Tales of Sierra - A 997.1 Story
#61

Finally bit the bullet and took care of replacing the foam on the blend air flap. Didn't feel like cutting into the HVAC ducts to replace the other flap that distributes the air to the different vents.
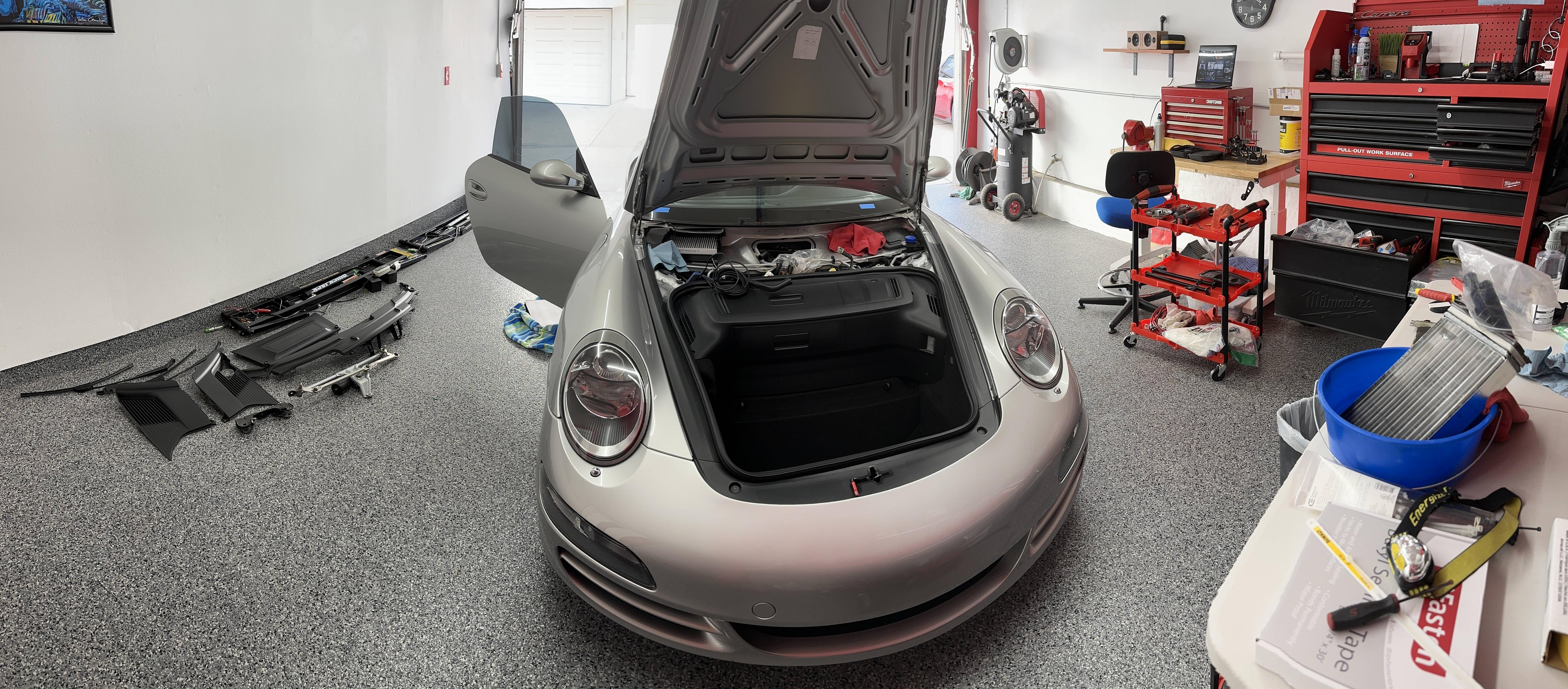

Supplies: new foam, butyl tape for the heater core cover, clamps for coolant hoses, and a fresh hacksaw blade.

Remove the windshield wiper blades and then take out the cowl:

Remove the tower braces and the wiper mechanism with 3, 10 mm bolts:

Remove the battery but first slide the passenger seat back all the way. You'll need the room later on.
Cut the butyl tape without damaging the foam. Probably could've re-used the tape as in just press it back together afterwards, but I didn't wanna take any chances with potential water ingress.

Now we're here with minimal coolant loss.

Gently extract the heater core. Those fins are super thin.

Now you can see the flap and sure, you're thinking the foam looks pretty good, but a slight poke and it starts to crumble.

There are 2 clips that hold the flap in place. There's no access to the top one as this isn't meant to be a serviceable part, so cut off the top and pull out the clip.

Now for the uncomfortable part of getting to the bottom clip. There's a motor that operates the flap and the linkage arm is attached to the bottom of the clip. Remove the 6 mm bolt and move the arm away...

...to expose the bottom of the clip. Getting this out (without breaking it) was a pain, but of course now I'm smarter about what needs to happen. I read about people "just using a pick" to remove it, others screwed in the bolt and yanked on it (not recommended given the plastic threads), and others struggled like I did, as evidenced by all the visible scratches:

Eventually I got it to pop out by using a screwdriver that ended up pushing down on the tab you see below. I tried using a pick at first and while that was thin enough to fit in the slot, I wasn't able to push down on the tab with the small tip. The screwdriver I used was a little too wide for the slot, but with enough persuasion it worked out.

With the clip removed, you can see the bottom of the flap at the hinge line:

Victory is mine.

Sanded it smooth and wiped it down with alcohol before applying the new foam.


Use paint thinner to remove the butyl tape. Nice & shiny for the win.

Vacuum the area.

Used the same butyl tape to seal the plastic cap back on.

Reinstalled the flap and got the clip to snap back into place. The flap needs to be perfectly centered, otherwise it'll fight you. Fight you hard.

Original cover back on. In hindsight, the 3/4" wide tape was excessive but the next time the foam cover needs to be removed, there should be plenty to re-use.

No need to bleed the coolant system, so I just topped it off, turned the heat to max, opened the breather valve on the expansion tank, and purged the air.

Cleaning up the cowl for good measure.

I think what I'm going to do, knowing the other flap still has the old foam, is just run the fan on max every time I wash the car. Just try to force the foam to fly out while also picking it out of the vents as eventually all of it will fly off. I also noticed the original foam has a clear layer that will likely remain attached to the flap; it's different to the gray foam. Even though it's porous, I think that'll still help in directing the flow to the different vents.
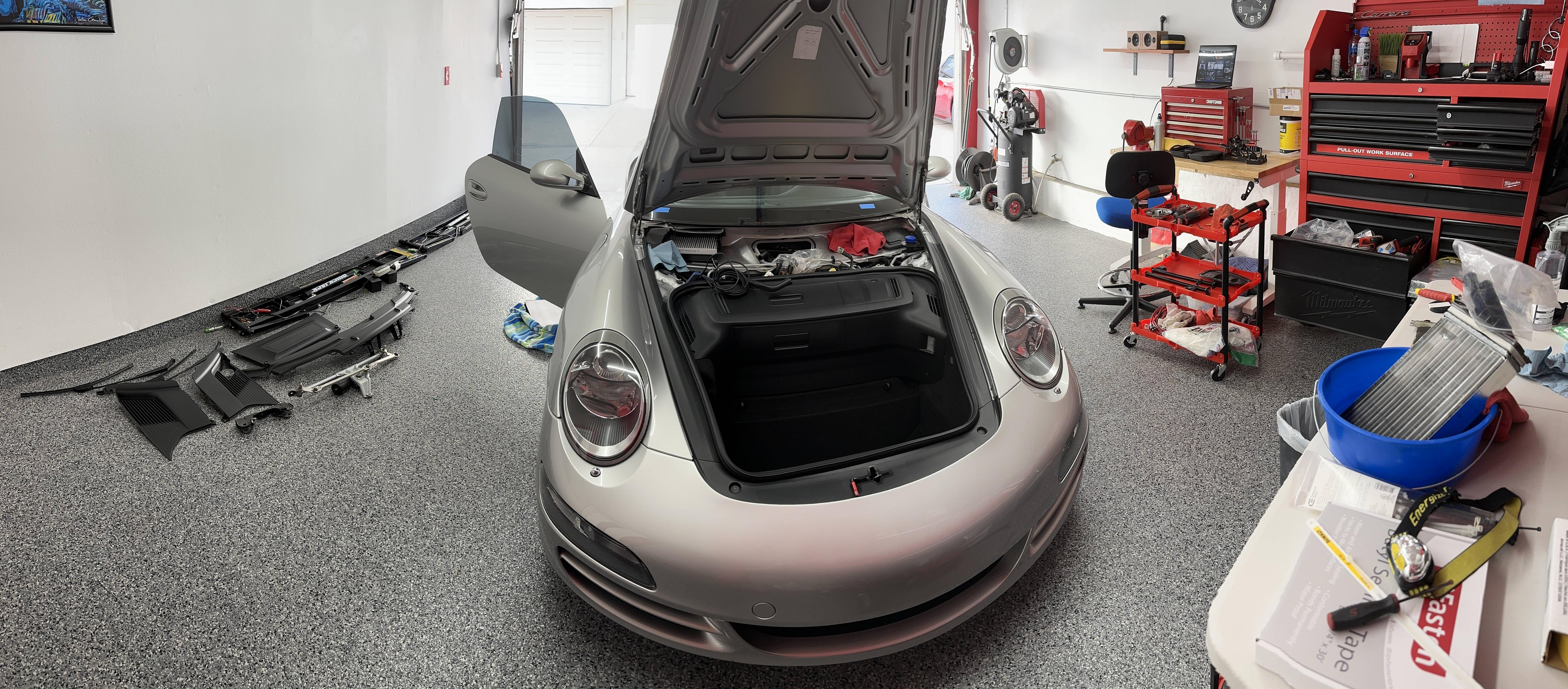

