Drilled Crank Thoughts...
#421
Rennlist Member

Yes those fit in a 928, we have been selling them for many years and have always gotten great feedback.
https://www.928gt.com/p-1774-oil-che...-pressure.aspx
https://www.928gt.com/p-1774-oil-che...-pressure.aspx
#422
Under the Lift
Lifetime Rennlist
Member
Lifetime Rennlist
Member

Volume and pressure are different but related. Higher pressure oil will bleed through clearances at a higher rate though I believe that function is asymptotic to some maximum value for a given viscosity oil.
So, up to a point, higher pressure will mean that more oil is collecting in the head waiting for drainback to the sump. This drainback is often hindered by sustained lateral G forces.
The other function of the Porsche 944 and 928 restrictor valve is to retain oil in the galley so that initial startup is working with a primed system.
The pressure relief valve at the pump and the internal design of the lifters themselves helps ward against pump-up of the hydraulic lifters at high rpm. This is a related issue.
So, up to a point, higher pressure will mean that more oil is collecting in the head waiting for drainback to the sump. This drainback is often hindered by sustained lateral G forces.
The other function of the Porsche 944 and 928 restrictor valve is to retain oil in the galley so that initial startup is working with a primed system.
The pressure relief valve at the pump and the internal design of the lifters themselves helps ward against pump-up of the hydraulic lifters at high rpm. This is a related issue.
#423

Sorry to drop this in after calling a draw -- I think it is important to explain the machining process.
That's a good practice.
The edges of the rod and cap show the relative depth of the pieces clamped in a machining fixture. There are depressions that are somewhat U shaped on both sides of both parts. GKN was very proud of the fact that the parts emerging from the forging process could use these depressions as the standardized indexes for subsequent machining operations. That means the depressions and therefore the morphology would be held not only mutually parallel but on the same level.
For a part -- these surfaces that are to be even -- to show almost a 1.9mm shift to one side means they were not held in the same fixture at the same time. That is a huge shift for a precision operation.
Note that this does not mean you would end up with two parts with overall different widths -- it just means they were not in the same fixture at the same time. The fixture(s) could certainly shift or be adjusted at some point in production but the shift would be mutual for both the cap and beam.
There are two possibilities for the PF rod:
1) That it was a single forging that was machined, cracked in two and subsequently machined: the surfaces would be parallel and even.
2) That it was a combination of two separate forgings that were subsequently brought together and machined in the same fixture: the surfaces would be parallel and even.
No, the sizing is completed on the fixture before rod bolts are put in. In fact, in a recent patent application describing the prior art for all PF cracked rods one of the weaknesses stated was that the bolts were installed loose and could come apart easily and parts would then be mixed up.
People are confusing resizing operations or the manufacturing methods on non-PF components with the techniques used at GKN.
The mid 1970s Porsche 928 rods developed by GKN in the UK were the first volume production PF rod. This should be a bragging point for 928 owners more so than integrated flexible bumpers.
For a part -- these surfaces that are to be even -- to show almost a 1.9mm shift to one side means they were not held in the same fixture at the same time. That is a huge shift for a precision operation.
Note that this does not mean you would end up with two parts with overall different widths -- it just means they were not in the same fixture at the same time. The fixture(s) could certainly shift or be adjusted at some point in production but the shift would be mutual for both the cap and beam.
There are two possibilities for the PF rod:
1) That it was a single forging that was machined, cracked in two and subsequently machined: the surfaces would be parallel and even.
2) That it was a combination of two separate forgings that were subsequently brought together and machined in the same fixture: the surfaces would be parallel and even.
People are confusing resizing operations or the manufacturing methods on non-PF components with the techniques used at GKN.
The mid 1970s Porsche 928 rods developed by GKN in the UK were the first volume production PF rod. This should be a bragging point for 928 owners more so than integrated flexible bumpers.
#424

So, what is it? I've been worried about making sure there was adequate oiling of the lifters and cam faces at high RPM. However, I gather the 944 valve is used to reduce EXCESSIVE oil flow to the head under race condition and oil loss via the breather system. I always thought there was something not right about the breather system and not the oiling to the head.
#425
Addict
Rennlist Member
Rennlist
Site Sponsor
Rennlist Member
Rennlist
Site Sponsor

The rods could have easily been saw cut as well. Possibility # 3 The grooving and fracturing seems to be a later design element with the irregular fractured faces used to strengthen the joint. 928 rods show no evidence of a groove (stress riser) and the faces are machined. The problem of doing machining on an irregular shaped part was encountered the very first time anyone ever machined a part ! You have to cut one surface.....any surface and reference everything off of that. You can make a cube out of a sphere and the first surface cut makes no difference at all. The same is true of a roughly forged rod after it cools from 1,000 C while there is no flat true surface you create one and reference everything off that . I also believe that the rod caps are firmly torqued to the rod with bolts for the final machining of the rods on all but possibly the latest fractured rods. The primary advantage of the powder forging was ease of manufacturing , cost savings , limited waste , and less machining needed . Not so much that it makes a superior product although better than cast. Even with all their Porsche design and engineering they completely screwed up on the early GTS rods !
#426
Under the Lift
Lifetime Rennlist
Member
Lifetime Rennlist
Member

I don't think that is an issue unless you pick one of the "energy efficient" oils. The SM or SL are still fine for antiwear and OK for our engines as long as they exceed Porsche's requirement of a HTHS of 3.5 cSt. Doug Hillary has covered this.
#427

