Overhaul of waterpump DIY
#1

After posting an earlier thread where I asked for experiences with overhauling the waterpump, I had the feeling that it hasen't been done a lot. Since I'm selfish, I went down that route to find out it was a hard, but nice one.
Main reason for me to do this is to find out whether I succeed. Second reason is the current prices of these pumps, while they're getting more difficult to buy new.
In this post, I'll try to explain what I did. First dismantling the old one and finding the rootcause of it's failure (It had only done 8000 km from new or so...)
Of course, it all started with dismantling the old one. Luckily I have a 10 tons press at work that I could use. When assembled, this is what it looked like:
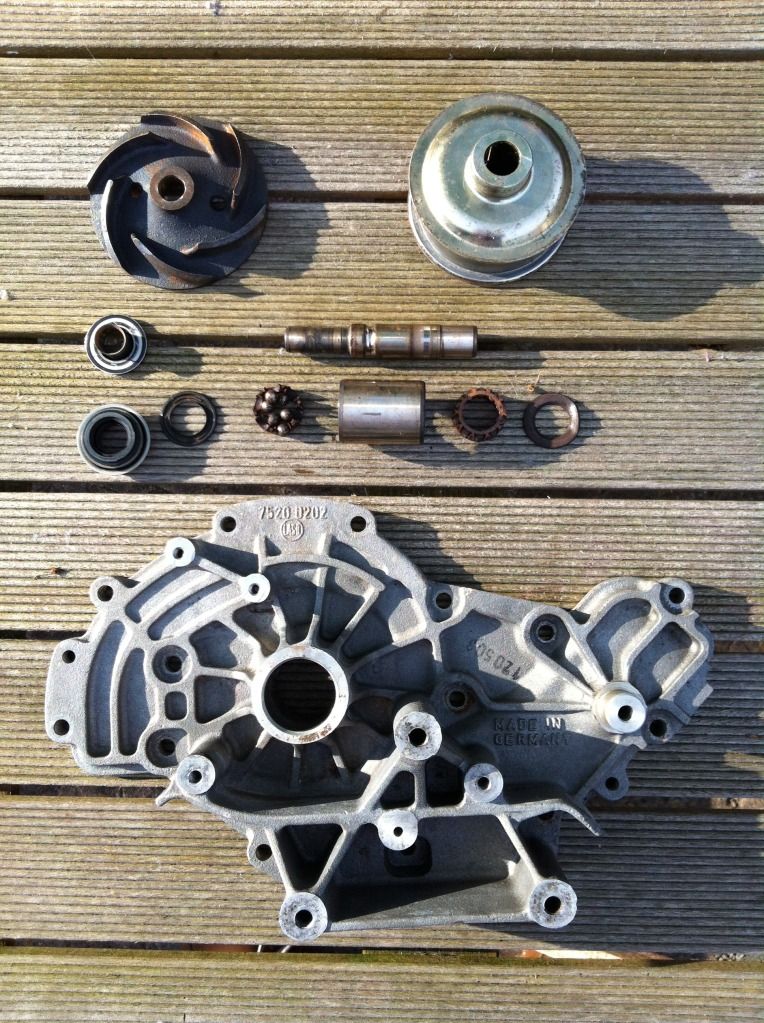
As can be seen, the roller bearing is completely rusted, like many of the rest of the bearing surfaces. The shaft had a lot of play before dismantling, which is probably due to a broken water seal. The seal consists of basically two parts: a ceramic disc and a graphite disc that are pushed on to each other by a spring.
