My IMS Solution DIY installation thread...
#76
Former Vendor

It's clear this guy is a Follower of someone who develops intake products using a shop vac set on "blow" instead of "suck".
It's funny how he discounted all the aspects of the Alan Retrofit kit, but then chose a cheap ceramic hybrid bearing anyway!
He gives the LN tool kit an unfair review, because that tool kit is made to be used over and over again in a shop format. I've been using my first set of tools since 2007 and after over 600 retrofit procedures they still are not worn out! That included the very first commercially retrofitted engine in the world.
Like most, this guy is a reader, and a follower. He sits behind a screen and thinks that he is superman because he can read a bunch of web postings and form an "expert opinion". That's the kind of guy that pisses me off.
#77
Rennlist Member

Originally Posted by Flat6 Innovations
He gives the LN tool kit an unfair review, because that tool kit is made to be used over and over again in a shop format. I've been using my first set of tools since 2007 and after over 600 retrofit procedures they still are not worn out! That included the very first commercially retrofitted engine in the world.
The price of ANYTHING is based on far more than basic material cost...
#78

Yea, the IMS Solution was glaringly omitted. Probably not the price range he was considering. It still blows my mind why people are so confident about running their own experiments
Boxster engines are pretty cheap so maybe that's why.
To his credits though, he posts a lot of DIY videos and you can see his home-made IMS tool here @ 6:42s
Not a fair comparison like you said.

To his credits though, he posts a lot of DIY videos and you can see his home-made IMS tool here @ 6:42s
Not a fair comparison like you said.
#79

I hate how people also dismiss the value of intellectual property and R&D time. While I wasn't there, I would imagine you all didn't wake up one morning and crank these Tools out without a lot of testing and broken engines/parts.
The price of ANYTHING is based on far more than basic material cost...
The price of ANYTHING is based on far more than basic material cost...
#80

Most internet reviews are flawed for the most part on anything these days. You don't need to be an expert to review anything these days or have logged x amount of time and have x amount of experience.
It's like a newbie giving a review of the 996 here that's only previously owned econobox's like an Accord and having him say the 996 handles like rails and is fast as $hit.
The dangerous part though is we have too many sheeps in this world that follow these people.
It's like a newbie giving a review of the 996 here that's only previously owned econobox's like an Accord and having him say the 996 handles like rails and is fast as $hit.
The dangerous part though is we have too many sheeps in this world that follow these people.
#81
Race Director

