Crack in engine at the valley
#16
Rennlist Member
Thread Starter

I have nothing to add that @FredR (and others) have not already said, apart from suggesting that you make sure which "flavor" of epoxy you want to use. In my own work to investigate certain repairs (nothing as serious as what is described in these threads, but with similar heat and chemical exposures) there are different grades of JB Weld that may be more or less appropriate to what you're trying to do. To wit, there is a marine grade JB Weld, as well as a high temperature version. From the nature of what you're trying to keep contained perhaps one of those might be more helpful for a long term solution. I don't know what availability is like for you but, much as I would love to deliver it in person, I would be happy to help send you some in the post.
Finally, to expand a little on the necessity to clean the aluminum very, very carefully prior to repair. If you already know this, apologies for the explanation but perhaps it helps others. Aluminum, without its protective oxide, is an amazingly reactive material. What is particularly useful with aluminum is that the reactivity with oxygen (and water, either as vapor in the atmosphere or with water itself) forms a passivating, protective layer. Unlike other metals such as iron (and plutonium, but that's out of scope here) the oxide on aluminum has a good match to the physical properties of the underlying metal so that, unlike iron oxide (rust), it continues to exhibit good adhesion to the underlying aluminum under a variety of conditions. Rust, as you know, tends to flake off quite easily, obviating any potential benefits of physical protection of the iron itself. The other interesting thing with aluminum oxide is that you can force it to be a reasonably thick layer. This layer is reasonably porous and can trap small molecules; this is what happens in anodizing and how you can get such interesting colors on aluminum, those are trapped dyes in the oxide layer. In your case, what Fred is referring to is the same absorption of oil or grease in the oxide layer. When they are heated they will tend to be driven out. This is how you can clean things up, but is also the root cause for failure of adhesion, as they will move to the surface and interfere with bonding.
Best of luck, I also remain very interested in how you fix this. As I said above, please PM me if I can be of help.
Cheers
Finally, to expand a little on the necessity to clean the aluminum very, very carefully prior to repair. If you already know this, apologies for the explanation but perhaps it helps others. Aluminum, without its protective oxide, is an amazingly reactive material. What is particularly useful with aluminum is that the reactivity with oxygen (and water, either as vapor in the atmosphere or with water itself) forms a passivating, protective layer. Unlike other metals such as iron (and plutonium, but that's out of scope here) the oxide on aluminum has a good match to the physical properties of the underlying metal so that, unlike iron oxide (rust), it continues to exhibit good adhesion to the underlying aluminum under a variety of conditions. Rust, as you know, tends to flake off quite easily, obviating any potential benefits of physical protection of the iron itself. The other interesting thing with aluminum oxide is that you can force it to be a reasonably thick layer. This layer is reasonably porous and can trap small molecules; this is what happens in anodizing and how you can get such interesting colors on aluminum, those are trapped dyes in the oxide layer. In your case, what Fred is referring to is the same absorption of oil or grease in the oxide layer. When they are heated they will tend to be driven out. This is how you can clean things up, but is also the root cause for failure of adhesion, as they will move to the surface and interfere with bonding.
Best of luck, I also remain very interested in how you fix this. As I said above, please PM me if I can be of help.
Cheers
Perhaps interesting remark : wouldn't it be better to first weld seams just near/around the crack, because the crack contains impurities (oil, coolant) that cannot be removed easily. So actually make a sort of closed seam around the crack and then seal the crack with a seam on top of the other seams.
#18
Rennlist Member

Hi Fred, thanks for your elaborated explanation. This is really usefull information because I have little experience with applying epoxy on aluminium to seal. It often works for fixing sump pan damages on motorcycles but a big V8 Porsche engine is quite something else.
Especially because of the high temperatures and cooling fluid pressure.
Considering this, I eventually will go for a more solid solution : welding.
I also need to make sure the crack doesn't go any further .
Especially because of the high temperatures and cooling fluid pressure.
Considering this, I eventually will go for a more solid solution : welding.
I also need to make sure the crack doesn't go any further .
Unless one is near the exhaust manifold temperatures will max out around 90C or so and most modern quality epoxy's can handle that. The epoxy route can only offer you a means to help seal the leaking crack like the famous little Dutch boy with his finger in the Dyke. Then it is more a question of whether it will seal and for how long but as with anything, incorrect prepartion will scupper the chances of success rapidly as you experienced previously.
If you want to go down the welding route then it is a whole different ball game you are playing in. Welding aluminium is an art and if one looks at the photo of the welding done by our friend earlier in the thread you will not see neater welding than that period. However that was in a controlled environment where the welder knew what he was doing, knew exactly what rods and material conditions he was working with, probably had a well defined WPS [weld procedure specification] and was tested and qualified to weld the joints in question. In your case the situation is entirely the opposite.
For starters you are dealing with alusil- it is not impossible to weld but in alloy terms is probably more difficult than most such alloys to weld, you have aged material that will be heavily contaminated with oily vapours, you have a major defect of unknown proportion and for all you know the crack may have propagated along the length of the entire block. you know there is communication between the base of the water jacket and the bottom of the vee- as I alluded to in your earlier thread, although one cannot be certain the odds are that this engine suffered a frost heave incident somewhere in its history- if so think about the stresses that were inflicted to cause the block to crack and ultimately to fail as and when the crack propagated. I also suggested a dye pen examination to see if that revealed surface cracking that the eye cannot as yet see and even then the underlying damage may well be even more severe.
If the above were not enough you also have the prospect of corroded heads along the inevitable lines i have commented on extensively in other threads [I take it you have not had the heads off during your ownership]. Then of course GB has advised of the difficulties he had addressing something similar. In short, I do not see a viable solution to your problem unless an until you can expunge the crack and thus leave the welder with something he can actually work with. Leave a crack in there and sure enough sooner or later the stresses will most likely open it again. Maybe UT examination would reveal the extent of the cracking but then the $$$'s start rolling.
Whereas I hate to be pessimistic as a professional engineering and project manager with over 40 years experience of managing engineering related problems it seems to me you are dealing with a pretty poor hand here and unless you attack the issue correctly the odds are the effort will fail. I am sure there will be potential workarounds for all these issues - it all boils down to skill and cost to eradicate. As GB and JG have alluded to already [and myself previously] you are looking at a total engine out and complete strip down- you will almost certainly need to get the block in an industrial oven and bake it at something like 200C for a couple of hours or whatever to de-gas it. Hopefully someone can be a bit more specific to help guide you at what you are likely in for. Only then will you be able to make a real world assessment as to what is economically viable relative to your means and desires.
Trust the above constructive even if it is not what you would ideally like to hear.
#19
Rennlist Member
Thread Starter

Gerrit,
Unless one is near the exhaust manifold temperatures will max out around 90C or so and most modern quality epoxy's can handle that. The epoxy route can only offer you a means to help seal the leaking crack like the famous little Dutch boy with his finger in the Dyke. Then it is more a question of whether it will seal and for how long but as with anything, incorrect prepartion will scupper the chances of success rapidly as you experienced previously.
