy white paper you published on the issue. Great resource.
Vision machines the case half I would say very very similar to yours based on photo evidence. I know they do use an autoclave to heat the case half prior to pressing in the room temp cylinder which also has an oring at it's base for proper oil/water sealing.
Analyzing 4130 cromoly cylinder (no coating) vs Alloy cylinder w/Nikasil coating vs Nickie liner for daily street use. One of these must naturally be a better material solution given the application however, doesn't the water cooled affect to a large degree render the dissimilar material a non issue? I assume your alloy cylinder is made of billet? The case we know is cast so isn't that technically also a dissimilar material?
Thanks again for engaging in the process!
Can I just say t hat it is absolutely not my intention to get into a competition about rebuilding these engines. We have been involved since the first set of rebuild gaskets and seals was available and now build 1/day - but are stuck at that because we cannot just increase output in one place (without shift working) but everywhere and we didn't start Hartech to dominate everything - just to provide a good quality affordable engineered based service to Porsche owners.
The unexpected engine problems just happened to fit into a sphere of my education, previous experience and familiarity and that is probably why we are managing very well rebuilding them our way over here but it is unlikely to go on for decades when Gen 2 engines and eventually plasma coated alloy cylinder blocks take the stage and reduce failure rates.
I also don't want to criticise others - because there are always different ways to do things and - properly engineered - it is in my experience - often the case that several different solutions all work.
Good engineers and specialists recognise each other and similarly quickly realise who provides a less than reliable and cheaper solution for more commercial reasons - but in our opinion it is not good practice to expose that directly - just to instead explain why we do things our way and leave it to the consumer to make up their own minds where to go.
Because we cannot easily expand anymore in the UK but have developed such a reliable solution - and because of the transport cost for cylinders and timing delays - we are assisting a Canadian specialist in setting up to replicate our system and production over there and they are doing a great job setting it all up with considerable investment in machinery and tooling - but in the States there seem to already be many quite large operations doing OK - so it is not my intention to compare our differences for any reason other than to support those that understand how to do things properly and explain why some other solutions may not in my opinion (for what it is worth) be quite as good.
However - unless I miss-understand the photo on page 5 - it seems that ours is still the only wet cylinder where the top hat section fits into a precision machined locations to support the cylinder - preventing it from tipping or stretching the locating bore - and creating a true closed deck. That is not to say other systems are necessarily inferior - just different. The GT3 and Turbo variants also have a similar top hat precision location to ours and of course are also alloy Nikasil plated.
If you view either of the 2 short videos available from us on www.hartech.org you will clearly see the machined recess in the block and the flat on the sides of the cylinder necessary because the top diameter is larger to fit the machined block top recess.
It is having to manufacture the cylinder from a bigger billet and to machine out the top diameter and cylinder flats - that increases our costs - so I would like to claim that no other solution we have seen is better and in our case we compensated for the extra costs by setting up our own IN HOUSE machine shop to carry out all the work within our own premises and under our total control reducing the number of margins added on by each sub-contractor and speeding up deliveries.
In situations where racing is the requirement it is not so important to use alloy instead of steel because the clearances are only ever going to be used flat out (and for relatively low overall mileages) but for road use with an engine that has to perform well at very low and high speeds and has relatively large diameter pistons - it is better to match the cylinder and piston expansion coefficients as much as possible (which is why Porsche and others have gone to such lengths to do just that).
If the diameter of a bigger than standard piston results in there being little clearance for the coolant it is possible to make a steel wet liner a little thinner (for racing) or to drill coolant holes along its height to compensate for the lower thermal cooling coefficient and this has often been used for special low volume racing applications but is more expensive yet again.
Fitting alloy wet liners is a special procedure and requires a lot more "engineering" and extremely close tolerances to make it reliable. In our experience - in applications where the original cylinder block is recognised as weak - it is usually better to machine it all away in the area of the coolant but then essential to support the top (as we do). We are lucky that Porsche's original design allowed for that by making the inside of the top of each cylinder coolant area circular!
In our experience over here - very thin alloy dry liners can twist and work loose over time and distort whereas a thicker wet liner is much more stable.
It seems from my occasional reading of the International forums (that generally record different solutions in the USA) that a lot of different methods are all working well and providing a satisfactory outcome for our cousins over there!
