Port and Polish by Comiittee thread (Cool pics throughout)
#151
Intermediate
Join Date: Nov 2007
Location: New Jersey
Posts: 29
Likes: 0
Received 0 Likes
on
0 Posts

Hijack alert - Just a quick note on the "hemi". It was invented by Peugeot, in I believe 1910. Citroen was using them extensively in the 30's and Alfa Romeo's entire line had hemi heads starting sometime in the 40's.
#152
Nordschleife Master
#154
Rennlist Member

There was a great show on the national geographic channel that went inside the Ferrari factory and covered a cars production from the foundry to the finish line.
Some things I found interesting were that they did clean up their sand casting molds before pouring them. The sand casting's are made from a die and when the die seperates it leaves a pretty common ridge around where the two plate halves meet. Ferrari takes this part and uses a die grinder and removes it from the sand mold which is incredibly easy before pouring aluminum into it. Machining the aluminum would be more work so they eliminate the problem at the easiest step, when working with sand.
I have to think that its overlooked by other makes because it seems to be a hand done process. The sand cores are probably too fragile to be handled by robots and there would be so many castings that they couldnt keep up. That and most engine blocks for Porsche , BMW, and so on are made off site by someone else. Ferrari has their own foundry and produces their own blocks and heads. Its also good that they have very good quality control. Something i think you can do when you only make 5000 cars a year.
Some things I found interesting were that they did clean up their sand casting molds before pouring them. The sand casting's are made from a die and when the die seperates it leaves a pretty common ridge around where the two plate halves meet. Ferrari takes this part and uses a die grinder and removes it from the sand mold which is incredibly easy before pouring aluminum into it. Machining the aluminum would be more work so they eliminate the problem at the easiest step, when working with sand.
I have to think that its overlooked by other makes because it seems to be a hand done process. The sand cores are probably too fragile to be handled by robots and there would be so many castings that they couldnt keep up. That and most engine blocks for Porsche , BMW, and so on are made off site by someone else. Ferrari has their own foundry and produces their own blocks and heads. Its also good that they have very good quality control. Something i think you can do when you only make 5000 cars a year.
There were some videos of Ferrari pouring magnesium back in the 80's and when I saw it it looked exactly like my shop. Ironically the person who owns the Alfa worked for Ferrari before he went to Lamborghini and he always says there are only 2 places in the world to get a good mag casting. Marinello Italy (Ferrari plant) and my shop.

Sorry for the tangent now back to porting and polishing.
#155
Nordschleife Master

you sure we were looking at the same thing? It sure as hell looked like sand to me. Wether or not it was sand or some sand like substance is debatable of course but what i was talking about was an inner mold that looked like it was used as the water passage section of the casting. The only way i know of for removing that once the metal is poured is to dissolve it with water or who knows what.
I'll try and find more info but the block molds are made up of 4, 5 6 or more separate disposable molds into which the aluminum alloy is poured. I don't know how you can die cast an engine block, its far to complex for die casting.
Maybe my terminology is different but i would love to know more about this.
When you say sand casting is the oldest method do you suggest its also the worst? I would think technology has changed so that they can make very good sand molds. This appears to be your business so i am sure you know what your talking about, but I think your thinking of a different video or different scene or something.
So were on the same page: Ive known a die casting to be two large plates attached to giant press's. They close and alloy is poured in then the moulds separate.
Ferrari build's something of a Negative engine block leaving air in all areas that are to be filled with aluminum. The moulds are some type of fine black powder for the exterior casing into which other (what appear to be sand) parts are stacked into (after first being scorched to put some carbon on the part to help remove them when the casting is hard). There appears to be more then a few of these smaller sand parts which are there to make up the water passageways or oil passageways and rough holes for the cylinder bores. The alloy is poured and after a set time the entire block is put onto a giant tumbler to loosen up the sand and the rough alloy block or head comes loose when its then finish machined and later assembled. Die casting cannot make engine blocks to my knowledge, and nor did i see a die casting setup for ferrari V12's. Mind you they probably only cast about 1000 blocks a year if not less then that so sand casting would seem to be the way to go when it comes to production numbers that must be met.
I'll try and find more info but the block molds are made up of 4, 5 6 or more separate disposable molds into which the aluminum alloy is poured. I don't know how you can die cast an engine block, its far to complex for die casting.
Maybe my terminology is different but i would love to know more about this.
When you say sand casting is the oldest method do you suggest its also the worst? I would think technology has changed so that they can make very good sand molds. This appears to be your business so i am sure you know what your talking about, but I think your thinking of a different video or different scene or something.
So were on the same page: Ive known a die casting to be two large plates attached to giant press's. They close and alloy is poured in then the moulds separate.
Ferrari build's something of a Negative engine block leaving air in all areas that are to be filled with aluminum. The moulds are some type of fine black powder for the exterior casing into which other (what appear to be sand) parts are stacked into (after first being scorched to put some carbon on the part to help remove them when the casting is hard). There appears to be more then a few of these smaller sand parts which are there to make up the water passageways or oil passageways and rough holes for the cylinder bores. The alloy is poured and after a set time the entire block is put onto a giant tumbler to loosen up the sand and the rough alloy block or head comes loose when its then finish machined and later assembled. Die casting cannot make engine blocks to my knowledge, and nor did i see a die casting setup for ferrari V12's. Mind you they probably only cast about 1000 blocks a year if not less then that so sand casting would seem to be the way to go when it comes to production numbers that must be met.
#156
Rennlist Member