Supplies: new foam, butyl tape for the heater core cover, clamps for coolant hoses, and a fresh hacksaw blade.

Remove the windshield wiper blades and then take out the cowl:

Remove the tower braces and the wiper mechanism with 3, 10 mm bolts:

Remove the battery but first slide the passenger seat back all the way. You'll need the room later on.
Cut the butyl tape without damaging the foam. Probably could've re-used the tape as in just press it back together afterwards, but I didn't wanna take any chances with potential water ingress.

Now we're here with minimal coolant loss.

Gently extract the heater core. Those fins are super thin.

Now you can see the flap and sure, you're thinking the foam looks pretty good, but a slight poke and it starts to crumble.

There are 2 clips that hold the flap in place. There's no access to the top one as this isn't meant to be a serviceable part, so cut off the top and pull out the clip.

Now for the uncomfortable part of getting to the bottom clip. There's a motor that operates the flap and the linkage arm is attached to the bottom of the clip. Remove the 6 mm bolt and move the arm away...

...to expose the bottom of the clip. Getting this out (without breaking it) was a pain, but of course now I'm smarter about what needs to happen. I read about people "just using a pick" to remove it, others screwed in the bolt and yanked on it (not recommended given the plastic threads), and others struggled like I did, as evidenced by all the visible scratches:

Eventually I got it to pop out by using a screwdriver that ended up pushing down on the tab you see below. I tried using a pick at first and while that was thin enough to fit in the slot, I wasn't able to push down on the tab with the small tip. The screwdriver I used was a little too wide for the slot, but with enough persuasion it worked out.

With the clip removed, you can see the bottom of the flap at the hinge line:

Victory is mine.

Sanded it smooth and wiped it down with alcohol before applying the new foam.


Use paint thinner to remove the butyl tape. Nice & shiny for the win.

Vacuum the area.

Used the same butyl tape to seal the plastic cap back on.

Reinstalled the flap and got the clip to snap back into place. The flap needs to be perfectly centered, otherwise it'll fight you. Fight you hard.

Original cover back on. In hindsight, the 3/4" wide tape was excessive but the next time the foam cover needs to be removed, there should be plenty to re-use.

No need to bleed the coolant system, so I just topped it off, turned the heat to max, opened the breather valve on the expansion tank, and purged the air.

Cleaning up the cowl for good measure.

I think what I'm going to do, knowing the other flap still has the old foam, is just run the fan on max every time I wash the car. Just try to force the foam to fly out while also picking it out of the vents as eventually all of it will fly off. I also noticed the original foam has a clear layer that will likely remain attached to the flap; it's different to the gray foam. Even though it's porous, I think that'll still help in directing the flow to the different vents.
The following users liked this post:
kiznarsh (10-21-2022)
#63

Thank you for detailing the process and sharing with us all. I'm not sure I have the stomach for a project like that, so I hope I won't need this anytime soon.
The following users liked this post:
kiznarsh (11-13-2022)
The following users liked this post:
kiznarsh (11-13-2022)
#65

After driving with the aluminum shifter bushings for a few months, decided I want more precise action so got myself the Numeric shifter. I have the updated OEM cables and right now don't plan on swapping those out.
Removing the shift **** is much easier when it's new.
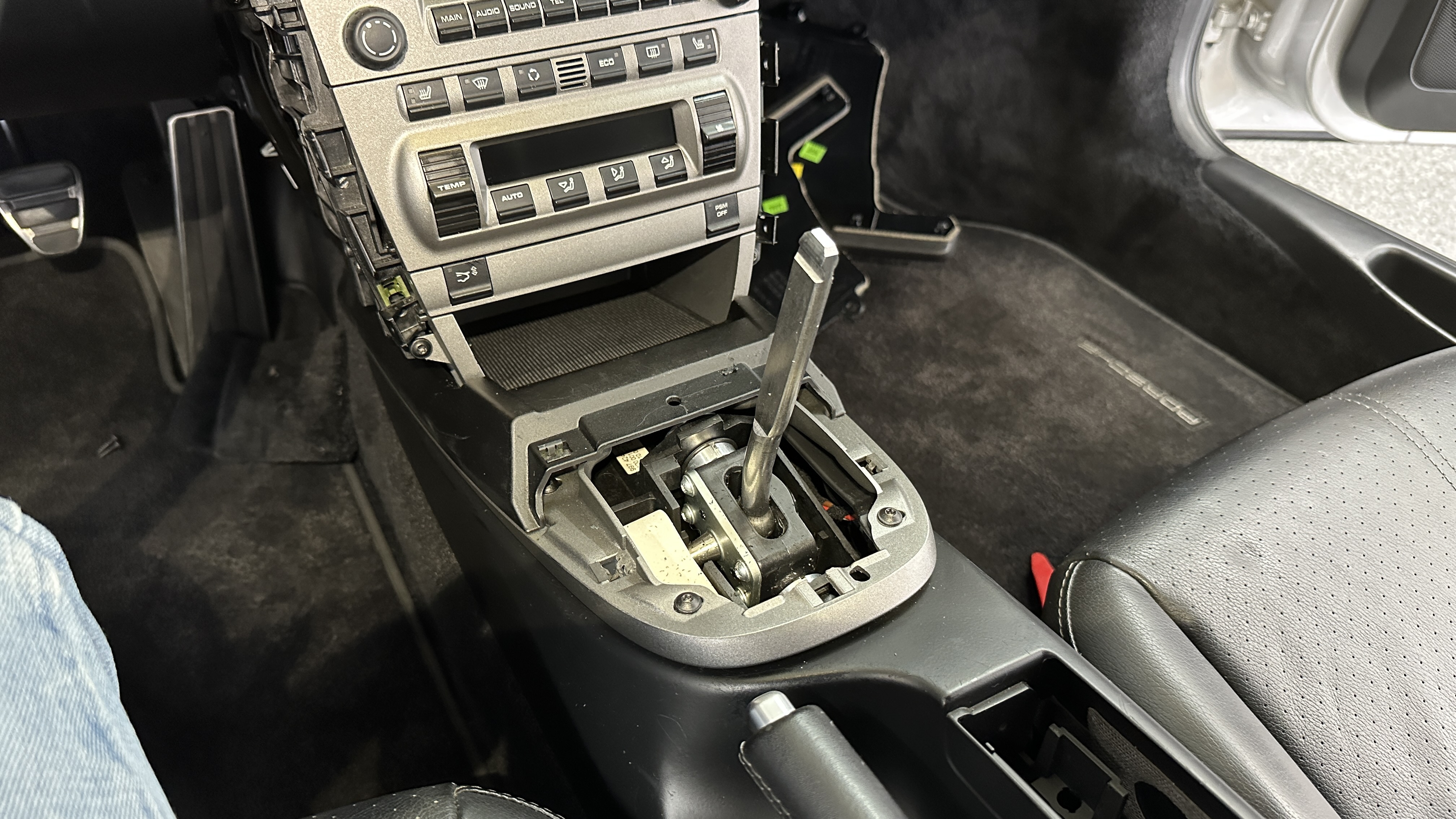
Significant difference between the two. Not a single piece of plastic to be found! And the spherical bearings are great.



