85 Timing Belt / WP - Here Goes Nothin
#76
Three Wheelin'
Thread Starter

It didn't come out with the old roller. Managed to rescue the carcass of the old pump and see the bushing. What's the best method to remove it without damaging it? There's no room to get behind it to lever it off. Heat and vice grips wrapped in a towel??
#77
Under the Lift
Lifetime Rennlist
Member
Lifetime Rennlist
Member

I don't think you will have much luck with heating this. Heat is unlikely to help as the aluminum boss may expand more than the steel sleeve. I would get the bushing off even if it mars it's outside surface. This is not a sealing or moving surface, so any proud nicks on the bushing can be sanded or filed down flush even if it doesn't look too nice. I believe this roller is sold with this bushing per photos on 928 International.
Similar report..
https://rennlist.com/forums/928-foru...ller-boss.html
Similar report..
https://rennlist.com/forums/928-foru...ller-boss.html
#78
Three Wheelin'
Thread Starter

I don't think you will have much luck with heating this. Heat is unlikely to help as the aluminum boss may expand more than the steel sleeve. I would get the bushing off even if it mars it's outside surface. This is not a sealing or moving surface, so any proud nicks on the bushing can be sanded or filed down flush even if it doesn't look too nice.
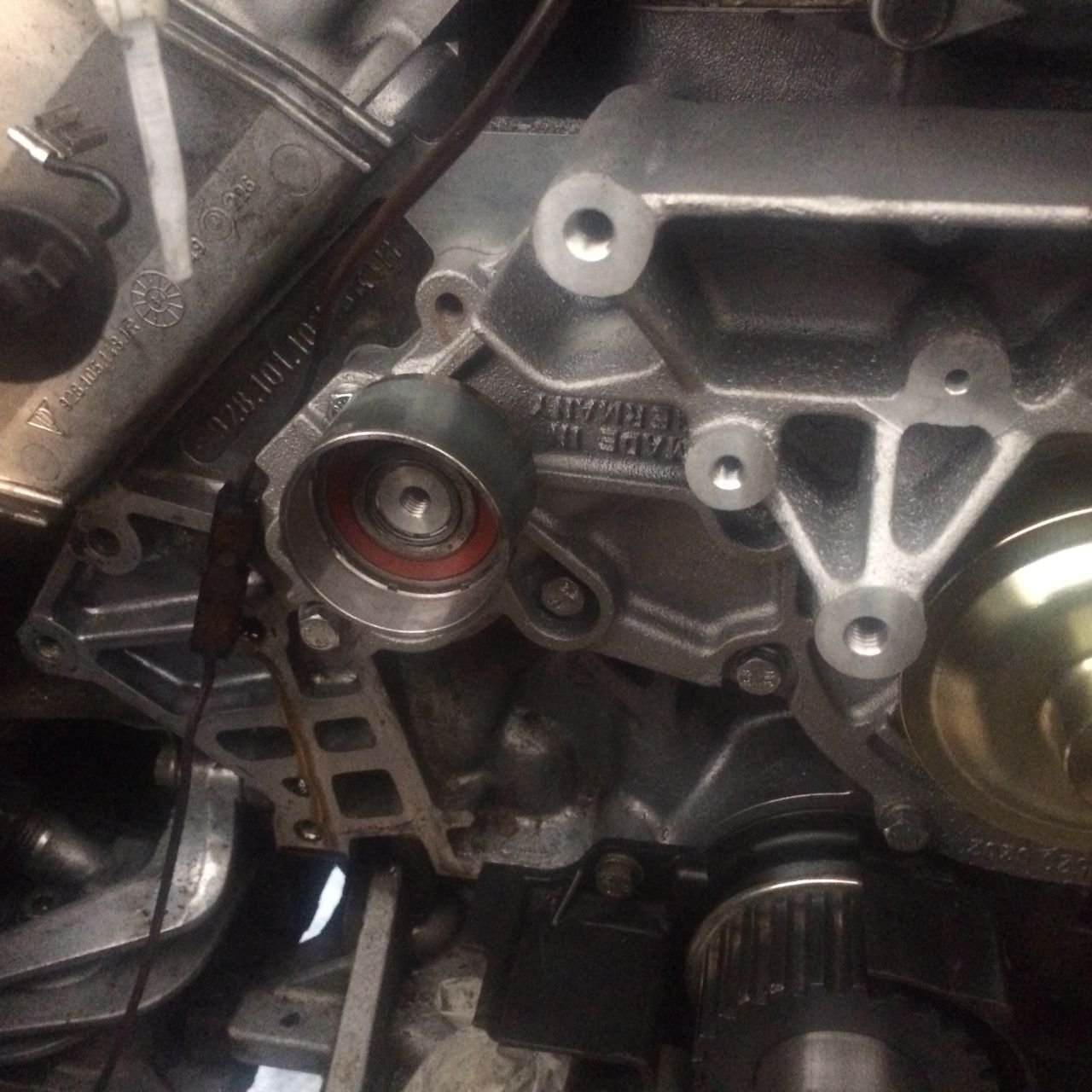
#81
Burning Brakes

