'87 S4 Timing Death
#391
Inventor
Rennlist Member
Rennlist Member

You fail to see that failures occur with the stock system. Many people have seen themselves what can happen with a poorly maintained stock system.
You yourself admitted you had a belt jump at least once with the stock system, fortunately without damage. You blame it on the belt or whatever but stuff happens.
No one has had a problem, but you are 'creating' one out of loincloth.
#392
Nordschleife Master

I do think there's value in trying to think all these things thru using engineering physics. You may disagree, which is fine. Using the engineering physics, to best of my ability, requires reading books and using a computer. Not everyone uses those tools. I am working on just a couple of 928 engines and very slowly at that, so I will have to do as much theory as I can. To the extent I post those ruminations here, I'm hopefully always clear what the source of the statements is and what's the appropriate confidence one should have in them.
I'd say that when various "professionals" here start slinging mud, I've found it very useful to me to compare various statements with what Newton and successors have come up with over the centuries. It's not enough to build an engine for sure, but it can sometimes separate factual statements from fictional ones.
Each to their own.
I'd say that when various "professionals" here start slinging mud, I've found it very useful to me to compare various statements with what Newton and successors have come up with over the centuries. It's not enough to build an engine for sure, but it can sometimes separate factual statements from fictional ones.
Each to their own.
#393
Nordschleife Master

I posted the chart to answer your question as you were wondering why the whole thing didn't fall off in a year. I think the graph answers that question. You don't get enough cycles. I can't think of an easier and more reliable way to answer that question that looking the fatigue properties of the materials up.
Heh, the guy that contracted the belt to be made by Gates (Roger) told me they were made with Kevlar.....and I've read several different conflicting descriptions of what they are made from....
Don't think this is something that I need to correct.
Look, I get that you are as giddy as a school girl about this system and think it's the best thing since sliced bread.....rhat's cool with me.
I understand that the original design has its own limitations and I'm sure that a properly engineered hydraulic damper/tensioner would work much better....I have no argument with that.
I just don't feel that a random Audi piece, made for a shorter lighter belt, plucked off of NAPA's shelf, in a completely different application, is automatically the correct solution to keep this long belt with completely different camshaft arrangement properly tensioned. I don't feel that a steel bracket "stuck" on the front of an aluminum engine is a long term solution. I think that arbitrarily deciding that the lower rollers are "vestigial" borders on stupidity. And, as an engine builder (something you would not understand), trying to accurately set the cam timing with this system is a virtual guessing game.
I understand you love the system and can find no faults with it, support it to the point of making random crap up.
Seems like I should be able to have a contrary point of view.....especially given that I've installed 1000's of stock tensioners, without one single failure. None.
Just because you drank the Koolaid, that doesn't mean it is a good idea to jump back in line for another cup, while ignoring the dying people around you....
Don't think this is something that I need to correct.
Look, I get that you are as giddy as a school girl about this system and think it's the best thing since sliced bread.....rhat's cool with me.
I understand that the original design has its own limitations and I'm sure that a properly engineered hydraulic damper/tensioner would work much better....I have no argument with that.
I just don't feel that a random Audi piece, made for a shorter lighter belt, plucked off of NAPA's shelf, in a completely different application, is automatically the correct solution to keep this long belt with completely different camshaft arrangement properly tensioned. I don't feel that a steel bracket "stuck" on the front of an aluminum engine is a long term solution. I think that arbitrarily deciding that the lower rollers are "vestigial" borders on stupidity. And, as an engine builder (something you would not understand), trying to accurately set the cam timing with this system is a virtual guessing game.
I understand you love the system and can find no faults with it, support it to the point of making random crap up.
Seems like I should be able to have a contrary point of view.....especially given that I've installed 1000's of stock tensioners, without one single failure. None.
Just because you drank the Koolaid, that doesn't mean it is a good idea to jump back in line for another cup, while ignoring the dying people around you....
#394
Inventor
Rennlist Member
Rennlist Member

The PKT bracket had to fit through the stock hole in the cover, be hardly flexible, and had to be a minimum thickness so that the belt would be centered on the pulley*. Given these constraints, mild steel was the best option, with its low modulus and high fatique resistance vs. aluminum.
Many of the very early 928 brackets were formed and welded steel. The starter bracket 83-95 is cast steel.
*Which is wider than the belt, one piece and machined flat. Compare to the thin stamped steel two piece riveted factory pulley.
Many of the very early 928 brackets were formed and welded steel. The starter bracket 83-95 is cast steel.
*Which is wider than the belt, one piece and machined flat. Compare to the thin stamped steel two piece riveted factory pulley.
#395
Former Sponsor