928 rods show no evidence of a groove (stress riser) and the faces are machined. The problem of doing machining on an irregular shaped part was encountered the very first time anyone ever machined a part ! You have to cut one surface.....any surface and reference everything off of that. You can make a cube out of a sphere and the first surface cut makes no difference at all. The same is true of a roughly forged rod after it cools from 1,000 C while there is no flat true surface you create one and reference everything off that .
The primary advantage of the powder forging was ease of manufacturing , cost savings , limited waste , and less machining needed . Not so much that it makes a superior product although better than cast. Even with all their Porsche design and engineering they completely screwed up on the early GTS rods !
But I agree that there is a lot of room for improvement in the 928 rods. While the static balance may be accurate the dynamic balance would be off because of the variations in machining that I mentioned previously. They are what they are -- nothing more or less.
#428
#430

Before making any more comments about the TAG Porsche Engine being 944 based you might want to count the number of cylinders....here is a hint. In the mid 1980s, Team McLaren dominated Grand Prix racing with their carbon fibre MP4 chassis and their Porsche-built TAG Turbo engines. Between 1984 and ...
www.motorsportcollector.com/MEMtag.html - 10k - Cached - Similar pages
www.motorsportcollector.com/MEMtag.html - 10k - Cached - Similar pages
#431

Before making any more comments about the TAG Porsche Engine being 944 based you might want to count the number of cylinders....here is a hint. In the mid 1980s, Team McLaren dominated Grand Prix racing with their carbon fibre MP4 chassis and their Porsche-built TAG Turbo engines. Between 1984 and ...
www.motorsportcollector.com/MEMtag.html - 10k - Cached - Similar pages
www.motorsportcollector.com/MEMtag.html - 10k - Cached - Similar pages
You're an interesting guy. In the spirit of Easter, be nice... ok.

Here's something you may want to look into. The Suzuki G10 is based on the G13. The G10 has 3 cylinders while the G13 has four.
The engine in the 928 has 8 cylinders while the 944 has 4 cylinders. The 944 is known to be based on the 928 and the G10 is known to be based on the G13. Add a second bank with an 80 degree included angle.
Hans Mezger designed the P01 so you could always consult with him.
Much information about F1 engines is not common knowledge.
#432
Man of many SIGs
Rennlist Member
Rennlist Member

Mr. Manfred Lerbs at GKN Hueckeswagen mentioned that "it was not generally known that a Krebsoege PF con rod went into the Porsche 944 engine used in the McLaren-TAG Formula 1 racing car, which in 1984 not only won 12 out of 16 races, but also secured the world championship for Niki Lauda the same year."
Following this train of thought, shouldn't we be able to claim that the TAG F1 engine is 928 based?

#433

I get caught by this fairly regularly, though. The G10 and G13 are examples where it is really obvious the block was truncated. Same with the Mopar 3.9 V6 versus the 318 LA. However, the SBC into the 4.3 90 degree V6 -- lots of changes at least in areas I had to pay attention to.
When BMW redesigned their sixes and fours they allowed (some) crank interchangeability.
I was surprised when the Ford and Datsun guys told me about how you can machine a Datsun crank to fit in a Twink.
Benneli Sei -- that's a Honda 500 with two extra cylinders tacked on.
Then there's the modular Volvos...
After a while you can even begin to recognize the style of the designers -- before I knew about the Volvo/Porsche connection the interior of the modular block just shouted "Porsche."
Gotta love engines.
#434
Rest in Peace
Rennlist Member
Rennlist Member
Join Date: May 2006
Location: Bird lover in Sharpsburg
Posts: 9,903
Likes: 0
Received 2 Likes
on
2 Posts

He says that Lucas Oil has a additive now that contains the missing anti wear additives and is made for just that.
I have no idea what the additive is called.
For what it is worth.
Greg Nettles

#435
Addict
Rennlist Member
Rennlist Member

Yes those fit in a 928, we have been selling them for many years and have always gotten great feedback.
https://www.928gt.com/p-1774-oil-che...-pressure.aspx
https://www.928gt.com/p-1774-oil-che...-pressure.aspx
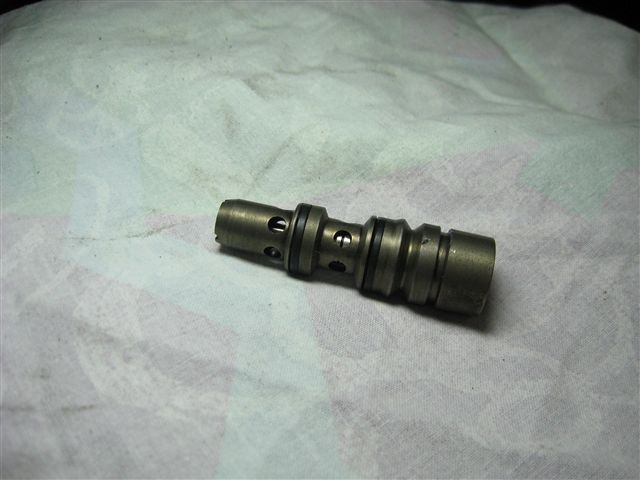
Oil enters in from the left and exits at the middle. Lower of the two o-rings keeps different pressure areas separated and upper one prevents 3bar pressure escaping to the head.