Screw it: "Sheet Metal" intakes
#122

Just started playing with Alibre. Interresting software.
Don't think I would have any problem doing any kind of shape on it.
I still highly prefer SketchUp.
Horribly easy, horribly fast.
But guess Alibre is made to export in data for CMC machine, right?
Don't think I would have any problem doing any kind of shape on it.
I still highly prefer SketchUp.

But guess Alibre is made to export in data for CMC machine, right?
#123

I sure as hell hope so or this whole exercise is mute.
#124

Brendon,
Having done similar projects, i prefer your idea showing the injector bosses in the flange. It would give you a more modular option. If you go back to your original drawing, it would cost less to use a flange, and tube with weld on injector bung. Machining that piece is possible, but both the materials and machine time would be considerable.
Hans
Having done similar projects, i prefer your idea showing the injector bosses in the flange. It would give you a more modular option. If you go back to your original drawing, it would cost less to use a flange, and tube with weld on injector bung. Machining that piece is possible, but both the materials and machine time would be considerable.
Hans
#126

Brendon,
If you are referring to the pic in post 114, then it is machinable, it will just be expensive. to do that, you are looking at buying a 4"x4"x16" piece of aluminum for each flange. Essentially, you are removing more aluminum than you will be keeping. The cost of the material itself will be high, plus the time to remove that much aluminum will be high. Going with a flange similar to what was shown in post 117 will require less material to begin with, and will have lower amount of machine time, plus is truly modular.... so its a win-win-win. The most reasonable solution will be to just machine a basic flange, thick enough to transition the 928 port shape to stock intake tube size, and use pre-machined generic injector holder. To use Ross Machine as an example, you could easily design a saddle-style injector holder like this to match stock tubing size. A stock flange can be waterjet cut for a very reasonable price, taking that blank to the machine shop to be routed out for port matching and tube matching will save a lot more money, then the material expense and machine time for the saddle style injectors will allow you to raise or lower the injector for atomization purposes, creating a modular system which would be marketable to other 928 owners.

The other idea would be just to weld on an injector boss like this, which would acomplish the same task:

Just an idea. I once designed a twin-roller throttle with the idea that less pieces would be better. The initial machining bill was $900, breaking down the original design into smaller pieces brought the bill down to around $350, and my material costs for aluminum reduced 40% as i was able to use smaller stock to begin with.
Hans
If you are referring to the pic in post 114, then it is machinable, it will just be expensive. to do that, you are looking at buying a 4"x4"x16" piece of aluminum for each flange. Essentially, you are removing more aluminum than you will be keeping. The cost of the material itself will be high, plus the time to remove that much aluminum will be high. Going with a flange similar to what was shown in post 117 will require less material to begin with, and will have lower amount of machine time, plus is truly modular.... so its a win-win-win. The most reasonable solution will be to just machine a basic flange, thick enough to transition the 928 port shape to stock intake tube size, and use pre-machined generic injector holder. To use Ross Machine as an example, you could easily design a saddle-style injector holder like this to match stock tubing size. A stock flange can be waterjet cut for a very reasonable price, taking that blank to the machine shop to be routed out for port matching and tube matching will save a lot more money, then the material expense and machine time for the saddle style injectors will allow you to raise or lower the injector for atomization purposes, creating a modular system which would be marketable to other 928 owners.

The other idea would be just to weld on an injector boss like this, which would acomplish the same task:

Just an idea. I once designed a twin-roller throttle with the idea that less pieces would be better. The initial machining bill was $900, breaking down the original design into smaller pieces brought the bill down to around $350, and my material costs for aluminum reduced 40% as i was able to use smaller stock to begin with.
Hans
#127