you sure we were looking at the same thing? It sure as hell looked like sand to me. Wether or not it was sand or some sand like substance is debatable of course but what i was talking about was an inner mold that looked like it was used as the water passage section of the casting. The only way i know of for removing that once the metal is poured is to dissolve it with water or who knows what.
I'll try and find more info but the block molds are made up of 4, 5 6 or more separate disposable molds into which the aluminum alloy is poured. I don't know how you can die cast an engine block, its far to complex for die casting.
Maybe my terminology is different but i would love to know more about this.
When you say sand casting is the oldest method do you suggest its also the worst? I would think technology has changed so that they can make very good sand molds. This appears to be your business so i am sure you know what your talking about, but I think your thinking of a different video or different scene or something.
So were on the same page: Ive known a die casting to be two large plates attached to giant press's. They close and alloy is poured in then the moulds separate.
Ferrari build's something of a Negative engine block leaving air in all areas that are to be filled with aluminum. The moulds are some type of fine black powder for the exterior casing into which other (what appear to be sand) parts are stacked into (after first being scorched to put some carbon on the part to help remove them when the casting is hard). There appears to be more then a few of these smaller sand parts which are there to make up the water passageways or oil passageways and rough holes for the cylinder bores. The alloy is poured and after a set time the entire block is put onto a giant tumbler to loosen up the sand and the rough alloy block or head comes loose when its then finish machined and later assembled. Die casting cannot make engine blocks to my knowledge, and nor did i see a die casting setup for ferrari V12's. Mind you they probably only cast about 1000 blocks a year if not less then that so sand casting would seem to be the way to go when it comes to production numbers that must be met.
I'll try and find more info but the block molds are made up of 4, 5 6 or more separate disposable molds into which the aluminum alloy is poured. I don't know how you can die cast an engine block, its far to complex for die casting.
Maybe my terminology is different but i would love to know more about this.
When you say sand casting is the oldest method do you suggest its also the worst? I would think technology has changed so that they can make very good sand molds. This appears to be your business so i am sure you know what your talking about, but I think your thinking of a different video or different scene or something.
So were on the same page: Ive known a die casting to be two large plates attached to giant press's. They close and alloy is poured in then the moulds separate.
Ferrari build's something of a Negative engine block leaving air in all areas that are to be filled with aluminum. The moulds are some type of fine black powder for the exterior casing into which other (what appear to be sand) parts are stacked into (after first being scorched to put some carbon on the part to help remove them when the casting is hard). There appears to be more then a few of these smaller sand parts which are there to make up the water passageways or oil passageways and rough holes for the cylinder bores. The alloy is poured and after a set time the entire block is put onto a giant tumbler to loosen up the sand and the rough alloy block or head comes loose when its then finish machined and later assembled. Die casting cannot make engine blocks to my knowledge, and nor did i see a die casting setup for ferrari V12's. Mind you they probably only cast about 1000 blocks a year if not less then that so sand casting would seem to be the way to go when it comes to production numbers that must be met.
In order to make inner passages in casting you need a core this is usually made of hardened sand or sometimes ceramic. This is the only way to passage or core a casting. Otherwise you would end up with a solid block. You had mentioned albeit confusing to me because you are mixing terminology:
Some things I found interesting were that they did clean up their sand casting molds before pouring them. The sand casting's are made from a die and when the die seperates it leaves a pretty common ridge around where the two plate halves meet. Ferrari takes this part and uses a die grinder and removes it from the sand mold which is incredibly easy before pouring aluminum into it. Machining the aluminum would be more work so they eliminate the problem at the easiest step, when working with sand.
Basic sand casting 101 Usually a sand mold is made up of 2 parts the upper half (Cope) and lower half (Drag). green sand or no bake sand is used, Both look black in appearance. green sand is compacted no bake is cured and hardened. These are only used once and the sand is then discarded or reclaimed. If it were a metal half it is a die ie. die casting and is usually split vertically vs horizontally for sand molds. Die molds can also be made of multiple sections that come together to make a single mold. If it is made in sand than there are ways to use the same core sand and make multiple outer sections and glue them together to make a mold although this is not common practice and has its drawbacks. Without having the clip or show to review I cannot say but I believe the show I saw was a die casting with sand core. Most automotive castings today are die castings. Although some use a baked hardened sand to make the entire mold.
Actually BMW has a process were they die cast an aluminum sleeve for the pistons and encase this casting in a die mold and inject magnesium around it to make their engine blocks. Rather interesting process and only cost effective for large scale single product production. This is a die casting.
Each has its merits and disadvantages. I make Aluminum and Magnesium sand castings and I achieve tensile strengths equivalent to non heat treated steel from both materials. Die castings don't allow for slow dissipation of heat and are limited to how the casting can be feed or risered. Instead the metal is injected under pressure to achieve similar results. Sand castings have issues with included material and loose tolerances, but allow for low production and more intricate configurations. Common tolerances for sand castings are +/- .030" as were die is closer to +/- .020/.015 and investment +/-.010" this is because sand is sand and can only be controlled so much unlike a hard metal die.. Sand castings can allow you to core and make shapes that Die castings cannot. Investment has more of this advantage but also has issues with solidification that sand is not restricted by. I make a 1 pound aluminum casting that is 8" tall by 5" wide and 3" deep varying in shape from top to bottom and it has over 380 dimensions is more open air passages than metal. Each dimension has to be held to a +/- .030" tolerance which is not easy to do but can only be done in sand. Each process needs to be researched before designing a product based on the merits of the process and fluidity of the alloy being used as they differ in composition based on process.
Again sorry to get so off topic.
Try this link for Die casting info.
http://www.diecasting.org/faq/
Sand casting
http://www.efunda.com/processes/meta...ting_intro.cfm
Investment casting
http://www.hitchiner.com/HIMCO/Basics.html
#157
Nordschleife Master