If you want to go down the welding route then it is a whole different ball game you are playing in. Welding aluminium is an art and if one looks at the photo of the welding done by our friend earlier in the thread you will not see neater welding than that period. However that was in a controlled environment where the welder knew what he was doing, knew exactly what rods and material conditions he was working with, probably had a well defined WPS [weld procedure specification] and was tested and qualified to weld the joints in question. In your case the situation is entirely the opposite.
For starters you are dealing with alusil- it is not impossible to weld but in alloy terms is probably more difficult than most such alloys to weld, you have aged material that will be heavily contaminated with oily vapours, you have a major defect of unknown proportion and for all you know the crack may have propagated along the length of the entire block. you know there is communication between the base of the water jacket and the bottom of the vee- as I alluded to in your earlier thread, although one cannot be certain the odds are that this engine suffered a frost heave incident somewhere in its history- if so think about the stresses that were inflicted to cause the block to crack and ultimately to fail as and when the crack propagated. I also suggested a dye pen examination to see if that revealed surface cracking that the eye cannot as yet see and even then the underlying damage may well be even more severe.
If the above were not enough you also have the prospect of corroded heads along the inevitable lines i have commented on extensively in other threads [I take it you have not had the heads off during your ownership]. Then of course GB has advised of the difficulties he had addressing something similar. In short, I do not see a viable solution to your problem unless an until you can expunge the crack and thus leave the welder with something he can actually work with. Leave a crack in there and sure enough sooner or later the stresses will most likely open it again. Maybe UT examination would reveal the extent of the cracking but then the $$$'s start rolling.
Whereas I hate to be pessimistic as a professional engineering and project manager with over 40 years experience of managing engineering related problems it seems to me you are dealing with a pretty poor hand here and unless you attack the issue correctly the odds are the effort will fail. I am sure there will be potential workarounds for all these issues - it all boils down to skill and cost to eradicate. As GB and JG have alluded to already [and myself previously] you are looking at a total engine out and complete strip down- you will almost certainly need to get the block in an industrial oven and bake it at something like 200C for a couple of hours or whatever to de-gas it. Hopefully someone can be a bit more specific to help guide you at what you are likely in for. Only then will you be able to make a real world assessment as to what is economically viable relative to your means and desires.
Trust the above constructive even if it is not what you would ideally like to hear.
Unless one is near the exhaust manifold temperatures will max out around 90C or so and most modern quality epoxy's can handle that. The epoxy route can only offer you a means to help seal the leaking crack like the famous little Dutch boy with his finger in the Dyke. Then it is more a question of whether it will seal and for how long but as with anything, incorrect prepartion will scupper the chances of success rapidly as you experienced previously.
If you want to go down the welding route then it is a whole different ball game you are playing in. Welding aluminium is an art and if one looks at the photo of the welding done by our friend earlier in the thread you will not see neater welding than that period. However that was in a controlled environment where the welder knew what he was doing, knew exactly what rods and material conditions he was working with, probably had a well defined WPS [weld procedure specification] and was tested and qualified to weld the joints in question. In your case the situation is entirely the opposite.
For starters you are dealing with alusil- it is not impossible to weld but in alloy terms is probably more difficult than most such alloys to weld, you have aged material that will be heavily contaminated with oily vapours, you have a major defect of unknown proportion and for all you know the crack may have propagated along the length of the entire block. you know there is communication between the base of the water jacket and the bottom of the vee- as I alluded to in your earlier thread, although one cannot be certain the odds are that this engine suffered a frost heave incident somewhere in its history- if so think about the stresses that were inflicted to cause the block to crack and ultimately to fail as and when the crack propagated. I also suggested a dye pen examination to see if that revealed surface cracking that the eye cannot as yet see and even then the underlying damage may well be even more severe.
If the above were not enough you also have the prospect of corroded heads along the inevitable lines i have commented on extensively in other threads [I take it you have not had the heads off during your ownership]. Then of course GB has advised of the difficulties he had addressing something similar. In short, I do not see a viable solution to your problem unless an until you can expunge the crack and thus leave the welder with something he can actually work with. Leave a crack in there and sure enough sooner or later the stresses will most likely open it again. Maybe UT examination would reveal the extent of the cracking but then the $$$'s start rolling.
Whereas I hate to be pessimistic as a professional engineering and project manager with over 40 years experience of managing engineering related problems it seems to me you are dealing with a pretty poor hand here and unless you attack the issue correctly the odds are the effort will fail. I am sure there will be potential workarounds for all these issues - it all boils down to skill and cost to eradicate. As GB and JG have alluded to already [and myself previously] you are looking at a total engine out and complete strip down- you will almost certainly need to get the block in an industrial oven and bake it at something like 200C for a couple of hours or whatever to de-gas it. Hopefully someone can be a bit more specific to help guide you at what you are likely in for. Only then will you be able to make a real world assessment as to what is economically viable relative to your means and desires.
Trust the above constructive even if it is not what you would ideally like to hear.
sorry about my late reply but here are some pics of top of engine where crack is situated.
