5.0L Screamer Motor goes to the dyno. (w/ graphs & video)
#196
Rennlist Member

Well considering the race videos show my car running gear for gear with GT3RSs now, I would say what ever they are putting down to the wheels , so am I. At 310rwhp, obviously, not so much, but not that far behind. Remember also that it is not just rwhp that determines acceleration over a distance and speed range, its at least, average HP over that range as well.
The power figures are correct and you can see my car against all sorts of race cars with known weights and dynoed hp values over the years in wheel to wheel competition. What I like to see are the cars that have been on the engine dyno and then end up on a dynojet. Often the difference is about 15% loss at max hp in top or near top gear. Ever notice that most S4s make about 266 to 275rwhp stock, when their flywheel ratings were around 312HP? One of the most known and controlled power values are those of the Porsche GT3 cup car. in '02, most were rated at 395rwhp and often, the strongest ones were running around 340rwhp. I dont know about you, but seeing dyno runs of a lot of cup cars, and knowing how consistant the porsche supercup engines are, that shoud be proof enough.
The power figures are correct and you can see my car against all sorts of race cars with known weights and dynoed hp values over the years in wheel to wheel competition. What I like to see are the cars that have been on the engine dyno and then end up on a dynojet. Often the difference is about 15% loss at max hp in top or near top gear. Ever notice that most S4s make about 266 to 275rwhp stock, when their flywheel ratings were around 312HP? One of the most known and controlled power values are those of the Porsche GT3 cup car. in '02, most were rated at 395rwhp and often, the strongest ones were running around 340rwhp. I dont know about you, but seeing dyno runs of a lot of cup cars, and knowing how consistant the porsche supercup engines are, that shoud be proof enough.
#197
Rennlist Member

my car was near 6 seconds from 60 to 100mph, all in 3rd gear. 315ish rwhp
Now, more like 4.8 seconds from 60 to 100mph in 3rd gear as well. 373rwhp, but average 360rwhp over the run. (big difference). 0-60 a few times in the 4.5second range now and was in the 5second range before. I dont like doing that test, as there are too many factors and lots of mechanical stress.
also keep in mind, my car was near 3000lbs with me in the car.
mk
Now, more like 4.8 seconds from 60 to 100mph in 3rd gear as well. 373rwhp, but average 360rwhp over the run. (big difference). 0-60 a few times in the 4.5second range now and was in the 5second range before. I dont like doing that test, as there are too many factors and lots of mechanical stress.
also keep in mind, my car was near 3000lbs with me in the car.
mk
By IcemanG17
Brian, that seems pretty reasonable hp number especially given your accel times. I have around 310 rwhp, btw I put in your best time, it will be interesting to compare Mark's time.
----GT3 Greg's928 Brian's 928
0-30 1.4 ___2.3_____3.0
0-40 1.9___ 3.0_____4.0
0-50 2.6 ___4.5_____5.0
0-60 3.9____5.4____6.2
0-70 4.8 ___6.9_____7.6
0-80 5.8 ___8.1_____9.2
0-90 7.7 ___9.4_____10.9
0-100 9.2 __10.9____13.6
Greg
Brian, that seems pretty reasonable hp number especially given your accel times. I have around 310 rwhp, btw I put in your best time, it will be interesting to compare Mark's time.
----GT3 Greg's928 Brian's 928
0-30 1.4 ___2.3_____3.0
0-40 1.9___ 3.0_____4.0
0-50 2.6 ___4.5_____5.0
0-60 3.9____5.4____6.2
0-70 4.8 ___6.9_____7.6
0-80 5.8 ___8.1_____9.2
0-90 7.7 ___9.4_____10.9
0-100 9.2 __10.9____13.6
Greg
#198

Here's an article on airspeed by Darin Morgan, he is quite the guru of cylinder head design, if any of you don't believe him about the airspeed, start hitting yourself on the head with a hammer. That will allow the discussion to move forward at least.
http://www.competitionplus.com/2006_...der_heads.html
Air speed is the key driver in efficiency, I eagerly await Tuomo numbers on the ports.
By Ptuomov
http://www.epi-eng.com/piston_engine..._yardstick.htm
Since you asked, the link above is to the information below.
- Brake Mean Effective Pressure -
BMEP: An important performance yardstick
We have covered the topics of Thermal Efficiency and Volumetric Efficiency as methods for estimating the potential output of a given engine configuration.
Brake Mean Effective Pressure (BMEP) is another very effective yardstick for comparing the performance of one engine to another, and for evaluating the reasonableness of performance claims or requirements.
The definition of BMEP is: the average (mean) pressure which, if imposed on the pistons uniformly from the top to the bottom of each power stroke, would produce the measured (brake) power output.
Note that BMEP is purely theoretical and has nothing to do with actual cylinder pressures. It is simply an effective comparison tool.If you work through the arithmetic, you find that BMEP is simply a multiple of the torque per cubic inch of displacement. A torque output of 1.0 lb-ft per cubic inch of displacement equals a BMEP of 150.8 psi. in a four-stroke engine and 75.4 psi. in a two-stroke engine.
(The discussion on the remainder of this page is with respect to four-stroke engines, but it applies equally to two strike engines if you simply substitute 75.4 everywhere you see 150.8)
If you know the torque and displacement of an engine, a very practical way to calculate BMEP is:
BMEP = 150.8 x TORQUE (lb-ft) / DISPLACEMENT (ci)
(Equation 8)
This tool is extremely handy to evaluate the performance which is claimed for any particular engine. For example, the 200 HP IO-360 (360 CID) and 300 HP IO-540 (540 CID) Lycomings make their rated power at 2700 RPM. At that RPM, the rated power requires 389 lb-ft and 584 lb-ft of torque respectively.
From those torque values, it is easy to see (from Equation 8 above) that both engines operate at a BMEP of about 163 PSI. (1.08 lb-ft of torque per cubic inch) at peak power. The BMEP at peak torque is slightly greater.
For a long-life, naturally-aspirated, gasoline-fueled, two-valve-per-cylinder, pushrod engine, a BMEP over 200 PSI is difficult to achieve and requires a serious development program and very specialized components.
For comparison purposes, let's look at what is commonly believed to be the very pinnacle of engine performance: Formula-1 (Grand Prix).
An F1 engine is purpose-built and essentially unrestricted. For 2006, the rules required a 90° V8 engine of 2.4 liters displacement (146.4 CID) with a maximum bore of 98mm (3.858) and a required bore spacing of 106.5 mm (4.193). The resulting stroke to achieve 2.4 liters is 39.75 mm (1.565) and is implemented with a 180° crankshaft. The typical rod length is approximately 4.016 (102 mm), for a Rod/Stroke ratio of about 2.57.
These engines are typically a 4-valve-per cylinder layout with two overhead cams per bank, and pneumatic valvesprings. In addition to the few restrictions stated above, there are the following additional restrictions: (a) no beryllium compounds, (b) no MMC pistons, (c) no variable-length intake pipes, (d) one injector per cylinder, and (e) the requirement that one engine last for two race weekends.
At the end of the 2006 season, most of these F1 engines ran up to 20,000 RPM in a race, and made in the vicinity of 750 HP. One engine for which I have the figures made 755 BHP at an astonishing 19,250 RPM. At a peak power of 755 HP, the torque is 206 lb-ft and peak-power BMEP would be 212 psi. (14.63 bar). Peak torque of 214 lb-ft occurred at 17,000 RPM for a BMEP of 220 psi (15.18 bar). There can be no argument that 212 psi at 19,250 RPM is truly amazing.
However, let's look at some astounding domestic technology. The 2006 Nextel Cup engine is a severely-restricted powerplant, being derived from production components. It uses a production-based cast-iron 90° V8 block and 90° steel crankshaft, with a maximum displacement of 358 CID (5.87 liters). A typical configuration has a 4.185" bore with a 3.25" stroke and a 6.20" conrod (R/S = 1.91).
Cylinder heads are similarly production-based, limited to two valves per cylinder, but highly developed. The valves are operated by a single, engineblock-mounted, flat-tappet camshaft (that's right, still no rollers as of 2007) and a pushrod / rocker-arm / coil-spring valvetrain. It is further hobbled by the requirement for a single four-barrel carburetor. Electronically-controlled ignition is not allowed, and there are minimum weight requirements for the conrods and pistons.
How does it perform? At the end of the 2006 season, the engines were producing in the neighborhood of 825 HP at 9000 RPM (and could produce more at 10,000 RPM, but engine RPM has been restricted by means of a rule limiting the final drive ratio at each venue). 825 HP at 9000 RPM requires 481 lb-ft of torque, for a peak-power BMEP of nearly 203 PSI (14.0 bar). Peak torque was typically about 520 lb-ft at 7500 RPM, for a peak BMEP of over 219 psi (15.1 bar).
THAT is truly astonishing. Compare the F1 engine figures to the Cup engine figures for a better grip on just how clever these Cup engine guys are.
To appreciate the value of this tool, suppose someone offers to sell you a 2.8 liter (171 cubic inch) Ford V6 which allegedly makes 230 HP at 5000 RPM, and is equipped with the standard iron heads and an aftermarket intake manifold and camshaft.
You could evaluate the reasonableness of this claim by calculating that 230 HP at 5000 RPM requires 242 lb-ft of torque (230 x 5252 ÷ 5000), and that 242 lb-ft. of torque from 171 cubic inches requires a BMEP of 213 PSI (150.8 x 242 ÷ 171).
You would then dismiss the claim as preposterous because you know that if a guy could do the magic required to make that kind of performance with the stock heads and intake design, he would be renowned as one of the pre-eminent engine gurus in the world. (You would later discover that the engine rating of "230" is actually "Blantonpower", not Horsepower.)
As a matter of fact, in order to get a BMEP value of 214 from our aircraft V8, we had to use extremely well developed, high-flowing, high velocity heads, a specially-developed tuned intake and fuel injection system, very well developed roller-cam profiles and valve train components, and a host of very specialized components which we designed and manufactured.
End of Article
The correct (Or maximum potential) airspeeds for various ports will be different, straighter ports will have the potential to flow faster and will smaller than a equivalent flowing more contorted port. Every time you turn the air you will loose something. In saying that the S4 manifold is very contorted and that never helps. If I didn't mention it before if the ports and runners are too big the helmholtz effect will be diminished. Clearly the S4 manifold works however that doesn't mean it can't be better.
Greg