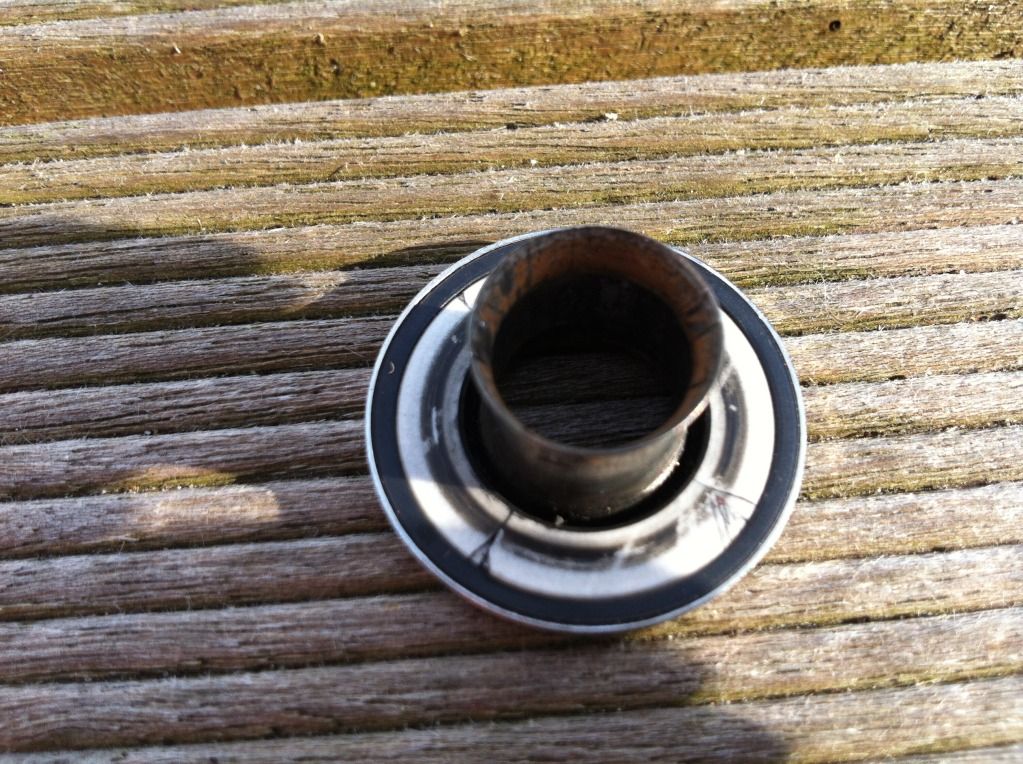
This is the ceramic disc held in a stainless steel container with rubber in between. It it fixed on the shaft and rests with the back (the side resting on the table) on the impeller. The disc is quite thin and is broken in many pieces:
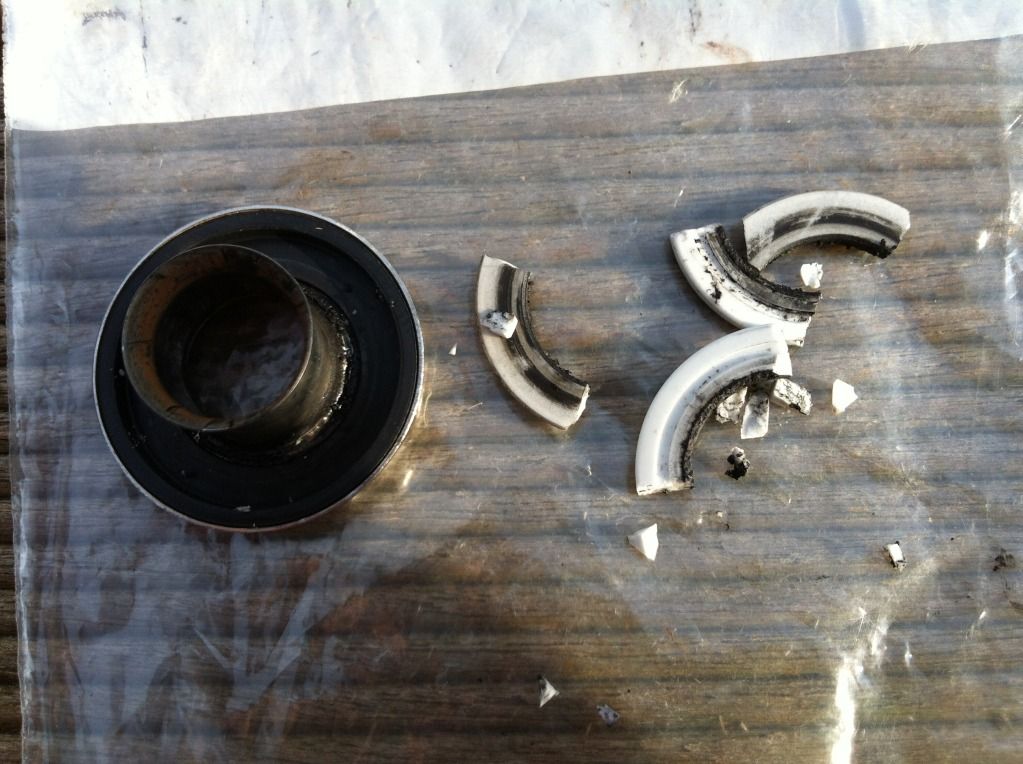
The root cause for the ceramic disc to be broken is probably rust on the impeller, pushing away the stainless holder under the ceramic disc. This way, the ceramic disc is not pushed evenly on it's counterpart, the graphite ring attached to the housing of the pump.
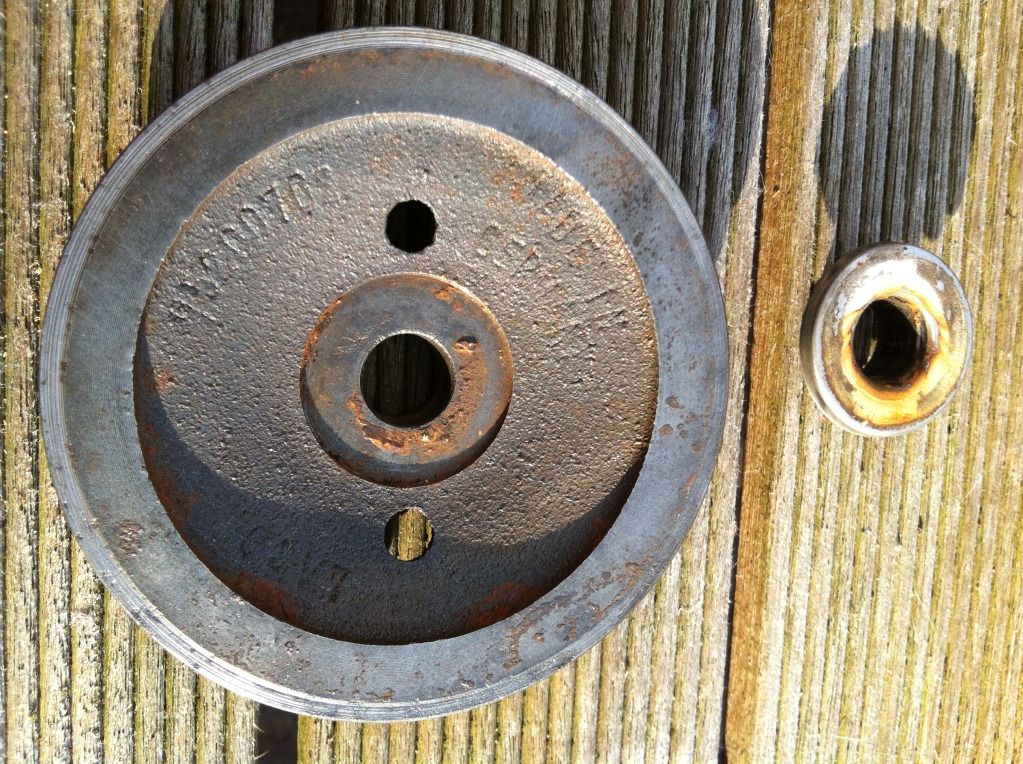
Water can now seep through the water seal, pushing against an oil seal which rests behind it to keep the oil/fat in the bearing. After some time, this seal will fail, because it is not made to keep out (hot) water at pressure. When the cooling water enters the bearings, well than hell breaks loose for those little ***** and shafts inside...