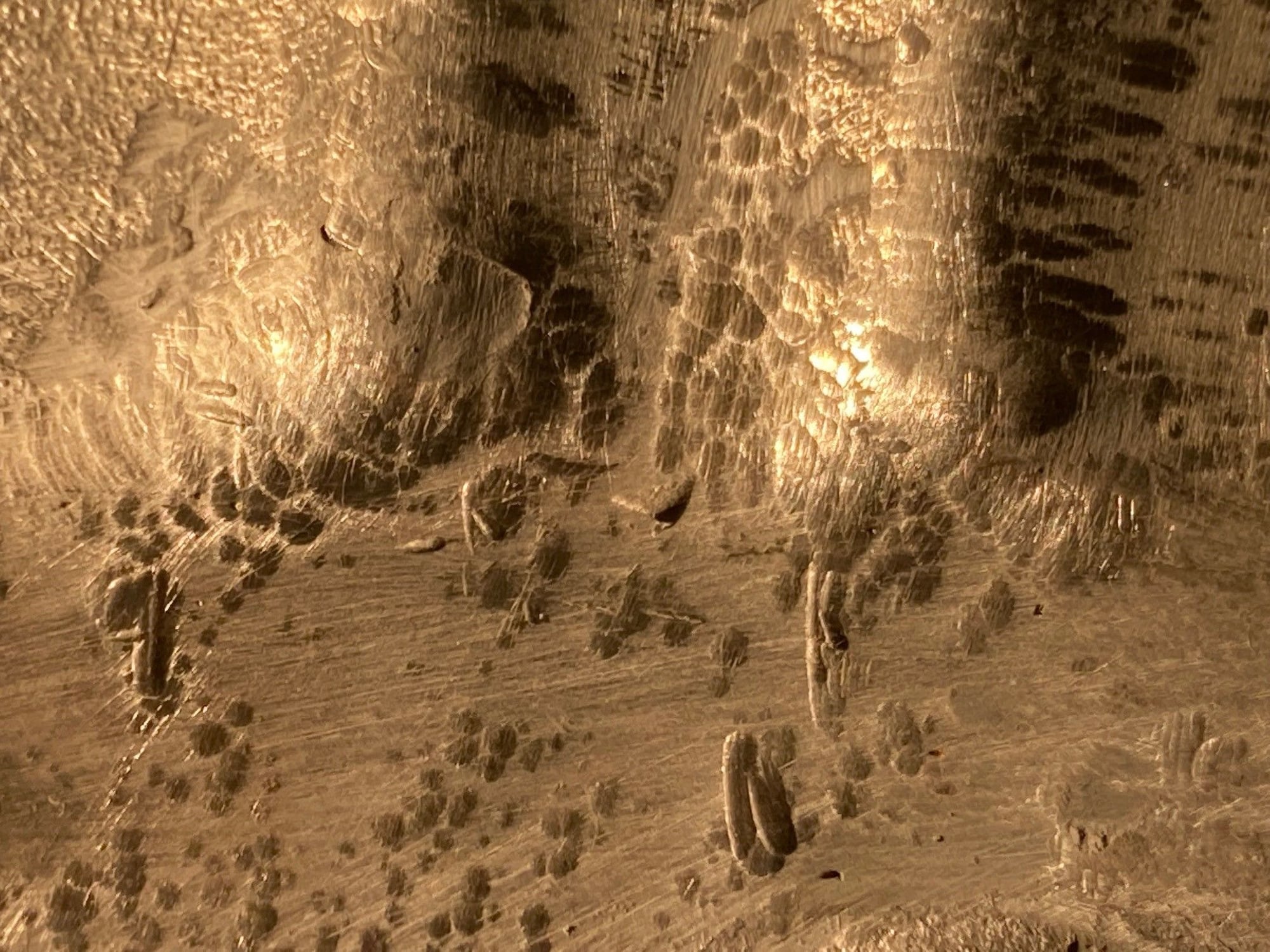

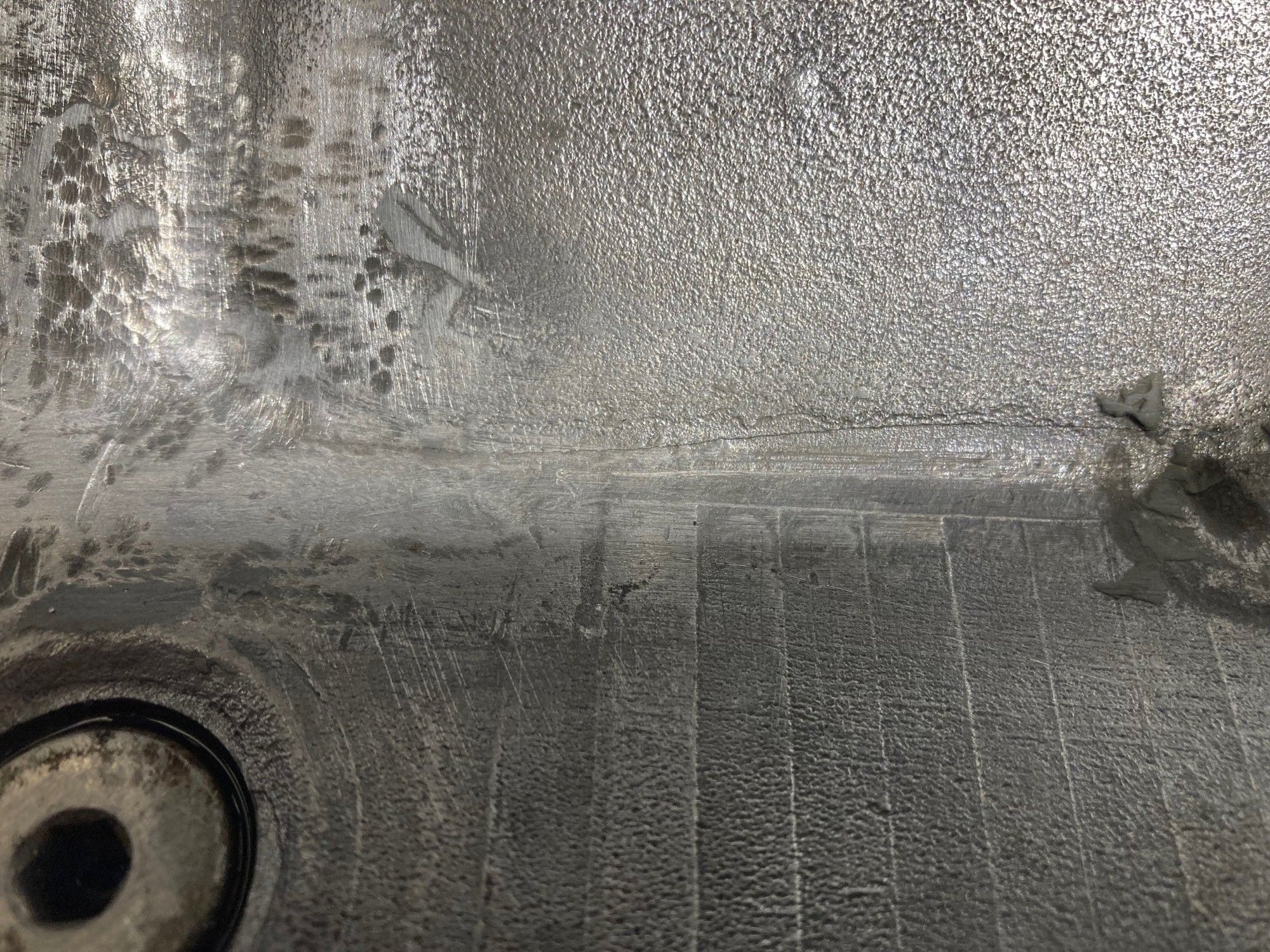
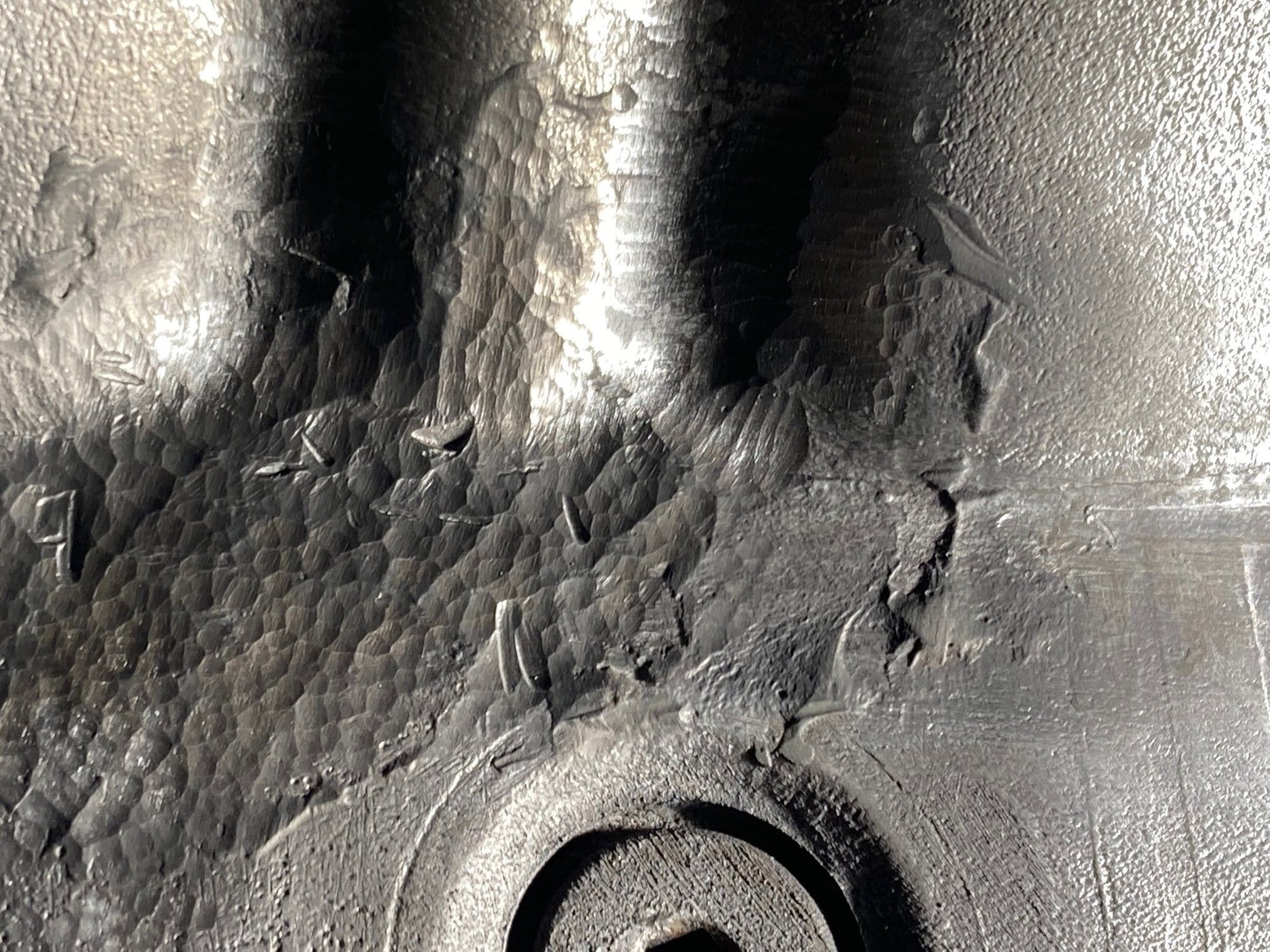
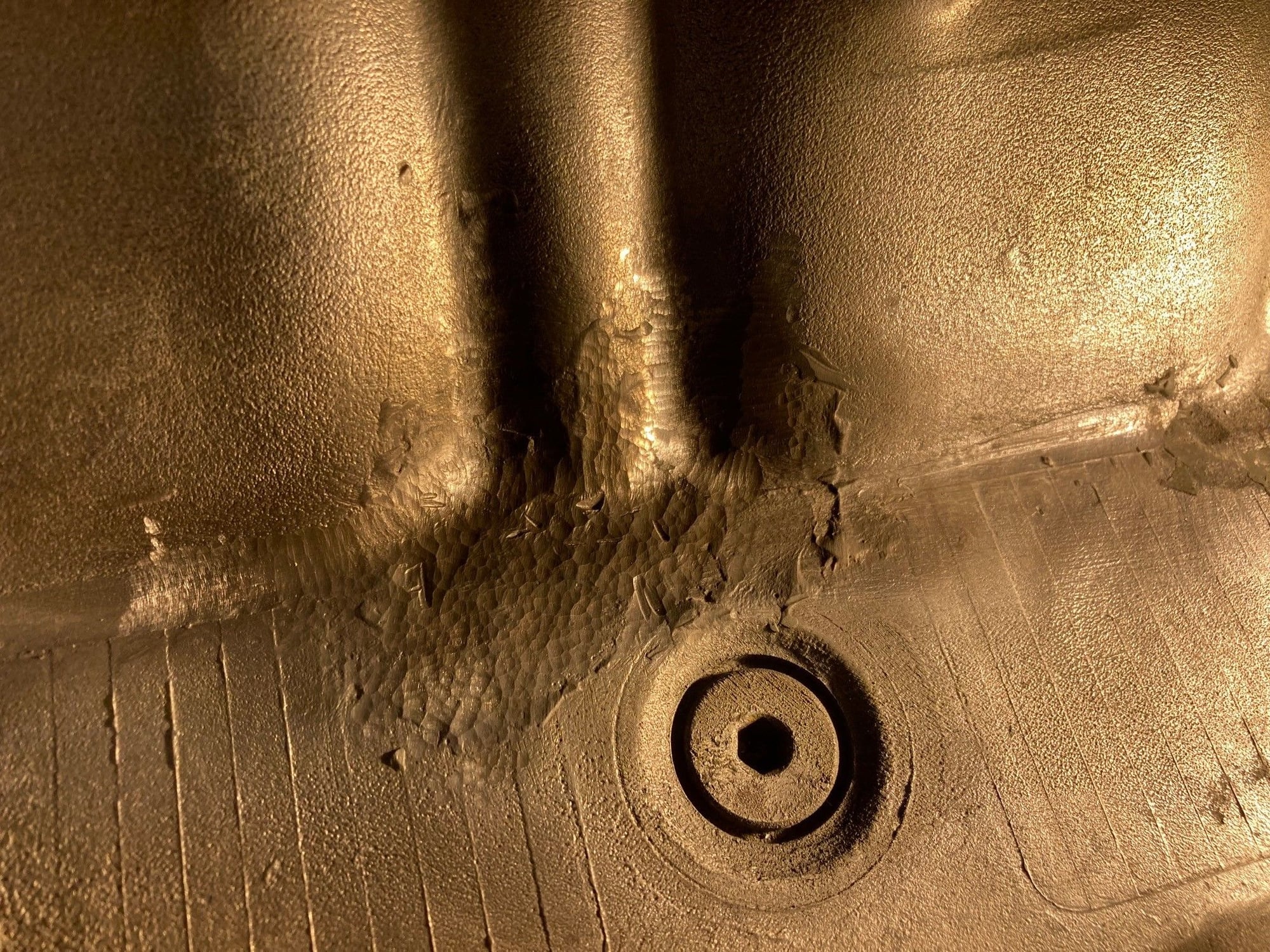
You can see that by removing the chunks of JB Weld of my first fix, the surface has become rather rough ....I even cannot see the crack anymore.