http://www.competitionplus.com/2006_...der_heads.html
Air speed is the key driver in efficiency, I eagerly await Tuomo numbers on the ports.
By Ptuomov
What are these BMEP numbers used for / what should they be used for?
Since you asked, the link above is to the information below.
- Brake Mean Effective Pressure -
BMEP: An important performance yardstick
We have covered the topics of Thermal Efficiency and Volumetric Efficiency as methods for estimating the potential output of a given engine configuration.
Brake Mean Effective Pressure (BMEP) is another very effective yardstick for comparing the performance of one engine to another, and for evaluating the reasonableness of performance claims or requirements.
The definition of BMEP is: the average (mean) pressure which, if imposed on the pistons uniformly from the top to the bottom of each power stroke, would produce the measured (brake) power output.
Note that BMEP is purely theoretical and has nothing to do with actual cylinder pressures. It is simply an effective comparison tool.If you work through the arithmetic, you find that BMEP is simply a multiple of the torque per cubic inch of displacement. A torque output of 1.0 lb-ft per cubic inch of displacement equals a BMEP of 150.8 psi. in a four-stroke engine and 75.4 psi. in a two-stroke engine.
(The discussion on the remainder of this page is with respect to four-stroke engines, but it applies equally to two strike engines if you simply substitute 75.4 everywhere you see 150.8)
If you know the torque and displacement of an engine, a very practical way to calculate BMEP is:
BMEP = 150.8 x TORQUE (lb-ft) / DISPLACEMENT (ci)
(Equation 8)
This tool is extremely handy to evaluate the performance which is claimed for any particular engine. For example, the 200 HP IO-360 (360 CID) and 300 HP IO-540 (540 CID) Lycomings make their rated power at 2700 RPM. At that RPM, the rated power requires 389 lb-ft and 584 lb-ft of torque respectively.
From those torque values, it is easy to see (from Equation 8 above) that both engines operate at a BMEP of about 163 PSI. (1.08 lb-ft of torque per cubic inch) at peak power. The BMEP at peak torque is slightly greater.
For a long-life, naturally-aspirated, gasoline-fueled, two-valve-per-cylinder, pushrod engine, a BMEP over 200 PSI is difficult to achieve and requires a serious development program and very specialized components.
For comparison purposes, let's look at what is commonly believed to be the very pinnacle of engine performance: Formula-1 (Grand Prix).
An F1 engine is purpose-built and essentially unrestricted. For 2006, the rules required a 90° V8 engine of 2.4 liters displacement (146.4 CID) with a maximum bore of 98mm (3.858) and a required bore spacing of 106.5 mm (4.193). The resulting stroke to achieve 2.4 liters is 39.75 mm (1.565) and is implemented with a 180° crankshaft. The typical rod length is approximately 4.016 (102 mm), for a Rod/Stroke ratio of about 2.57.
These engines are typically a 4-valve-per cylinder layout with two overhead cams per bank, and pneumatic valvesprings. In addition to the few restrictions stated above, there are the following additional restrictions: (a) no beryllium compounds, (b) no MMC pistons, (c) no variable-length intake pipes, (d) one injector per cylinder, and (e) the requirement that one engine last for two race weekends.
At the end of the 2006 season, most of these F1 engines ran up to 20,000 RPM in a race, and made in the vicinity of 750 HP. One engine for which I have the figures made 755 BHP at an astonishing 19,250 RPM. At a peak power of 755 HP, the torque is 206 lb-ft and peak-power BMEP would be 212 psi. (14.63 bar). Peak torque of 214 lb-ft occurred at 17,000 RPM for a BMEP of 220 psi (15.18 bar). There can be no argument that 212 psi at 19,250 RPM is truly amazing.
However, let's look at some astounding domestic technology. The 2006 Nextel Cup engine is a severely-restricted powerplant, being derived from production components. It uses a production-based cast-iron 90° V8 block and 90° steel crankshaft, with a maximum displacement of 358 CID (5.87 liters). A typical configuration has a 4.185" bore with a 3.25" stroke and a 6.20" conrod (R/S = 1.91).
Cylinder heads are similarly production-based, limited to two valves per cylinder, but highly developed. The valves are operated by a single, engineblock-mounted, flat-tappet camshaft (that's right, still no rollers as of 2007) and a pushrod / rocker-arm / coil-spring valvetrain. It is further hobbled by the requirement for a single four-barrel carburetor. Electronically-controlled ignition is not allowed, and there are minimum weight requirements for the conrods and pistons.
How does it perform? At the end of the 2006 season, the engines were producing in the neighborhood of 825 HP at 9000 RPM (and could produce more at 10,000 RPM, but engine RPM has been restricted by means of a rule limiting the final drive ratio at each venue). 825 HP at 9000 RPM requires 481 lb-ft of torque, for a peak-power BMEP of nearly 203 PSI (14.0 bar). Peak torque was typically about 520 lb-ft at 7500 RPM, for a peak BMEP of over 219 psi (15.1 bar).
THAT is truly astonishing. Compare the F1 engine figures to the Cup engine figures for a better grip on just how clever these Cup engine guys are.
To appreciate the value of this tool, suppose someone offers to sell you a 2.8 liter (171 cubic inch) Ford V6 which allegedly makes 230 HP at 5000 RPM, and is equipped with the standard iron heads and an aftermarket intake manifold and camshaft.
You could evaluate the reasonableness of this claim by calculating that 230 HP at 5000 RPM requires 242 lb-ft of torque (230 x 5252 ÷ 5000), and that 242 lb-ft. of torque from 171 cubic inches requires a BMEP of 213 PSI (150.8 x 242 ÷ 171).
You would then dismiss the claim as preposterous because you know that if a guy could do the magic required to make that kind of performance with the stock heads and intake design, he would be renowned as one of the pre-eminent engine gurus in the world. (You would later discover that the engine rating of "230" is actually "Blantonpower", not Horsepower.)
As a matter of fact, in order to get a BMEP value of 214 from our aircraft V8, we had to use extremely well developed, high-flowing, high velocity heads, a specially-developed tuned intake and fuel injection system, very well developed roller-cam profiles and valve train components, and a host of very specialized components which we designed and manufactured.
End of Article
The correct (Or maximum potential) airspeeds for various ports will be different, straighter ports will have the potential to flow faster and will smaller than a equivalent flowing more contorted port. Every time you turn the air you will loose something. In saying that the S4 manifold is very contorted and that never helps. If I didn't mention it before if the ports and runners are too big the helmholtz effect will be diminished. Clearly the S4 manifold works however that doesn't mean it can't be better.
Greg
#199
Nordschleife Master

