New Crankshafts
#286
Former Sponsor
Thread Starter

I am far from a expert in failure analysis but for high output fatigue to be happening I would have thought that it was the lower cradle cracking and I don't know of myself any cases of this happening? Or is this the case? The lower cradle is made from a different alloy of aluminum and does not suffer from cracking problems, at this point of power development.
If it is the block that is cracking and granted it is a brittle material I would be more suspicious of mass forces. To have ago at analsysing from a far I would say you have to look and compare high output stock stroke engines that have been converted to forced induction. That way you have a relatively good engine to make a comparison. If those engines are not cracking blocks then mass forces may well be the culprit. Anything is possible.
As you know I have always been suspicious of the use of high mass forces and some strokers aslo have tied into the mix 6CWT cranks for additional imbalances and flexing. The other factor that may well be an issue is a stroke that is overly long. Again, there are multiple possibilities.
This was the reason I had Moldex make me a few years ago a 8CWT crank that had a reduced stroke of 3.55" and used 48 mm rod journals. It came with a bob weight of approx 1600 grams versus the stock Porsche crank at 2350 grams. When I visited with Moldex and discussed crankshafts design, they thought it very humorous that people were debating the use of 6 counterweight and 8 counterweight crankshafts. They absolutely felt that an 8 counterweweight crankshaft was a complete waste of material and additional unnecessary weight, at the rpm ranges that the 928 engine was then being used for. More specifically, they actually laughed about it. As my engines become more "evolved" and I have access to camshafts that allow higher rpm use, I've seen the potential for these engines to spin at increased rpms, over what they have, in the past. My "new" crankshafts have 8 counterweights and are designed for significantly lighter bob weights, looking forward to this end.
Now not being one for paying attention in maths class but wondering how much quicker this new lightweight wunder assembly would spin up, I posted that very question on a technical engine building site. The answer came back, no difference! The reason I was given was that because of my increased stroke the effect of swinging these parts further from the centreline of the mains was that it basically equalled the higher stock mass much closer to the centerline.
I hadn't though achieved nothing, I hadn't increased the mass force loadings, if my stroker was the conventional stroker stroke which was used from the very early days, that being 3.75" then I would have had slightly increased loadings over stock.
So those are my thoughts on main bearing fatigue cracking, not saying it is right but it might be. The other minor supporting fact is when you view Conrods that have run in race engines you can seen the loadings are very much in a downward direction and that the power loading would be felt more by the lower cradle. If this is the cracking hot spot well that would make sense as the lower cradle seems to be made from a poorer quality material.
If it is the block that is cracking and granted it is a brittle material I would be more suspicious of mass forces. To have ago at analsysing from a far I would say you have to look and compare high output stock stroke engines that have been converted to forced induction. That way you have a relatively good engine to make a comparison. If those engines are not cracking blocks then mass forces may well be the culprit. Anything is possible.
As you know I have always been suspicious of the use of high mass forces and some strokers aslo have tied into the mix 6CWT cranks for additional imbalances and flexing. The other factor that may well be an issue is a stroke that is overly long. Again, there are multiple possibilities.
This was the reason I had Moldex make me a few years ago a 8CWT crank that had a reduced stroke of 3.55" and used 48 mm rod journals. It came with a bob weight of approx 1600 grams versus the stock Porsche crank at 2350 grams. When I visited with Moldex and discussed crankshafts design, they thought it very humorous that people were debating the use of 6 counterweight and 8 counterweight crankshafts. They absolutely felt that an 8 counterweweight crankshaft was a complete waste of material and additional unnecessary weight, at the rpm ranges that the 928 engine was then being used for. More specifically, they actually laughed about it. As my engines become more "evolved" and I have access to camshafts that allow higher rpm use, I've seen the potential for these engines to spin at increased rpms, over what they have, in the past. My "new" crankshafts have 8 counterweights and are designed for significantly lighter bob weights, looking forward to this end.
Now not being one for paying attention in maths class but wondering how much quicker this new lightweight wunder assembly would spin up, I posted that very question on a technical engine building site. The answer came back, no difference! The reason I was given was that because of my increased stroke the effect of swinging these parts further from the centreline of the mains was that it basically equalled the higher stock mass much closer to the centerline.
I hadn't though achieved nothing, I hadn't increased the mass force loadings, if my stroker was the conventional stroker stroke which was used from the very early days, that being 3.75" then I would have had slightly increased loadings over stock.
So those are my thoughts on main bearing fatigue cracking, not saying it is right but it might be. The other minor supporting fact is when you view Conrods that have run in race engines you can seen the loadings are very much in a downward direction and that the power loading would be felt more by the lower cradle. If this is the cracking hot spot well that would make sense as the lower cradle seems to be made from a poorer quality material.
While anything is possible, sometimes one needs to look at the development of similar engines with similar construction, in order not to spend hundreds of thousands of dollars trying to figure out what is causing a specific underlying problem. Having been fairly active in the 944GTR world, the block problems they encountered, as the power output increased, pretty much answered the question, for me.
#288
Drifting