Ok well i have my terms mixed up them
When i think die casting i have in my head the "die cast" cars i used to collect when i was a kid. I imagined those being giant steel die's, but now that i think of it what i am imagining sounds more like a metal press.
So your telling me that die casting use's sand cores to complete the mold? Ok cool, i am mistaken in my terminology but i know i saw sand molds and assumed it was called sand casting. I am mistaken, thanks for clarifying.
Nice links BTW, i will check those out.
Q: since you may know, can you give me a general price on what it would cost to make a Jaguar XJR type manifold and intercooler housing that would fit a 928? I tried to mess around with this years back for BMW's but at some point decided that it would be best to construct the manifold and intercooler endcaps out of sheet aluminum and tig it all together instead of bothering with casting. If i was making a half dozen, which method would you use and what do you think the tooling costs would be. If you can answer, I am thinking more about turbo's these days, but i always wanted to know since it was at one point very much on the front burner. Being that you are in this business, maybe you could throw out a number?
When i think die casting i have in my head the "die cast" cars i used to collect when i was a kid. I imagined those being giant steel die's, but now that i think of it what i am imagining sounds more like a metal press.
So your telling me that die casting use's sand cores to complete the mold? Ok cool, i am mistaken in my terminology but i know i saw sand molds and assumed it was called sand casting. I am mistaken, thanks for clarifying.
Nice links BTW, i will check those out.
Q: since you may know, can you give me a general price on what it would cost to make a Jaguar XJR type manifold and intercooler housing that would fit a 928? I tried to mess around with this years back for BMW's but at some point decided that it would be best to construct the manifold and intercooler endcaps out of sheet aluminum and tig it all together instead of bothering with casting. If i was making a half dozen, which method would you use and what do you think the tooling costs would be. If you can answer, I am thinking more about turbo's these days, but i always wanted to know since it was at one point very much on the front burner. Being that you are in this business, maybe you could throw out a number?
#158
Rennlist Member