Tuomo and others that are interested, as to the explanation that the tuning (adjusting air fuel) is the reason for the high BMEP, well that can not be the case. To achieve with a 5 litre engine at 6,000 rpms with power in the range of 440 to 450 hp that requires approx 120% volumetric efficiency. Volumetric efficiency has nothing to do with the air fuel ratio. It is assumed that the engine is tuned properly when you talk efficiency numbers let alone ones that are over 100% efficiency. Greg
Volumetric efficiency is how much air you get in the engine. It doesn't say anything about the completeness of the burn, for example. It's possible to have a very high volumetric efficiency but mediocre BMEP with carburated engine with an intake manifold that has poor wet flow characteristics.
It is true that if the volumetric efficiency is low and the fuel type is given, tuning can only go so far. There's a limit when every fuel molecule and every oxygen molecule combine and no oxygen is left behind unburned and no fuel molecules are taking away the power by cooling. But the factory tune or any generic tune is going to be very far from that ideal.
(It's like a college party, it gets really good when there's the same number of boys and girls and the tune is such that everyone hooks up. Beyond that, tune can't help. Where the analogy breaks down is that that party would turn into a total orgy with much more interesting combinations, but it's just an analogy.)
The spark timing is another issue. A car from the factory, even with knock sensors, basically doesn't knock when run with good fuel. There's a lot of hp, torque, and BMEP left on the table. If one then tunes the engine to it's individual limit, one is going to get more power.
The bottom line is that going from the factory tune to a tune specific for an individual engine is always going to give you a BMEP bump. By your estimates, this engine beats the production engine but not individually tuned race engine. That's not shocking to me.
#200
Rennlist Member

interesting article. I didnt have a chance to read the links, as Im really responding in general terms, using comparisons with what ive seen on the track.
As far as teh BMEP, it is interesting that the BMW I quoted is right around 183 (which is good right) and incorporates a very old engine, some head work, raised compression and modified air intake air box. My 928s, both the stock engine with 85 cams making 320 to 335rwhp, has only a BMEP of 125, and when the engine was stroked and bored to 6.4 liters (390ci), it stays at a BMEP of 125.
If what you are saying is true, as far as velocities, you would think the BMEP to go up, because we would have much greater intake speeds with the larger displacement for a given RPM, correct? But, as you elluded to, there are other factors, such as pressure drops across the intake path which reduce flow efficiency. remember my test with the intake spacers? the Hemhotz effect was certainly changed for the worse. our intakes are probably the most restrictive factor of our engines performance, as proved by anderson and fan (as well as Ott) with HUGE gains with just intake manifold changes. However, some pretty big performace was seen by the Devek motors with stock intakes making 440rwhp.
I think what Tuomo was getting at later, is that there is VE and there is combustion efficiency. certainly large ports and slower velocities can get mass flow into the cylinders, but what does the atomization look like? The more complicated momentum/inertia aspects of the flow is another. It is much more complicated, and there are also trade offs.Just ask bernoulli about that.
I dont have a clear understanding of the factors that allow for over 100% volumetric efficiencies, but I understand what you are getting at. You think some of the dyno results are optimistic, but in most cases they are pretty real.
How do you fool a known drum mass and size, into giving more hp than it shows when driven by the tires of one of our cars?
EDIT: by the way, I just noticed that my numbers above are for rear wheel hp and torque. Just think of what that little e30 BMW engine's BMEP would be with flwheel numbers! Yes, 200 BMEP!! Now, do you not believe that those little 2.5 liter engines can make 240 to 260rwhp (i.e. 300flywheel)? Thats '86 technology as well with some tender loving care
(
As far as teh BMEP, it is interesting that the BMW I quoted is right around 183 (which is good right) and incorporates a very old engine, some head work, raised compression and modified air intake air box. My 928s, both the stock engine with 85 cams making 320 to 335rwhp, has only a BMEP of 125, and when the engine was stroked and bored to 6.4 liters (390ci), it stays at a BMEP of 125.


I think what Tuomo was getting at later, is that there is VE and there is combustion efficiency. certainly large ports and slower velocities can get mass flow into the cylinders, but what does the atomization look like? The more complicated momentum/inertia aspects of the flow is another. It is much more complicated, and there are also trade offs.Just ask bernoulli about that.

I dont have a clear understanding of the factors that allow for over 100% volumetric efficiencies, but I understand what you are getting at. You think some of the dyno results are optimistic, but in most cases they are pretty real.
How do you fool a known drum mass and size, into giving more hp than it shows when driven by the tires of one of our cars?
EDIT: by the way, I just noticed that my numbers above are for rear wheel hp and torque. Just think of what that little e30 BMW engine's BMEP would be with flwheel numbers! Yes, 200 BMEP!! Now, do you not believe that those little 2.5 liter engines can make 240 to 260rwhp (i.e. 300flywheel)? Thats '86 technology as well with some tender loving care

