Changing half shaft axle boots
#31
Chronic Tool Dropper
Lifetime Rennlist
Member
Lifetime Rennlist
Member

Hi Fred--
Once I got the inner joint sort of cleaned and the snap ring was off, I cut the inner boot to make room for a dead-blow hammer, and just tapped the spider off the shaft. No press was needed.
WSM shows no thread lock on the inner drive flange bolts, and that's worked OK for me so far. The 60+ lbs/ft seems to be enough particularly in the service my car sees. You can see my efforts above holding the end of the driver in the bolts while Rob did the hard work -- he set the parking brake and actually turned the torque wrench, then released the brake so I could spin the other wheel (to line up the opposing bolt in the pattern) and get the driver into the new bolt. I've done it single-handed, just took better aim than I'm used to needing. I seldom need to aim a 32" extension that accurately, but with a little patience you'll get the hang of it.
Once I got the inner joint sort of cleaned and the snap ring was off, I cut the inner boot to make room for a dead-blow hammer, and just tapped the spider off the shaft. No press was needed.
WSM shows no thread lock on the inner drive flange bolts, and that's worked OK for me so far. The 60+ lbs/ft seems to be enough particularly in the service my car sees. You can see my efforts above holding the end of the driver in the bolts while Rob did the hard work -- he set the parking brake and actually turned the torque wrench, then released the brake so I could spin the other wheel (to line up the opposing bolt in the pattern) and get the driver into the new bolt. I've done it single-handed, just took better aim than I'm used to needing. I seldom need to aim a 32" extension that accurately, but with a little patience you'll get the hang of it.
#32
Rennlist Member
Thread Starter

Hi Fred--
Once I got the inner joint sort of cleaned and the snap ring was off, I cut the inner boot to make room for a dead-blow hammer, and just tapped the spider off the shaft. No press was needed.
WSM shows no thread lock on the inner drive flange bolts, and that's worked OK for me so far. The 60+ lbs/ft seems to be enough particularly in the service my car sees. You can see my efforts above holding the end of the driver in the bolts while Rob did the hard work -- he set the parking brake and actually turned the torque wrench, then released the brake so I could spin the other wheel (to line up the opposing bolt in the pattern) and get the driver into the new bolt. I've done it single-handed, just took better aim than I'm used to needing. I seldom need to aim a 32" extension that accurately, but with a little patience you'll get the hang of it.
Once I got the inner joint sort of cleaned and the snap ring was off, I cut the inner boot to make room for a dead-blow hammer, and just tapped the spider off the shaft. No press was needed.
WSM shows no thread lock on the inner drive flange bolts, and that's worked OK for me so far. The 60+ lbs/ft seems to be enough particularly in the service my car sees. You can see my efforts above holding the end of the driver in the bolts while Rob did the hard work -- he set the parking brake and actually turned the torque wrench, then released the brake so I could spin the other wheel (to line up the opposing bolt in the pattern) and get the driver into the new bolt. I've done it single-handed, just took better aim than I'm used to needing. I seldom need to aim a 32" extension that accurately, but with a little patience you'll get the hang of it.
not sure what you mean by "snap ring" -presumably the indented "circlip" as I would call it?
I followed your photo with the long extension but the hex socket I had was not up to it as it rounded the tool edges on the second bolt - thought I had crapped out and the bolt was shot but I have a very robust set of extended allen keys so tried the 8mm one with a tube over it for extra leverage- it was a right royal pain in the butt and each bolt I had to position it such that I could get the key and sleeve positioned so that I could get the requisite amount of travel from underneath. I then had crawl from underneath, set the handbrake and put the gear lever in P. Maybe the handbrake would have been enough but...? After undoing the 6 bolts the shaft dropped from the inner drive flange and I used a wooden drift and a hammer to pop the stub axle out of the wheel carrier. Tested my back and stomach muscles- now got the start of a 6 pack once more!
I was looking at the inner joint to see if I could jury rig something to drive it off without damaging anything. First of all have to de-grease the thing. It sure is a messy job. I reckon one has to try these things.
Only one boot has split but the three others are tired and it is only a question of a short time before the next one let's go.
Rgds
Fred
#33
Chronic Tool Dropper
Lifetime Rennlist
Member
Lifetime Rennlist
Member