I do think there's value in trying to think all these things thru using engineering physics. You may disagree, which is fine. Using the engineering physics, to best of my ability, requires reading books and using a computer. Not everyone uses those tools. I am working on just a couple of 928 engines and very slowly at that, so I will have to do as much theory as I can. To the extent I post those ruminations here, I'm hopefully always clear what the source of the statements is and what's the appropriate confidence one should have in them.
I'd say that when various "professionals" here start slinging mud, I've found it very useful to me to compare various statements with what Newton and successors have come up with over the centuries. It's not enough to build an engine for sure, but it can sometimes separate factual statements from fictional ones.
Each to their own.
I'd say that when various "professionals" here start slinging mud, I've found it very useful to me to compare various statements with what Newton and successors have come up with over the centuries. It's not enough to build an engine for sure, but it can sometimes separate factual statements from fictional ones.
Each to their own.
You have no practical experience so you are required to use theory. I have 50 years of practical experience and use my own head.
As I said, I've yet to remove or see removed a Portensioner bracket that hasn't been "working" on the front of a 928 engine.
Not "witness" marks where it got bolted down, but actual "movement" marks.
In the engineering world, "movement" marks are the precursor to failure. Movement means wear. Wear means loose hardware. Loosent hardware means failure.
There's not a single automotive company, race team, or qualified engineer thst would see movement between two metal pieces and let it go.
No one. Anywhere.
Yet, in this application you've decided that this is perfectly normal.
Sorry, I'm going to go with what I know, this time.
#396
#397
Nordschleife Master

There's also the problem that although you may have the experience, I don't trust you telling the truth on this matter.
There's one of the very basic differences between me and you.
You have no practical experience so you are required to use theory. I have 50 years of practical experience and use my own head.
As I said, I've yet to remove or see removed a Portensioner bracket that hasn't been "working" on the front of a 928 engine.
Not "witness" marks where it got bolted down, but actual "movement" marks.
In the engineering world, "movement" marks are the precursor to failure. Movement means wear. Wear means loose hardware. Loosent hardware means failure.
There's not a single automotive company, race team, or qualified engineer thst would see movement between two metal pieces and let it go.
No one. Anywhere.
Yet, in this application you've decided that this is perfectly normal.
Sorry, I'm going to go with what I know, this time.
You have no practical experience so you are required to use theory. I have 50 years of practical experience and use my own head.
As I said, I've yet to remove or see removed a Portensioner bracket that hasn't been "working" on the front of a 928 engine.
Not "witness" marks where it got bolted down, but actual "movement" marks.
In the engineering world, "movement" marks are the precursor to failure. Movement means wear. Wear means loose hardware. Loosent hardware means failure.
There's not a single automotive company, race team, or qualified engineer thst would see movement between two metal pieces and let it go.
No one. Anywhere.
Yet, in this application you've decided that this is perfectly normal.
Sorry, I'm going to go with what I know, this time.
#398
Former Sponsor

Great example.
Now tell everyone that the starter bracket it is rigidly held in place with two steel circular locating dowels, countersunk into the aluminum and the bracket, to keep it from moving.
Glad you dropped into this part of the conversation.
Have you seen the "movement" on your own bracket, like I have.?
Certainly you've seen way more removed brackets than I have...
Now tell everyone that the starter bracket it is rigidly held in place with two steel circular locating dowels, countersunk into the aluminum and the bracket, to keep it from moving.
Glad you dropped into this part of the conversation.
Have you seen the "movement" on your own bracket, like I have.?
Certainly you've seen way more removed brackets than I have...
#399
Nordschleife Master

I have pulled off a number for secondary belt changes, and upgrading to the PKT black version.
I have not witnessed any movement indications on any of them that I have installed.
I am used to looking for that movement from my time working on hydraulics and seeing the for/aft plate lift and move due to excessive pressure.
Added as a data point.
My comment about what Audi and VW do when the T/D is out of range was more so looking to see if there is an already "engineered" solution. I doubt that they drill the holes out either. But I've seen far far dumber stuff come out of factories. Ford triton spark plugs are a great example of how smart some engineers are.......
I have not witnessed any movement indications on any of them that I have installed.
I am used to looking for that movement from my time working on hydraulics and seeing the for/aft plate lift and move due to excessive pressure.
Added as a data point.
My comment about what Audi and VW do when the T/D is out of range was more so looking to see if there is an already "engineered" solution. I doubt that they drill the holes out either. But I've seen far far dumber stuff come out of factories. Ford triton spark plugs are a great example of how smart some engineers are.......
#400
Inventor
Rennlist Member
Rennlist Member

No. Regardless of your glee in your new theory, I have not seen anything like you indicate.
Again, no problems have been reported with the current design. All bolts have been reported as tight when removed.
Again, no problems have been reported with the current design. All bolts have been reported as tight when removed.
#401
Rennlist Member