(
Here's an article on airspeed by Darin Morgan, he is quite the guru of cylinder head design, if any of you don't believe him about the airspeed, start hitting yourself on the head with a hammer. That will allow the discussion to move forward at least.
http://www.competitionplus.com/2006_...der_heads.html
Air speed is the key driver in efficiency, I eagerly await Tuomo numbers on the ports.
By Ptuomov
http://www.epi-eng.com/piston_engine..._yardstick.htm
Since you asked, the link above is to the information below.
- Brake Mean Effective Pressure -
BMEP: An important performance yardstick
We have covered the topics of Thermal Efficiency and Volumetric Efficiency as methods for estimating the potential output of a given engine configuration.
Brake Mean Effective Pressure (BMEP) is another very effective yardstick for comparing the performance of one engine to another, and for evaluating the reasonableness of performance claims or requirements.
The definition of BMEP is: the average (mean) pressure which, if imposed on the pistons uniformly from the top to the bottom of each power stroke, would produce the measured (brake) power output.
Note that BMEP is purely theoretical and has nothing to do with actual cylinder pressures. It is simply an effective comparison tool.If you work through the arithmetic, you find that BMEP is simply a multiple of the torque per cubic inch of displacement. A torque output of 1.0 lb-ft per cubic inch of displacement equals a BMEP of 150.8 psi. in a four-stroke engine and 75.4 psi. in a two-stroke engine.
(The discussion on the remainder of this page is with respect to four-stroke engines, but it applies equally to two strike engines if you simply substitute 75.4 everywhere you see 150.8)
If you know the torque and displacement of an engine, a very practical way to calculate BMEP is:
BMEP = 150.8 x TORQUE (lb-ft) / DISPLACEMENT (ci)
(Equation 8)
This tool is extremely handy to evaluate the performance which is claimed for any particular engine. For example, the 200 HP IO-360 (360 CID) and 300 HP IO-540 (540 CID) Lycomings make their rated power at 2700 RPM. At that RPM, the rated power requires 389 lb-ft and 584 lb-ft of torque respectively.
From those torque values, it is easy to see (from Equation 8 above) that both engines operate at a BMEP of about 163 PSI. (1.08 lb-ft of torque per cubic inch) at peak power. The BMEP at peak torque is slightly greater.
For a long-life, naturally-aspirated, gasoline-fueled, two-valve-per-cylinder, pushrod engine, a BMEP over 200 PSI is difficult to achieve and requires a serious development program and very specialized components.
For comparison purposes, let's look at what is commonly believed to be the very pinnacle of engine performance: Formula-1 (Grand Prix).
An F1 engine is purpose-built and essentially unrestricted. For 2006, the rules required a 90° V8 engine of 2.4 liters displacement (146.4 CID) with a maximum bore of 98mm (3.858) and a required bore spacing of 106.5 mm (4.193). The resulting stroke to achieve 2.4 liters is 39.75 mm (1.565) and is implemented with a 180° crankshaft. The typical rod length is approximately 4.016 (102 mm), for a Rod/Stroke ratio of about 2.57.
These engines are typically a 4-valve-per cylinder layout with two overhead cams per bank, and pneumatic valvesprings. In addition to the few restrictions stated above, there are the following additional restrictions: (a) no beryllium compounds, (b) no MMC pistons, (c) no variable-length intake pipes, (d) one injector per cylinder, and (e) the requirement that one engine last for two race weekends.
At the end of the 2006 season, most of these F1 engines ran up to 20,000 RPM in a race, and made in the vicinity of 750 HP. One engine for which I have the figures made 755 BHP at an astonishing 19,250 RPM. At a peak power of 755 HP, the torque is 206 lb-ft and peak-power BMEP would be 212 psi. (14.63 bar). Peak torque of 214 lb-ft occurred at 17,000 RPM for a BMEP of 220 psi (15.18 bar). There can be no argument that 212 psi at 19,250 RPM is truly amazing.
However, let's look at some astounding domestic technology. The 2006 Nextel Cup engine is a severely-restricted powerplant, being derived from production components. It uses a production-based cast-iron 90° V8 block and 90° steel crankshaft, with a maximum displacement of 358 CID (5.87 liters). A typical configuration has a 4.185" bore with a 3.25" stroke and a 6.20" conrod (R/S = 1.91).
Cylinder heads are similarly production-based, limited to two valves per cylinder, but highly developed. The valves are operated by a single, engineblock-mounted, flat-tappet camshaft (that's right, still no rollers as of 2007) and a pushrod / rocker-arm / coil-spring valvetrain. It is further hobbled by the requirement for a single four-barrel carburetor. Electronically-controlled ignition is not allowed, and there are minimum weight requirements for the conrods and pistons.
How does it perform? At the end of the 2006 season, the engines were producing in the neighborhood of 825 HP at 9000 RPM (and could produce more at 10,000 RPM, but engine RPM has been restricted by means of a rule limiting the final drive ratio at each venue). 825 HP at 9000 RPM requires 481 lb-ft of torque, for a peak-power BMEP of nearly 203 PSI (14.0 bar). Peak torque was typically about 520 lb-ft at 7500 RPM, for a peak BMEP of over 219 psi (15.1 bar).
THAT is truly astonishing. Compare the F1 engine figures to the Cup engine figures for a better grip on just how clever these Cup engine guys are.
To appreciate the value of this tool, suppose someone offers to sell you a 2.8 liter (171 cubic inch) Ford V6 which allegedly makes 230 HP at 5000 RPM, and is equipped with the standard iron heads and an aftermarket intake manifold and camshaft.
You could evaluate the reasonableness of this claim by calculating that 230 HP at 5000 RPM requires 242 lb-ft of torque (230 x 5252 ÷ 5000), and that 242 lb-ft. of torque from 171 cubic inches requires a BMEP of 213 PSI (150.8 x 242 ÷ 171).
You would then dismiss the claim as preposterous because you know that if a guy could do the magic required to make that kind of performance with the stock heads and intake design, he would be renowned as one of the pre-eminent engine gurus in the world. (You would later discover that the engine rating of "230" is actually "Blantonpower", not Horsepower.)
As a matter of fact, in order to get a BMEP value of 214 from our aircraft V8, we had to use extremely well developed, high-flowing, high velocity heads, a specially-developed tuned intake and fuel injection system, very well developed roller-cam profiles and valve train components, and a host of very specialized components which we designed and manufactured.
End of Article
The correct (Or maximum potential) airspeeds for various ports will be different, straighter ports will have the potential to flow faster and will smaller than a equivalent flowing more contorted port. Every time you turn the air you will loose something. In saying that the S4 manifold is very contorted and that never helps. If I didn't mention it before if the ports and runners are too big the helmholtz effect will be diminished. Clearly the S4 manifold works however that doesn't mean it can't be better.
Greg