Baz
The unexpected engine problems just happened to fit into a sphere of my education, previous experience and familiarity and that is probably why we are managing very well rebuilding them our way over here but it is unlikely to go on for decades when Gen 2 engines and eventually plasma coated alloy cylinder blocks take the stage and reduce failure rates.
I also don't want to criticise others - because there are always different ways to do things and - properly engineered - it is in my experience - often the case that several different solutions all work.
Good engineers and specialists recognise each other and similarly quickly realise who provides a less than reliable and cheaper solution for more commercial reasons - but in our opinion it is not good practice to expose that directly - just to instead explain why we do things our way and leave it to the consumer to make up their own minds where to go.
Because we cannot easily expand anymore in the UK but have developed such a reliable solution - and because of the transport cost for cylinders and timing delays - we are assisting a Canadian specialist in setting up to replicate our system and production over there and they are doing a great job setting it all up with considerable investment in machinery and tooling - but in the States there seem to already be many quite large operations doing OK - so it is not my intention to compare our differences for any reason other than to support those that understand how to do things properly and explain why some other solutions may not in my opinion (for what it is worth) be quite as good.
However - unless I miss-understand the photo on page 5 - it seems that ours is still the only wet cylinder where the top hat section fits into a precision machined locations to support the cylinder - preventing it from tipping or stretching the locating bore - and creating a true closed deck. That is not to say other systems are necessarily inferior - just different. The GT3 and Turbo variants also have a similar top hat precision location to ours and of course are also alloy Nikasil plated.
If you view either of the 2 short videos available from us on www.hartech.org you will clearly see the machined recess in the block and the flat on the sides of the cylinder necessary because the top diameter is larger to fit the machined block top recess.
It is having to manufacture the cylinder from a bigger billet and to machine out the top diameter and cylinder flats - that increases our costs - so I would like to claim that no other solution we have seen is better and in our case we compensated for the extra costs by setting up our own IN HOUSE machine shop to carry out all the work within our own premises and under our total control reducing the number of margins added on by each sub-contractor and speeding up deliveries.
In situations where racing is the requirement it is not so important to use alloy instead of steel because the clearances are only ever going to be used flat out (and for relatively low overall mileages) but for road use with an engine that has to perform well at very low and high speeds and has relatively large diameter pistons - it is better to match the cylinder and piston expansion coefficients as much as possible (which is why Porsche and others have gone to such lengths to do just that).
If the diameter of a bigger than standard piston results in there being little clearance for the coolant it is possible to make a steel wet liner a little thinner (for racing) or to drill coolant holes along its height to compensate for the lower thermal cooling coefficient and this has often been used for special low volume racing applications but is more expensive yet again.
Fitting alloy wet liners is a special procedure and requires a lot more "engineering" and extremely close tolerances to make it reliable. In our experience - in applications where the original cylinder block is recognised as weak - it is usually better to machine it all away in the area of the coolant but then essential to support the top (as we do). We are lucky that Porsche's original design allowed for that by making the inside of the top of each cylinder coolant area circular!
In our experience over here - very thin alloy dry liners can twist and work loose over time and distort whereas a thicker wet liner is much more stable.
It seems from my occasional reading of the International forums (that generally record different solutions in the USA) that a lot of different methods are all working well and providing a satisfactory outcome for our cousins over there!
Baz
#90
Former Vendor

Vision machines the case half I would say very very similar to yours based on photo evidence. I know they do use an autoclave to heat the case half prior to pressing in the room temp cylinder which also has an oring at it's base for proper oil/water sealing.
The dissimilar material issue doesn't come into play until you start mixing ferrous, with non- ferrous materials. The Nickies billet extrusion has 18 years of proven performance under its belt. Hundreds of coolant samples, thousands of oil samples, and I have many engines with over 200 track hours on them, some producing 120HP more than stock power. Some of the builders today that have centered onto their own, once used Nickies while they were learning about these engines. I know 2-3 of them who only stepped away because the process either cost too much, or took too long. You can go back a few years into some Pano and Excellence magazine articles to prove these facts, as some of the cars these shops built were featured, and the story proves what I have just stated.
Dissimilar materials are a bigger player with water- cooling, since all the ingredients for electrolysis are in place. This is an issues that Subaru engine builders know about, and I first experienced it in 1995 with an EJ series Subaru engine.