This probably is the reason for pumps with a plastic impeller to have a longer life than metal ones.
Main reason for me to do this is to find out whether I succeed. Second reason is the current prices of these pumps, while they're getting more difficult to buy new.
In this post, I'll try to explain what I did. First dismantling the old one and finding the rootcause of it's failure (It had only done 8000 km from new or so...)
Of course, it all started with dismantling the old one. Luckily I have a 10 tons press at work that I could use. When assembled, this is what it looked like:
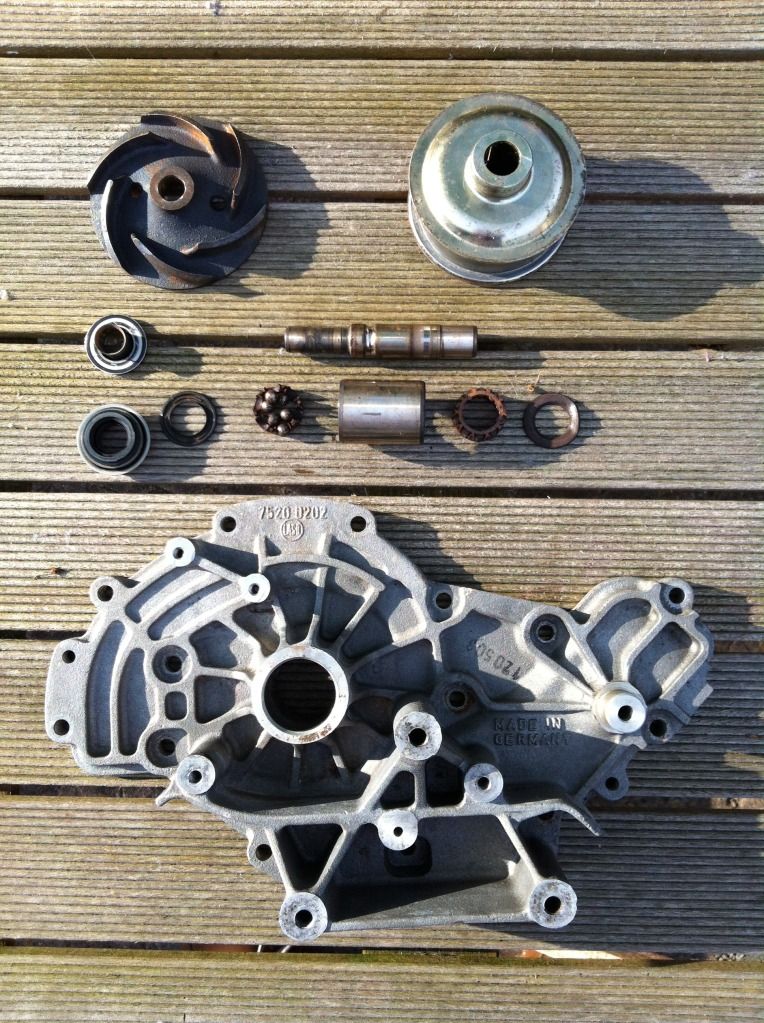
As can be seen, the roller bearing is completely rusted, like many of the rest of the bearing surfaces. The shaft had a lot of play before dismantling, which is probably due to a broken water seal. The seal consists of basically two parts: a ceramic disc and a graphite disc that are pushed on to each other by a spring.