No. Regardless of your glee in your new theory, I have not seen anything like you indicate.
Again, no problems have been reported with the current design. All bolts have been reported as tight when removed.
Again, no problems have been reported with the current design. All bolts have been reported as tight when removed.
I also told you that the fasteners were much looser than I expected-- not finger-loose but certainly took much less than the original torque to remove.
Here is the picture that I shared at that time, the block side of the gasket under our PKT when it was removed after 70K miles. The ridge around the edge of mounting boss can only be formed if there was movement, and there must certain have been movement-- no clamping force in the world will resist the thermal expansion of a big hunk of aluminum.
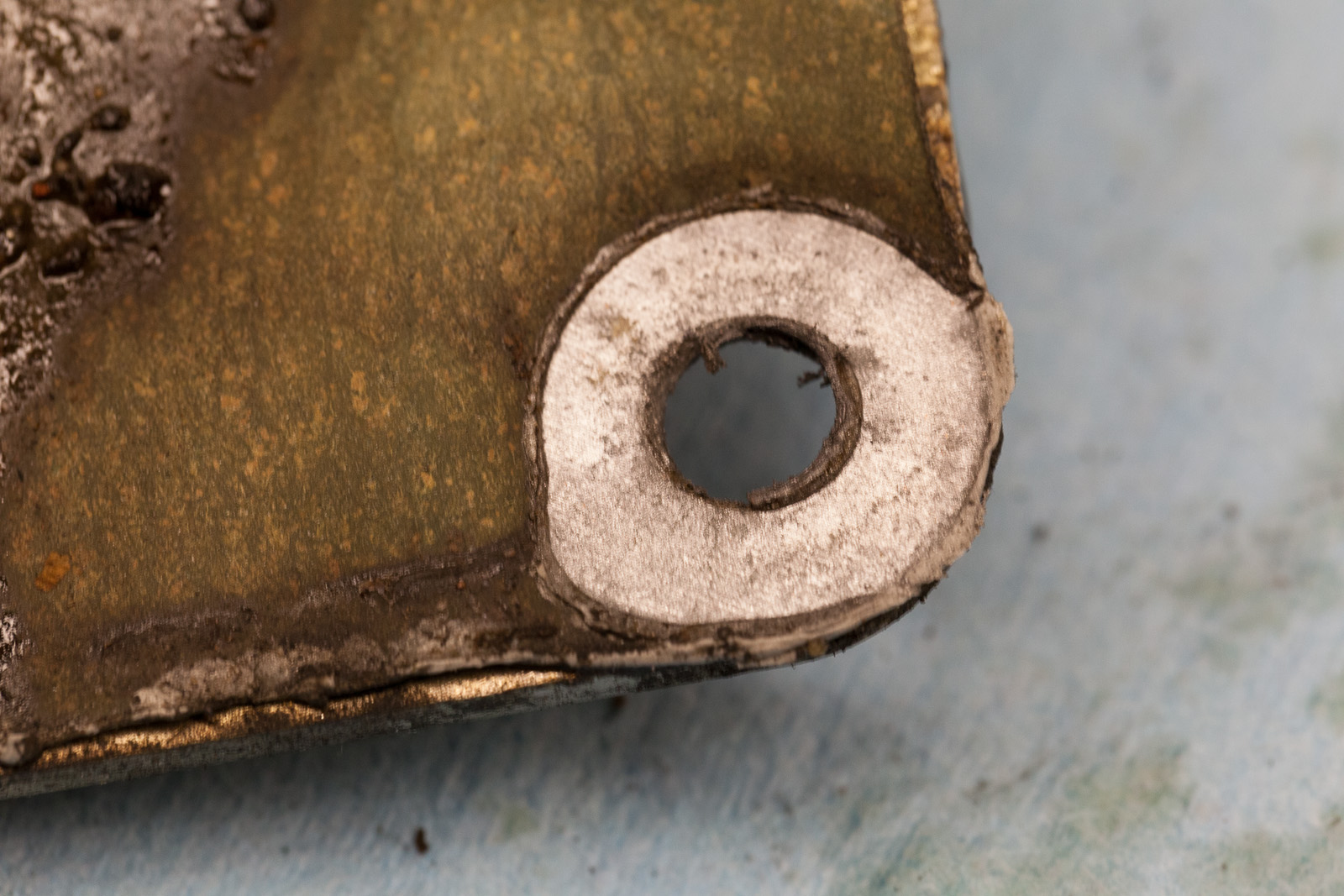
#402
Inventor
Rennlist Member
Rennlist Member

You will find the same 'wear' on the factory tensioner. The gasket is no longer specified for the PKT.
Bolt tension should be checked at each belt change and is required by the design of the PKT-B (or hardware update pack) if replacing the lever and pulley.
#403
Inventor
Rennlist Member
Rennlist Member

The bracket had nothing to do with the anomaly of this low mileage installation.
Is it possible we get back to factual discovery instead of primae donnae posturing?
Is it possible we get back to factual discovery instead of primae donnae posturing?
#404
Pro
Thread Starter

Yes. Not today, as I am off for the weekend. Assume you are standing in front of this car. The belt has been removed, along with the tensioner roller and crank gear. Everything else is still in place as installed back in 2013. What would you do next?
#405
Pro
Thread Starter