Oh, god, no, not that guy again. He's the one whose voice and cadence makes me want to kill myself.
When he's lauding the DOF, he also mentions the wonderful option of "sourcing your own bearing" for retrofit and ultimately congratulates himself for doing just that. That ALWAYS works out well...
An 18 minute video to present two minutes' worth of content masquerading as "research" when the guy makes up information for any details he doesn't actually know...the cylindrical ball bearing, for example, is eliminated because it is "dicey" to use a different type of bearing, and the oil pump is "weakened" although - obviously - no data is offered to validate this claim. I detest sh*t like this. At least Pedro uses Mega Maid (er, I mean a shop vac) switched from suck to blow and some foam chips instead of unsubstantiated conjecture.
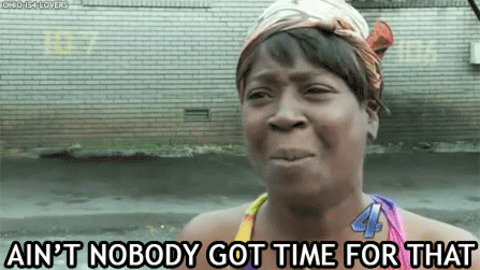
I also liked the part about the Solution being too new-and-untested to include - never mind that as far as I know there are no statistics about any of the other products he "evaluated." So instead of using this untested solution, he rolled his own. Because that, of course, is much more reliable.
To his credit, he uses just as much fact and logic as the anti-vaxxers. Maybe that's why he skipped over the Solution - it probably causes the autism real bad.
"Certainly Porsche didn't think that [splash lubrication] was enough, because they sealed the bearing to hold oil into the bearing." Yes, this definitely convinces me that this dude is an unimpeachable source of information.
TL;DR: Assclown who giggles about how clever he is at 14:00.
An 18 minute video to present two minutes' worth of content masquerading as "research" when the guy makes up information for any details he doesn't actually know...the cylindrical ball bearing, for example, is eliminated because it is "dicey" to use a different type of bearing, and the oil pump is "weakened" although - obviously - no data is offered to validate this claim. I detest sh*t like this. At least Pedro uses Mega Maid (er, I mean a shop vac) switched from suck to blow and some foam chips instead of unsubstantiated conjecture.
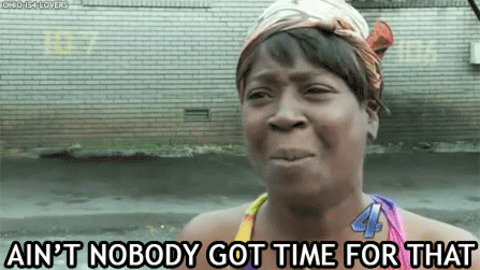
I also liked the part about the Solution being too new-and-untested to include - never mind that as far as I know there are no statistics about any of the other products he "evaluated." So instead of using this untested solution, he rolled his own. Because that, of course, is much more reliable.
To his credit, he uses just as much fact and logic as the anti-vaxxers. Maybe that's why he skipped over the Solution - it probably causes the autism real bad.
"Certainly Porsche didn't think that [splash lubrication] was enough, because they sealed the bearing to hold oil into the bearing." Yes, this definitely convinces me that this dude is an unimpeachable source of information.
TL;DR: Assclown who giggles about how clever he is at 14:00.
Last edited by 5CHN3LL; 07-28-2016 at 07:33 PM.
#83
Rennlist Member
Thread Starter