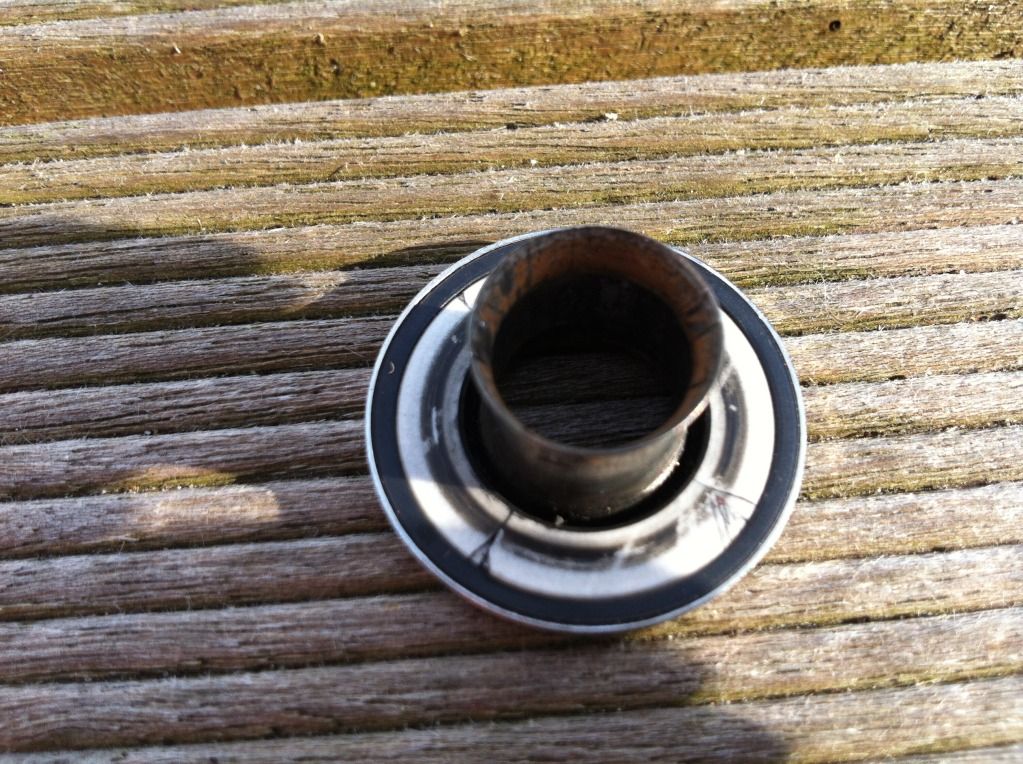
This is the ceramic disc held in a stainless steel container with rubber in between. It it fixed on the shaft and rests with the back (the side resting on the table) on the impeller. The disc is quite thin and is broken in many pieces:
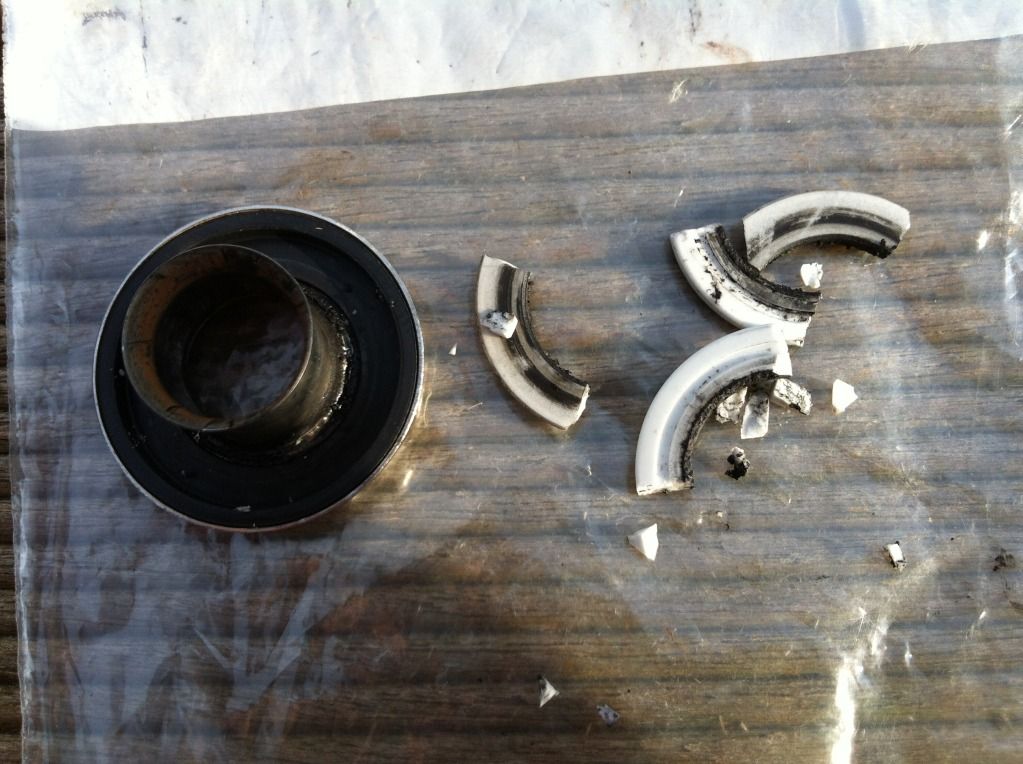
The root cause for the ceramic disc to be broken is probably rust on the impeller, pushing away the stainless holder under the ceramic disc. This way, the ceramic disc is not pushed evenly on it's counterpart, the graphite ring attached to the housing of the pump.