No worries Bill- I did a double-take when I saw my thumb, and then my wall... I didn't remember taking that picture!
Yeah, Scott, I should have credited you. It's from your epic thread...
https://rennlist.com/forums/928-foru...rst-timer.html
https://rennlist.com/forums/928-foru...rst-timer.html
#82
Three Wheelin'
Thread Starter

Question for those of you who lock the crank at TDC for this job - when removing the belt both cams rotated about four teeth outboard (clockwise on the left side and counterclockwise on the right side)- for the left cam am I ok rotating counter clockwise (using the cam gear washer and not the bolt) to line up the timing mark while stringing the belt or should I go all the way around clockwise? Obviously on the right side I will just rotate clockwise.
#83
Team Owner

from the info provided you can put the cams back into time.
turning them back from whence they came is OK.
Always use the 30mm washer to turn the cams dont use the 17mm bolt
NOTE do not do any full revolutions of the cams unless the crank is at 45deg BTDC
NOTE it may be helpful to have a helper to hold one of the cams in position,
and or zip tie the driver side belt to the cam pulley
turning them back from whence they came is OK.
Always use the 30mm washer to turn the cams dont use the 17mm bolt
NOTE do not do any full revolutions of the cams unless the crank is at 45deg BTDC
NOTE it may be helpful to have a helper to hold one of the cams in position,
and or zip tie the driver side belt to the cam pulley
#84
Chronic Tool Dropper
Lifetime Rennlist
Member
Lifetime Rennlist
Member

So the "!!never counterclockwise!!" rule applies to crank and cams tied together with the belt installed. The concern is that turning the crank counterclockwise pulls directly on the tensioner, collapsing it enough to let the belt start to jump teeth on the passenger side sprocket. If the belt starts walking up on the gear rather than fitting in the grooves, the cam nose breaks off with the gear. With the belt off, you can move the cams in either direction with no worries, --so long as no pistons are at the top of their stroke--.
Howeever, with the crank locked at TDC #1, there's at least 1 other cylinder with piston at the top, so there are two cylinders with potential valve damage if the cams move. Why risk it?
On the interference engines, Porsche thought this a big enough concern that they added the 45º BTDC mark on the balancer, and shared a procedure to remove and install the belt only when the crank is locked at that "safe" position. Just mark your gears with a paint mark, or count teeth if you failed to mark or are installing new gears. Then when valve springs and cam lobes conspire to roll the cams a little with the belt off, you can just use a wrench on the washer flats to rotate the cams as you string the belt.
I find that getting the cam timing marks lined up correctly isn't that tough. I pull the belt snug from crank through oil pump drive towards the left gear (driver's side on US cars), and rotate the cam one tooth clockwise from where it's easy to get the belt on. Once the belt is on the gear, rotate the same cam counterclockwise with the wrench to tighten the belt in that section, and look to see how the marks line up. If you are off a tooth, lift the belt loose from that gear, rotate the cam as needed, belt goes back on, pull the gear counterclockwise to remove slack, and verify that the gear is in the proper position with marks lined up. I've used tie-wraps to hold the belt to the gear then, or small woodworker's spring clamps. You can use metal binder's clamps from the box over your desk. That way the belt stays engaged with the gear as you do the right (passenger's side on US cars) side cam the same way. More spring clamps or a cable tie as needed, so you can set up the tensioner if it isn't already in place. Since you used the wrench in the cam gears to tension the two sections of belt before any serious tensioning with the tensioner, the cams are already in correct 'time' with the crankshaft. All of this is done with crank at 45ºBTDC. Once you are sure that the cams are indexed correctly, only then remove the crank lock tool, and gently turn the crank the 45º to the TDC mark before you start the more serious adjustment on the tensioner.
Bottom line is that there is no good reason to have the crank at any position other than 45ºBTDC while the belt is off. In My Opinion anyway.
Howeever, with the crank locked at TDC #1, there's at least 1 other cylinder with piston at the top, so there are two cylinders with potential valve damage if the cams move. Why risk it?
On the interference engines, Porsche thought this a big enough concern that they added the 45º BTDC mark on the balancer, and shared a procedure to remove and install the belt only when the crank is locked at that "safe" position. Just mark your gears with a paint mark, or count teeth if you failed to mark or are installing new gears. Then when valve springs and cam lobes conspire to roll the cams a little with the belt off, you can just use a wrench on the washer flats to rotate the cams as you string the belt.
I find that getting the cam timing marks lined up correctly isn't that tough. I pull the belt snug from crank through oil pump drive towards the left gear (driver's side on US cars), and rotate the cam one tooth clockwise from where it's easy to get the belt on. Once the belt is on the gear, rotate the same cam counterclockwise with the wrench to tighten the belt in that section, and look to see how the marks line up. If you are off a tooth, lift the belt loose from that gear, rotate the cam as needed, belt goes back on, pull the gear counterclockwise to remove slack, and verify that the gear is in the proper position with marks lined up. I've used tie-wraps to hold the belt to the gear then, or small woodworker's spring clamps. You can use metal binder's clamps from the box over your desk. That way the belt stays engaged with the gear as you do the right (passenger's side on US cars) side cam the same way. More spring clamps or a cable tie as needed, so you can set up the tensioner if it isn't already in place. Since you used the wrench in the cam gears to tension the two sections of belt before any serious tensioning with the tensioner, the cams are already in correct 'time' with the crankshaft. All of this is done with crank at 45ºBTDC. Once you are sure that the cams are indexed correctly, only then remove the crank lock tool, and gently turn the crank the 45º to the TDC mark before you start the more serious adjustment on the tensioner.
Bottom line is that there is no good reason to have the crank at any position other than 45ºBTDC while the belt is off. In My Opinion anyway.
#85
Three Wheelin'
Thread Starter