http://www.competitionplus.com/2006_...der_heads.html
Air speed is the key driver in efficiency, I eagerly await Tuomo numbers on the ports.
By Ptuomov
http://www.epi-eng.com/piston_engine..._yardstick.htm
Since you asked, the link above is to the information below.
- Brake Mean Effective Pressure -
BMEP: An important performance yardstick
We have covered the topics of Thermal Efficiency and Volumetric Efficiency as methods for estimating the potential output of a given engine configuration.
Brake Mean Effective Pressure (BMEP) is another very effective yardstick for comparing the performance of one engine to another, and for evaluating the reasonableness of performance claims or requirements.
The definition of BMEP is: the average (mean) pressure which, if imposed on the pistons uniformly from the top to the bottom of each power stroke, would produce the measured (brake) power output.
Note that BMEP is purely theoretical and has nothing to do with actual cylinder pressures. It is simply an effective comparison tool.If you work through the arithmetic, you find that BMEP is simply a multiple of the torque per cubic inch of displacement. A torque output of 1.0 lb-ft per cubic inch of displacement equals a BMEP of 150.8 psi. in a four-stroke engine and 75.4 psi. in a two-stroke engine.
(The discussion on the remainder of this page is with respect to four-stroke engines, but it applies equally to two strike engines if you simply substitute 75.4 everywhere you see 150.8)
If you know the torque and displacement of an engine, a very practical way to calculate BMEP is:
BMEP = 150.8 x TORQUE (lb-ft) / DISPLACEMENT (ci)
(Equation 8)
This tool is extremely handy to evaluate the performance which is claimed for any particular engine. For example, the 200 HP IO-360 (360 CID) and 300 HP IO-540 (540 CID) Lycomings make their rated power at 2700 RPM. At that RPM, the rated power requires 389 lb-ft and 584 lb-ft of torque respectively.
From those torque values, it is easy to see (from Equation 8 above) that both engines operate at a BMEP of about 163 PSI. (1.08 lb-ft of torque per cubic inch) at peak power. The BMEP at peak torque is slightly greater.
For a long-life, naturally-aspirated, gasoline-fueled, two-valve-per-cylinder, pushrod engine, a BMEP over 200 PSI is difficult to achieve and requires a serious development program and very specialized components.
For comparison purposes, let's look at what is commonly believed to be the very pinnacle of engine performance: Formula-1 (Grand Prix).
An F1 engine is purpose-built and essentially unrestricted. For 2006, the rules required a 90° V8 engine of 2.4 liters displacement (146.4 CID) with a maximum bore of 98mm (3.858) and a required bore spacing of 106.5 mm (4.193). The resulting stroke to achieve 2.4 liters is 39.75 mm (1.565) and is implemented with a 180° crankshaft. The typical rod length is approximately 4.016 (102 mm), for a Rod/Stroke ratio of about 2.57.
These engines are typically a 4-valve-per cylinder layout with two overhead cams per bank, and pneumatic valvesprings. In addition to the few restrictions stated above, there are the following additional restrictions: (a) no beryllium compounds, (b) no MMC pistons, (c) no variable-length intake pipes, (d) one injector per cylinder, and (e) the requirement that one engine last for two race weekends.
At the end of the 2006 season, most of these F1 engines ran up to 20,000 RPM in a race, and made in the vicinity of 750 HP. One engine for which I have the figures made 755 BHP at an astonishing 19,250 RPM. At a peak power of 755 HP, the torque is 206 lb-ft and peak-power BMEP would be 212 psi. (14.63 bar). Peak torque of 214 lb-ft occurred at 17,000 RPM for a BMEP of 220 psi (15.18 bar). There can be no argument that 212 psi at 19,250 RPM is truly amazing.
However, let's look at some astounding domestic technology. The 2006 Nextel Cup engine is a severely-restricted powerplant, being derived from production components. It uses a production-based cast-iron 90° V8 block and 90° steel crankshaft, with a maximum displacement of 358 CID (5.87 liters). A typical configuration has a 4.185" bore with a 3.25" stroke and a 6.20" conrod (R/S = 1.91).
Cylinder heads are similarly production-based, limited to two valves per cylinder, but highly developed. The valves are operated by a single, engineblock-mounted, flat-tappet camshaft (that's right, still no rollers as of 2007) and a pushrod / rocker-arm / coil-spring valvetrain. It is further hobbled by the requirement for a single four-barrel carburetor. Electronically-controlled ignition is not allowed, and there are minimum weight requirements for the conrods and pistons.
How does it perform? At the end of the 2006 season, the engines were producing in the neighborhood of 825 HP at 9000 RPM (and could produce more at 10,000 RPM, but engine RPM has been restricted by means of a rule limiting the final drive ratio at each venue). 825 HP at 9000 RPM requires 481 lb-ft of torque, for a peak-power BMEP of nearly 203 PSI (14.0 bar). Peak torque was typically about 520 lb-ft at 7500 RPM, for a peak BMEP of over 219 psi (15.1 bar).
THAT is truly astonishing. Compare the F1 engine figures to the Cup engine figures for a better grip on just how clever these Cup engine guys are.
To appreciate the value of this tool, suppose someone offers to sell you a 2.8 liter (171 cubic inch) Ford V6 which allegedly makes 230 HP at 5000 RPM, and is equipped with the standard iron heads and an aftermarket intake manifold and camshaft.
You could evaluate the reasonableness of this claim by calculating that 230 HP at 5000 RPM requires 242 lb-ft of torque (230 x 5252 ÷ 5000), and that 242 lb-ft. of torque from 171 cubic inches requires a BMEP of 213 PSI (150.8 x 242 ÷ 171).
You would then dismiss the claim as preposterous because you know that if a guy could do the magic required to make that kind of performance with the stock heads and intake design, he would be renowned as one of the pre-eminent engine gurus in the world. (You would later discover that the engine rating of "230" is actually "Blantonpower", not Horsepower.)
As a matter of fact, in order to get a BMEP value of 214 from our aircraft V8, we had to use extremely well developed, high-flowing, high velocity heads, a specially-developed tuned intake and fuel injection system, very well developed roller-cam profiles and valve train components, and a host of very specialized components which we designed and manufactured.
End of Article
The correct (Or maximum potential) airspeeds for various ports will be different, straighter ports will have the potential to flow faster and will smaller than a equivalent flowing more contorted port. Every time you turn the air you will loose something. In saying that the S4 manifold is very contorted and that never helps. If I didn't mention it before if the ports and runners are too big the helmholtz effect will be diminished. Clearly the S4 manifold works however that doesn't mean it can't be better.
Greg
Last edited by mark kibort; 10-04-2009 at 01:19 PM.
#201
Rennlist Member

Is this really the situation?
Just a quick calculation of my car at 320rwhp. that would be near 375flywheel hp and the BMEP is still in the modest 150 range.
But, when we look at Dennis' engine at 375rwhp or near 440, it gets more in the 180 BMEP range.
so, is the point you make have really to do with the doubt that his motor cant make that kind of torque at 6000rpm with only a cam modification?
I also would mention that the efficiency of the drivetrain would change as the power went up, due to some of the factors not changing due to the increased power. (i.e. the rolling friction factor vs gear efficiency). in otherwords, 20hp of losses due to rolling friction would not change, but the power loss due to the fact that the power is transfered through gear ratios would and might be half those values. So,in the end, maybe we start out at 15 % efficiency and end up with 10% efficiency losses. that also brings up a good point regarding the larger hp cars and their efficiencies. Since all of us would have similar losses in the rolling friction area, the total rear wheel to flywheel ratio might change as the cars we look at have more and more power. just a thought.
Just a quick calculation of my car at 320rwhp. that would be near 375flywheel hp and the BMEP is still in the modest 150 range.
But, when we look at Dennis' engine at 375rwhp or near 440, it gets more in the 180 BMEP range.
so, is the point you make have really to do with the doubt that his motor cant make that kind of torque at 6000rpm with only a cam modification?
I also would mention that the efficiency of the drivetrain would change as the power went up, due to some of the factors not changing due to the increased power. (i.e. the rolling friction factor vs gear efficiency). in otherwords, 20hp of losses due to rolling friction would not change, but the power loss due to the fact that the power is transfered through gear ratios would and might be half those values. So,in the end, maybe we start out at 15 % efficiency and end up with 10% efficiency losses. that also brings up a good point regarding the larger hp cars and their efficiencies. Since all of us would have similar losses in the rolling friction area, the total rear wheel to flywheel ratio might change as the cars we look at have more and more power. just a thought.
Tuomo and others that are interested, as to the explanation that the tuning (adjusting air fuel) is the reason for the high BMEP, well that can not be the case. To achieve with a 5 litre engine at 6,000 rpms with power in the range of 440 to 450 hp that requires approx 120% volumetric efficiency. Volumetric efficiency has nothing to do with the air fuel ratio. It is assumed that the engine is tuned properly when you talk efficiency numbers let alone ones that are over 100% efficiency.
Greg
Greg
#203
Addict
Rennlist Member
Rennlist Member
Thread Starter