Figured it was time to post an updated and get things back on topic. I've been a little slow to progress lately as I wait for some parts to be delivered. I got a decent amount of work done this weekend though and have everything I need parts-wise with a few exceptions.
Installing the IMS Solution - thanks to the great video and instructions that came with the product, went relatively smoothly. In fact, this was the easiest part of the job thus far. For anyone questioning the value/investment of buying the proper toolkits from LN Engineering, don't be penny wise and pound foolish. Even if you manage to get everything installed correctly with home made solutions, the amount of extra time frustration and headache still put you in the negative - and that is your BEST case scenario. Not to mention these tools are quality and can easily be sold (I believe) after you complete the job for close to what you paid for them.
I installed the little cap in the end of the IMS shaft using the tool that sets it to the appropriate depth - everything went perfect. Next up was the bushing/bearing itself. I applied the lube provided and bolted it to the installation tool.
It took some patience and some pounding to get the bearing fully inserted. Due to the confined space under the car it was difficult to get leverage and a full swing in with the rubber mallet.
Once the bearing was in I added the protective shim and snap ring (the snap ring install was an absolutely BREEZE with my new craftsman ring pliers - do not go cheap on these or you'll regret it).
Next I installed the oil fitting to the flange, lubricated and put it in place. I quickly realized that I did not take enough material off the left side of the crank case for the oil fitting to fully clear. This sucks because now the engine block is open/exposed - not the best time to be filing. To help prevent contaminants from getting where they shouldn't, I taped over the IMS opening and proceeded to file + I remembered I have a cordless dremel tool with cutting discs so that helped make quick work of it. I found that I had to remove more material than shown in the video and instructions - even some lower down - required for the oil line head to be able to spin on (see pic). After taking off more material I got my Dyson and vacuumed then wiped everything down the best I could before removing the tape and continuing.
Due to my space constraints I used the flange bolts to pull the flange fully flush with the crank case. The instructions say to lightly tap with a mallet but I opted to use the bolts by slowly going around and tightening them a little bit at a time. It worked great.
Next up was the oil filter adapter. This is a very cool and nicely machined piece. I put it on and found that my crank case oil threading is improperly indexed. The hole for the oil feed line pointed directly at the block. No worries, the kit came with a shim just for this purpose! Unfortunately I guess mine is a really odd duck because while the shim rotated everything in the right direction, it still wasn't far enough to finish the install. I emailed LN Engineering and receive a reply back almost immediately (on a Sunday!) stating this is uncommon but happens, they included instructions to measure what angle the assembly needs to be rotated and they are shipping out a shim for me Monday (awesome).
So, with that piece of the project on hold, I cleaned up the timing chain tensioners, submerged them in clean oil and pumped them and set to reinstall them. Things seem to go back together much faster. With those installed I removed the cam lock and installed a new plug on the hole.
Next up I installed the flywheel, clutch and pressure plate. The flywheel bolts have a torque spec and then get turned an extra 120 degrees. I marked each bolt (after torquing) at 6pm with white nail polish, that made it much easier to measure the correct angle since I was using a non-ratcheting breaker bar to tighten them.
That being said, I may have made a stupid mistake that requires pulling the flywheel and clutch off again. When I retorqued the flange bolts, I did not re-check the center nut. EDIT: I removed the flywheel and the center nut was torqued properly. Just an example of not double checking and then needing to go back to be sure - to avoid worrying about it for the rest of my life.
Installing the IMS Solution - thanks to the great video and instructions that came with the product, went relatively smoothly. In fact, this was the easiest part of the job thus far. For anyone questioning the value/investment of buying the proper toolkits from LN Engineering, don't be penny wise and pound foolish. Even if you manage to get everything installed correctly with home made solutions, the amount of extra time frustration and headache still put you in the negative - and that is your BEST case scenario. Not to mention these tools are quality and can easily be sold (I believe) after you complete the job for close to what you paid for them.
I installed the little cap in the end of the IMS shaft using the tool that sets it to the appropriate depth - everything went perfect. Next up was the bushing/bearing itself. I applied the lube provided and bolted it to the installation tool.
It took some patience and some pounding to get the bearing fully inserted. Due to the confined space under the car it was difficult to get leverage and a full swing in with the rubber mallet.
Once the bearing was in I added the protective shim and snap ring (the snap ring install was an absolutely BREEZE with my new craftsman ring pliers - do not go cheap on these or you'll regret it).
Next I installed the oil fitting to the flange, lubricated and put it in place. I quickly realized that I did not take enough material off the left side of the crank case for the oil fitting to fully clear. This sucks because now the engine block is open/exposed - not the best time to be filing. To help prevent contaminants from getting where they shouldn't, I taped over the IMS opening and proceeded to file + I remembered I have a cordless dremel tool with cutting discs so that helped make quick work of it. I found that I had to remove more material than shown in the video and instructions - even some lower down - required for the oil line head to be able to spin on (see pic). After taking off more material I got my Dyson and vacuumed then wiped everything down the best I could before removing the tape and continuing.
Due to my space constraints I used the flange bolts to pull the flange fully flush with the crank case. The instructions say to lightly tap with a mallet but I opted to use the bolts by slowly going around and tightening them a little bit at a time. It worked great.
Next up was the oil filter adapter. This is a very cool and nicely machined piece. I put it on and found that my crank case oil threading is improperly indexed. The hole for the oil feed line pointed directly at the block. No worries, the kit came with a shim just for this purpose! Unfortunately I guess mine is a really odd duck because while the shim rotated everything in the right direction, it still wasn't far enough to finish the install. I emailed LN Engineering and receive a reply back almost immediately (on a Sunday!) stating this is uncommon but happens, they included instructions to measure what angle the assembly needs to be rotated and they are shipping out a shim for me Monday (awesome).
So, with that piece of the project on hold, I cleaned up the timing chain tensioners, submerged them in clean oil and pumped them and set to reinstall them. Things seem to go back together much faster. With those installed I removed the cam lock and installed a new plug on the hole.
Next up I installed the flywheel, clutch and pressure plate. The flywheel bolts have a torque spec and then get turned an extra 120 degrees. I marked each bolt (after torquing) at 6pm with white nail polish, that made it much easier to measure the correct angle since I was using a non-ratcheting breaker bar to tighten them.
That being said, I may have made a stupid mistake that requires pulling the flywheel and clutch off again. When I retorqued the flange bolts, I did not re-check the center nut. EDIT: I removed the flywheel and the center nut was torqued properly. Just an example of not double checking and then needing to go back to be sure - to avoid worrying about it for the rest of my life.
Last edited by charlieaf92; 08-03-2016 at 12:46 AM.
#84
Rennlist Member
Thread Starter