I can get by with running .00175" piston to cylinder clearance @ 72F, and still have .00075" at zero degrees F with our cylinder and piston combo. I've put just as much time into cold weather optimization of these arrangements than hot. Why? Because we build a ton of Canadian engines, and they all come here due to cylinder failures. This also comes from a non- generic skirt cam design on the piston, one that's wider, and higher than the standard, off the shelf parts. Another reason that it takes us so many months to build an engine, is related to not using generic, off the shelf, mass produced parts. It takes longer to land a set of pistons here, than other builders have for their total turn around time for an engine. The same goes with valves, seats, springs, and hardware- I throw all the factory parts away, and its all replaced. This is done whether the parts are good, or bad.
That said, the GT series and Turbo engines may use an O ring design, but the cylinders are fully floating in their water jackets, and they are also alloy, and in many cases (up to 2011) were Nikisil plated. These O rings are on the cylinder, and also in the removable water jacket that accepts the cylinder that is pressed into it during assembly, as pictured below. This is a Mezger based turbo I finished a few months back. Note the extremely cold cylinder, in this picture I was setting my ring gaps cold, and these are LN Nickies cylinders, for the turbo. Because of the HUGE difference in engine design you can't effectively compare whats done with the M96/ 97 to that of a GT/ Turbo engine, since the cylinders are not