Pop off the plastic rivet on one cable end, and twist off the other.

T27 for the tightening screw.

Permanent thread locker and grease, as applicable.

There's a washer on each side of the shift lever. Access is tight but using grease to hold them in place simplifies things quite a bit. Quite a bit.

Reading for install.

The brackets that hold the cables are adjustable which is a great design feature. Made reassembly straightforward.

Went with the middle position which is shorter than stock, but not too short.

Then out for a test drive by the Kianski Tree (I'm just gonna claim it's mine now).

So now I have experience with:
~~~
After driving for a while, I swapped it back to the stock height (lowest hole) and much happier with it. Still very crisp and precise, and feels more natural.
Removing the shift **** is much easier when it's new.

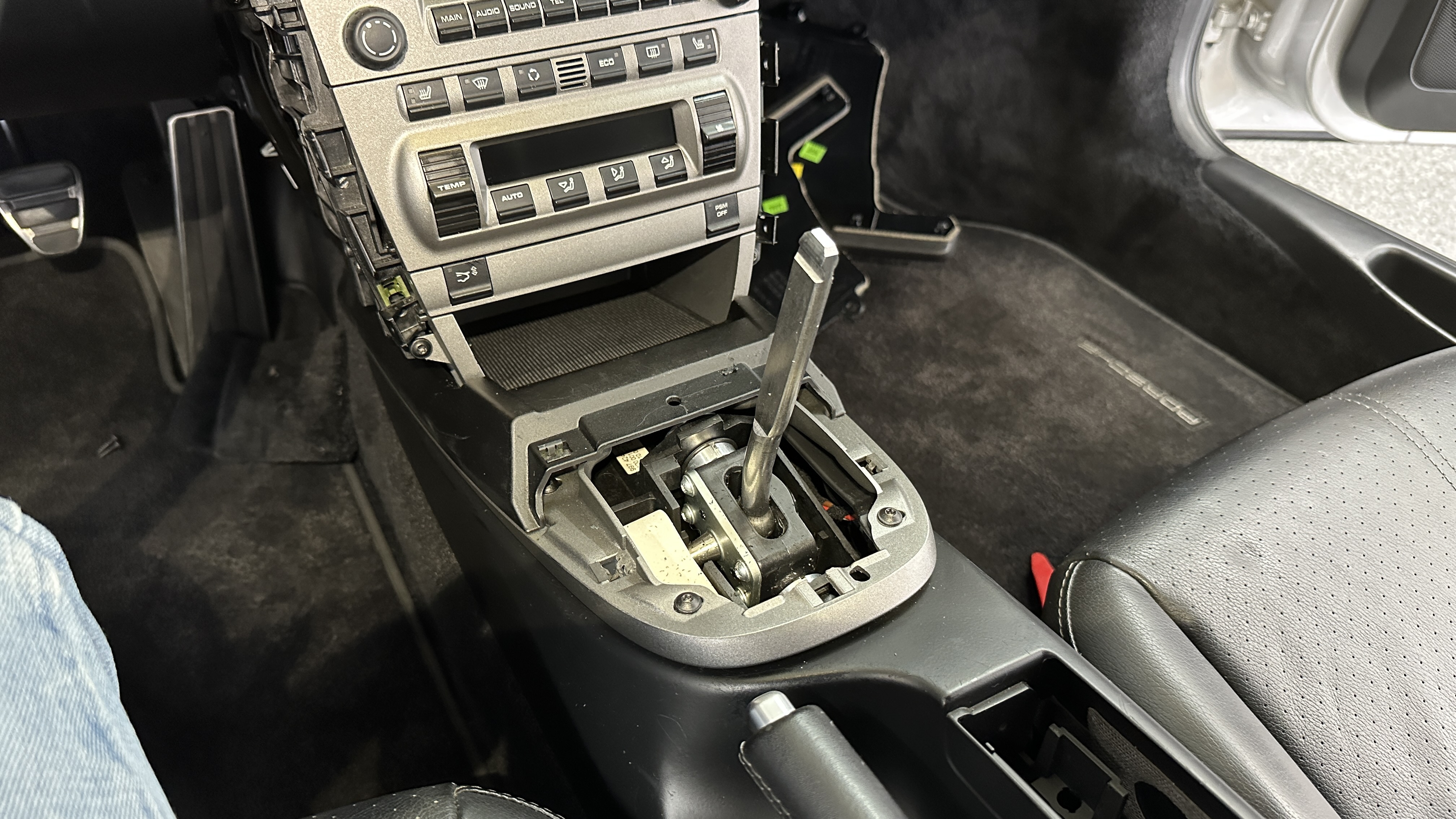
Significant difference between the two. Not a single piece of plastic to be found! And the spherical bearings are great.



Pop off the plastic rivet on one cable end, and twist off the other.

T27 for the tightening screw.

Permanent thread locker and grease, as applicable.

There's a washer on each side of the shift lever. Access is tight but using grease to hold them in place simplifies things quite a bit. Quite a bit.

Reading for install.

The brackets that hold the cables are adjustable which is a great design feature. Made reassembly straightforward.

Went with the middle position which is shorter than stock, but not too short.

Then out for a test drive by the Kianski Tree (I'm just gonna claim it's mine now).

So now I have experience with:
- Stock shifter + stock cables
- Stock shifter + Numeric cables (987)
- Stock shifter with aluminum bushings + stock cables
- Numeric shifter (middle hole) + stock cables
- Easy to engage each gear but sloppy
- Rifle-bolt action changes, increased NVH, loudest gear change, ideal for spirited driving
- Probably best for a daily with sufficient feel for occasional spirited driving
- Shorter throw, solid engagement, getting into reverse requires more effort
~~~
After driving for a while, I swapped it back to the stock height (lowest hole) and much happier with it. Still very crisp and precise, and feels more natural.
The following users liked this post:
Graufuchs (11-13-2022)
#66

Time for another update. Back in November I installed the 991 front spoiler through @Emc2design.


Used my new cribs which I bought specifically for these types of jobs. Weight capacity: 1,500 lbs each for those keeping track at home.

Freshened up some of the fasteners while I had easy access.

Marking centerlines.


Gotta cut off the tabs.

Mark the holes and start drilling (9 total).

These adapters grab the OEM tabs.

The installation process begins: 3 in the middle, 2 support adapters on each side, then 2 at each end.

Rubber trim piece to cover the part of the spoiler that can't be hidden because...well...because this isn't designed for a 997. Also covers any unintentional gaps.

And here we are:


Used my new cribs which I bought specifically for these types of jobs. Weight capacity: 1,500 lbs each for those keeping track at home.

Freshened up some of the fasteners while I had easy access.

Marking centerlines.


Gotta cut off the tabs.

Mark the holes and start drilling (9 total).

These adapters grab the OEM tabs.

The installation process begins: 3 in the middle, 2 support adapters on each side, then 2 at each end.

Rubber trim piece to cover the part of the spoiler that can't be hidden because...well...because this isn't designed for a 997. Also covers any unintentional gaps.

And here we are:
#67

Time for the biannual maintenance plus some other goodies and unpleasant discoveries. Well, just one.
I recently discovered my local Pep Boys which has become an Advance Auto Parts stocks Liqui Moly (same price as online: $50 for a 5-liter jug).

Looks like a little seepage from the RTV that I cleaned up for now.

Flushed the brake fluid with ATE 200.

While bleeding the front right caliper, noticed what looks like wheel bearing grease starting to leak out. I'll do more investigating later but the easiest option appears to be removing the hub and having it pressed out.

I had no records of the plugs being replaced and decided to tackle the coils at the same time. There's a newer version that came out since the original ones had a tendency to crack. Stuck with OEM brands and bought the kit from FCP Euro. Also finally bought a better spark plug socket where the extension is pinned so you don't have to mess with taping it on.

Knowing access is tight, bit the bullet and removed a bunch of parts to make extraction easier. Tail lights and rear bumper cover are straightforward.

Then removed the outer heat shield, muffler, and the inner heat shield that provided me great access, except for that pesky muffler bracket that's in the way.