Ok well i have my terms mixed up them
When i think die casting i have in my head the "die cast" cars i used to collect when i was a kid. I imagined those being giant steel die's, but now that i think of it what i am imagining sounds more like a metal press.
So your telling me that die casting use's sand cores to complete the mold? Ok cool, i am mistaken in my terminology but i know i saw sand molds and assumed it was called sand casting. I am mistaken, thanks for clarifying.
When i think die casting i have in my head the "die cast" cars i used to collect when i was a kid. I imagined those being giant steel die's, but now that i think of it what i am imagining sounds more like a metal press.
So your telling me that die casting use's sand cores to complete the mold? Ok cool, i am mistaken in my terminology but i know i saw sand molds and assumed it was called sand casting. I am mistaken, thanks for clarifying.
If the outer sections of the mold were sand than it was sand casting if metal, die casting. Still can't be positive without seeing the actual clip again. Although the links should explain everything you would ever want to know about castings.
#159
Nordschleife Master

The exterior block or die or whatever was a fine black powder that was compacted iirc. brown colored sand parts were stacked in sequence to make an inverse or negative block and the top was more of this compressed black powder that when compressed becomes something like a brick. Because you can errode it pretty easily they simpley throw the entire block, casting sand and hardened alloy into a giant vibrating bed and the exterior sand crumbles off and leaves the rough casting of a block. The internal passageways are cleaned out and the head or block is then machined to exacting tolerances and cylinders are bored out.
Maybe the show is on National Geographic on Demand or something, it was a great show.
Maybe the show is on National Geographic on Demand or something, it was a great show.
#160
Rennlist Member

The exterior block or die or whatever was a fine black powder that was compacted iirc. brown colored sand parts were stacked in sequence to make an inverse or negative block and the top was more of this compressed black powder that when compressed becomes something like a brick. Because you can errode it pretty easily they simpley throw the entire block, casting sand and hardened alloy into a giant vibrating bed and the exterior sand crumbles off and leaves the rough casting of a block. The internal passageways are cleaned out and the head or block is then machined to exacting tolerances and cylinders are bored out.
Maybe the show is on National Geographic on Demand or something, it was a great show.
Maybe the show is on National Geographic on Demand or something, it was a great show.
Sand
#161
Three Wheelin'
Join Date: Jan 2007
Location: not where you think I am
Posts: 1,466
Likes: 0
Received 0 Likes
on
0 Posts

on "How it's Made" today on Discovery Channel.
sand casting of blocks.......quite educational for those who have never seen it done.
Sorry for the intrusion-
--back to my paint removal project
--Russ
sand casting of blocks.......quite educational for those who have never seen it done.
Sorry for the intrusion-
--back to my paint removal project
--Russ
#162

Greg Grey? has done extensive and expensive 2 valve development . Oversize valves titanium components to reduce valvetrain weight and extensive flow bench supported porting. I'm surprized he hasn't joined this dicussion.
What I have done is had 6 different valves made with different angles and the margins of course can be altered too and had them flowed. We also had a development head to experiment with so that we could try ideas that might work.
I loved the look of those Honda heads, wow! One thing you will need to decide on is what rpm ranges are being used, capacity etc. If this is a forced engine well cc ing the heads, polishing out any hot spots in the chambers. Forced stuff is not my forte. I would have thought camshafts, that is lobe separation angle and lift on the exhaust side would be critical.
I like the N/A stuff for which I would run the 968 head as it is more like the current 4V heads, that is oval ports on the intakes and modern engines also have oval exhausts too. I bought a 980 intake gasket to look at the shape and size and the 968 is still quite good. The exhaust valves should probably be 21 4N EV8 that is what I have in my 5.4 litre engine build but on the intake side, you can run them on both sides.
I think for this particular build take away very minimal material, just a clean up and look at the valves. Depending on the boost and the full throttle intervals those valves may not like it long term although I do like Porsche's valves per say.
BTW I got about 415 hp at the flywheel for my 5.0 litre engine with standard euro valves. The car did 311 hp at the wheels and on this brand of dyno, Dyno Dynamics equates to that figure, on a Ferrari site the 360 CS did 302 hp and the 360 Modena did 311 hp and the LS2s do around 300 hp on this particular dyno so I should be pretty close. Its a pretty good number from a old girl. We have a big dyno day coming up on the 24 of May at a Porsche specialist, so all types of Porsche will run that day.
Greg
#164
Rennlist Member
Thread Starter