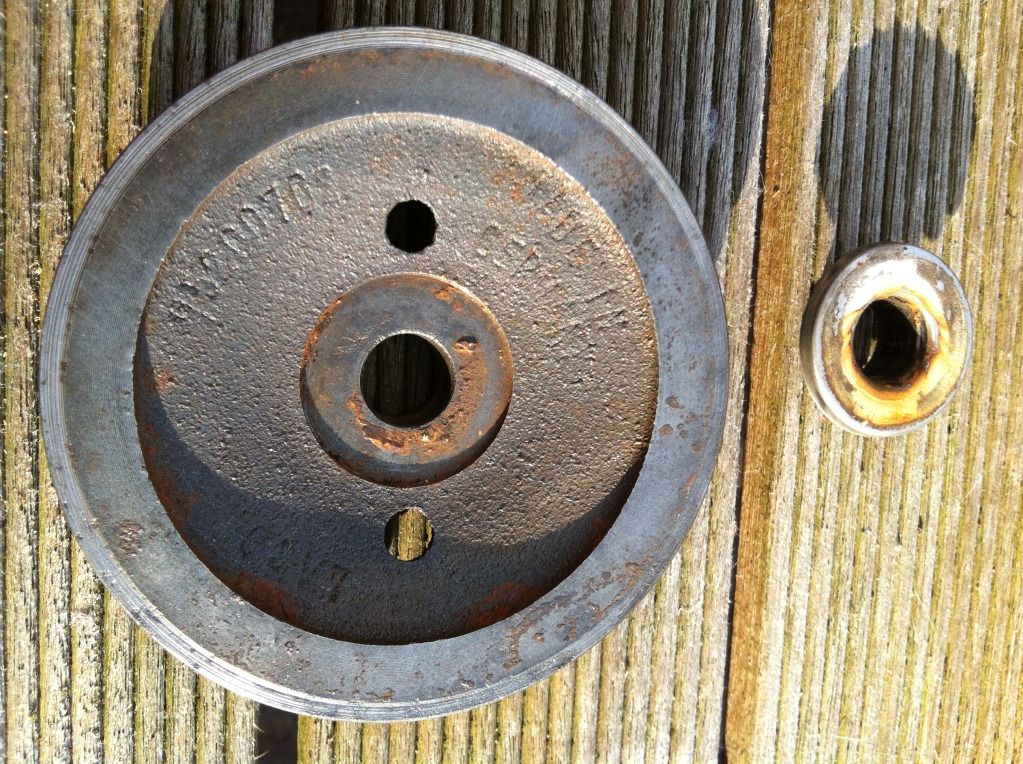
Water can now seep through the water seal, pushing against an oil seal which rests behind it to keep the oil/fat in the bearing. After some time, this seal will fail, because it is not made to keep out (hot) water at pressure. When the cooling water enters the bearings, well than hell breaks loose for those little ***** and shafts inside...
This probably is the reason for pumps with a plastic impeller to have a longer life than metal ones.
#2

Interesting - was it a new pump or a rebuilt pump?
If new it is an old design Laso. No plastic impeller or additional bush on the shaft.
What was the coolant makeup? Lots of rust.
If new it is an old design Laso. No plastic impeller or additional bush on the shaft.
What was the coolant makeup? Lots of rust.
__________________

Does it have the "Do It Yourself" manual transmission, or the superior "Fully Equipped by Porsche" Automatic Transmission?
George Layton March 2014
928 Owners are ".....a secret sect of quietly assured Porsche pragmatists who in near anonymity appreciate the prodigious, easy going prowess of the 928."

Does it have the "Do It Yourself" manual transmission, or the superior "Fully Equipped by Porsche" Automatic Transmission?

928 Owners are ".....a secret sect of quietly assured Porsche pragmatists who in near anonymity appreciate the prodigious, easy going prowess of the 928."

#3

It was sold as being a new pump.
What additional bush on the shaft do you mean?
The coolant was brand new; it had a HGF in the mean time, but in both (before and after HGF) cases the water was not dirty.
What additional bush on the shaft do you mean?
The coolant was brand new; it had a HGF in the mean time, but in both (before and after HGF) cases the water was not dirty.
#4

Rebuild started with setting requirements and after that finding suitable parts that would be able to fit or made to fit.
Basic requirements are:
1. water seal for keeping out coolant
2. axial bearing to keep the shaft in place and to put mechanical force on the water seal
3. radial seal for those huge timing belt forces
4. oil seals to keep the bearings lubricated
5. water seeping through exit
First the water bearing. I found one with approximately the right diameter and length for only 8 Euros. It comes from an industrial irrigation pump.
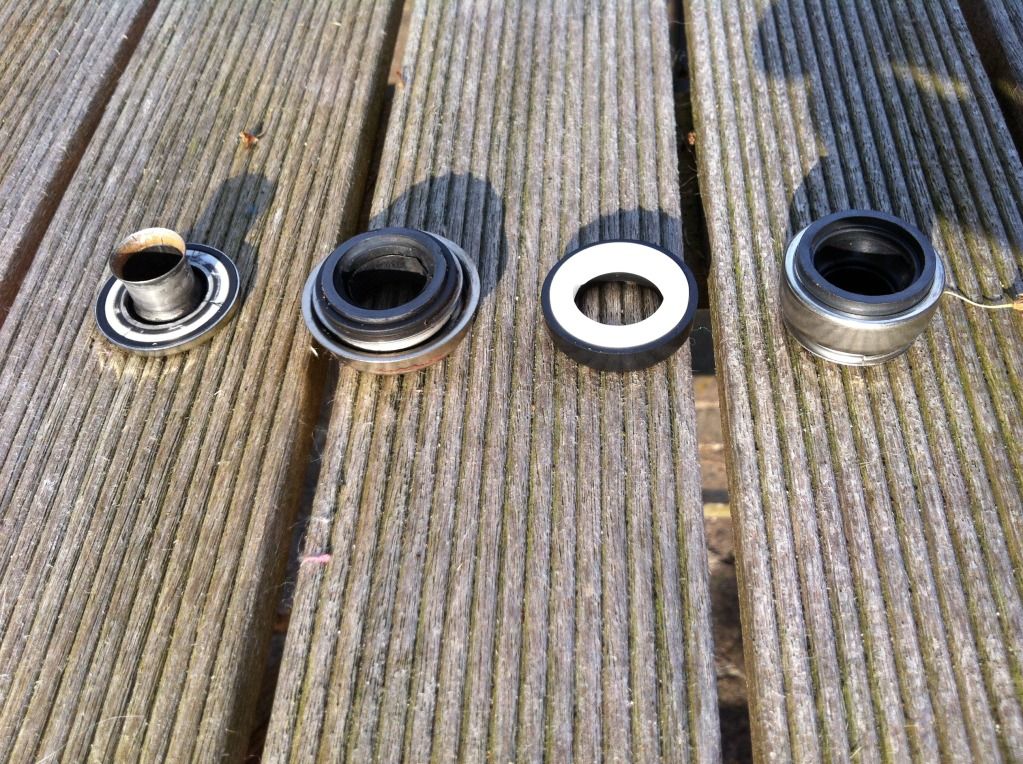
From left to right: old ceramic disc in housing, spring pushed graphite ring, new ceramic disc (not the thickness!!!), spring pushed graphite disc.