Needed a 13mm crowfoot for the inner heat shield.
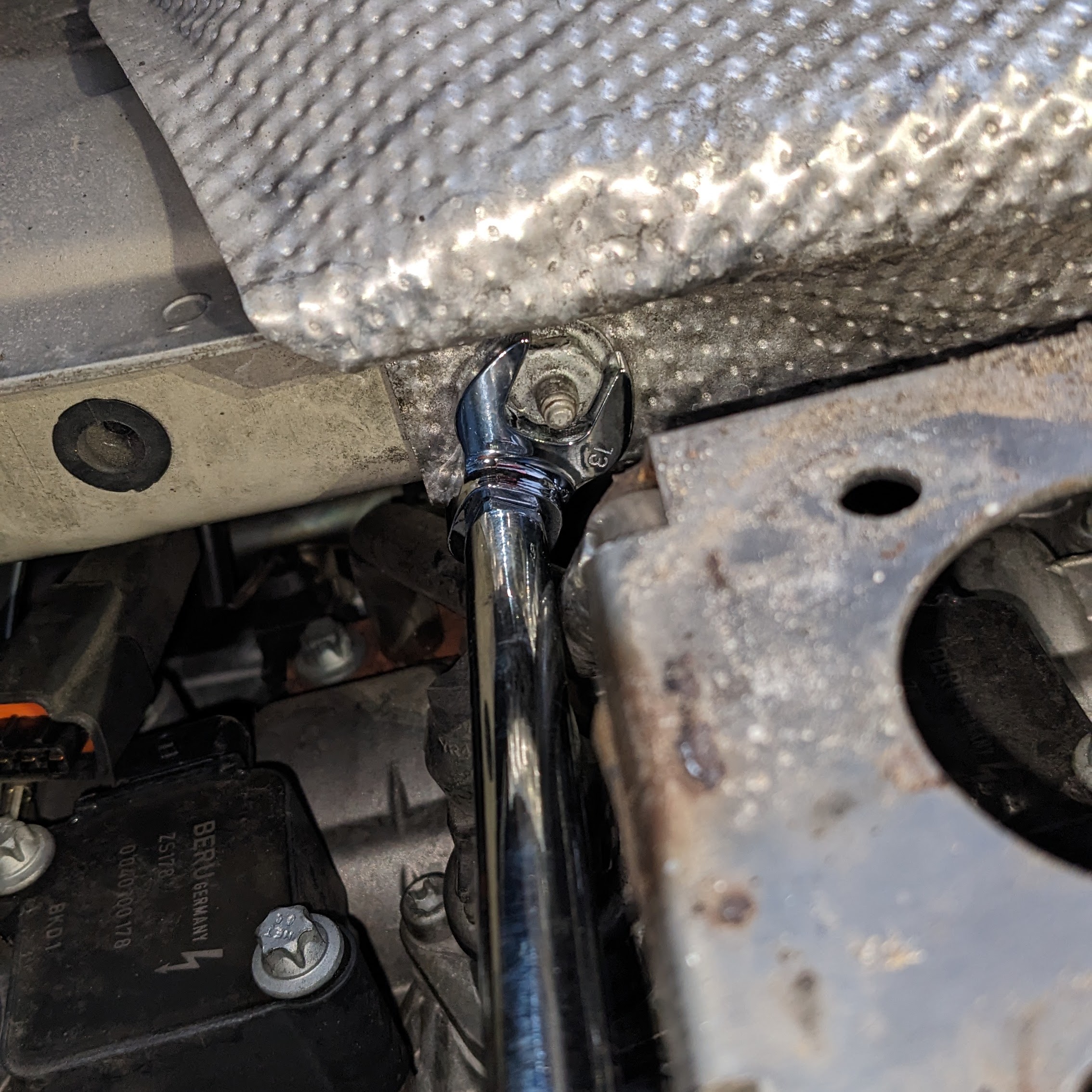
The new coil packs come with longer screws since the part is thicker, but when I compared them, they're actually the same. Then I went back and realized the coils were actually replaced 3 years ago with the updated version. Welp, I reset the clock and now have a spare set.

Access for the coil pack on the passenger side (cylinder 5) was tough but I was able to pull it out with zip ties.

And with the muffler bracket in there, still had to use my old socket for the 2 middle plugs.

But hey, they all came out easily so I do recommend taking the time to remove everything.

Good to go.

Cleaned the area before reassembling everything, because reasons.

New engine and cabin air filters.


The mesh screen at the bottom of the air filter housing was getting a little nasty, so replaced that (special order part).

This protective film in the door jamb was an eye sore. Well, it's an eye sore no more!

New ignition trim. I always look before inserting the key specifically so I don't scratch it.

And a little NEVR DULL polish on the exhaust tips.

I'm at 45k miles right now and after another road trip in December, still really enjoying it. Comfortable on the highways but extremely capable in the twisties. It'll rest for a while and I don't plan on driving it until I get the wheel bearing replaced.
The rear seats creak more than I'd like (although only audible without playing music) so that's something I'd like to address. And for some reason the trick of disconnecting the navigation to allow a manual reset of the date no longer works. It keeps reverting to April 2003 and there's no way to hide the date on the main screen which is what I like to see. The Bluetooth module sometimes resets to AUX IN which requires a power cycle, so I gotta crawl in the passenger footwell to do that, but it's not that often.
I recently discovered my local Pep Boys which has become an Advance Auto Parts stocks Liqui Moly (same price as online: $50 for a 5-liter jug).

Looks like a little seepage from the RTV that I cleaned up for now.

Flushed the brake fluid with ATE 200.

While bleeding the front right caliper, noticed what looks like wheel bearing grease starting to leak out. I'll do more investigating later but the easiest option appears to be removing the hub and having it pressed out.

I had no records of the plugs being replaced and decided to tackle the coils at the same time. There's a newer version that came out since the original ones had a tendency to crack. Stuck with OEM brands and bought the kit from FCP Euro. Also finally bought a better spark plug socket where the extension is pinned so you don't have to mess with taping it on.

Knowing access is tight, bit the bullet and removed a bunch of parts to make extraction easier. Tail lights and rear bumper cover are straightforward.

Then removed the outer heat shield, muffler, and the inner heat shield that provided me great access, except for that pesky muffler bracket that's in the way.

Needed a 13mm crowfoot for the inner heat shield.
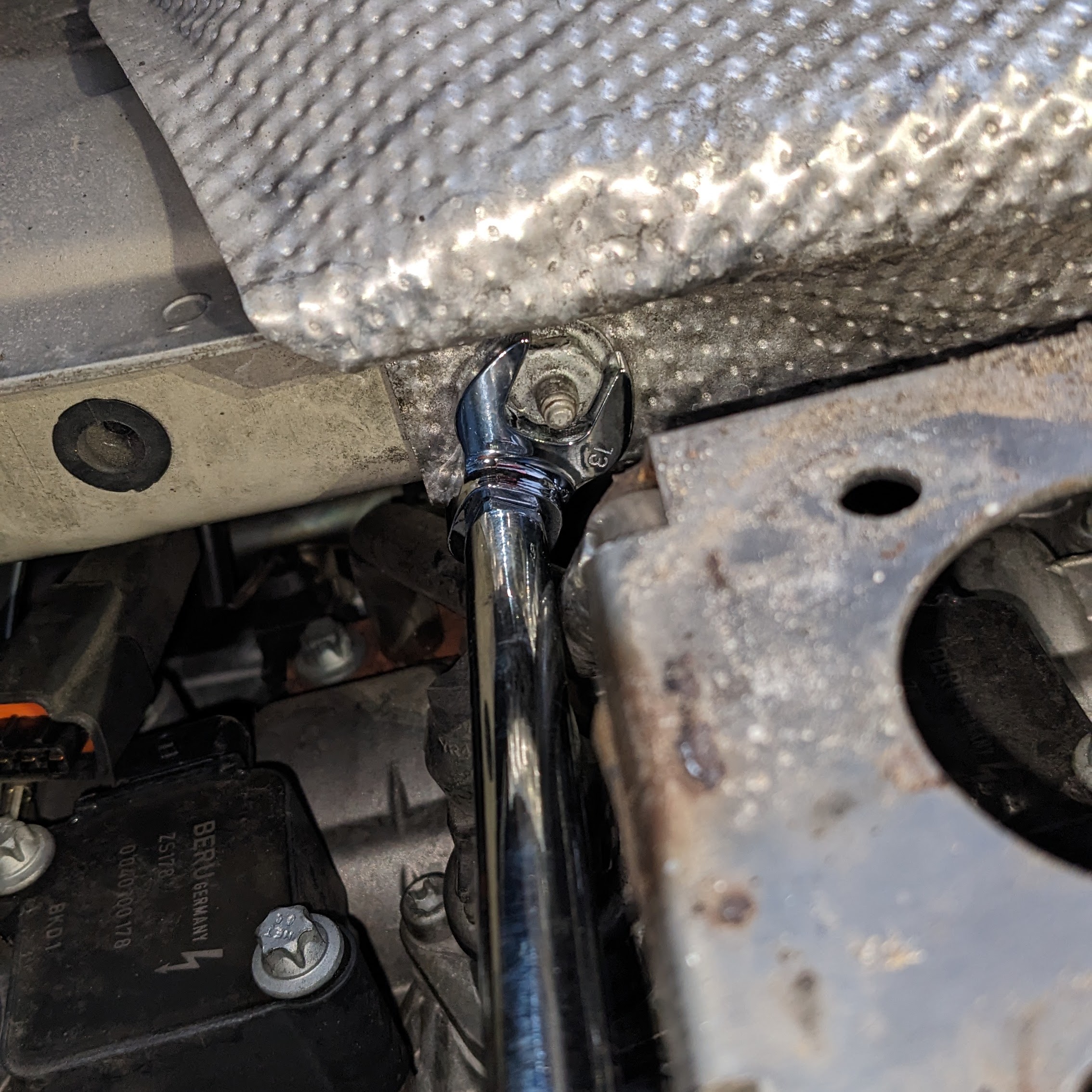
The new coil packs come with longer screws since the part is thicker, but when I compared them, they're actually the same. Then I went back and realized the coils were actually replaced 3 years ago with the updated version. Welp, I reset the clock and now have a spare set.