Skepticism is good. If I had read an internet post such as my initial post a couple years ago, I wouldn't have believed it either. I've been extremely open about what we've done to this motor, far more open than most. I've also tried to be as responsible as possible with the results.
There seem to be a lot of assumptions about flywheel HP (& in turn BMEP) & BSFC (& in turn volumetric efficiency) that I haven't & wouldn't make. I have been careful not to claim a flywheel hp number. Unless the engine is put on an engine dyno, I would not feel comfortable stating a number.
Currently, we're maxxed out on duty cycle on 24lb injectors w/ a 13:1 AFR so that's a sign something good is happening. I've run the car side by side w/ Bill's supercharged S4 & Jim's stock GTS and I've played w/ Kibort's stroker at the track and the results seem to confirm where we are.
I think there are two big stories - the torque curve (1st graph) and the gain via tuning (2nd graph). The engine makes the same torque (or BMEP if you like) at 5000 rpm as 4000 rpm. To me, that's the real breakthrough. This is the first 5.0L 928 motor I've ever seen that does that. In the second graph, we gained 50 lb-ft of torque in some places all via tuning. It shows how valuable Sharktuner + a great tuner like Jim can be.
As a final note, none of the information I've posted has come cheaply. The amount of hours that Jim & Bill have donated to this project is ungodly. Jim has traded equipment & labor for dyno time. John Holleran certainly hasn't made money given the amount of time he's spent w/ us on his dyno. If people want further confirmation or to parse out the result of each modification, please consider making a large cash donation for the dyno time and our time.
The information I've posted is free. It's worth what you've paid. Believe it, don't believe it - it's up to you. We've done the best we can. And as Bill said, we're having a whole lot of fun!
There seem to be a lot of assumptions about flywheel HP (& in turn BMEP) & BSFC (& in turn volumetric efficiency) that I haven't & wouldn't make. I have been careful not to claim a flywheel hp number. Unless the engine is put on an engine dyno, I would not feel comfortable stating a number.
Currently, we're maxxed out on duty cycle on 24lb injectors w/ a 13:1 AFR so that's a sign something good is happening. I've run the car side by side w/ Bill's supercharged S4 & Jim's stock GTS and I've played w/ Kibort's stroker at the track and the results seem to confirm where we are.
I think there are two big stories - the torque curve (1st graph) and the gain via tuning (2nd graph). The engine makes the same torque (or BMEP if you like) at 5000 rpm as 4000 rpm. To me, that's the real breakthrough. This is the first 5.0L 928 motor I've ever seen that does that. In the second graph, we gained 50 lb-ft of torque in some places all via tuning. It shows how valuable Sharktuner + a great tuner like Jim can be.
As a final note, none of the information I've posted has come cheaply. The amount of hours that Jim & Bill have donated to this project is ungodly. Jim has traded equipment & labor for dyno time. John Holleran certainly hasn't made money given the amount of time he's spent w/ us on his dyno. If people want further confirmation or to parse out the result of each modification, please consider making a large cash donation for the dyno time and our time.

Last edited by Dennis K; 10-04-2009 at 05:56 PM.
#204
Rennlist Member

The work you all did (and time spent) is immeasurable. The research and preparation, the uber-fine dyno sharktuning... the nuance modifications and the combinations thereof all add up to something extraordinary.
That may be why it's so hard for some to believe.
Believe it or not? I believe it. In the Jack Palance way, not Dean Cain.
PS. I agree with Ryan... one of the tops threads on RL. I've read it more than twice. Including the engine build thread.
That may be why it's so hard for some to believe.
Believe it or not? I believe it. In the Jack Palance way, not Dean Cain.

PS. I agree with Ryan... one of the tops threads on RL. I've read it more than twice. Including the engine build thread.
#205

By Mark Kibort
For the calc with Denis's engine I used 450 hp as that is what was quoted by a responder to the thread and I used 6,000 rpm as the dyno graph seems to peak there. If you use 440 hp the number is still in the 190 range and more than the current GT3.
The number was almost 200 psi and you can now tell that is extremely high. So much higher than the standard engine with 140 psi and anything with 200 psi is very efficient, as the article says huge work with a roller cam required for 214 psi, much more than a cam change and tuning. Roller cams generally have quicker valve action which is a very powerful tool in building cylinder pressure, i.e torque.
Tuomo and others tuning will change the BMEP figures but volumetric efficiency in the calculators is presumed with properly running engines. No where in a calculator will it say, give engine a tune up and gain 10%. Then the levels that are being discussed are such lofty levels. Especially for one that doesn't have special manifolds. Please read up on Engine Masters and then you can see what they do to get to these levels at that rpm band.
Now as I said before Pipemax gives around 200 feet per second airspeed for this engine at 6,000 rpm , i.e very slow, now Mark your airspeed will be higher but as soon as any part of your intake system chokes then it is game over. Once an intake has a sonic choke it is limited to that amount of flow. The engine is still a system, it will make sure you don't forget that.
As I mentioned before 270 feet per second (minimum) was told to me by a trusted source as the figure needed to achieve 105% volumetric efficiency, so 200 FPS is no where near it, Tuomo got a higher figure but I don't know how he got it. The reason I am chucking the stroker into it is that if Tuomo figures are correct the stroker airspeeds will be extremely high, now they may be able to run them depending on how high they are as they generally have throttle bodies but every engine has a limit before the friction losses of pumping the air overwhelm the gains from burning more air and fuel. I await those figures with interest.
Some F1 engines have achieved up to 145% and it might be of further interest that the port of an F1 engine is no bigger than your 4 valve 928 ports and in another thread with Tuomo I posted how similar they were showing a pic of one. Current spec V8 F1 engines are in the high 700s maybe some have hit 800 hp and that is with same port size, so what does that say to you? Well for one, the air must travel twice as fast as what it does in the 928 port when the 928 engine is producing around 400 hp.
So my velocity figure was calculated of a port size of 2.42 sq" and as Darin's article says average velocity is very important and he also names the calculator I use to calculate it, it is in fact very simple to use. The domestic V8 guys aim generally for 310 FPS in properly running engines, as you see it is quite a long way from 200 FPS. The calculator I have calculates average velocity and at 28"
As to Mark's Ks engine, it is probably running somewhat like an air restricted engine, they normally like little overlap on the cams but with plenty of lift, heaps of compression and not too many revs.
The stuff I didn't respond to, maybe later, I have addressed the main issues I believe. Hope it helps.
Greg
Is this really the situation?
Just a quick calculation of my car at 320rwhp. that would be near 375flywheel hp and the BMEP is still in the modest 150 range.
But, when we look at Dennis' engine at 375rwhp or near 440, it gets more in the 180 BMEP range.
so, is the point you make have really to do with the doubt that his motor cant make that kind of torque at 6000rpm with only a cam modification?
Just a quick calculation of my car at 320rwhp. that would be near 375flywheel hp and the BMEP is still in the modest 150 range.
But, when we look at Dennis' engine at 375rwhp or near 440, it gets more in the 180 BMEP range.
so, is the point you make have really to do with the doubt that his motor cant make that kind of torque at 6000rpm with only a cam modification?
The number was almost 200 psi and you can now tell that is extremely high. So much higher than the standard engine with 140 psi and anything with 200 psi is very efficient, as the article says huge work with a roller cam required for 214 psi, much more than a cam change and tuning. Roller cams generally have quicker valve action which is a very powerful tool in building cylinder pressure, i.e torque.
Tuomo and others tuning will change the BMEP figures but volumetric efficiency in the calculators is presumed with properly running engines. No where in a calculator will it say, give engine a tune up and gain 10%. Then the levels that are being discussed are such lofty levels. Especially for one that doesn't have special manifolds. Please read up on Engine Masters and then you can see what they do to get to these levels at that rpm band.
Now as I said before Pipemax gives around 200 feet per second airspeed for this engine at 6,000 rpm , i.e very slow, now Mark your airspeed will be higher but as soon as any part of your intake system chokes then it is game over. Once an intake has a sonic choke it is limited to that amount of flow. The engine is still a system, it will make sure you don't forget that.
As I mentioned before 270 feet per second (minimum) was told to me by a trusted source as the figure needed to achieve 105% volumetric efficiency, so 200 FPS is no where near it, Tuomo got a higher figure but I don't know how he got it. The reason I am chucking the stroker into it is that if Tuomo figures are correct the stroker airspeeds will be extremely high, now they may be able to run them depending on how high they are as they generally have throttle bodies but every engine has a limit before the friction losses of pumping the air overwhelm the gains from burning more air and fuel. I await those figures with interest.
Some F1 engines have achieved up to 145% and it might be of further interest that the port of an F1 engine is no bigger than your 4 valve 928 ports and in another thread with Tuomo I posted how similar they were showing a pic of one. Current spec V8 F1 engines are in the high 700s maybe some have hit 800 hp and that is with same port size, so what does that say to you? Well for one, the air must travel twice as fast as what it does in the 928 port when the 928 engine is producing around 400 hp.
So my velocity figure was calculated of a port size of 2.42 sq" and as Darin's article says average velocity is very important and he also names the calculator I use to calculate it, it is in fact very simple to use. The domestic V8 guys aim generally for 310 FPS in properly running engines, as you see it is quite a long way from 200 FPS. The calculator I have calculates average velocity and at 28"
As to Mark's Ks engine, it is probably running somewhat like an air restricted engine, they normally like little overlap on the cams but with plenty of lift, heaps of compression and not too many revs.
The stuff I didn't respond to, maybe later, I have addressed the main issues I believe. Hope it helps.
Greg
#206