Here are the pics. The first pic shows the flange as far as I was able to push it on by hand. Subsequent pics of are flange fully seated and flush with bolts tightened and oil fitting installed. I tried to get a shot showing where I had to remove material to make room for the oil feed line to screw onto the fitting. Final pic is of the brand new pressure plate / clutch / flywheel that are unfortunately coming back off tomorrow. Better to backtrack now and make sure everything is right vs. find out the hard way when its all back together.
Last edited by charlieaf92; 08-03-2016 at 12:42 AM.
#85
Rennlist Member
Thread Starter

Alright - we're getting towards the end of this project. Today the new shim arrived from LN Engineering (shipped overnight, at no cost to me, no questions asked - great service!). The shim worked perfectly and I now have the oil adapter and feed line hooked up. Since the creation of the IMS Solution install video it appears they switched from a feed line that the installer cuts/sizes to a pre-sized one. This one proved to be a little longer than I would have liked and the result is it kind of has to bow out in a horseshoe shape and part of it is touching the top of the rear sway bar. My only alternative was to have it stick down, below the sway bar - and that seems like a more risky alternative as it can get easily damaged and snagged. The hose is shrouded in stainless so I don't expect it to be an issue but definitely will be something I check from time to time.
Next up I removed my pressure plate / clutch / flywheel again to double check the torque of the center nut. It was tight. So, basically I was worried for no reason but I feel much better knowing for certain. New bolts are on order so I'm in a holding pattern at the moment.
I'm using that time to address a separate issue (front diff seal leaks) and pulled out the front differential tonight. It was quite a bit easier than the transmission pull and I plan to add some of the details to a separate thread.
Cheers
Charlie
Next up I removed my pressure plate / clutch / flywheel again to double check the torque of the center nut. It was tight. So, basically I was worried for no reason but I feel much better knowing for certain. New bolts are on order so I'm in a holding pattern at the moment.
I'm using that time to address a separate issue (front diff seal leaks) and pulled out the front differential tonight. It was quite a bit easier than the transmission pull and I plan to add some of the details to a separate thread.
Cheers
Charlie
#86
Former Vendor

Alright - we're getting towards the end of this project. Today the new shim arrived from LN Engineering (shipped overnight, at no cost to me, no questions asked - great service!). The shim worked perfectly and I now have the oil adapter and feed line hooked up. Since the creation of the IMS Solution install video it appears they switched from a feed line that the installer cuts/sizes to a pre-sized one. This one proved to be a little longer than I would have liked and the result is it kind of has to bow out in a horseshoe shape and part of it is touching the top of the rear sway bar. My only alternative was to have it stick down, below the sway bar - and that seems like a more risky alternative as it can get easily damaged and snagged. The hose is shrouded in stainless so I don't expect it to be an issue but definitely will be something I check from time to time.
Next up I removed my pressure plate / clutch / flywheel again to double check the torque of the center nut. It was tight. So, basically I was worried for no reason but I feel much better knowing for certain. New bolts are on order so I'm in a holding pattern at the moment.
I'm using that time to address a separate issue (front diff seal leaks) and pulled out the front differential tonight. It was quite a bit easier than the transmission pull and I plan to add some of the details to a separate thread.
Cheers
Charlie
Next up I removed my pressure plate / clutch / flywheel again to double check the torque of the center nut. It was tight. So, basically I was worried for no reason but I feel much better knowing for certain. New bolts are on order so I'm in a holding pattern at the moment.
I'm using that time to address a separate issue (front diff seal leaks) and pulled out the front differential tonight. It was quite a bit easier than the transmission pull and I plan to add some of the details to a separate thread.
Cheers
Charlie
That's why I stepped away. That's why I always step away.
#87
Rennlist Member