Access for the coil pack on the passenger side (cylinder 5) was tough but I was able to pull it out with zip ties.

And with the muffler bracket in there, still had to use my old socket for the 2 middle plugs.

But hey, they all came out easily so I do recommend taking the time to remove everything.

Good to go.

Cleaned the area before reassembling everything, because reasons.

New engine and cabin air filters.


The mesh screen at the bottom of the air filter housing was getting a little nasty, so replaced that (special order part).

This protective film in the door jamb was an eye sore. Well, it's an eye sore no more!

New ignition trim. I always look before inserting the key specifically so I don't scratch it.

And a little NEVR DULL polish on the exhaust tips.

I'm at 45k miles right now and after another road trip in December, still really enjoying it. Comfortable on the highways but extremely capable in the twisties. It'll rest for a while and I don't plan on driving it until I get the wheel bearing replaced.
The rear seats creak more than I'd like (although only audible without playing music) so that's something I'd like to address. And for some reason the trick of disconnecting the navigation to allow a manual reset of the date no longer works. It keeps reverting to April 2003 and there's no way to hide the date on the main screen which is what I like to see. The Bluetooth module sometimes resets to AUX IN which requires a power cycle, so I gotta crawl in the passenger footwell to do that, but it's not that often.
The following 4 users liked this post by kiznarsh:
#69

@kiznarsh Thanks for taking the time to document the process, for visual learners like me the photos/descriptions are a huge help. I've had the laptop on the garage floor with me more than once!
Quick question regarding the protective strips - are they removed essentially like stone guards with a bit of heat?
Quick question regarding the protective strips - are they removed essentially like stone guards with a bit of heat?
#70

@kiznarsh Thanks for taking the time to document the process, for visual learners like me the photos/descriptions are a huge help. I've had the laptop on the garage floor with me more than once!
Quick question regarding the protective strips - are they removed essentially like stone guards with a bit of heat?
Quick question regarding the protective strips - are they removed essentially like stone guards with a bit of heat?
Yes, heat will work fine on the protective strips but don't need anything more than just a heat gun (no steam). The material is thicker and becomes "gummy" if you heat it too much so I just applied a little at a time, then used a plastic trim tool to remove it. The residue is also not as bad as the stone guards; I just used alcohol which you'll need to do anyway for a clean surface before applying the new film.
The following users liked this post:
TheMurse (01-05-2023)
#71

Previously in this thread, we were investigating the presence of grease where it didn't really belong on a single hub.

Removed the caliper and rotor for a closer look, and realized there's really no path for the wheel bearing grease to get there...

Without the rotor, I rotated the hub and it definitely felt notchy. Thus began the process of getting it out with the goal of just removing the carrier and having a shop press it out. The tie rod ball joint popped out quite easily, but the control arm was being...oh how shall I put it...uncooperative.
After removing the strut for more access, a friend and I tried using an air hammer as my ball joint removal tool wouldn't fit. Then once the threads on the ball joint shaft started getting mangled, I busted out the propane torch (seen below in yellow) cuz that's all I had. Heated up the carrier and that was enough to release it with another powerful blow of the air hammer. The heat-resistant blanket is protecting the bushing the middle of the control arm. Yeah, don't forget to protect that, mkay?

At this point we really could've (and likely should've) stopped, but we were high off the celebration of getting the ball joint out and decided to press on. Having neither a puller for the hub nor a hydraulic press for the bearing, we used the 4 bolts for the bearing retaining plate as push-off screws to separate the hub. Same philosophy as a puller of course, just way more tedious.

After many blows, the bearing was finally out. It's a double row bearing that gets destroyed during this process.

The inner race was still stuck on the hub that I was planning on re-using, so I cut a slot in it, then used a chisel to release its grip on the hub and ultimately pounded it off with a punch and dead-blow hammer.
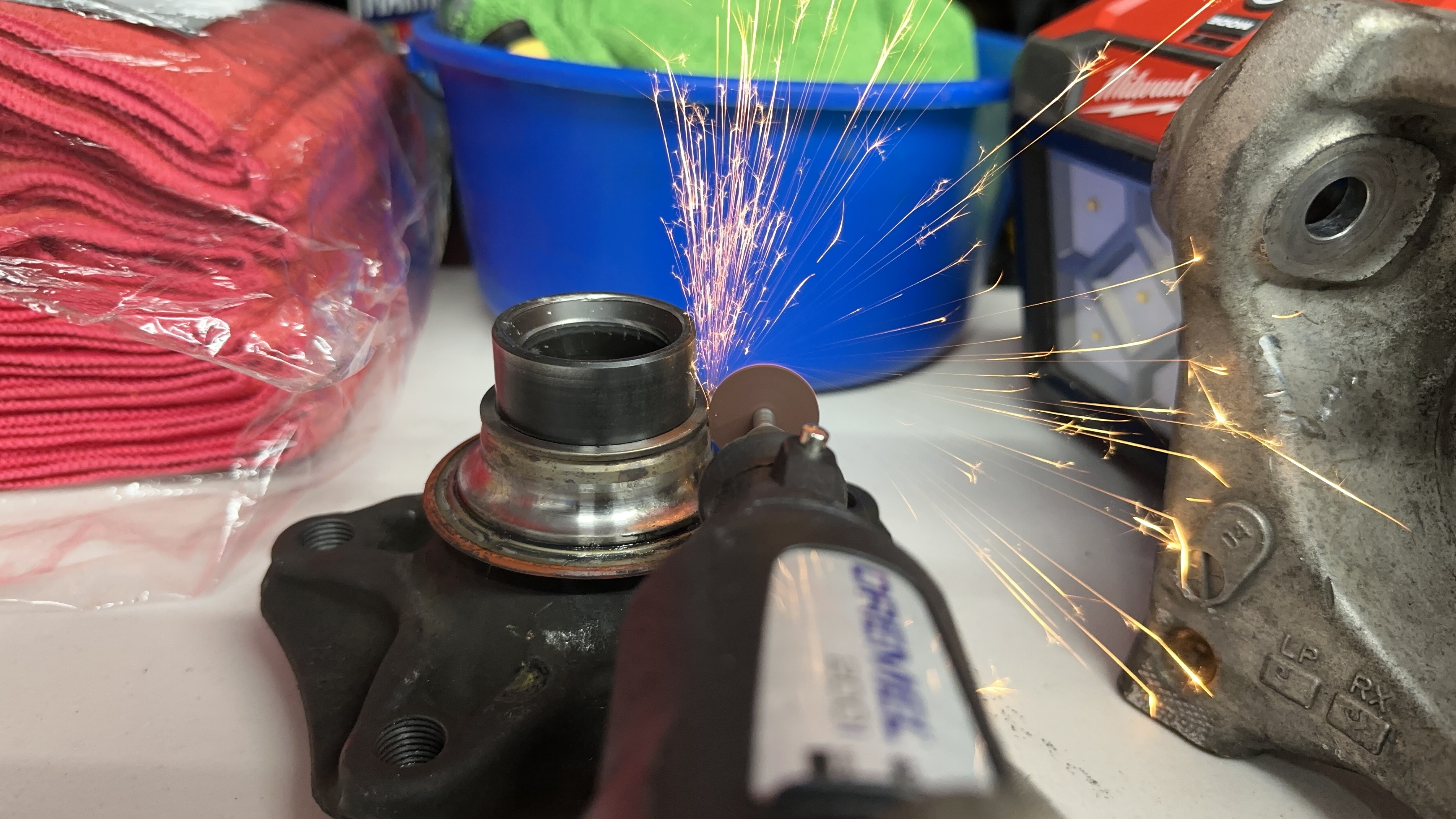