integral to the block on the GT/ Turbo, and they are with the M96/ 97. Its a whole different world- just so you can understand how to compare apples, to apples, not grapefruits.
People think of steel as stronger. Based on direct experience I think of it as cheaper, quicker, louder, and less than optimum. Thats just me, and I can be an *******. At least I'm an honest one.
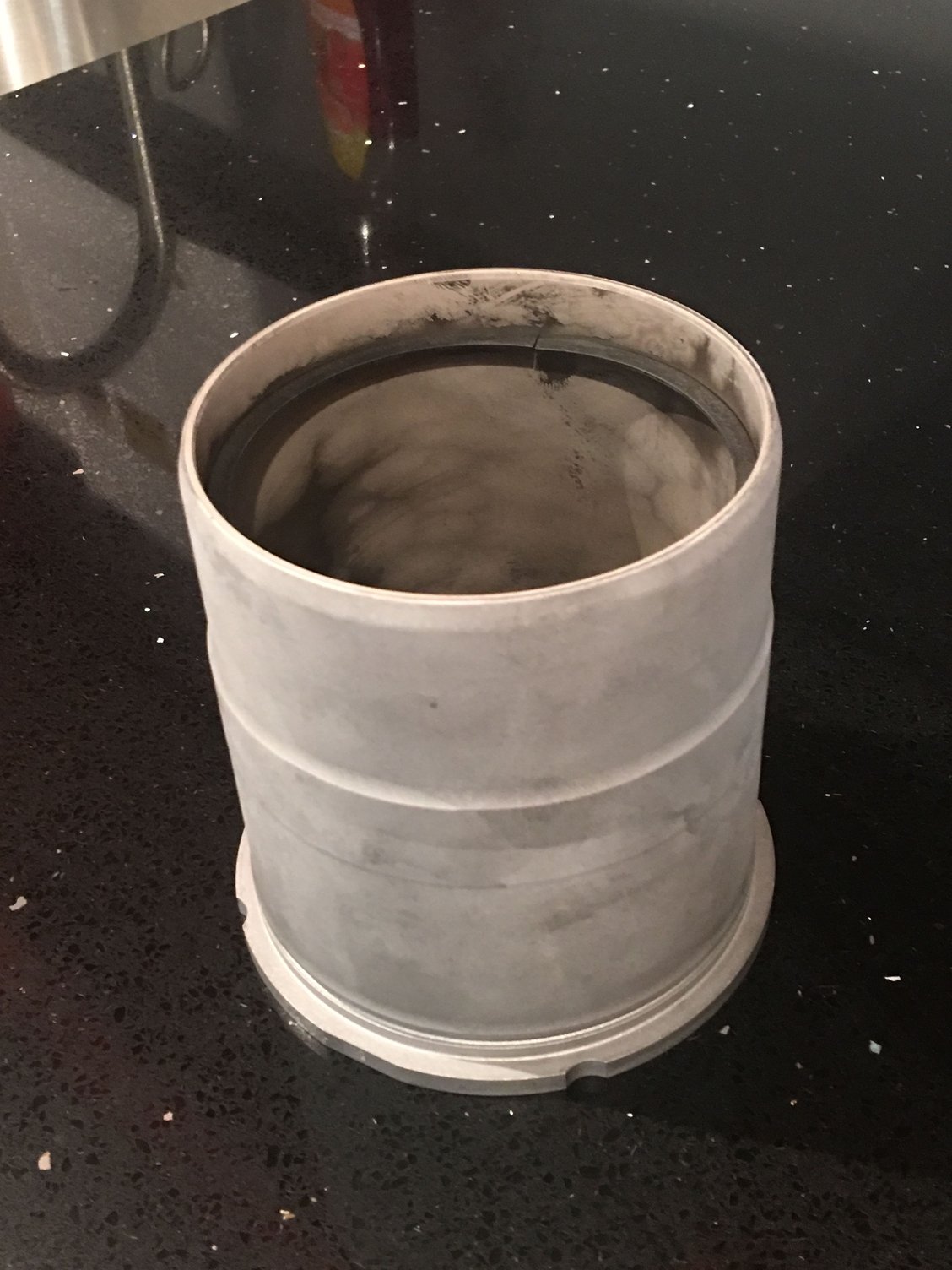

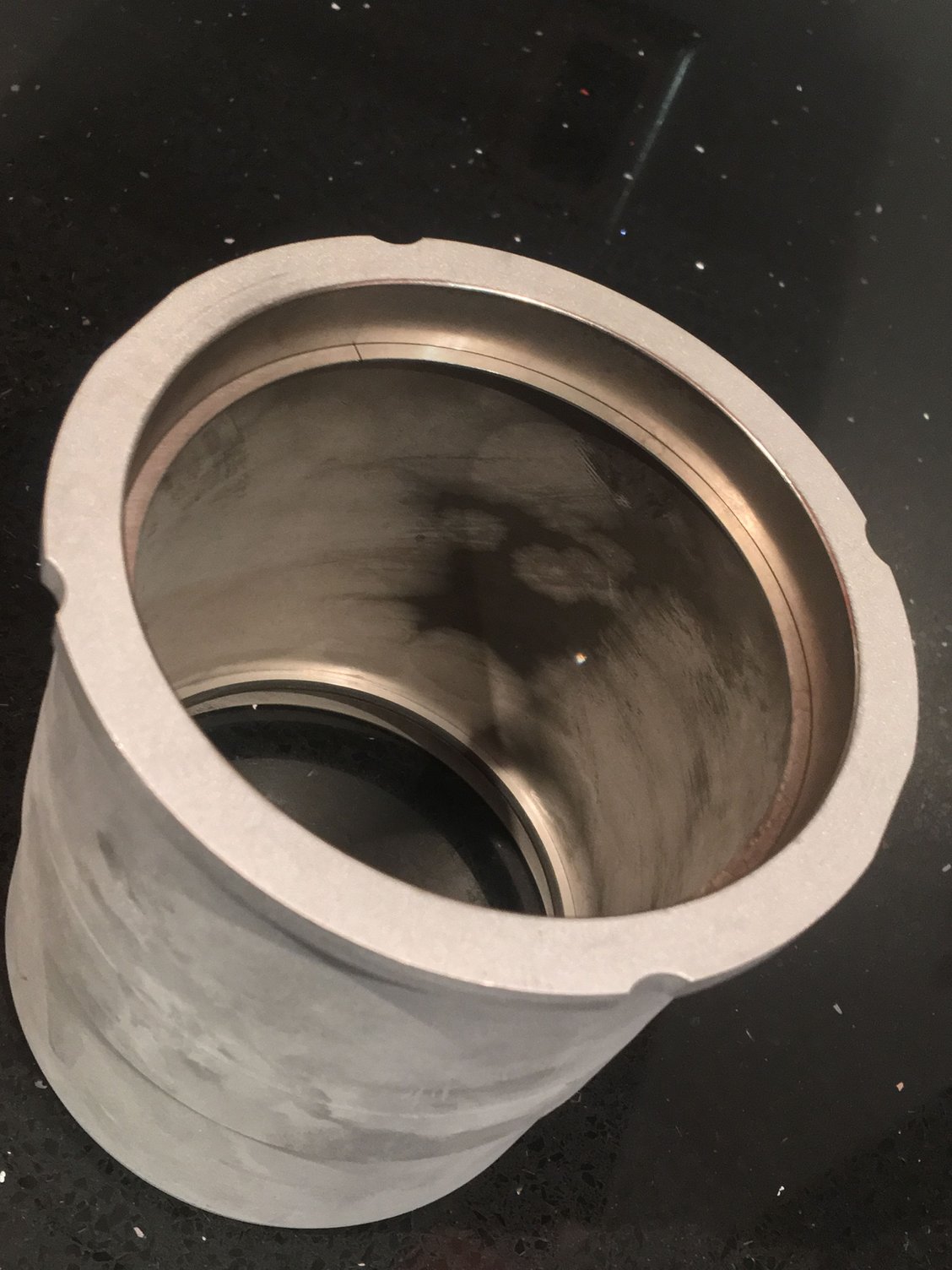
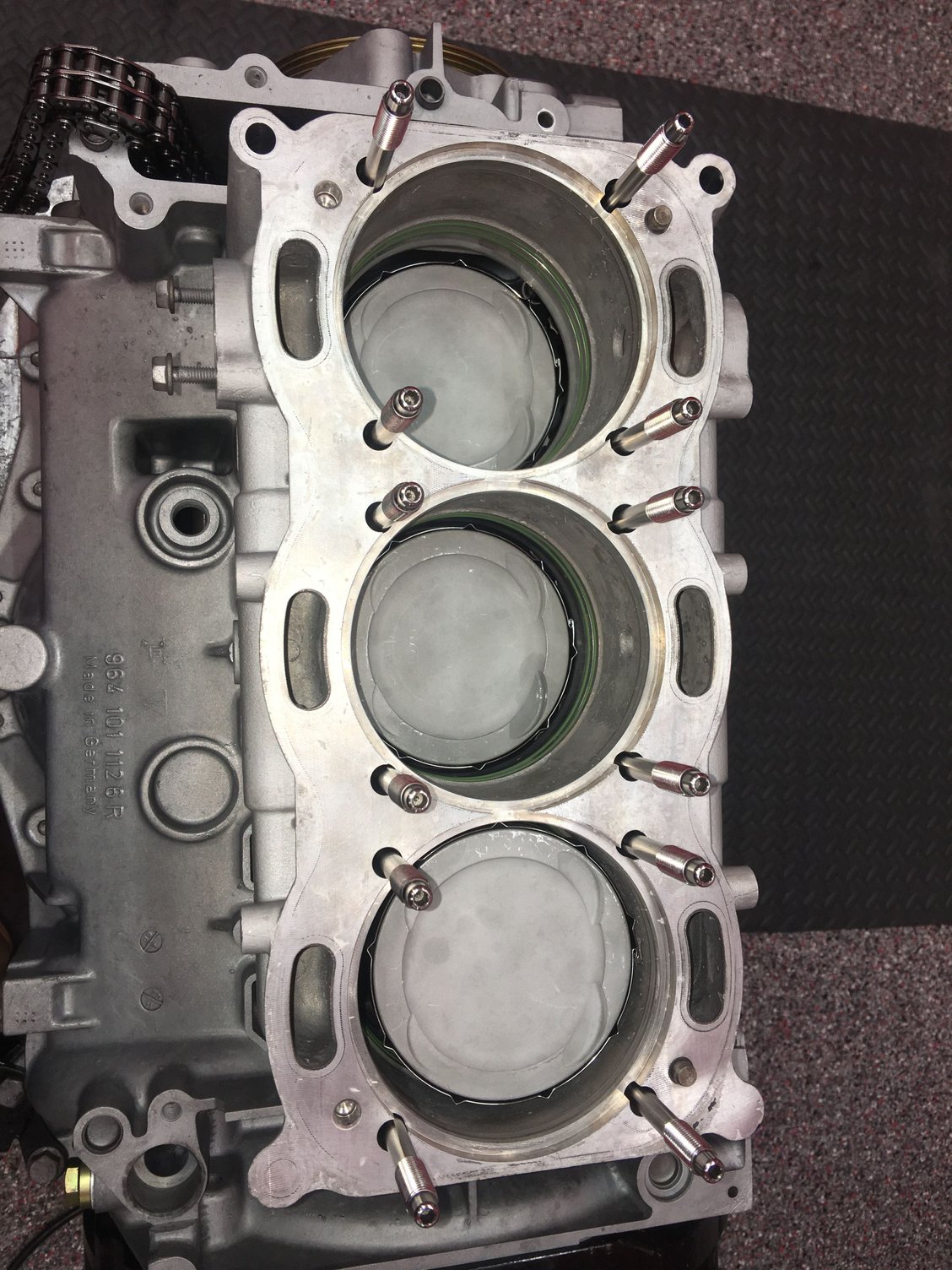
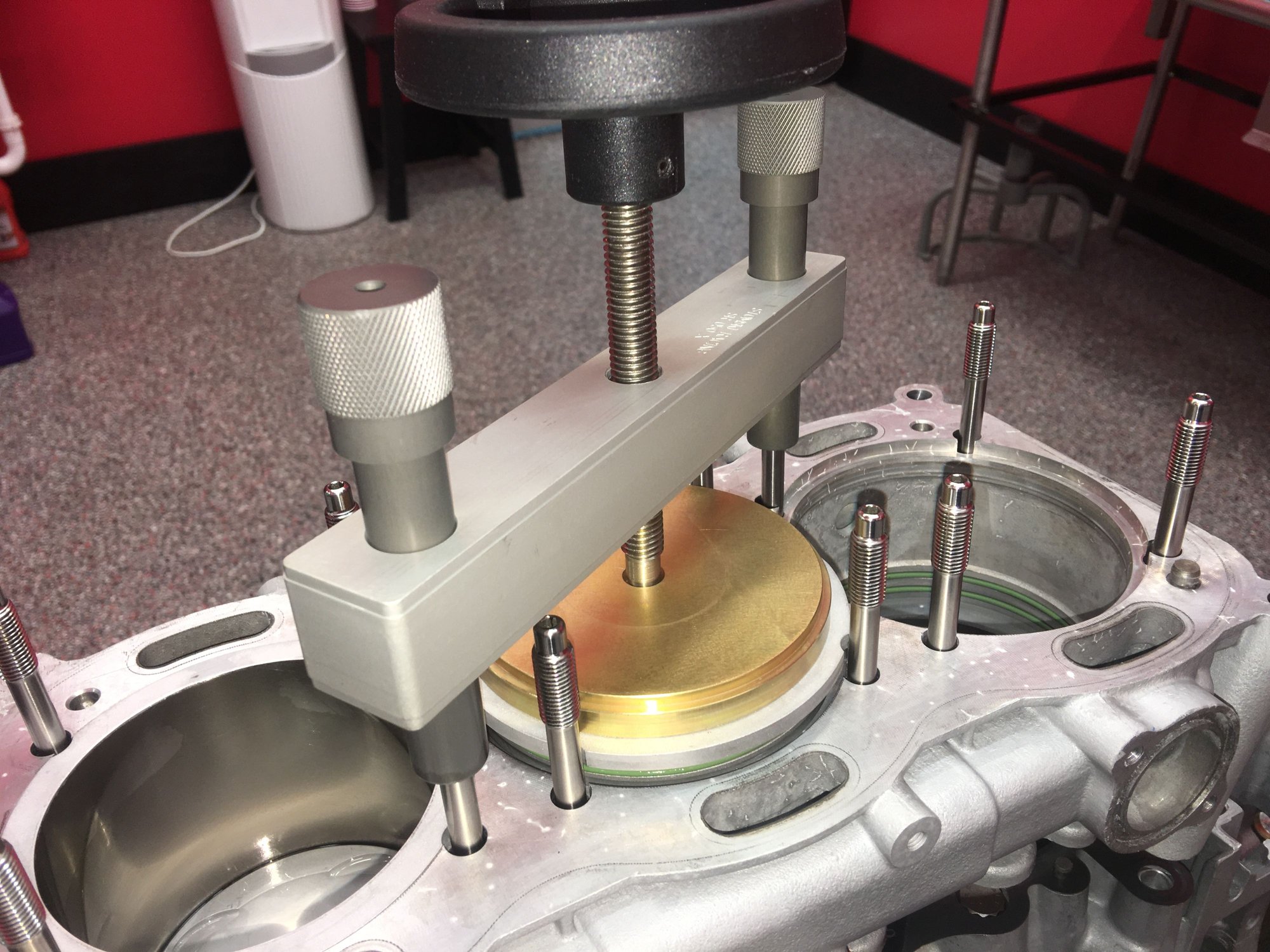