By Dennis K
My comments are certainly not meant to be an attack and in fact it is a response to high flywheel numbers are general that get bandied around and in fact were posted by someone in this thread.
Given nobody had ever to my knowledge had brought up BMEP or intake velocities (although I do acknowledge Kim Crumb as he has discussed it elsewhere) and given this is a mainly technical forum I thought it appropriate and like your hard work and mine, none of it comes cheaply.
Greg
Skepticism is good. If I had read an internet post such as my initial post a couple years ago, I wouldn't have believed it either. I've been extremely open about what we've done to this motor, far more open than most. I've also tried to be as responsible as possible with the results.
There seem to be a lot of assumptions about flywheel HP (& in turn BMEP) & BSFC (& in turn volumetric efficiency) that I haven't & wouldn't make. I have been careful not to claim a flywheel hp number. Unless the engine is put on an engine dyno, I would not feel comfortable stating a number.
Currently, we're maxxed out on duty cycle on 24lb injectors w/ a 13:1 AFR so that's a sign something good is happening. I've run the car side by side w/ Bill's supercharged S4 & Jim's stock GTS and I've played w/ Kibort stroker at the track and the results seem to confirm where we are.
I think there are two big stories - the torque curve (1st graph) and the gain via tuning (2nd graph). The engine makes the same torque (or BMEP if you like) at 5000 rpm as 4000 rpm. To me, that's the real breakthrough. This is the first 5.0L 928 motor I've ever seen that does that. In the second graph, we gained 50 lb-ft of torque in some places all via tuning. It shows how valuable Sharktuner + a great tuner like Jim can be.
As a final note, none of the information I've posted has come cheaply. The amount of hours that Jim & Bill have donated to this project is ungodly. Jim has traded equipment & labor for dyno time. John Holleran certainly hasn't made money given the amount of time he's spent w/ us on his dyno. If people want further confirmation or to parse out the result of each modification, please consider making a large cash donation for the dyno time and our time. The information I've posted is free. It's worth what you've paid. Believe it, don't believe it - it's up to you. We've done the best we can. And as Bill said, we're having a whole lot of fun!
__________________
Dennis
There seem to be a lot of assumptions about flywheel HP (& in turn BMEP) & BSFC (& in turn volumetric efficiency) that I haven't & wouldn't make. I have been careful not to claim a flywheel hp number. Unless the engine is put on an engine dyno, I would not feel comfortable stating a number.
Currently, we're maxxed out on duty cycle on 24lb injectors w/ a 13:1 AFR so that's a sign something good is happening. I've run the car side by side w/ Bill's supercharged S4 & Jim's stock GTS and I've played w/ Kibort stroker at the track and the results seem to confirm where we are.
I think there are two big stories - the torque curve (1st graph) and the gain via tuning (2nd graph). The engine makes the same torque (or BMEP if you like) at 5000 rpm as 4000 rpm. To me, that's the real breakthrough. This is the first 5.0L 928 motor I've ever seen that does that. In the second graph, we gained 50 lb-ft of torque in some places all via tuning. It shows how valuable Sharktuner + a great tuner like Jim can be.
As a final note, none of the information I've posted has come cheaply. The amount of hours that Jim & Bill have donated to this project is ungodly. Jim has traded equipment & labor for dyno time. John Holleran certainly hasn't made money given the amount of time he's spent w/ us on his dyno. If people want further confirmation or to parse out the result of each modification, please consider making a large cash donation for the dyno time and our time. The information I've posted is free. It's worth what you've paid. Believe it, don't believe it - it's up to you. We've done the best we can. And as Bill said, we're having a whole lot of fun!
__________________
Dennis
Given nobody had ever to my knowledge had brought up BMEP or intake velocities (although I do acknowledge Kim Crumb as he has discussed it elsewhere) and given this is a mainly technical forum I thought it appropriate and like your hard work and mine, none of it comes cheaply.

Greg
#207
Nordschleife Master

Tuomo and others tuning will change the BMEP figures but volumetric efficiency in the calculators is presumed with properly running engines. No where in a calculator will it say, give engine a tune up and gain 10%. Then the levels that are being discussed are such lofty levels. Especially for one that doesn't have special manifolds. Please read up on Engine Masters and then you can see what they do to get to these levels at that rpm band.
As far as using BMEP numbers as a bull**** detector, that's a reasonable thing to do. However, if we do that, let's calibrate the scale for the rear wheel Dynojet numbers. Once we estimate driveline losses, Dynojet correction factors, and whatnot, these errors are going to swamp the signal. Since Dynojet is standard in the US, perhaps because the owners like the results, let's calibrate our BMEP scales to Dynojet RWHP.
Now as I said before Pipemax gives around 200 feet per second airspeed for this engine at 6,000 rpm , i.e very slow, now Mark your airspeed will be higher but as soon as any part of your intake system chokes then it is game over. Once an intake has a sonic choke it is limited to that amount of flow. The engine is still a system, it will make sure you don't forget that.
Greg, I value these exchanges a lot as I think I learn all the time. So even if it may sometimes read as if I am lecturing about stuff to you, that's not what's going on. There's no question that you understand these issues better than I am, which is evident to everyone on the forum as well as to me. If I am challenging your assertions, that's because I want to learn why that is.
As I mentioned before 270 feet per second (minimum) was told to me by a trusted source as the figure needed to achieve 105% volumetric efficiency, so 200 FPS is no where near it, Tuomo got a higher figure but I don't know how he got it. The reason I am chucking the stroker into it is that if Tuomo figures are correct the stroker airspeeds will be extremely high, now they may be able to run them depending on how high they are as they generally have throttle bodies but every engine has a limit before the friction losses of pumping the air overwhelm the gains from burning more air and fuel. I await those figures with interest.