Then called around and got quotes from Porsche indy shops to press in the bearing, one gave an estimate of $345 and one that quoted me $150. That's about what I expected for about an hour's worth of work. Made an appointment and in the mean time, ordered parts:
Bearing:

New caliper bolts and axle nut (single-use items). Also new lock nuts for the ball joints.
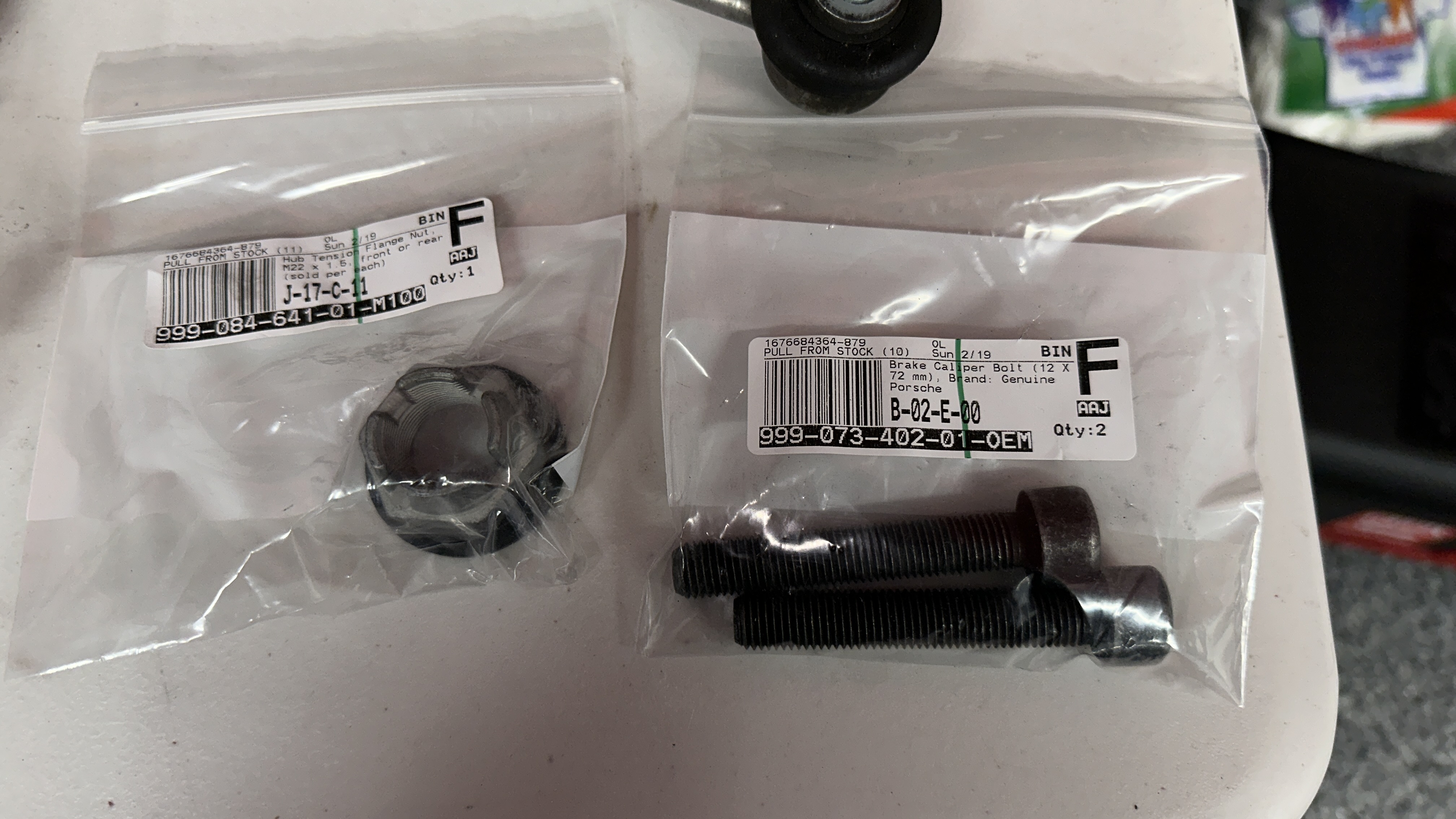
Noticed the boot on the sway bar end link was torn, so replaced both of them too.

And lastly a new hub with a 991 part number.

Picked up the assembled carrier after an indy shop pressed everything back together. I cleaned up the M12x1.5 threads on the control arm ball joint.

Torqued the sway bar end links:

Used the thin wrench against the chassis to counter-hold:

Back in business.
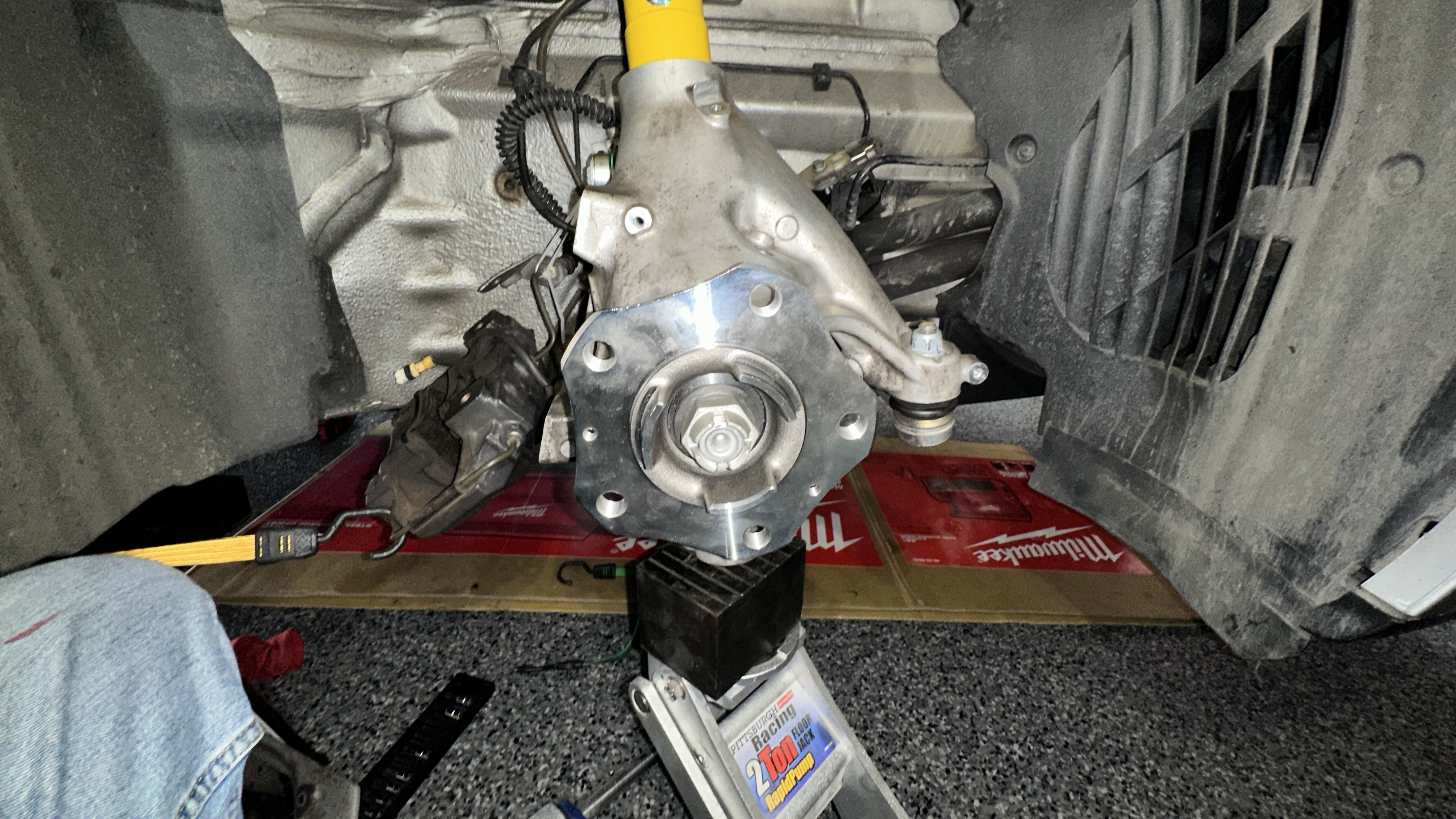
Then the fun part: torquing the axle nut to 340 ft-lbs. Yeah, it's a big boy.