For the bearings I chose to use a single needle shaft bearing with oil seals integrated and a combined needle shaft, roller bearing:
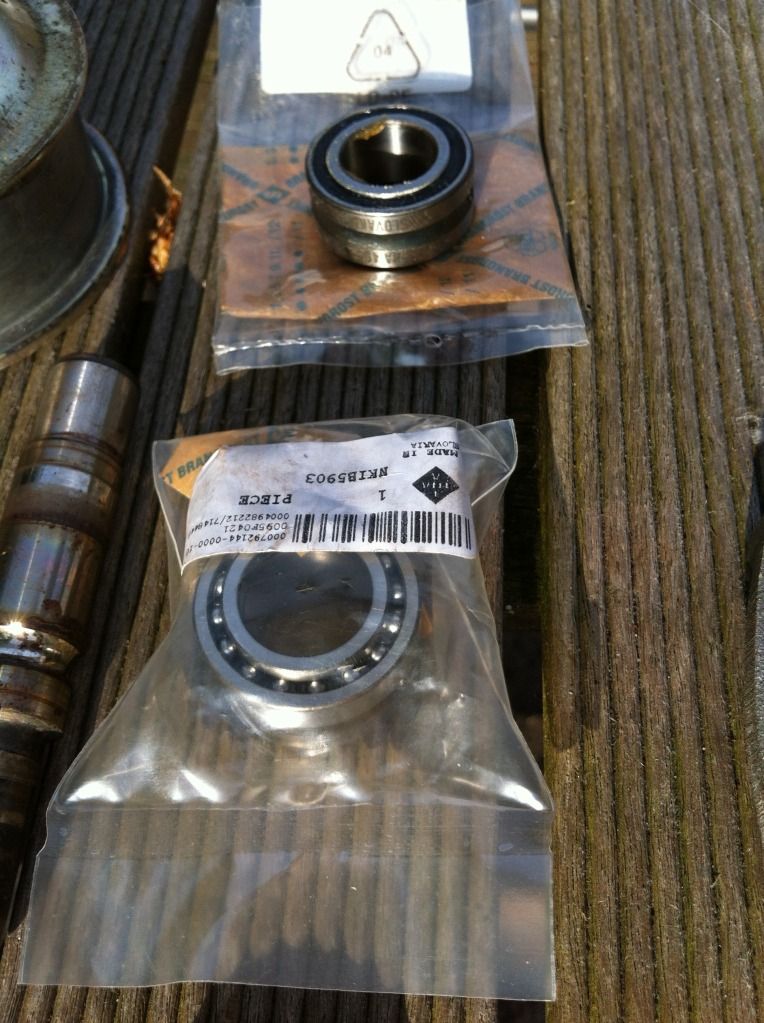
Only one extra oil seal is needed, which can be seen on this image:
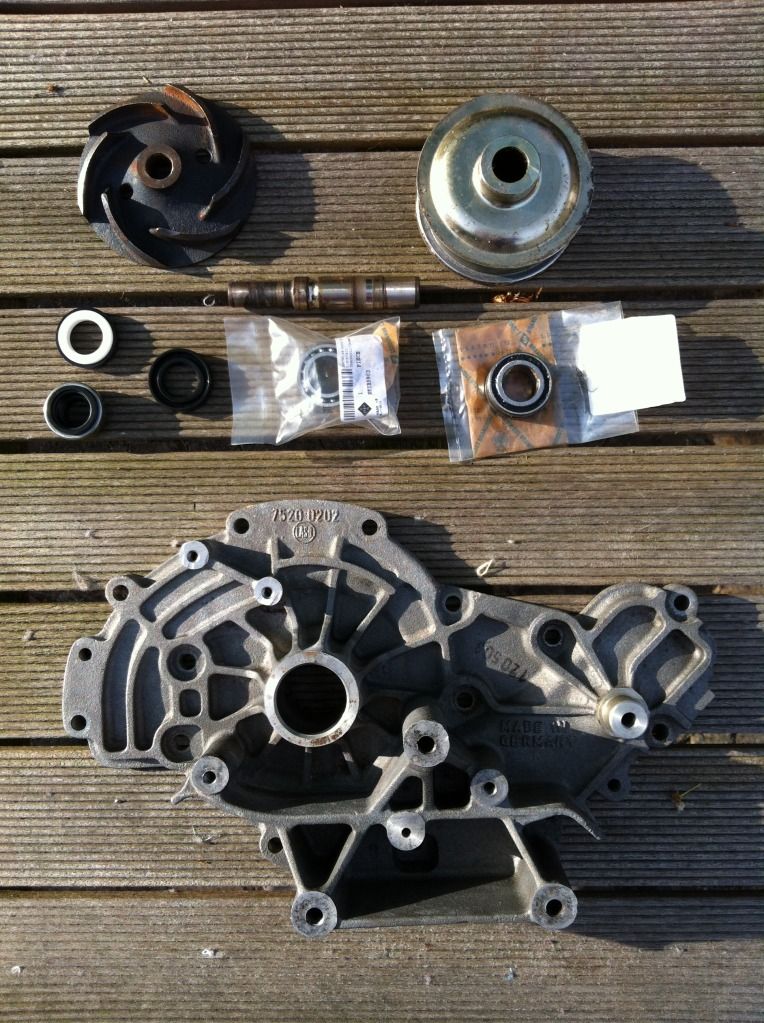
Now all was needed is to make it fit. Both bearings and oil seal outer diameters are exactly 30 mm, like the old bearing housing. So that would fit directly into the housing. The internal diamete however, is a different story. More about that in a next post.