Hi Fred--
Circlip, snap-ring, same thing I suspect. Separated by the same language.
Get the joint cleaned up some, and cut off the boot. With the circlip removed and all the crud out of the splines where the circlip lives, a few taps of a plastic or other soft-faced mallet will get it off smartly. Note the direction it sits on the shaft so it can go back the same way it was. Then clean-clean-clean, pack-pack-pack, boots and clamps.
I all the way with you on changing all 4 at the same time. It's reasonable to expect that the other three have seen pretty much the same duty as the one you are changing. Plus, as sure as I try to shortcut by replacing just the inner, the outer will fail soon after, and I get to do both this time. I think that doing all of them at once is the real shortcut method. You'll sleep better, knowing all is good back there.
Circlip, snap-ring, same thing I suspect. Separated by the same language.
Get the joint cleaned up some, and cut off the boot. With the circlip removed and all the crud out of the splines where the circlip lives, a few taps of a plastic or other soft-faced mallet will get it off smartly. Note the direction it sits on the shaft so it can go back the same way it was. Then clean-clean-clean, pack-pack-pack, boots and clamps.
I all the way with you on changing all 4 at the same time. It's reasonable to expect that the other three have seen pretty much the same duty as the one you are changing. Plus, as sure as I try to shortcut by replacing just the inner, the outer will fail soon after, and I get to do both this time. I think that doing all of them at once is the real shortcut method. You'll sleep better, knowing all is good back there.
#34
Chronic Tool Dropper
Lifetime Rennlist
Member
Lifetime Rennlist
Member

Forgot....
I use an impact-rated driver, which seems to be a lot better at not rounding than most 'common' drivers. Downside is that the tip is not replaceable, and the hex is pretty short so no chance to grind back the end to get to "fresh" hex corners if it does get damaged.
I use an impact-rated driver, which seems to be a lot better at not rounding than most 'common' drivers. Downside is that the tip is not replaceable, and the hex is pretty short so no chance to grind back the end to get to "fresh" hex corners if it does get damaged.
#35
Rennlist Member
Thread Starter

Forgot....
I use an impact-rated driver, which seems to be a lot better at not rounding than most 'common' drivers. Downside is that the tip is not replaceable, and the hex is pretty short so no chance to grind back the end to get to "fresh" hex corners if it does get damaged.
I use an impact-rated driver, which seems to be a lot better at not rounding than most 'common' drivers. Downside is that the tip is not replaceable, and the hex is pretty short so no chance to grind back the end to get to "fresh" hex corners if it does get damaged.
Impact sockets and tools do have harder steel- or so I believe. Just itching to have a go with my new windy gun.
Rgds
fred
#36
Chronic Tool Dropper
Lifetime Rennlist
Member
Lifetime Rennlist
Member

Those drive flange bolts wouln't be a place to test the new tool. Impacts on final drive parts do funny damage, like put little flat spots in places where they aren't supposed to be flat. Watched a good-sized industrial reduction box getting torn down for bearings, without heat to pull off the drive coupling on the pinion. Extra-large industrial impact managed to break a couple teeth off the 15"-diameter pinion inside. Not pretty!
#37
Rennlist Member
Thread Starter

Those drive flange bolts wouln't be a place to test the new tool. Impacts on final drive parts do funny damage, like put little flat spots in places where they aren't supposed to be flat. Watched a good-sized industrial reduction box getting torn down for bearings, without heat to pull off the drive coupling on the pinion. Extra-large industrial impact managed to break a couple teeth off the 15"-diameter pinion inside. Not pretty!
I was thinking more the wheel nuts on my landlords MB or his wife's BMW! Probably the latter as he is a really nice chap.
Not sure why I bought the thing- just seemed like a good idea at the time. Damm thing is very heavy- with all the tools I purchased from amazon in the UK I had 22kg in my carry on [had to go in the hold of course] and the weight broke one of the wheels. At least Emirates allow 30kg and that was exactly what I had when the torque wrench and the breaker bar were thrown in.
The customs officer at Oman International airport was rather enthused by the contents!
Rgds
Fred
#38
Rennlist Member
Thread Starter