Are you sure it's a metallurgy issue, and not a design issue?
I've seen more than a few twin turbo Audi V8s make a lot of power and not come apart. Those blocks are using Alusil.
I've seen more than a few twin turbo Audi V8s make a lot of power and not come apart. Those blocks are using Alusil.
#289
Three Wheelin'

The CanAm Reynolds 390 sleeveless blocks were pretty good at the time. Wonder if it's the difference between open (928)& closed decks (Chevy)? H.P. was in the high 700's, which at the time - 40 years ago & no engine management was not bad.
#290
Former Sponsor
Thread Starter

Mike Simard made some highly intelligent comments on the forces impacting the block. Perhaps not coincidentally, his engine sleeved with his own sleeves is holding together.
If a block fails, it would be nice to know the specific circumstances of the failure. First, was it an S4 or earlier crank, a GTS crank, or stroker crank? That matters for the main bearing loads in many ways. The GTS crank, for example, appears to be a design that minimizes production cost and not main bearing loads. Second, was the engine sleeved or with original cylinder towers. Mike's success aside, I am sure that it's possible to sleeve these blocks in a way that weakens them. Third, was that just a thrust bearing failure that caused it? The answer to all of these failures is not "let's make a new block." It might be "let's make a new crankshaft" (the topic of this thread) or "let's not sleeve the engines the wrong way" or "let's not let the thrust bearing fail."
If a block fails, it would be nice to know the specific circumstances of the failure. First, was it an S4 or earlier crank, a GTS crank, or stroker crank? That matters for the main bearing loads in many ways. The GTS crank, for example, appears to be a design that minimizes production cost and not main bearing loads. Second, was the engine sleeved or with original cylinder towers. Mike's success aside, I am sure that it's possible to sleeve these blocks in a way that weakens them. Third, was that just a thrust bearing failure that caused it? The answer to all of these failures is not "let's make a new block." It might be "let's make a new crankshaft" (the topic of this thread) or "let's not sleeve the engines the wrong way" or "let's not let the thrust bearing fail."
Once Porsche attempted to remove the liners from the 944 engines, they cracked very quickly and proved to be not be reliable. The problem was so bad, that they never released a "sleeved" Alusil cast block.
The Alusil 928 block casting is very brittle. There is relatively little reason to debate that. Minor TBF failure almost always results in large cracks in the blocks, way before the main bearing spins.
Porsche broke 928 engine blocks, in the very early development of the 928 engines, and they were forced to improve the design. Doubtfully, they bothered to engineer the blocks at the current power outputs that we are seeing....much less beyond this point.
I'm always looking to the future. I'm now building cranks with higher rpm potential, designed for lighter bob weights. I've got camshafts and heads that allow increased airflow, which allow higher rpm potential. I'd like to be able to make engines with increased displacement. I'd like to be able to build engines with increased power output.
My feeling is that a block, made from a different material, with separate liners, and designed for use with dry sump is a step forward. It's just my "feeling", based on my experience and what I'm seeing.....no one here is required to pay for the development or buy one.
Hell, there's still people that think Chevy offset rods are correct in a 928 engine....
#291

I don't think anyone is saying that many engines are coming apart "at the seams" per say.
What I am thinking is being discussed is making better designed pieces to bring the next level of performance in.
And what is "Alot of power" and what usage is it seeing? A couple stop light drags? Or day in day out running on a track? (Straight or curvy).
Even F1 motors break. So knowing they spend millions on the smallest details, we know we are going to break stuff.
What I am thinking is being discussed is making better designed pieces to bring the next level of performance in.
And what is "Alot of power" and what usage is it seeing? A couple stop light drags? Or day in day out running on a track? (Straight or curvy).
Even F1 motors break. So knowing they spend millions on the smallest details, we know we are going to break stuff.
#292
Nordschleife Master