So after quite a few fits and starts, Bill made his way out to Hollister last weekend to help with the stringing of the belt and cam timing. Everything pretty much went to plan, however I have the following observations:
1) I don't see how it's possible to string the belt as a one person job - it took every one of our four hands to hold the left cam gear on time while barely sneaking the leading edge of the belt over the right cam gear so that it could be slid the rest of the way onto the gear. Even then I had to give up my task on the right side and have Bill do it as I could not get it more than 3/4 engaged after 10 minutes of struggling with it. Bill had it on with a bit of effort in less than half of that time.
2) Never ever say "I'll get the proper torque on this bolt later." Inevitably you will forget and (if you are lucky) wake up in the middle of the night realizing that the shoulder bolt never got torqued down properly. Yes, that means you have to strip everything back down so you can get a torque wrench on it. Fortunately by now you are getting good at dis/re-assembly so it only takes you 3.5 hours total to get 20nm (about a flat and a half) on that bolt.
3) Order every possible belt and hose, even the thermostat to reservoir hose that you replaced 10k miles ago because it's definitely going to pinhole on you, causing another several days delay if you don't.
So from beginning to end the job took four weeks, with about half of that spent waiting for parts or Bill to be available to make it down to me. Happily all of the replaced seals and o-rings are dry so far (knock on wood), and the car seems to be running a bit smoother with the new caps and rotors. The plan is to drive it for a few weeks and then start the whole process over again for the intake. Stay tuned for a new thread on that one - thanks for everyone's help, I literally could not have done it without you.
1) I don't see how it's possible to string the belt as a one person job - it took every one of our four hands to hold the left cam gear on time while barely sneaking the leading edge of the belt over the right cam gear so that it could be slid the rest of the way onto the gear. Even then I had to give up my task on the right side and have Bill do it as I could not get it more than 3/4 engaged after 10 minutes of struggling with it. Bill had it on with a bit of effort in less than half of that time.
2) Never ever say "I'll get the proper torque on this bolt later." Inevitably you will forget and (if you are lucky) wake up in the middle of the night realizing that the shoulder bolt never got torqued down properly. Yes, that means you have to strip everything back down so you can get a torque wrench on it. Fortunately by now you are getting good at dis/re-assembly so it only takes you 3.5 hours total to get 20nm (about a flat and a half) on that bolt.
3) Order every possible belt and hose, even the thermostat to reservoir hose that you replaced 10k miles ago because it's definitely going to pinhole on you, causing another several days delay if you don't.
So from beginning to end the job took four weeks, with about half of that spent waiting for parts or Bill to be available to make it down to me. Happily all of the replaced seals and o-rings are dry so far (knock on wood), and the car seems to be running a bit smoother with the new caps and rotors. The plan is to drive it for a few weeks and then start the whole process over again for the intake. Stay tuned for a new thread on that one - thanks for everyone's help, I literally could not have done it without you.
#86
Chronic Tool Dropper
Lifetime Rennlist
Member
Lifetime Rennlist
Member