Basic requirements are:
1. water seal for keeping out coolant
2. axial bearing to keep the shaft in place and to put mechanical force on the water seal
3. radial seal for those huge timing belt forces
4. oil seals to keep the bearings lubricated
5. water seeping through exit
First the water bearing. I found one with approximately the right diameter and length for only 8 Euros. It comes from an industrial irrigation pump.
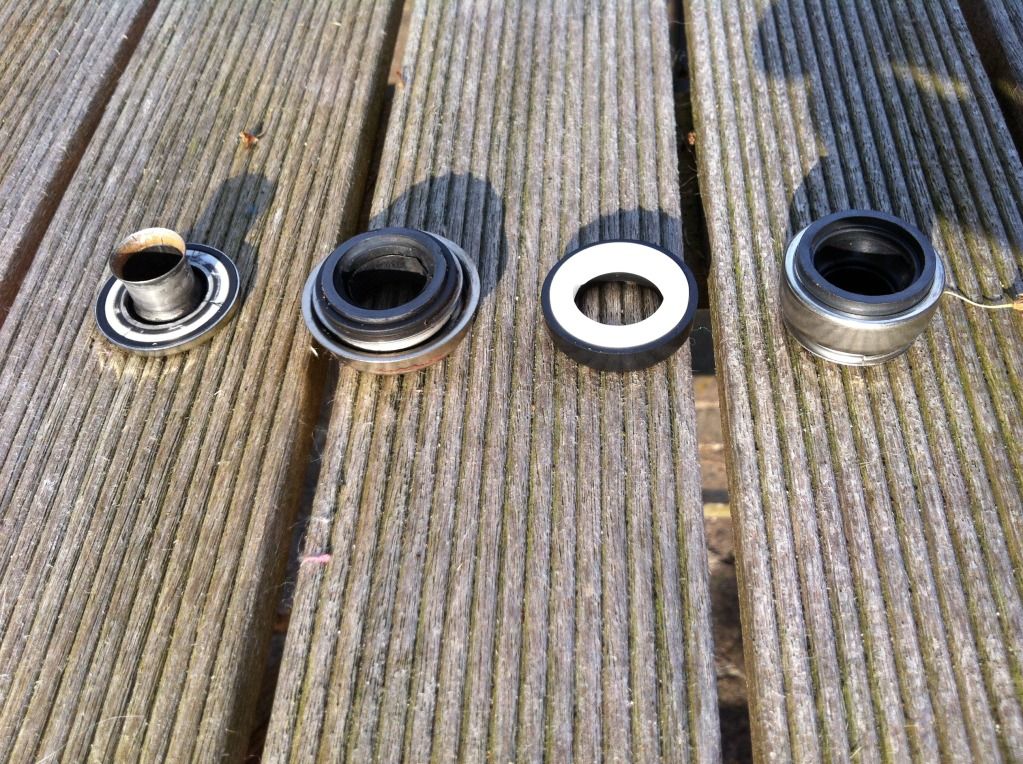
From left to right: old ceramic disc in housing, spring pushed graphite ring, new ceramic disc (not the thickness!!!), spring pushed graphite disc.
For the bearings I chose to use a single needle shaft bearing with oil seals integrated and a combined needle shaft, roller bearing:
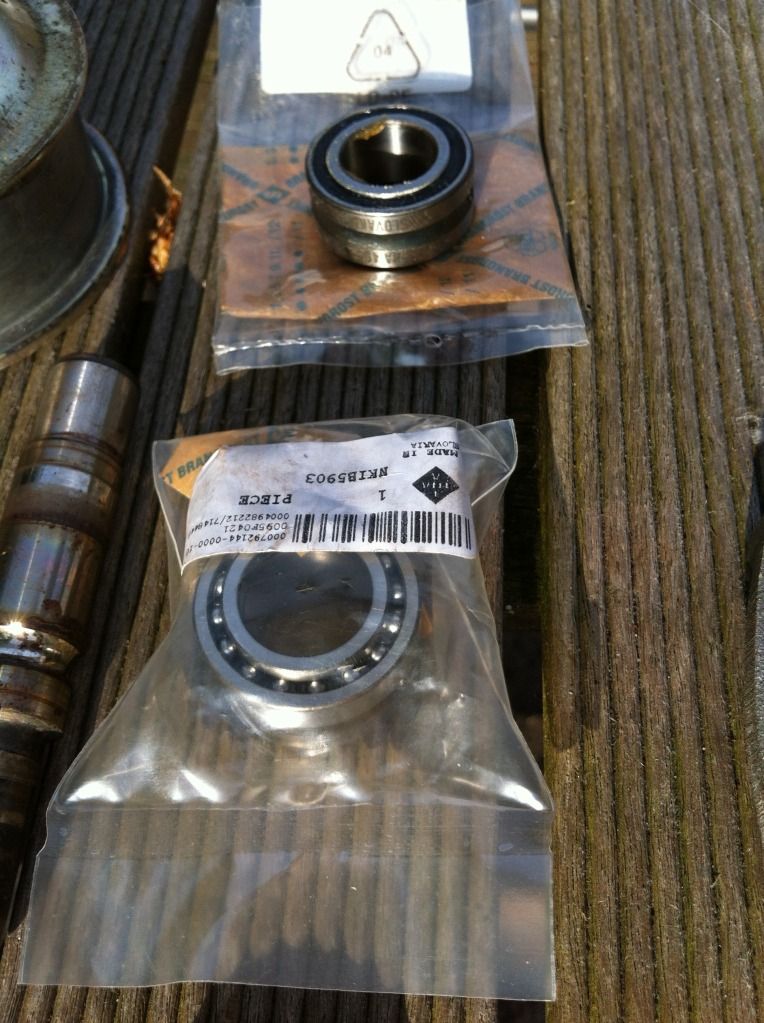
Only one extra oil seal is needed, which can be seen on this image:
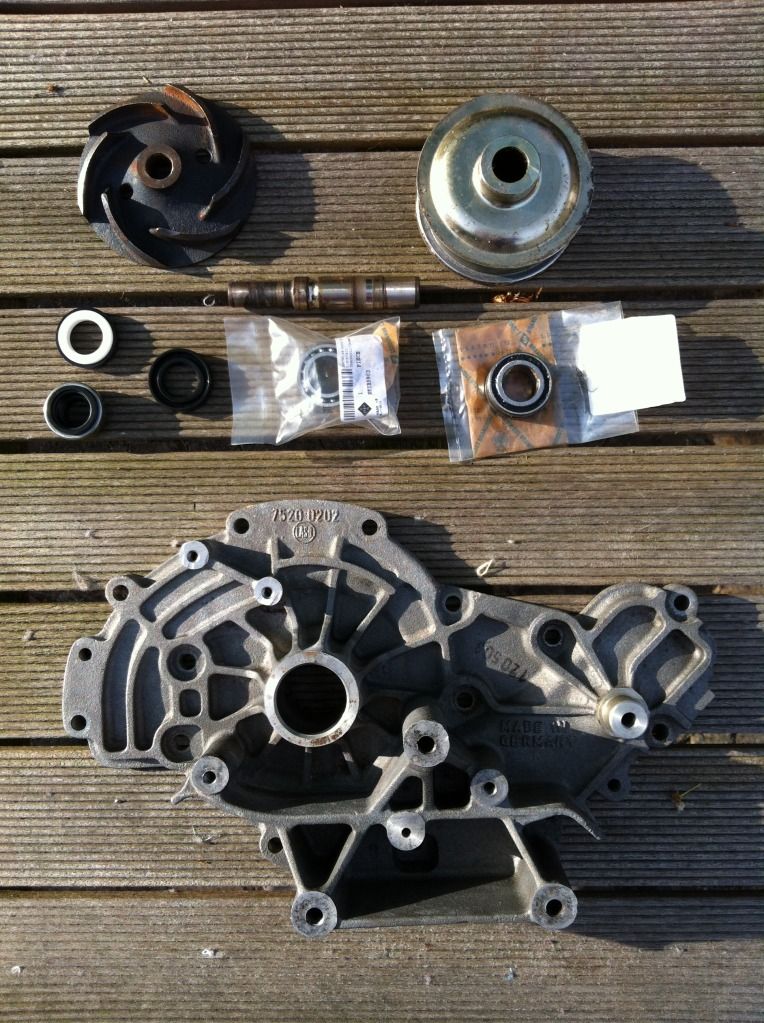
Now all was needed is to make it fit. Both bearings and oil seal outer diameters are exactly 30 mm, like the old bearing housing. So that would fit directly into the housing. The internal diamete however, is a different story. More about that in a next post.
#7

Great information. I keep data on failed water pumps that is why I asked.
The Laso water pump like others was prone to loosing the metal impeller and it could damage the block. After feedback from this forum they added an extra bush between the shaft and impeller to help keep it on there. They then modified it again and changed to a plastic impeller the same as Porsche.
Great work!
The Laso water pump like others was prone to loosing the metal impeller and it could damage the block. After feedback from this forum they added an extra bush between the shaft and impeller to help keep it on there. They then modified it again and changed to a plastic impeller the same as Porsche.
Great work!
Trending Topics
#12