Took it for a spin yesterday and everything seems to be good! I marked the shock mount nuts on the chassis to reposition the shock in the same spot, and only loosened the control arm bushing nut enough to let it swing down. So I think my alignment is still good, or at least imperceptibly off.

Removed the caliper and rotor for a closer look, and realized there's really no path for the wheel bearing grease to get there...

Without the rotor, I rotated the hub and it definitely felt notchy. Thus began the process of getting it out with the goal of just removing the carrier and having a shop press it out. The tie rod ball joint popped out quite easily, but the control arm was being...oh how shall I put it...uncooperative.
After removing the strut for more access, a friend and I tried using an air hammer as my ball joint removal tool wouldn't fit. Then once the threads on the ball joint shaft started getting mangled, I busted out the propane torch (seen below in yellow) cuz that's all I had. Heated up the carrier and that was enough to release it with another powerful blow of the air hammer. The heat-resistant blanket is protecting the bushing the middle of the control arm. Yeah, don't forget to protect that, mkay?

At this point we really could've (and likely should've) stopped, but we were high off the celebration of getting the ball joint out and decided to press on. Having neither a puller for the hub nor a hydraulic press for the bearing, we used the 4 bolts for the bearing retaining plate as push-off screws to separate the hub. Same philosophy as a puller of course, just way more tedious.

After many blows, the bearing was finally out. It's a double row bearing that gets destroyed during this process.

The inner race was still stuck on the hub that I was planning on re-using, so I cut a slot in it, then used a chisel to release its grip on the hub and ultimately pounded it off with a punch and dead-blow hammer.
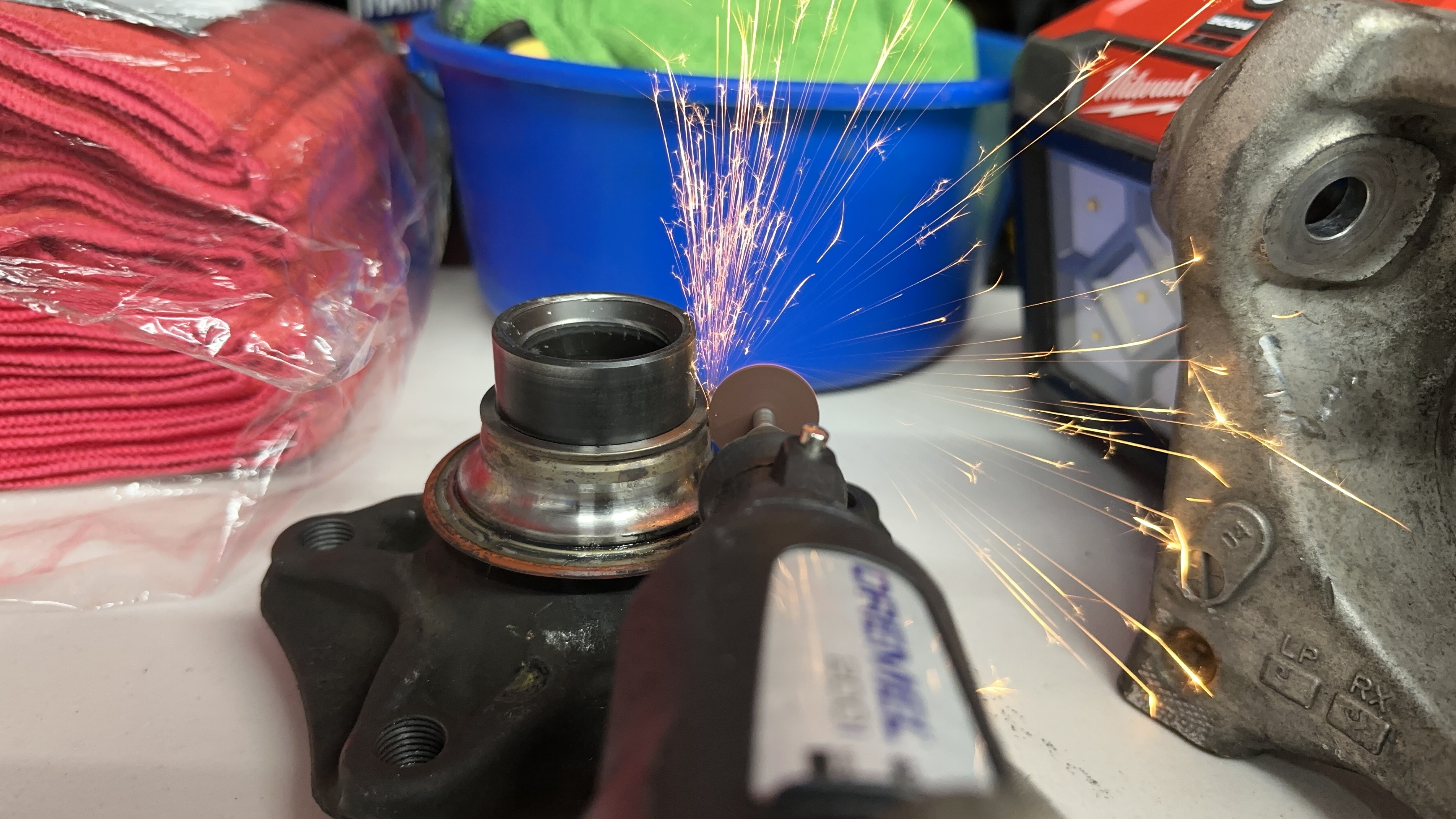

Then called around and got quotes from Porsche indy shops to press in the bearing, one gave an estimate of $345 and one that quoted me $150. That's about what I expected for about an hour's worth of work. Made an appointment and in the mean time, ordered parts:
Bearing:

New caliper bolts and axle nut (single-use items). Also new lock nuts for the ball joints.
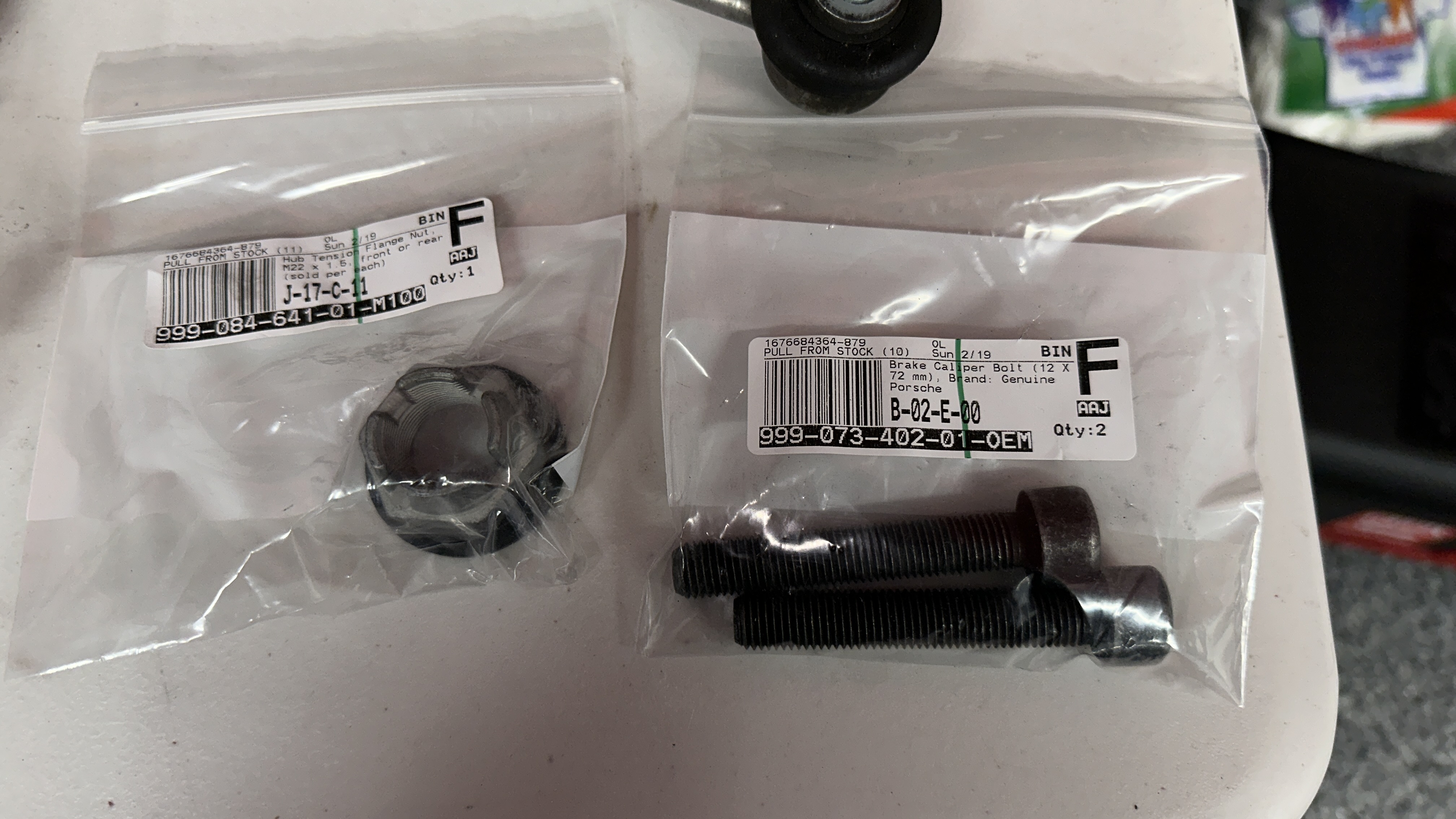
Noticed the boot on the sway bar end link was torn, so replaced both of them too.

And lastly a new hub with a 991 part number.

Picked up the assembled carrier after an indy shop pressed everything back together. I cleaned up the M12x1.5 threads on the control arm ball joint.

Torqued the sway bar end links:

Used the thin wrench against the chassis to counter-hold:

Back in business.
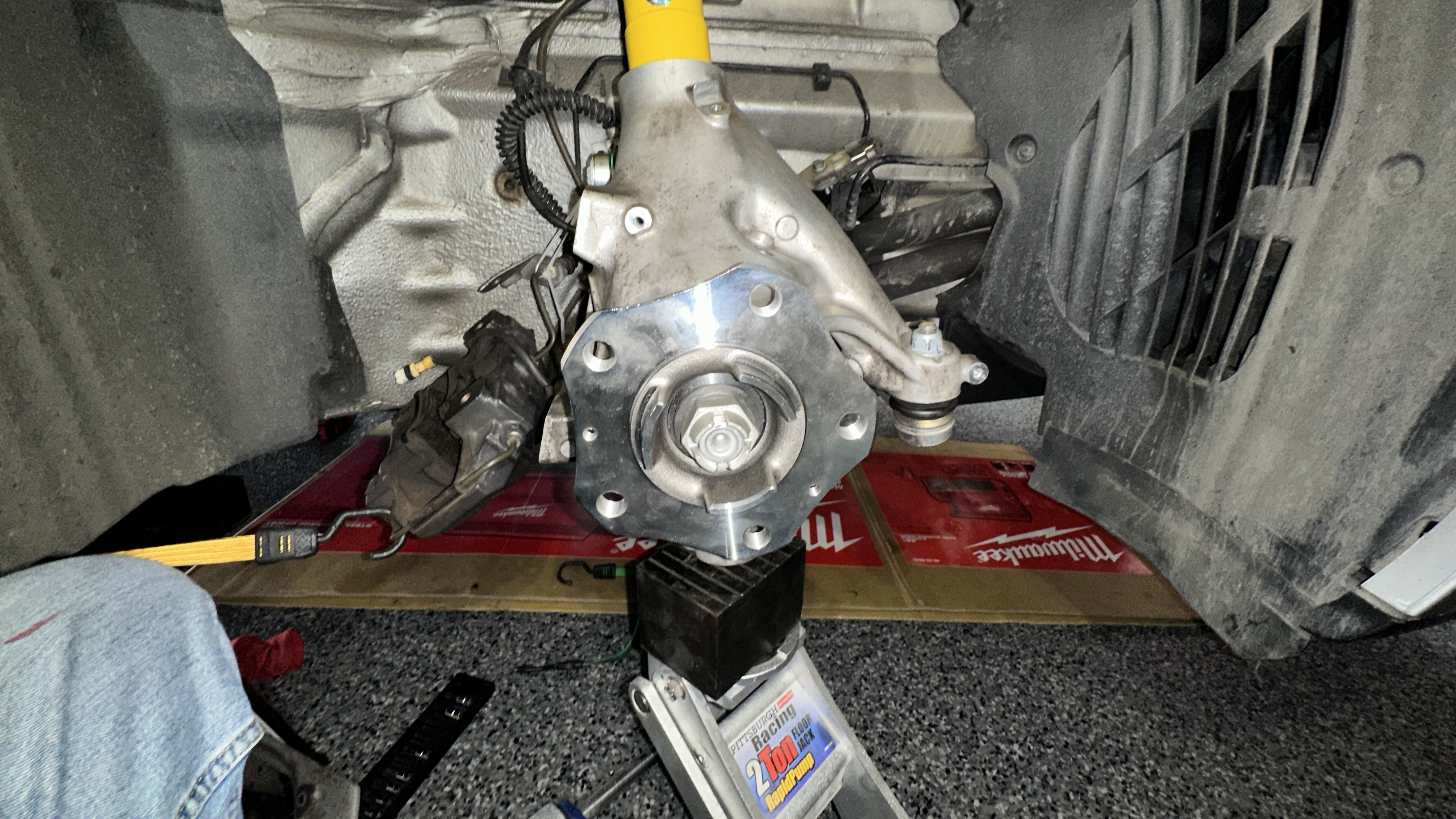
Then the fun part: torquing the axle nut to 340 ft-lbs. Yeah, it's a big boy.


Took it for a spin yesterday and everything seems to be good! I marked the shock mount nuts on the chassis to reposition the shock in the same spot, and only loosened the control arm bushing nut enough to let it swing down. So I think my alignment is still good, or at least imperceptibly off.
The following users liked this post:
Graufuchs (03-09-2023)
#72

kiznarsh - you are why i joined this forum. wouldn't have come across this epic thread had you not been posting to it, so please continue to do so. literally everything you've documented are projects I plan to do to my 06 C2. I will say I hope I never have to do a wheel bearing. There's a video on YT of a guy working on a yellow 996 and the process to get the old bearing out is just not worth it to DIY. I'm afraid your pictures aren't reconciling things any more for me and I've done a wheel bearing job before on a 2003 BMW M3.
Keep up the great work and documenting!
I've bookmarked your thread as it really encompasses a ton of the different maintenance and upgrade projects a 997 needs. I would certainly vote to have this thread being .... stickied!
Keep up the great work and documenting!
I've bookmarked your thread as it really encompasses a ton of the different maintenance and upgrade projects a 997 needs. I would certainly vote to have this thread being .... stickied!
Last edited by aasilvia; 03-09-2023 at 02:15 PM.
The following users liked this post:
fritzcurtis (03-10-2023)
#73

kiznarsh - you are why i joined this forum. wouldn't have come across this epic thread had you not been posting to it, so please continue to do so. literally everything you've documented are projects I plan to do to my 06 C2. I will say I hope I never have to do a wheel bearing. There's a video on YT of a guy working on a yellow 996 and the process to get the old bearing out is just not worth it to DIY. I'm afraid your pictures aren't reconciling things any more for me and I've done a wheel bearing job before on a 2003 BMW M3.
Keep up the great work and documenting!
I've bookmarked your thread as it really encompasses a ton of the different maintenance and upgrade projects a 997 needs. I would certainly vote to have this thread being .... stickied!
Keep up the great work and documenting!
I've bookmarked your thread as it really encompasses a ton of the different maintenance and upgrade projects a 997 needs. I would certainly vote to have this thread being .... stickied!
The wheel bearing replacement wasn't enjoyable and unusual given the mileage (45k) but glad it's sorted now.