Glad you were able to get it back together. Bill is a saint! How many folks can get part way through a major project like this and have the cavalry show up to guide you to the finish line?
For next time, wood workers spring clamps or even large metal binder clamps (office supply) hold the belt to the left-side gear while your other two Hans thread it around the rest of the rollers and the other gear.
For next time, wood workers spring clamps or even large metal binder clamps (office supply) hold the belt to the left-side gear while your other two Hans thread it around the rest of the rollers and the other gear.
#87
Three Wheelin'
Thread Starter

Glad you were able to get it back together. Bill is a saint! How many folks can get part way through a major project like this and have the cavalry show up to guide you to the finish line?
For next time, wood workers spring clamps or even large metal binder clamps (office supply) hold the belt to the left-side gear while your other two Hans thread it around the rest of the rollers and the other gear.
For next time, wood workers spring clamps or even large metal binder clamps (office supply) hold the belt to the left-side gear while your other two Hans thread it around the rest of the rollers and the other gear.
#88
Three Wheelin'
Thread Starter

Update:
Yesterday morning I got up to find a puddle about eight inches in diameter of what seemed to be lightweight oil under the front right side of the oil pan. Droplets of the same liquid were were seen on the oil pan as well along with some splashes of fluid on the inner tie rod boot on the same side.
Since the fluid seemed too light to be engine oil I looked at the AC compressor first and indeed it shows signs of the seal leaking - the back side of the pulley was damp and the felt wick was fairly soaked with fluid. I started a thread about how to proceed but in the meantime got the car up on ramps and then noticed that the same moisture was present at the bottom of the tensioner, so crap, time to tear it down again. I decided to try to get the covers off without taking off the coolant hoses to see what was going on and immediately noticed lots of dried coolant under the center cover - it was only then that I noticed a pool of oily coolant located in the valley directly below the coolant bridge and behind the top of the waterpump at the front of the block - the coolant was right up to the top edge of the valley and was being fed by a dripping upper radiator hose that only leaked under pressure. I moved some of this coolant over the edge of the block and sure enough a few seconds later it dripped out right under the tensioner. The coolant became oily after mixing with the remnants of oil that had made it's way there over the years and which for some reason I missed during my cleaning frenzy during the TB/WP job.
I cinched the upper radiator hose clamp down with a 10mm socket and sure enough the bolt took nearly three full revolutions before being considered truly tightened. I went back and did the same with the other clamps and most took at least an additional revolution (I was appropriately gentle with the radiator side of the hoses.) Buttoned everything up and just got back from a 20 minute ride, no additonal drips to be found. Moral of the story is follow the leak upwards till you don't see it any more, an don't assume that that the stuff that looks like oil isn't coolant.
Yesterday morning I got up to find a puddle about eight inches in diameter of what seemed to be lightweight oil under the front right side of the oil pan. Droplets of the same liquid were were seen on the oil pan as well along with some splashes of fluid on the inner tie rod boot on the same side.
Since the fluid seemed too light to be engine oil I looked at the AC compressor first and indeed it shows signs of the seal leaking - the back side of the pulley was damp and the felt wick was fairly soaked with fluid. I started a thread about how to proceed but in the meantime got the car up on ramps and then noticed that the same moisture was present at the bottom of the tensioner, so crap, time to tear it down again. I decided to try to get the covers off without taking off the coolant hoses to see what was going on and immediately noticed lots of dried coolant under the center cover - it was only then that I noticed a pool of oily coolant located in the valley directly below the coolant bridge and behind the top of the waterpump at the front of the block - the coolant was right up to the top edge of the valley and was being fed by a dripping upper radiator hose that only leaked under pressure. I moved some of this coolant over the edge of the block and sure enough a few seconds later it dripped out right under the tensioner. The coolant became oily after mixing with the remnants of oil that had made it's way there over the years and which for some reason I missed during my cleaning frenzy during the TB/WP job.
I cinched the upper radiator hose clamp down with a 10mm socket and sure enough the bolt took nearly three full revolutions before being considered truly tightened. I went back and did the same with the other clamps and most took at least an additional revolution (I was appropriately gentle with the radiator side of the hoses.) Buttoned everything up and just got back from a 20 minute ride, no additonal drips to be found. Moral of the story is follow the leak upwards till you don't see it any more, an don't assume that that the stuff that looks like oil isn't coolant.