At the 2nd picture on the right hand side you can see a small horizontal line ...but there was no coolant leaking via this line.
The leak concentrates really in the middle where the rough surface is :
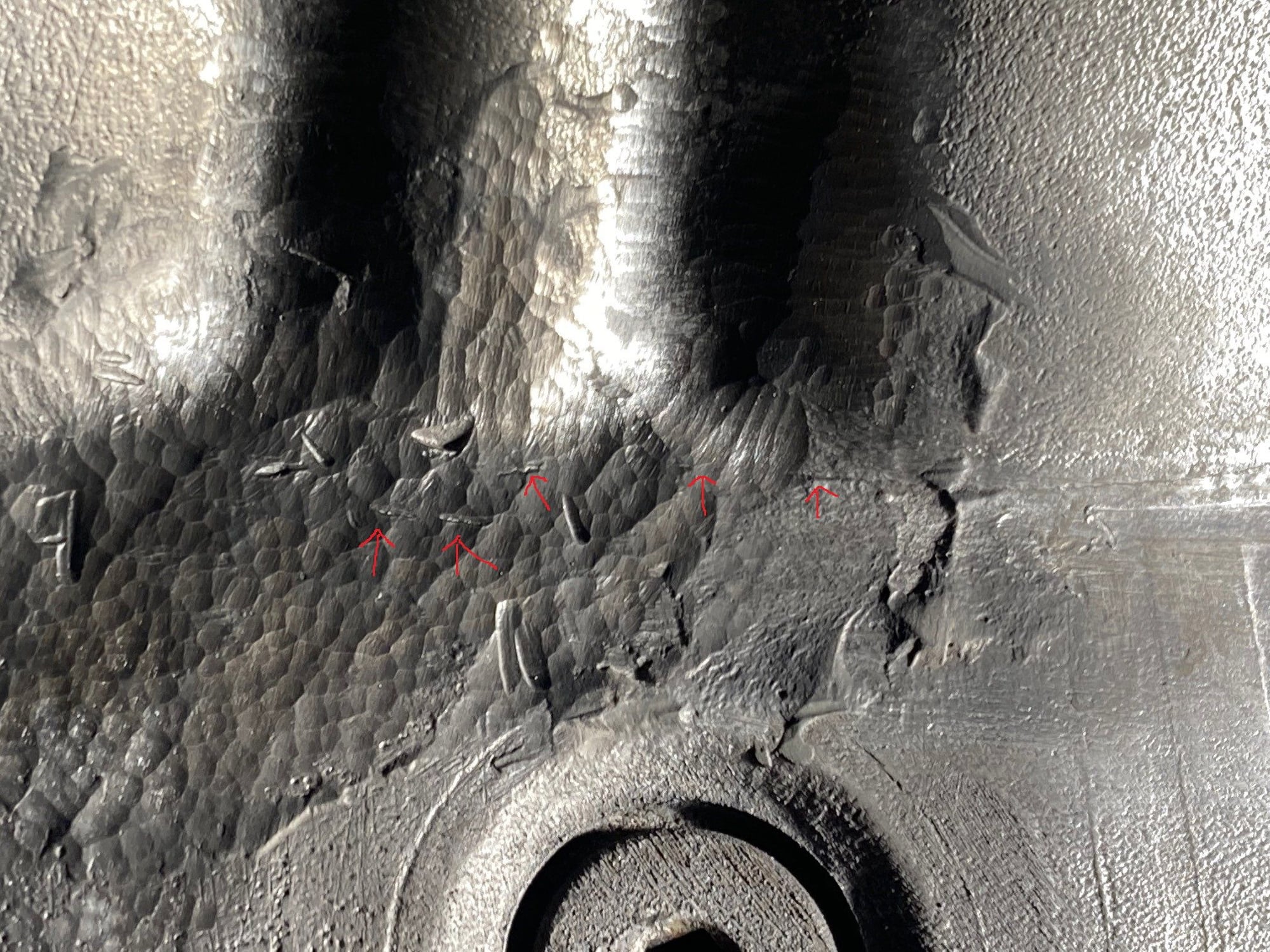
My question : I have an epoxy called Belzona 1212 which is a professional industrial epoxy used in the offshore.
Could I create a sort of aluminium patch over the crack , glued on the engine with this epoxy.
Like this :
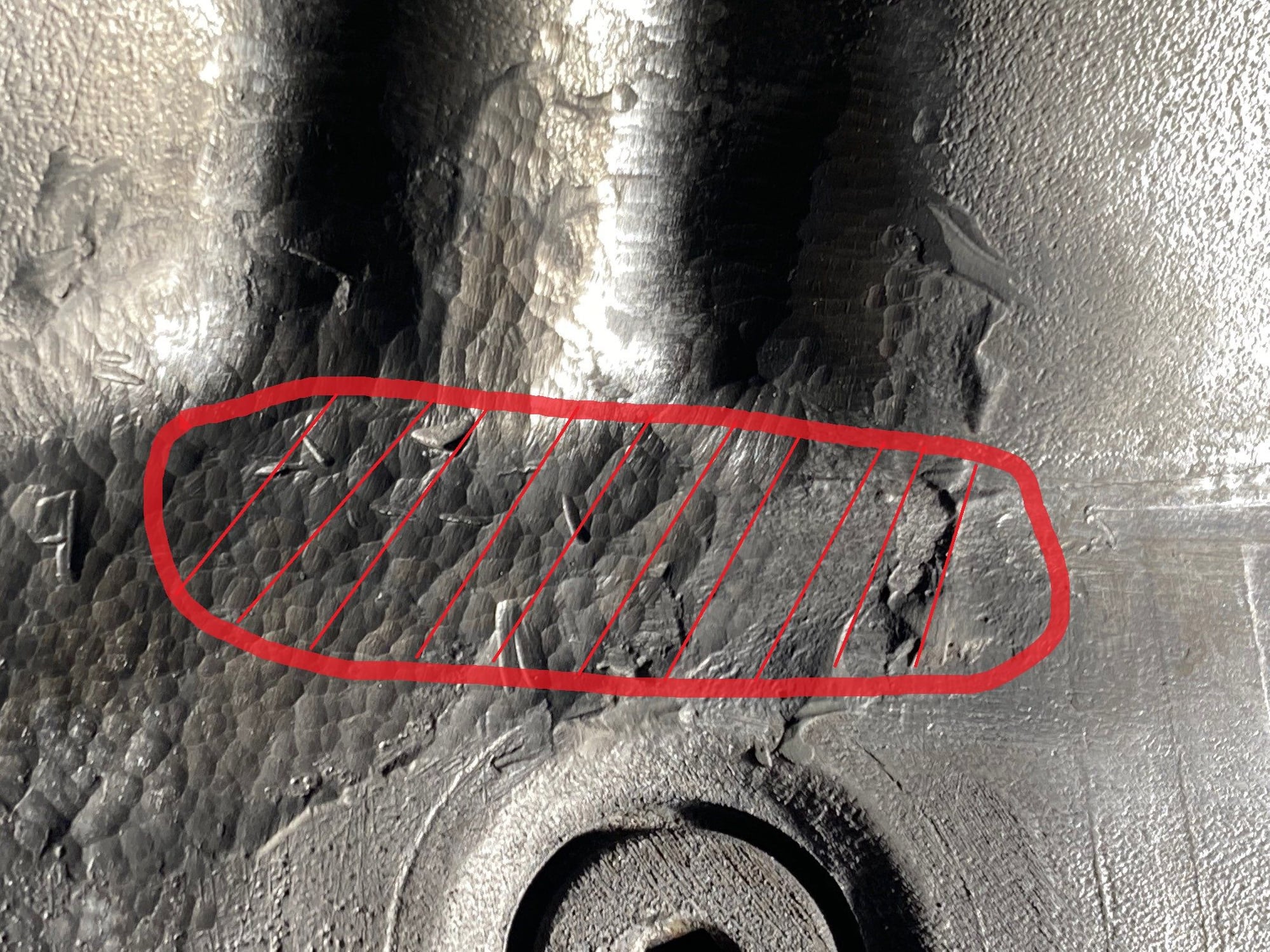
Problem with epoxy is that is rather tough and when the engine heats up, it will tear/crack at the bottom where it is glued over the crack => crack makes expansion larger
My idea was to use a thin aluminium foil (but strong enough to withstand temperatures and expansion forces) and glue it like a patch over the crack.