Took your advice this afternoon, cut the boots off, degreased in petrol [drained the tank of about 30 litres] , dropped the dust shroud from the rear of the transmission end bearing and made a drift out of the 1/2 inch hex socket I reported on, sat it on a washer same size as the shaft and used a extension bar on the socket and sat the job lot on my Black and Decker work mate adjacent to the main support beam. Gradually upped the ante with my hammer and hey presto the shaft was out. Would have been easier with a "bigger hammer" but do not trust myself with such!
Everything now ready to go back assuming I can get the thing back on - just not sure how I am going to achieve that but that is a problem for tomorrow. Interestingly when you remove the rear shroud you have to be careful or your ***** will drop off!
One thing I did notice and could do with some input- on Dwayne's right up he says that the bearing with the raised [about 1m] face should be outboard if I understood the write up correctly. On both my shafts the raised faces were facing inboard [as in toward the middle of the shaft]. Any comments?
Some pics herein:
Last edited by FredR; 11-20-2015 at 01:54 PM.
#39
Rennlist Member

I am currently beached pending arrival of some new axle boot kits. I am currently contemplating whether to do this myself or farm it out [too dammed hot at the moment].
If I am dumb enough to take this on in our heat much appreciate any thoughts as to how to go about this task taking into consideration I would be working from axle stand height.
From an initial inspection of the job at hand it looks as though it should be a straight forward affair but details of how best to undo and which end to undo first appreciated. I get the impression it would be best to work from underneath the car attacking the bolts both ends from the low point and rotate the axle until all bolts are loose and then remove the shaft. is it better to remove the inside flange and then the outside flange for instance [or the reverse]?
Thanks for any inputs
Regards
Fred
If I am dumb enough to take this on in our heat much appreciate any thoughts as to how to go about this task taking into consideration I would be working from axle stand height.
From an initial inspection of the job at hand it looks as though it should be a straight forward affair but details of how best to undo and which end to undo first appreciated. I get the impression it would be best to work from underneath the car attacking the bolts both ends from the low point and rotate the axle until all bolts are loose and then remove the shaft. is it better to remove the inside flange and then the outside flange for instance [or the reverse]?
Thanks for any inputs
Regards
Fred
since you already are knee deep in it.. how are you tightening the final boot clamps...
best of luck!
#40
Rennlist Member
Thread Starter

its a mess and a disaster... just buy the set complete with the axles and boots already installed. i did it once and it was a pain and i ended up not having the clamps on correctly (not able to tighten them with the right clamp tigthening tool) the came loose, grease everywhere. a disaster! for the $100 bucks you save, its not worth it to do it yourself. I think anyway!
since you already are knee deep in it.. how are you tightening the final boot clamps...
best of luck!
since you already are knee deep in it.. how are you tightening the final boot clamps...
best of luck!
If I could find someone to do the job reliably for me for the princely sum of $100 this thread would not exist. Not sure what the official hours are for this task but I expect it is probably about 6 to 8 hours for someone who knows what he is doing and presumably in the States you are talking about $100/hr for a non franchise dealer who is worth paying for.
The main agents over here are quite reasonable but still charge in the $80/hr region but cost saving is not really the issue [for me at least].
It is a very messy job but at the moment I am kind of enjoying it as I like to take on as much as I can when the weather is nice and at the moment I have time on my hands. Not a major incumbrance considering this task is only required once every 10 years I would say.
You raise a fair point about the clamps and I was going to raise this issue in the next day or two. The clamps supplied are of a type I have seen but not installed before and they look a bit like a jubilee clamp but do not have a worm drive. They are secured by two lugs and then crimp pinched into position. As you rightly suggest, knowing when enough is enough is the very next question I was going to pose to the list hoping that my half shaft guru [Dr Bob] will have an answer [edit: pic now loaded].
I have also noticed that my half shafts as installed [for the last 10 years] had no gaskets whatsoever and there are non in the kit I received from Roger so presume they are not needed but the manual and Dwayne's write up show two gasket locations- one of them for sure is not needed as there is a metal cover sandwiched on the end between the bearing and the tranny drive flange. I might put a very thin smear of RTV between the inboard metal cover and the bearing body but I doubt that should leak grease.
Given the boots seat in a well designed detente I doubt they need much tension on the clamp to seal them but as you rightly say, with anything of this nature it is important to get the correct tightness without squeezing the crap out of the clamp. Did yours fail because of over tightening or under tightening as a matter of interest?
The job sure beat the snot out of my wife's rubber kitchen gloves but they protected my delicate skin nicely before they gave up the ghost [my skin does not like petrol at all!].
I view this task a bit like the timing belt/water pump - you have to do it at least once [successfully] to call yourself an enthusiast! If I goose the job then at least I can say I went down fighting knowing I have someone who can pick up the pieces for me.
The beauty of this list is the shared knowledge and its application. For sure I would have packed up interest in the 928 long ago were it not for the likes of Dr Bob and so many others who have contributed over the last 16 years who I consider treasured friends which is kind of strange as I would not know them from Adam in a crowd [sad to say].