I'm a DIY kinda guy, so I appreciate your efforts here, although I'm almost certain I'm going with a new Laso next time. Are you comfortable that the seals and bearings you found are going to be realiable under these circumstances and that the shaft is not worn out of spec? What do you plan to do with the impeller?
#13

dont forget to glue the bearings into the pump housing with some green locktite,
the primary reason for the rebuilt pumps failing is,
the bearings moving in the bore,
due to the pump housing has heated up and the original fit of the bearing bore has been changed by fitting and then removing the original bearings.
Running slightly reduced belt tension may prolong the usefulness of this rebuild,
good luck,
I hope it works.
NOTE if the belt seemingly stretches or rather gets loose ,
then the waterpump should be replaced instead of tightening the belt
The other failure mode is for the impeller to get loose on the shaft and this is also an indication of the bearings moving in the housing
the primary reason for the rebuilt pumps failing is,
the bearings moving in the bore,
due to the pump housing has heated up and the original fit of the bearing bore has been changed by fitting and then removing the original bearings.
Running slightly reduced belt tension may prolong the usefulness of this rebuild,
good luck,
I hope it works.
NOTE if the belt seemingly stretches or rather gets loose ,
then the waterpump should be replaced instead of tightening the belt
The other failure mode is for the impeller to get loose on the shaft and this is also an indication of the bearings moving in the housing
#15

I love to tinker, take someones design and mess with it a little or a lot, and I have a personal goal to take apart and "fix" ever item on a 928. So I know where you are coming from on this.
Good luck, and hopefully your motor is non interference.
Good luck, and hopefully your motor is non interference.