So when temperature rises, the aluminium will be able to expand together with the alu engine block.
What's your opinion ?
#20

Great ideas here. So a few notes. I am first and foremost and national trainer for weld education specializing in GTAW and I also do a ton of magnesium repair for the 911 market.
That all said with this repair my biggest concern would be getting the area de-gassed as already mentioned . It is clear it's not really a crack but more likely a porous area. If it were me at my shop I would v groove then preheat in the area and do one pass and check for porisity and if need be regroove. The nice thing about GTAW or Oxy fuel for that matter (not that this is an option for this repair) is that typically if the weld looks good on top with good wash in it is likely good all the way through. My concern with having it welded is this.
You ever notice how everyone is a welder? They buy a welder from Eastwood, Amazon, home depot and now they are an expert. I can share that after doing this professionally for 26 years that each and every repair is different and requires a real In person assessment before proceeding. Most folks don't know how to properly assess the repair area. One thing I would suggest for those curious is what some repair videos on you tube. Type in 6061 repair and there is one guy that does nothing but aluminum repair and they are great videos and spell out everything I am talking about.
I would be really hesitant as to whom you bring it to for the repair. I would suggest someone that specializes in aviation repairs. Not an a&p mechanic but rather a welder that holds a repair station license. That is my background and can tell you they are going to be the correct people to get the job done.
Now if you insist on epoxy it is very possible it will work but again it is a glue and it is not an actually one with the parent material.
Clear as mud? Hope it helps a bit.
That all said with this repair my biggest concern would be getting the area de-gassed as already mentioned . It is clear it's not really a crack but more likely a porous area. If it were me at my shop I would v groove then preheat in the area and do one pass and check for porisity and if need be regroove. The nice thing about GTAW or Oxy fuel for that matter (not that this is an option for this repair) is that typically if the weld looks good on top with good wash in it is likely good all the way through. My concern with having it welded is this.
You ever notice how everyone is a welder? They buy a welder from Eastwood, Amazon, home depot and now they are an expert. I can share that after doing this professionally for 26 years that each and every repair is different and requires a real In person assessment before proceeding. Most folks don't know how to properly assess the repair area. One thing I would suggest for those curious is what some repair videos on you tube. Type in 6061 repair and there is one guy that does nothing but aluminum repair and they are great videos and spell out everything I am talking about.
I would be really hesitant as to whom you bring it to for the repair. I would suggest someone that specializes in aviation repairs. Not an a&p mechanic but rather a welder that holds a repair station license. That is my background and can tell you they are going to be the correct people to get the job done.
Now if you insist on epoxy it is very possible it will work but again it is a glue and it is not an actually one with the parent material.
Clear as mud? Hope it helps a bit.
#21
Rennlist Member

Hello Fred,
sorry about my late reply but here are some pics of top of engine where crack is situated.
You can see that by removing the chunks of JB Weld of my first fix, the surface has become rather rough ....I even cannot see the crack anymore.
At the 2nd picture on the right hand side you can see a small horizontal line ...but there was no coolant leaking via this line.
The leak concentrates really in the middle where the rough surface is :
My question : I have an epoxy called Belzona 1212 which is a professional industrial epoxy used in the offshore.
Could I create a sort of aluminium patch over the crack , glued on the engine with this epoxy.
Like this :
Problem with epoxy is that is rather tough and when the engine heats up, it will tear/crack at the bottom where it is glued over the crack => crack makes expansion larger
My idea was to use a thin aluminium foil (but strong enough to withstand temperatures and expansion forces) and glue it like a patch over the crack.
So when temperature rises, the aluminium will be able to expand together with the alu engine block.
What's your opinion ?
sorry about my late reply but here are some pics of top of engine where crack is situated.
You can see that by removing the chunks of JB Weld of my first fix, the surface has become rather rough ....I even cannot see the crack anymore.
At the 2nd picture on the right hand side you can see a small horizontal line ...but there was no coolant leaking via this line.
The leak concentrates really in the middle where the rough surface is :
My question : I have an epoxy called Belzona 1212 which is a professional industrial epoxy used in the offshore.
Could I create a sort of aluminium patch over the crack , glued on the engine with this epoxy.
Like this :
Problem with epoxy is that is rather tough and when the engine heats up, it will tear/crack at the bottom where it is glued over the crack => crack makes expansion larger
My idea was to use a thin aluminium foil (but strong enough to withstand temperatures and expansion forces) and glue it like a patch over the crack.
So when temperature rises, the aluminium will be able to expand together with the alu engine block.
What's your opinion ?
i have pretty much said all that can be said about what is going on here. If you see a hole in the floor full of sh*t the only way to find out how deep it is would be to use a dip stick and if you did not have one I will leave it to your imagingation as to how one has to find out how deep it really is! That is the kind of situation you are currently in. You have already tried a simple repair using a $10 tube of gumbo and despite being well respected it failed miserably.