Rgds
Fred
Last edited by FredR; 11-20-2015 at 04:06 PM.
#41
Rennlist Member

yep those are the clamps i had but didnt know how to clampen, or i didnt have in the kit. My point was, that i think you can buy the entire half shaft fully assembled and thats what i ended up doing after my screw hose clamps failed. i cant rememmber the price, but the kit was like $100 and the two new CV shafts were $300 .... its been 10years!

#42
Rennlist Member
Thread Starter

yep those are the clamps i had but didnt know how to clampen, or i didnt have in the kit. My point was, that i think you can buy the entire half shaft fully assembled and thats what i ended up doing after my screw hose clamps failed. i cant rememmber the price, but the kit was like $100 and the two new CV shafts were $300 .... its been 10years! 

I thought the kits were reasonably priced. Unfortunately I cannot access exchange units in the way you can because of the prohibitive shipping costs to get the core units there and the exchange units back assuming that is the "modus operandi".
Believe it or not I actually enjoyed doing this myself this afternoon and I will enjoy it even more if I get them back and it works.
Regarding those clamps I assume you push them as tight as you can by hand initially and then pinch the joint tight with carpenter's pincers [the kind of tool you pull nails with]. Maybe there is a special tool for this?
Regards
Fred
#43
Rennlist Member

Mark,
I thought the kits were reasonably priced. Unfortunately I cannot access exchange units in the way you can because of the prohibitive shipping costs to get the core units there and the exchange units back assuming that is the "modus operandi".
Believe it or not I actually enjoyed doing this myself this afternoon and I will enjoy it even more if I get them back and it works.
Regarding those clamps I assume you push them as tight as you can by hand initially and then pinch the joint tight with carpenter's pincers [the kind of tool you pull nails with]. Maybe there is a special tool for this?
Regards
Fred
I thought the kits were reasonably priced. Unfortunately I cannot access exchange units in the way you can because of the prohibitive shipping costs to get the core units there and the exchange units back assuming that is the "modus operandi".
Believe it or not I actually enjoyed doing this myself this afternoon and I will enjoy it even more if I get them back and it works.
Regarding those clamps I assume you push them as tight as you can by hand initially and then pinch the joint tight with carpenter's pincers [the kind of tool you pull nails with]. Maybe there is a special tool for this?
Regards
Fred

it was kind of like a mind bender putting the certain parts together if i recall because at first i couldnt figure out how it all went back together. with gloves and lots of paper towels, it wasnt too messy either.

#44
Chronic Tool Dropper
Lifetime Rennlist
Member
Lifetime Rennlist
Member

Fred--
There is of course a special tool, similar to your 'carpenter's pincers', but it includes a fancy little pad that keeps the middle clamped section from bending up as you squeeze it from the edges. If you decide to use the tool you have (and many have somewhat successfully), make sure it's a sacrificial tool, and plan to dull the sharp cutting edges so you don't accidentally cut off that clamped section.
In the US anyway, these tools are available for 'free-rent' at locap parts stores.
There is of course a special tool, similar to your 'carpenter's pincers', but it includes a fancy little pad that keeps the middle clamped section from bending up as you squeeze it from the edges. If you decide to use the tool you have (and many have somewhat successfully), make sure it's a sacrificial tool, and plan to dull the sharp cutting edges so you don't accidentally cut off that clamped section.
In the US anyway, these tools are available for 'free-rent' at locap parts stores.
#45
Racer
Join Date: Oct 2014
Location: Columbia, Missouri
Posts: 402
Likes: 0
Received 0 Likes
on
0 Posts