In the case of the 924GTR project, it may be that changing the alloy was much cheaper than making new molds. It's possible that slightly changing the design and molds would have worked as well. Since I've not even read about the project, let alone being involved with it, this is of course pure speculation. $2 and my speculation gets you a venti cup of coffee at SBUX.
I wouldn't discount the importance of crankshaft design when working out the main bearing loads. The GTS crankshaft is an example of what happens when an accountant and not an engineer designs a crankshaft. The S4 crankshaft is better, but I believe that even S4 counterweight design could be changed to produce lower main bearing loads. Which is not inconsistent with the main topic of this thread.
Finally, I'd just repeat the points that data about blocks cracking is much more useful if we know the exact circumstances of the failures.
Last edited by ptuomov; 12-06-2012 at 04:42 PM.
#293
Drifting
#294
Nordschleife Master

The question however is whether that's the best use for the next $25k or $50k if one wants to make more power with 928s reliably. An aftermarket custom block or something else? Without any exact factual basis, I feel that improving the oiling and cooling further from the current state of the art, for example, would give one a better bang for the buck in terms of reliability. Just an opinion.
#295
Former Sponsor
Thread Starter

Undoubtedly, anything can be improved with an intelligent application of $$$. With top talent engineering effort and lots of that $$$ one could probably make a block that would be better than the Porsche 928 block (but also higher variable cost to produce.)
The question however is whether that's the best use for the next $25k or $50k if one wants to make more power with 928s reliably. An aftermarket custom block or something else? Without any exact factual basis, I feel that improving the oiling and cooling further from the current state of the art, for example, would give one a better bang for the buck in terms of reliability. Just an opinion.
The question however is whether that's the best use for the next $25k or $50k if one wants to make more power with 928s reliably. An aftermarket custom block or something else? Without any exact factual basis, I feel that improving the oiling and cooling further from the current state of the art, for example, would give one a better bang for the buck in terms of reliability. Just an opinion.
I've got customers that don't blink at buying a "new" $100,000 Cup Engine and remove their perfectly good existing engine...just to gain 20 hp.
"Bang for the buck" is a relative thing.
I know this. I was approached by a client that was considering putting 928 engines into his off shore racing boats. I could certainly make the required horsepower and I could certainly have the engines turn the required rpms. However, from what I'd seen and what I'd experienced, I was not convinced(actually, quite the opposite) that I could build an engine whose block would survive the constant high rpm pounding.
There's also a class of off road race cars that could benefit from a nice 750hp, super reliable, 928 engine.....
I'm always moving forward, never trying to move backwards or sideways.
My next big development will be to put 700-750HP 928 engine that will turn 8,000rpms, into a flatbottom.....and go run the **** out of it....to see how it works.
I'm not going to even atttempt to do this with a stock engine block. From my eyes, that would be a complete waste of time.
#296

Mike Simard is a very intelligent human and I respect his efforts. That being said, I'm not convinced that his one experiment with a block is an answer, in itself. I'm also not convinced he has enough "hours" on this engine to prove or disprove anything.
Once Porsche attempted to remove the liners from the 944 engines, they cracked very quickly and proved to be not be reliable. The problem was so bad, that they never released a "sleeved" Alusil cast block.
Once Porsche attempted to remove the liners from the 944 engines, they cracked very quickly and proved to be not be reliable. The problem was so bad, that they never released a "sleeved" Alusil cast block.
So some of the important features of Mike's engine are very light conrods, very light pistons, mind you these are very expensive parts. The other factor that I feel is important, is his use of a long rod, while the stroke of his crankshaft is relatively long. I think 3.7"? The better rod to stroke that Mike has over the older traditional strokers (which I believed used 5.85" off the shelf chevy rods) lowers mass or stress forces.
If one inputs into a piston acceleration calculator, two engines, one with Mike's components and the other with traditional parts and then input 8,000 rpm which I believe Mike's engine can rev to. You get substantial differences in load forces regarding negative piston G forces. You need then to take the totals of the G forces and multiply them by the bob weight.
Given there doesn't seem to be a huge difference in G forces but when the increased G force is multiplied by the heavier weight in the traditional stroker the difference in loadings is quite marked. If the calculator can graph these loads you will see the loads being applied in a more instantaneous manner in the short rod to stroke engine. That in itself may well be a cause for concern, a more uniform and gradual application of force is always better for longevity.Anyway just my thoughts.
#297
Rennlist Member