Clearly, this is not the same as Dennis's engine. He's got those Elgin 65-6 cams and higher static compression. But I think it's relevant for the air speed discussion. Notice how even at 6000 rpm, with S3 cams the flow reverses a bit. Do I interpret this correctly when I say that this is evidence of even the S3 cams needing higher rpm (or more displacement) to work well in the S4 heads?
I also run a straight experiment, where I run the simulation software with different intake port diameters. The largest port is the 1.8 inch diameter port which corresponds to about the same area as the S4 stock (2.5 square inches, give or take). This is for S4 with static compression lifted to 10.5 and S3 cams installed. The results, below, say that the best peak and 4000-7000 average power comes with the largest 1.8 inch diameter port. This is with the intake manifold programmed to be restrictive. I don't know how much weight to put on these results.
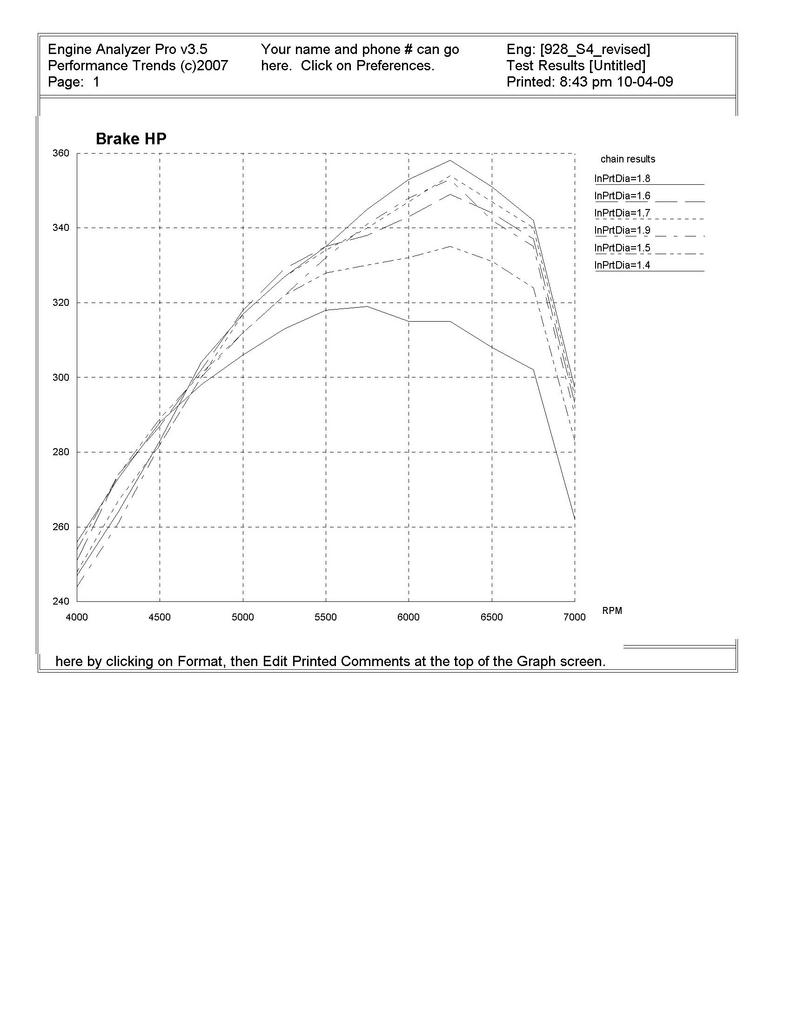
So my velocity figure was calculated of a port size of 2.42 sq" and as Darin's article says average velocity is very important and he also names the calculator I use to calculate it, it is in fact very simple to use. The domestic V8 guys aim generally for 310 FPS in properly running engines, as you see it is quite a long way from 200 FPS. The calculator I have calculates average velocity and at 28"
As to Mark's Ks engine, it is probably running somewhat like an air restricted engine, they normally like little overlap on the cams but with plenty of lift, heaps of compression and not too many revs.
As to Mark's Ks engine, it is probably running somewhat like an air restricted engine, they normally like little overlap on the cams but with plenty of lift, heaps of compression and not too many revs.
Not taking these simulations as the truth, but I guess they are at least as good as other rules of thumb.
#208
Nordschleife Master

I'd be willing to chip in on the cost of a trip down some sanctioned 1320ft track.
No need to spin tires or beat up the drive line, trap speed and weight of the car and driver for the run are plenty for me.

#209
Rennlist Member

1- see thread "Boost, head gaskets and bmep"
2 - in 1997/98 we bolted on B level cams onto a stock S4 and generated ~360 rwhp at 6800 rpm on Keiths Dynojet, no tuning, just rrfr and a few tricks to keep the pulses from reaching the MAF to keep it running at idle
3 - First gen B cam resulted in extremely poor fuel control and had no idle, B1 is slightly better with less overlap
4- 1997 and there was no SharkTuner...darn!!
5- on any given day at any given dyno, results will vary
2 - in 1997/98 we bolted on B level cams onto a stock S4 and generated ~360 rwhp at 6800 rpm on Keiths Dynojet, no tuning, just rrfr and a few tricks to keep the pulses from reaching the MAF to keep it running at idle
3 - First gen B cam resulted in extremely poor fuel control and had no idle, B1 is slightly better with less overlap
4- 1997 and there was no SharkTuner...darn!!
5- on any given day at any given dyno, results will vary
#210

Hey Tuomo, no offence is meant by my post if it came over strong maybe it was the just the difference between the written word or spoken word. You also know me from the other websites, as such you know that I am more than happy to be corrected. I don't need to hear my own voice. The more I have learnt, the less I realize I know, it is very very complex this business and I think that is the reason you sometimes get results that are not expected.
By Ptuomov
I am not really following this, if the S4 port is as you say 2.5sq" why does that correspond with the 1.8 sq" in the program? I would have thought it has to be the same. I think this is where we have the problem with these heads, too big for the size of motor. Maybe you can explain what is going on with the different sizes.
The charts you put up don't show the average velocity, the average velocity is what I am referring to. The port measure was done by volume by another Rennlister and I measured the length of the port. It may be the 2.5 sq" as you say, how did you measure it? I notice you are using ports down to 1.4 sq" so basically one sq" smaller that is a massive change that is one of the recommendations/suggestions of Pipemax. Of course every head is different and will respond accordingly.
Greg
By Ptuomov
I also run a straight experiment, where I run the simulation software with different intake port diameters. The largest port is the 1.8 inch diameter port which corresponds to about the same area as the S4 stock (2.5 square inches, give or take). This is for S4 with static compression lifted to 10.5 and S3 cams installed. The results, below, say that the best peak and 4000-7000 average power comes with the largest 1.8 inch diameter port. This is with the intake manifold programmed to be restrictive. I don't know how much weight to put on these results.
The charts you put up don't show the average velocity, the average velocity is what I am referring to. The port measure was done by volume by another Rennlister and I measured the length of the port. It may be the 2.5 sq" as you say, how did you measure it? I notice you are using ports down to 1.4 sq" so basically one sq" smaller that is a massive change that is one of the recommendations/suggestions of Pipemax. Of course every head is different and will respond accordingly.
Greg