I have also noticed that my half shafts as installed [for the last 10 years] had no gaskets whatsoever and there are non in the kit I received from Roger so presume they are not needed but the manual and Dwayne's write up show two gasket locations- one of them for sure is not needed as there is a metal cover sandwiched on the end between the bearing and the tranny drive flange. I might put a very thin smear of RTV between the inboard metal cover and the bearing body but I doubt that should leak grease.
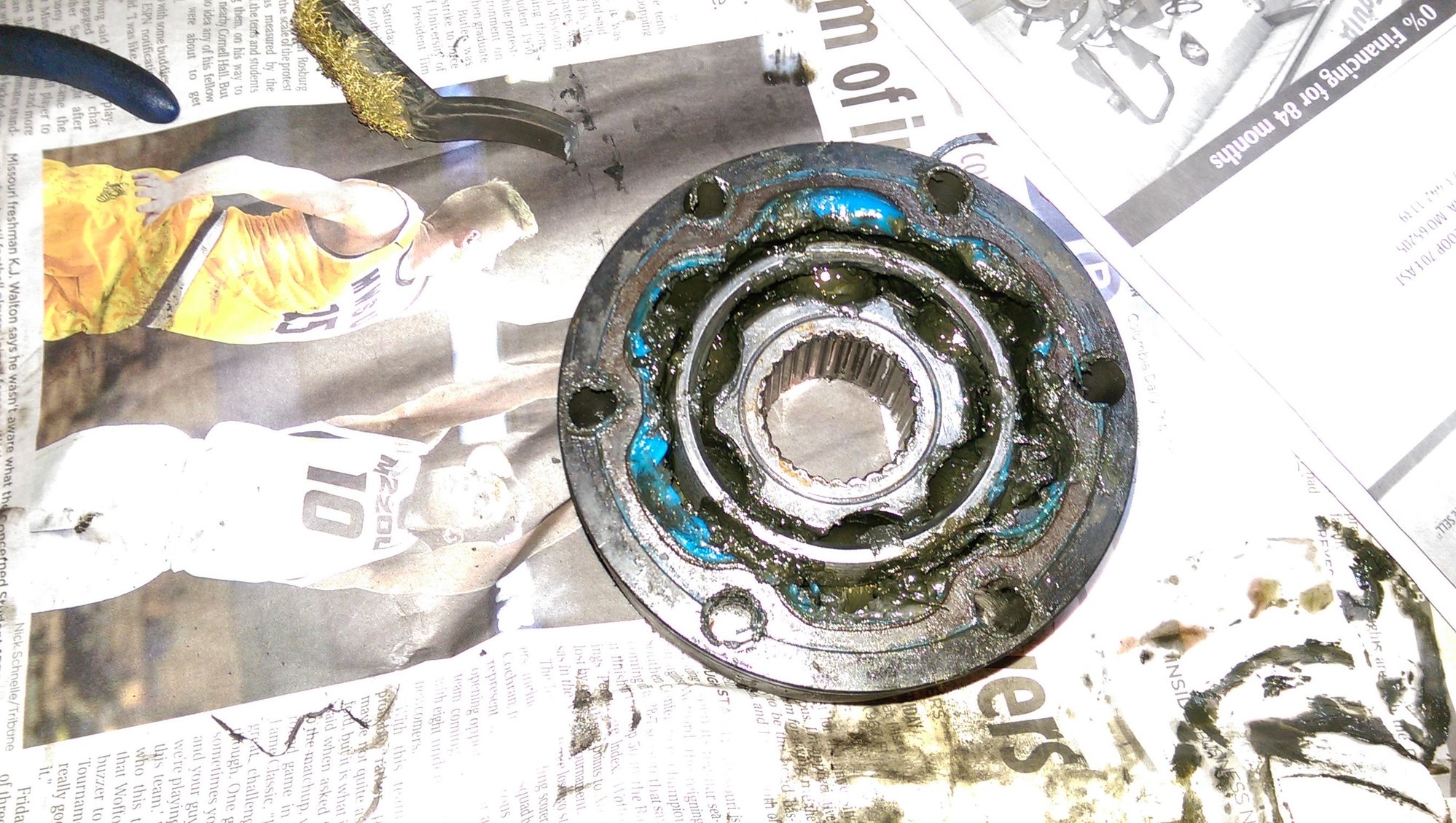
Say something about this photo
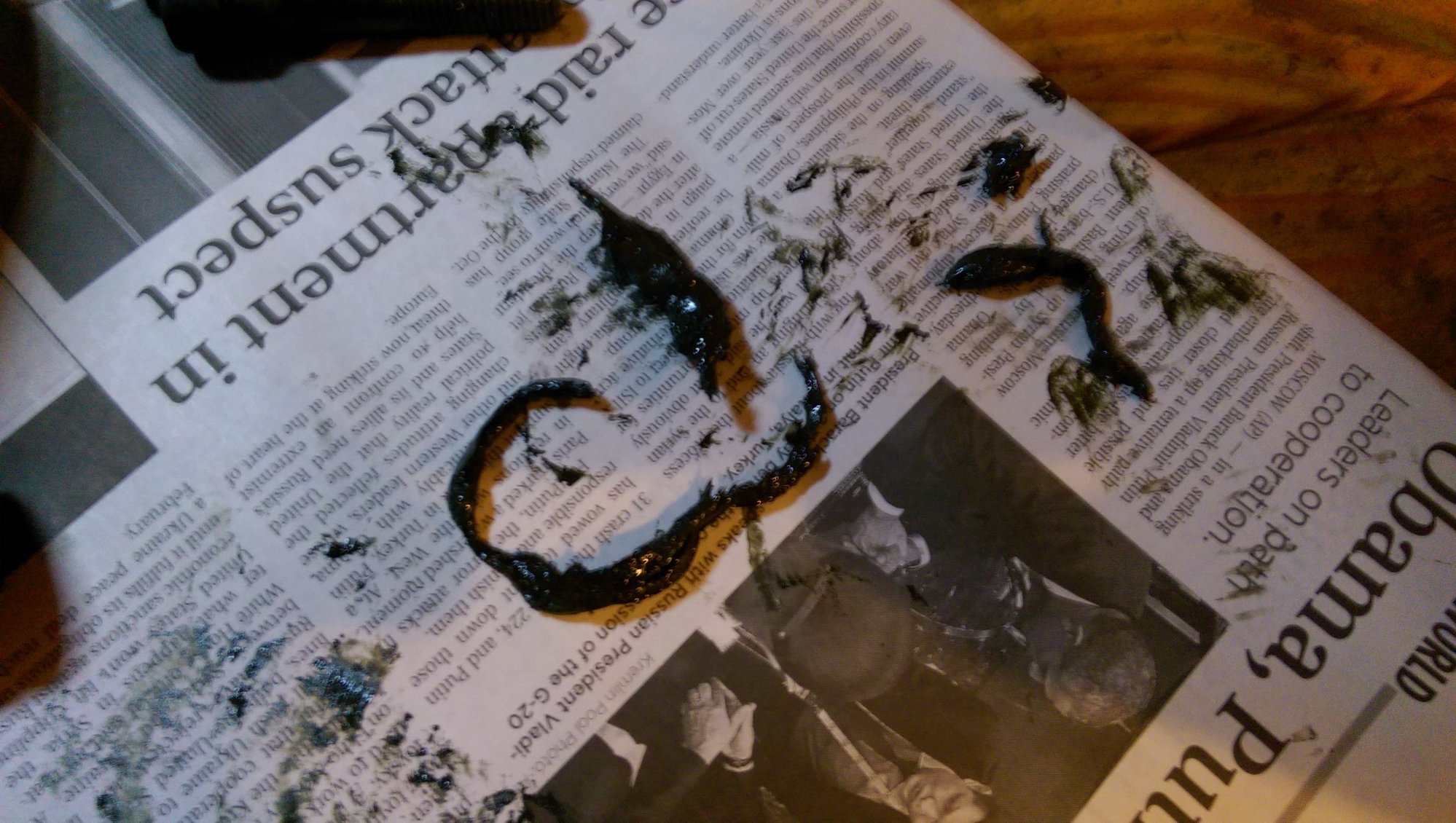
Say something about this photo