Well I only just read this thread, I have not much time for playing these days, my work is not really what Brendan is chasing up, what I have done with the 2V engine will not help him except in maybe procedure.
What I have done is had 6 different valves made with different angles and the margins of course can be altered too and had them flowed. We also had a development head to experiment with so that we could try ideas that might work.
I loved the look of those Honda heads, wow! One thing you will need to decide on is what rpm ranges are being used, capacity etc. If this is a forced engine well cc ing the heads, polishing out any hot spots in the chambers. Forced stuff is not my forte. I would have thought camshafts, that is lobe separation angle and lift on the exhaust side would be critical.
I like the N/A stuff for which I would run the 968 head as it is more like the current 4V heads, that is oval ports on the intakes and modern engines also have oval exhausts too. I bought a 980 intake gasket to look at the shape and size and the 968 is still quite good. The exhaust valves should probably be 21 4N EV8 that is what I have in my 5.4 litre engine build but on the intake side, you can run them on both sides.
I think for this particular build take away very minimal material, just a clean up and look at the valves. Depending on the boost and the full throttle intervals those valves may not like it long term although I do like Porsche's valves per say.
BTW I got about 415 hp at the flywheel for my 5.0 litre engine with standard euro valves. The car did 311 hp at the wheels and on this brand of dyno, Dyno Dynamics equates to that figure, on a Ferrari site the 360 CS did 302 hp and the 360 Modena did 311 hp and the LS2s do around 300 hp on this particular dyno so I should be pretty close. Its a pretty good number from a old girl. We have a big dyno day coming up on the 24 of May at a Porsche specialist, so all types of Porsche will run that day.
Greg
What I have done is had 6 different valves made with different angles and the margins of course can be altered too and had them flowed. We also had a development head to experiment with so that we could try ideas that might work.
I loved the look of those Honda heads, wow! One thing you will need to decide on is what rpm ranges are being used, capacity etc. If this is a forced engine well cc ing the heads, polishing out any hot spots in the chambers. Forced stuff is not my forte. I would have thought camshafts, that is lobe separation angle and lift on the exhaust side would be critical.
I like the N/A stuff for which I would run the 968 head as it is more like the current 4V heads, that is oval ports on the intakes and modern engines also have oval exhausts too. I bought a 980 intake gasket to look at the shape and size and the 968 is still quite good. The exhaust valves should probably be 21 4N EV8 that is what I have in my 5.4 litre engine build but on the intake side, you can run them on both sides.
I think for this particular build take away very minimal material, just a clean up and look at the valves. Depending on the boost and the full throttle intervals those valves may not like it long term although I do like Porsche's valves per say.
BTW I got about 415 hp at the flywheel for my 5.0 litre engine with standard euro valves. The car did 311 hp at the wheels and on this brand of dyno, Dyno Dynamics equates to that figure, on a Ferrari site the 360 CS did 302 hp and the 360 Modena did 311 hp and the LS2s do around 300 hp on this particular dyno so I should be pretty close. Its a pretty good number from a old girl. We have a big dyno day coming up on the 24 of May at a Porsche specialist, so all types of Porsche will run that day.
Greg
#165
Rennlist Member
Thread Starter

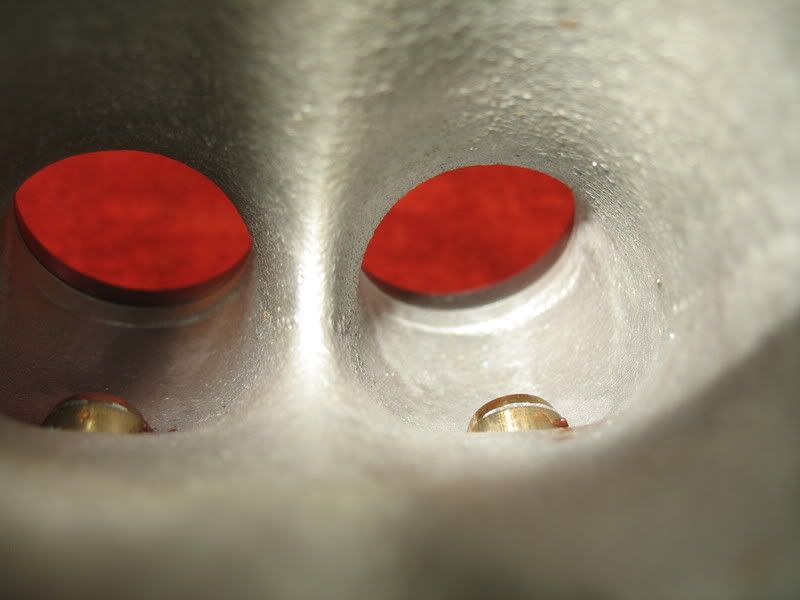
So I will take that ridge out from the intake.