Thanks for involving yourself Hans. I can design my way into a 2k part, I know that. I want to design a very functional, and easy to assembly part that can be thought of as modular for people like me who do not have access to people who can design an entire intake. I am also trying to make it lower cost. The pieces I described that are on Ross machine seem to allow this. I just need to come up with the flange.
What if I made the structure more like this?
What if I made the structure more like this?
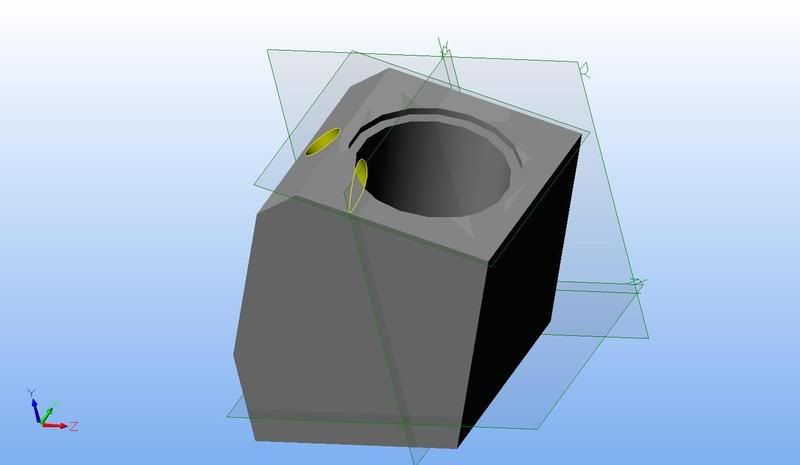
#128

Part of your problem is going to be boring that big hole for the runner. Its not hard, but takes time, and time is money. Also, you are paying for all that aluminum you are throwing away. Welding in an injector bung is very inexpensive. I would find a good welding shop near you, and just pay to have bungs welded to tube. You will probably have less than 2 hours worth of welding time to install all 8 bungs, and it will save a ton of money. You will already have to send it out to be welded anyway, in the above design for mating the runner to the flange. I am not trying to dissuade you from your original idea, as it is a very beautiful and user friendly part, it will just be horrifically expensive.
#129

Part of your problem is going to be boring that big hole for the runner. Its not hard, but takes time, and time is money. Also, you are paying for all that aluminum you are throwing away. Welding in an injector bung is very inexpensive. I would find a good welding shop near you, and just pay to have bungs welded to tube. You will probably have less than 2 hours worth of welding time to install all 8 bungs, and it will save a ton of money. You will already have to send it out to be welded anyway, in the above design for mating the runner to the flange. I am not trying to dissuade you from your original idea, as it is a very beautiful and user friendly part, it will just be horrifically expensive.
I guess I will have to give up on this idea of the holy grail and go back to the original idea of just a flange. There will be more time spent by me to make a smaller hole match the real hole, but I think the flange cost will go down. I needed to learn this. I fall inlove with an idea, and I must not hold onto an invalid idea just because I like it.
#130

No, I do appreciate your comments. I was just told by another friends that does machining that while my idea is very pretty, in no way is it user friendly in final costs or machining time (as you say, time is money).
I guess I will have to give up on this idea of the holy grail and go back to the original idea of just a flange. There will be more time spent by me to make a smaller hole match the real hole, but I think the flange cost will go down. I needed to learn this. I fall inlove with an idea, and I must not hold onto an invalid idea just because I like it.
I guess I will have to give up on this idea of the holy grail and go back to the original idea of just a flange. There will be more time spent by me to make a smaller hole match the real hole, but I think the flange cost will go down. I needed to learn this. I fall inlove with an idea, and I must not hold onto an invalid idea just because I like it.
Got an idea. A simple flange upon which you could bolt commercial ITBs.

#131


I was planning on using the plenum parts that are on that website to build a plenum and runners and twin throttle bodies. The ITBs seemed to be very expensive....
#132

I'm not sure to understand what you're trying to build. I admit, it's probably my poor English that's blocking me from understanding fully.
Do I understand you try to design the part that link the intake to the top of the cams?
Do I understand you try to design the part that link the intake to the top of the cams?
#133

Just joking with you Brendan. I've been down this road before and what at first seemed too expensive ended up being still very expensive, but not so bad when compared to some other approaches.
#134


#135

Do I understand that stock 928 doesn't really have a flange? Or are the spider's legs flanges? My only point of comparaison is my engine block.
I'm asking because I think I would like to try the exercise myself... Even if it will probably give no result at all.
Anywhere I could find size blueprint of the top of the cams?