As with any repair one really neds to know what one is dealing with in order to make an effective assessment of repair options. At the moment we do not have that luxury. It could of course be nothing more than a casting defect that eventually opened up. However the fact that the problem opened up with what to me were clear signs of cracking along the root of the Vee tells me that in all probability this is something rather ominous. The fact that the leak path appeared around the middle cylinders also tells me something if as I suspect frost heave was involved in the failure- that would logically be the path of least resistance as it were.
As I have articulated previously a weld repair is feasible but to do the job properly with the right kind of talent will not be cheap, there are no guarantees that it would be successful and I suspect it would be cheaper to source a new block or short engine.
For purposes of this discussion round I will assume you have made up your mind to go down the epoxy metal route. The Belzona product range as I am concerned are in a class of their own and have used their products a number of times on serious oilfield kit that needed urgent repair- it is amazing stuff and mentioning the word JB weld in the same breath would be equivalent to me saying I could build a 928 motor as good as GB- which of course would be utterly ridiculous- such is the chasm we are talking about here. So forget JB weld and focus on Belzona.
The product line you have mentioned I am well aware of- have seen it used to patch repair a submerged seawater intake cooling line that was doing a good imitation of the Lake Genva fountain! I kid you not you could use that stuff to stick sh*t to a wet blanket it really is that good as are all their products. In this application I would ideally recommend the use of 1511- a high temperature repair grade good for at least 160C. However you need something that is good for about 95C and as I recall the 1212 grade is good for precisely that number [you would need to confirm that] and in theory you could gob it on without any surface preparation whatsoever. The stuff can be further developed by post bonding heat applied at 100C or so. So if you have a tub and it has not expired date wise just go for it. I still recommend maximising surface preparation along the lines I indicated earlier.
For the repair procedure I would be thinking along the lines of a patch repair along the entire length of the Vee which at a guess is about 18 inches long.I would take a piece of aluminium of that length and approx two inches wide [at least 1mm thick] and fold it down the centerline to 45 degrees to match the profile it will cover. I would then form a shutter along the Vee incline and in the base of the valley the same thickness as the proposed layer to be cast. What we are talking about here is a layer of the epoxy whose purpose is to secure the strip to the block. The pressure of the cooling water jacket is to all intents and purposes irrelevant given the minimal escape area involved. So we have a patch that is 450mm long by 50mm wide and for purpsoes of discussion lets say 3mm deep epoxy. Unfortunately that would require 675cm3 of final product mix and each pack like yours contains about 212cm3 in every 450 gm kit. So either you need 3 packs, you thin out the layer to 1mm or fit a shorter length of seal strip of say150mm length in the first instance knowing you could add more later on to fill the length of the Vee on one side if you feel lucky!
The fully cured product has a tensile strength of some 4000 psi. If you used just epoxy and no sealing strip 3mm deep along the Vee it could restrain some 8500 lbs force in total. If you use the aluminium sealing strip that would generate a potential bonding force between the Vee surface of the block and the strip of some 72000 lbs force. In terms of the added resistance to tension caused by detonation the 3mm of epoxy would hold 8500 lbs of lift force and the 1mm aluminium would contain 28000 lb force. So if we wanted to maximise restraint of the cracked block to prevent lift we would need 3mm of aluminium and then the question becomes how big a layer could we build up before something fouls on the kit sitting in the Vee- that point needs to be addressed as I have not got a clue. To mitigate we could consider reducing the bonding layer thickness of 3mm but I am not sure how thin we could go. Again that is a point Belzona should be able to answer for you- I suspect an even layer 1mm thick might do the trick.
Another way of looking at the problem is to try and estimate how much force that joint has to restrain. The pistons in your engine are 96mm diameter as I recall. The maximum pressure generated after combustion occurs at around 14 degrees after TDC and will be approximately 1200 psig so for each firing stroke to restrain the heads requires a force of about 14,000 lbs force. If for purposes of simplicity we assume the force is restained equally by both banks of the head bolts and distributed evenly the damaged side of the block needs to restrain some 7000lbs of force assuming what is present has no value longer term. Although a bit rough and ready I reckon that whatever we did it would probably hold the fort as it were but the strongest option would be a 3mm strip bonded by 1mm of epoxy if that thickness is technically acceptable.
Any notion that the epoxy wiil not bond effectively is complete and utter technical garbage as is the notion that thermal expansion will cause issues.
As a closing anecdote and a source of amusement to me as a young senior engineer back around 1984 I was asked to develop a project for our client- the biggest refiner in the UK who had an excellent central engineering team. The project was to solve a problem on the piping of the marine terminal. Routine inspection revealed that at some tens of thousands of piping support positions the action of the pipe moving over the rub bars had thinned the pipe wall down to retirement thickness and thus we were asked to make a proposal to weld wear pads on the under surface of all those points and that involved welding on live hydrocarbon lines. Not impossible but highly dangerous, very risky asset wise and hugely expensive and time consuming. I developed two proposals- one as per client requirements and one using epoxy to bond the pads into postion. I figured that if NASA could bond ceramic tiles to the space shuttle to resist the heat of re-entry sticking these things on with epoxy and gravity working in our favour this had to be a no brainer. The problem safety wise would mosstly disappear and the technique would have saved many millions of dollars. i would have been the project manager [the youngest in the company's history] and my company would have made a very tidy profit. My proposal was rejected by the oil company's London based engineering team as being "too risky". I was gutted, We lost the project to a technically compliant cheaper bid. My company lost its contract, l lost my promotion and I said "effit" and went to work on a brand new refinery in Saud Arabia and later for their Ministry of Petroleum. Roll the clock on 3 years, Shiekh Yemani got the sack and with it his advisers including me. So back to the UK, Heard the contractor who replaced my company had a new project and went for an interview with their head honcho who wanted me to be their engineering manager - breezed the interview. After the discussion ended my new to be boss advised me that their client's manager wanted to have a coffee with me. A smashing chap who I got on with very well in my first stint. In the course of the discussion I remonstrated comically how dumb their engineers were to have rejected my proposal. Initially he looked a bit dumb struck but then burst out laughing to my puzzlement. He then duly asked me if that was my idea to whit I responded affirmatively and then he advised that my proposal was what they ended up doing. Turned out that their "subject matter expert" rejected my proposal, we lost the award and a few days after the new project was awarded poor chap keeled over at his desk. His sucessor came in, saw the proposal on his desk and thought "what a brililiant idea" . That really pissed me off. The closing anecdote to that story was that on one of the positions the crew were working on they stuck the pad only to realise a few minutes later that they had fitted it such that the pad instead of being centred over the rubbing bar it slipped over was positioned right at the end of the pad and if the pad slipped over the bar it would then be trapped and all kinds of crap might happen as the line would then be anchored in a false position. They got torches out, heated it, jack hammered it, chiselled it, pissed on it, cursed at it but could not budge it so they stuck another pad next to it and called it quits. I suggested a royalty payment was justified- i got the job instead!
Now ask me how I know about Belzona 1212!