I tested my gen 1 8 cwt stroker crank for high rpm (8000) use in 1995 against a stock 6 cwt 928 crank to identify potential failure modes, and validated Porsched predictions/recommendations. The gts crank is 8 cwt design for darn good reasons.
The block is a 1970 level design, strong on some areas, not so strong in others.
Mikes mods are consistent with known improvements.
The block is a 1970 level design, strong on some areas, not so strong in others.
Mikes mods are consistent with known improvements.
#298
Rennlist Member
Rennlist Site Sponsor

An additional data point that may or may not be germane - the first application of the Reynolds alloy was in 7- and 8-liter Chevy Can-Am engines. They did right well in the McLarens.
#299
Nordschleife Master

In my opinion, the only logical reason why the GTS crank looks the way it does is a dramatic cost cutting effort by the accounting team putting significant constraints on the engineering team. Eight counterweights or six counterweigths, the GTS crank design unnecessarily (other than manufacturing cost savings) puts high bearing loads on the main journals and that part of the block. So I guess I disagree with you on why GTS crank looks the way it looks.
Below is post on the topic in another forum by a person who models stuff like this for living. He's description of a poor but cheap crankshaft design matches the 928 GTS crankshaft pretty much exactly.
Just my opinion, with the usual caveats applying double.
---
http://speedtalk.com/forum/viewtopic.php?t=8980
Crankshaft Counterweight Design
by SchmidtMotorWorks » Thu Jan 10, 2008 3:27 pm
Here are two images to show different ways of designing counterweights to balance for the same engine and bob weights.
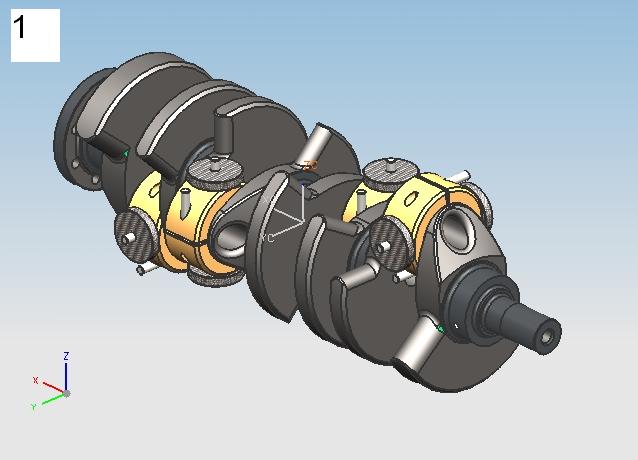
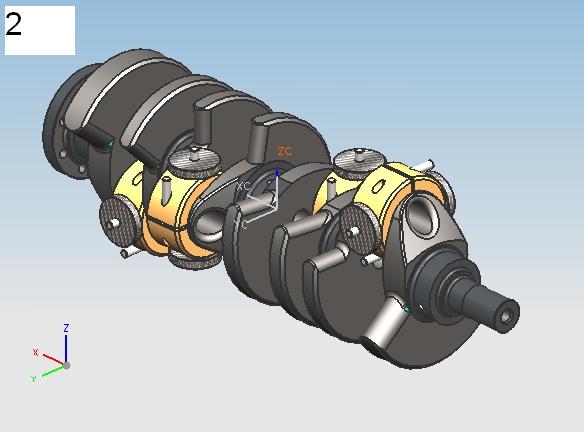
The main differences are:
In design 1, the CWs are positioned more closely to opposite of the nearest rod pin. This way is heavier, more expensive to balance because it usually needs heavy metal but it has lower bearing loads on all journals.
In design 2, the CWs are biased to being opposite of the nearest end rod pin this way can be lighter, rarely requires heavy metal but has higher bearing loads.
These differences are actually understated compared to the crank designs that were popular in the 70's. I think the most extreme of type 2 were Moldex. There was a cast crank made for 392s in the 60s made by Reath? that had a CW design like #1.
Forged cranks are rarely like #1 because it is a very difficult / expensive shape to forge.
SchmidtMotorWorks
Posts: 7794
Joined: Mon Apr 11, 2005 1:30 am
Location: Balboa California / Stuttgart Germany
---
#300
Race Director

750hp 928 engine at 8000rpm....thats only 492ftlbs.....that seems quite possible....its just a matter of how long it will live?
I think Mercruiser came out with a big displacement 4V twin turbo engine....1350hp..
http://www.mercuryracing.com/sterndr...1350/specs.php
I think Mercruiser came out with a big displacement 4V twin turbo engine....1350hp..
http://www.mercuryracing.com/sterndr...1350/specs.php