No IMS Solution kits have ever been sold with the user- assembled hose. That was added to the video because I was adamant about the user assembling the hose. This was simply because I would have lost my mind if someone blamed a hose for something negative that occurred with a kit.
That's why I stepped away. That's why I always step away.
That's why I stepped away. That's why I always step away.
The first thing that came to my mind when I saw the solution for the firs time, was WOW! Jack out did him self, designing a solution that acutely remove the caus of the problem.
The second thought was, what happens if the hose breaks?
Every chain is strong as its weakest link.
That hose is defenetly the weakest link in the chain.
Although I'm sure the chance for it to fail is slim to none, I was wondering what is the point that the engine fails (if at all), when the oil feed is cut to the bearing?
Scenario:
I got the solution installed. The mechanic forgot to tighten the hose.
500 miles later, it disconnects. Oil pressure light comes on.
How long from no oil to kabum?
I know I know. I will loose some oil pressure befor, I will see a puddle on the grage floor long before the hose will completely disconnect and so on.
But just for the sake of the argument.
I'm sur you preformed that test during R&d, and wonder what was the result.
Thanks in advance.
And kudos to Charlie.

#88
Rennlist Member
Thread Starter

Defenetly a smart move. The first thing that came to my mind when I saw the solution for the firs time, was WOW! Jack out did him self, designing a solution that acutely remove the caus of the problem. The second thought was, what happens if the hose breaks? Every chain is strong as its weakest link. That hose is defenetly the weakest link in the chain. Although I'm sure the chance for it to fail is slim to none, I was wondering what is the point that the engine fails (if at all), when the oil feed is cut to the bearing? Scenario: I got the solution installed. The mechanic forgot to tighten the hose. 500 miles later, it disconnects. Oil pressure light comes on. How long from no oil to kabum? I know I know. I will loose some oil pressure befor, I will see a puddle on the grage floor long before the hose will completely disconnect and so on. But just for the sake of the argument. I'm sur you preformed that test during R&d, and wonder what was the result. Thanks in advance. And kudos to Charlie. 

#89

The rest of the engine would explode before the Solution would self destruct from no oil pressure. Jake has tested the coating on the plain bearing under the worst conditions including no oil. Its in a thread somewhere.
#90
Former Vendor

Pressure" down for the count.
How about a video of an engine (under he car) running idle to 6,000 RPM with no oil hose even attached? How about oil dripping out of the solution flange oil port from inside the engine while running 6,000 RPM? I drove the car 20 miles and dynoed it for 3 hours straight with NO OIL supply.. Then pulled it apart... Yes it had wear, but he wear was only of the coating and was only visual, and not measurable.
Been there, done that.. Just to shut up one argument from people that can't find anything else wrong with the IMS Solution.
Ever worked on a turbine engine??? Know how many hoses are there feeding bearings on the engine?
Yes, the IMS Solution hose is an Aerospace unit. It's rated for hundreds more PSI than the M96 engine is capable of producing.
Yep... It wouldn't be the 996 forum on RL without a doubter and a hater... Where's the hater??? He just hasn't spoken up yet. He will.