The following 3 users liked this post by FredR:
#22
Rennlist Member

Flex tape is what you need 

#23
Rennlist Member
Join Date: Aug 2014
Location: Adirondack Mountains, New York
Posts: 2,415
Received 315 Likes
on
165 Posts

I have a PhD in metallurgy (thesis topic: crack propagation) and did R&D on hot section metallurgy for jet engines for the leading manufacturer. Here's what I've been thinking: do not post anything in this thread, because it will make me seem stupid. Problems like this one require a great deal of specific practical experience, about which I am indeed stupid.
But a few simple observations, with a decent chance of being correct: It looks like someone has peened the area of the leak, for which there was a chance that the compressive layer might seal the leak (until corrosion opens it up) (was that mentioned above? did Porsche do it at the factory?) The cracking is consistent with solidification shrinkage, but also with intergranular corrosion.
One more: those are excellent macro photographs of the cracking, Gerrit. They're what has led me to ignore my own advice. But metallurgists are infamous for insisting that something be sectioned for a proper analysis. The joke was that if you were to hand your non-working watch to a metallurgist, the first thing they'd want to do is cut it up.
But a few simple observations, with a decent chance of being correct: It looks like someone has peened the area of the leak, for which there was a chance that the compressive layer might seal the leak (until corrosion opens it up) (was that mentioned above? did Porsche do it at the factory?) The cracking is consistent with solidification shrinkage, but also with intergranular corrosion.
One more: those are excellent macro photographs of the cracking, Gerrit. They're what has led me to ignore my own advice. But metallurgists are infamous for insisting that something be sectioned for a proper analysis. The joke was that if you were to hand your non-working watch to a metallurgist, the first thing they'd want to do is cut it up.
The following users liked this post:
merope (04-06-2022)
#24
Rennlist Member
Thread Starter

Is there a way to measure cracks through metal with a special device ? I need to make sure whether crack is all the way over 2 or more cilinders or just a corrosion through the surface .
#27
Rennlist Member

This is not a corrosion issue it is a mechanical failure issue. It could be a localised failure due to a casting defect that has propagated until the point where there is a through communication from the main cooling chamber to the base of the Vee. The head bolts are anchored next to the axis of the crank and stop the cylinder heads from going into orbit- action and reaction are equal and opposite assuming Sir Isaac knew what he was talking about and therefore a casting defect could explain this and with time, vibration and cyclic heat stresses crack propagation should such a defect be present is a very distinct possibility. Your original thread and the pictures therein show what appeared to be a very distinct axial crack at the base of the Vee, around the middle cylinders and some two inches or so long. if the problem is contained to that location it is still going to propagate with time. That is the "upside" or "best case scenario" as it were. If this is the case then you do not know where the crack originated or whether the problem travelled inside to outside or vice versa.
The downside is if frost heave was involved in the failure one might expect the problem to be worse around the middle cylinder area around the base of the head bolts or perhaps more so in your case if your motor deploys stud bolts - thus my suspicions. Even worse, you would not know if any damage was sustained on the other bank that has just not come to the surface [yet] given the same fluid was in the engine with similar environmental exposure.
Whatever the cause the trouble is you do not know the extent of the problem and the best scenario you can hope for using material currently available to you is to make a repair such that it might just slow down the rate of propagation or seal off the attrition to buy you an increement of service life that at the moment is zero hours without in-flight refuelling of coolant!.
As to trying to determine the extent of the problem I have previously suggested to try some dye pen testing to indicate whether the surface cracking goes beyond what you could visibly see originally. Same would apply to the base of the cooling chamber were the cylinder heads off. The only other viable NDT tests are ultrasonic testing and radiography and then the bills start mounting. I am not sure you could get a meaningful external UT examination done given the local geometry - in that regard you would need an opinion from a skilled pratcitioner- I suspect that to achieve such you would need to have the engine stripped down and shoot the area from the inside of the crankcase. Probably much the same for radiographic examination.
Thus the simplest and lowest cost option you have at the moment is to go for the approach I suggested with full contact coverage along the base of the Vee. It might just bale you out and will cost you next to nothing to try it. That or try an overlapping strip 6 inches long and keep your fingers crossed a bit tighter. I have demonstrated why the aluminium brace approach improves your chances of success quite dramatically. Alternatively just gob some 1212 over the general area and flip a coin.
"Chance favours the prepared mind"
#28
Rennlist Member

I was wandering around the 944 board and came across a different idea for you. I'm sure there are a ton of not-fantastic reasons to do this, some of which I can even think of myself but... What about a wicking threadlocker like Loctite 294? The specs I read on it talk about temperature resistance of 450 deg F. It seems sort of reasonable, if you don't go the patch or welding paths. I don't think that it would stop crack propagation, but it is formulated to put itself into every place that there's already a crack. (There's a joke to be made there which I will leave alone, lest it follow me forever; this is the internet, after all).
Cheers
Cheers
#29
Rennlist Member

I was wandering around the 944 board and came across a different idea for you. I'm sure there are a ton of not-fantastic reasons to do this, some of which I can even think of myself but... What about a wicking threadlocker like Loctite 294? The specs I read on it talk about temperature resistance of 450 deg F. It seems sort of reasonable, if you don't go the patch or welding paths. I don't think that it would stop crack propagation, but it is formulated to put itself into every place that there's already a crack. (There's a joke to be made there which I will leave alone, lest it follow me forever; this is the internet, after all).
Cheers
Cheers
It was this class of product we first used to solve the flexplate clamp TBF issue 23 years ago. The initial recommendation from Earl Gilstrom was to use Loctite 290, I used Loctite 270 due to local availability. Earl did the first application - I did the 2nd one a day later and solved a problem not even Porsche could solve. Some folks said it would never work - my 23 years of experience with it says otherwise along with the many owners who consulted me as to how to apply it and make it work - some said "we would never be able to get it undone" but that was a crock- in the case of the front flexplate clamp you simply remove the pinch bolt, get a wood working chisel and hammer it gently into the gap the bolt pulls tight- easy peasy. The stuff cannot seem to handle tensile stress, Thus if you stick it in the "crack" of this "thread" I suspect one heat cycle will render it totally useless as it would not be able to handle the expansion/contraction difference or so I would think
.
There may well be some "cracks" it might seal but not this one!
Last edited by FredR; 04-05-2022 at 02:00 AM.
#30
Rennlist Member

Thanks Fred, that's some good information. Despite my background, I had no idea that Loctites are acrylates. I might have even looked for an SDS at some point, to figure out what made all these Henkel products so dang expensive but whatever I found, it obviously didn't stick (ba-dum, bump).
Anyway, I completely agree that these acrylates are going to be brittle and likely not stand up to the constant contraction and expansion that the block will experience.
Cheers
Anyway, I completely agree that these acrylates are going to be brittle and likely not stand up to the constant contraction and expansion that the block will experience.
Cheers