What Oil Pump for Transaxle??
#1

So... Rebuilt trans has provisions for additional cooling and lubrication. Clearly I want to use these...
Looking at the Tilton 40-527; rated for 1000 hour of continuous use without cool down. Supposed to handle temps and fluid viscosities well. While it's doubtful this car will be driven in severe cold, I do expect it to be chilly at times.
https://www.summitracing.com/parts/til-40-527
Thoughts? What say the gurus?
Thanks!
Looking at the Tilton 40-527; rated for 1000 hour of continuous use without cool down. Supposed to handle temps and fluid viscosities well. While it's doubtful this car will be driven in severe cold, I do expect it to be chilly at times.
https://www.summitracing.com/parts/til-40-527
Thoughts? What say the gurus?
Thanks!
#2
#4

I also read that article. The fittings etc. are in slightly different places now, 10 years later on. I'm assuming Evan's fittings are in the same place as mine are.

I used a Setrab pump with a 150-micron filter. That little oil-to-air heat exchanger is completely inadequate and installed in the wrong orientation. I expected that heat exchanger would be about useless; I ran out of time to get the car ready and that is all I could get my hands on.
The Setrab pump I used is this one: https://www.pegasusautoracing.com/pr...sp?RecID=29884 and it's rated for 240 minutes on/15 minutes off. I was really concerned about getting oil flow to the bearings and gears in the front of the gearbox so as not to trash 5th gear again. Any cooling from that heat exchanger was a complete bonus.
I also installed a trans temp gauge. The sensor for the trans temp gauge is in the suction line for the pump. I used an 8AN Male/Female adapter with an 1/8 NPT port for the temp sensor: https://www.summitracing.com/parts/sum-220676b and a short sensor that did not obstruct the flow: https://www.summitracing.com/parts/atm-2259 with a trans temp gauge that matches the factory gauges fairly closely: https://www.summitracing.com/parts/atm-8349.
With the temp sensor in the pump suction line the gauge is only useful when the pump is running. I installed a toggle switch for the pump.
Since I had to remove the console anyway to install the Numeric shifter and I have a GT3 console delete package to install, then I ran out of time, I did not yet install the console. I mounted the trans temp gauge like this, to the existing bracket for the stock center console:

I will eventually install the console and GT3 front console delete. When I do that I will make up a bracket that sticks out of the "hole" in front of the shifter and remount the Cobb and trans temp gauge there.
That picture was taken after 30 minutes on track at Lime Rock and shows the little oil-to-air heat exchanger is completely useless. I now have a much larger oil to air heat exchanger with two fans that I am going to install where the front diff used to be. I'm using dry break fittings on the lines to that heat exchanger that are this type: https://www.pegasusautoracing.com/pr...asp?RecID=3277 so I can remove the transmission without making my usual huge mess. I am also going to install a second sensor for the trans temp gauge to read oil temp into the transmission after the oil cooler, and a switch to select which temp sensor the gauge shows. This way I can see what the oil cooler is actually doing. The upgrade heat exchanger, piping, and second temp sensor are still waiting to be installed this week.

I used a Setrab pump with a 150-micron filter. That little oil-to-air heat exchanger is completely inadequate and installed in the wrong orientation. I expected that heat exchanger would be about useless; I ran out of time to get the car ready and that is all I could get my hands on.
The Setrab pump I used is this one: https://www.pegasusautoracing.com/pr...sp?RecID=29884 and it's rated for 240 minutes on/15 minutes off. I was really concerned about getting oil flow to the bearings and gears in the front of the gearbox so as not to trash 5th gear again. Any cooling from that heat exchanger was a complete bonus.
I also installed a trans temp gauge. The sensor for the trans temp gauge is in the suction line for the pump. I used an 8AN Male/Female adapter with an 1/8 NPT port for the temp sensor: https://www.summitracing.com/parts/sum-220676b and a short sensor that did not obstruct the flow: https://www.summitracing.com/parts/atm-2259 with a trans temp gauge that matches the factory gauges fairly closely: https://www.summitracing.com/parts/atm-8349.
With the temp sensor in the pump suction line the gauge is only useful when the pump is running. I installed a toggle switch for the pump.
Since I had to remove the console anyway to install the Numeric shifter and I have a GT3 console delete package to install, then I ran out of time, I did not yet install the console. I mounted the trans temp gauge like this, to the existing bracket for the stock center console:

I will eventually install the console and GT3 front console delete. When I do that I will make up a bracket that sticks out of the "hole" in front of the shifter and remount the Cobb and trans temp gauge there.
That picture was taken after 30 minutes on track at Lime Rock and shows the little oil-to-air heat exchanger is completely useless. I now have a much larger oil to air heat exchanger with two fans that I am going to install where the front diff used to be. I'm using dry break fittings on the lines to that heat exchanger that are this type: https://www.pegasusautoracing.com/pr...asp?RecID=3277 so I can remove the transmission without making my usual huge mess. I am also going to install a second sensor for the trans temp gauge to read oil temp into the transmission after the oil cooler, and a switch to select which temp sensor the gauge shows. This way I can see what the oil cooler is actually doing. The upgrade heat exchanger, piping, and second temp sensor are still waiting to be installed this week.
#6

Thanks Prf. That definitely helps me a lot. I'm looking at a MOCAL pump, $300, rated for continuous use. I want that trans getting oil all the time. Going to use a thermostat and probably a small front mounted cooler. I'll have to run lines somewhere, but I think I can make it work.
Even 250*F doesn't scare me, but it's definitely warmer than I'd have expected.
Even 250*F doesn't scare me, but it's definitely warmer than I'd have expected.
#7

The trans runs about 180F on the highway. That 250F was after 4, 30 minute sessions on track with 40 minutes between them. Each session the final temp got hotter so I know the heat exchanger was not doing much.
I realized the pictures I posted do not show the completed lines. This one from under the car with the gearbox installed shows how I routed the suction line to the pump. The 8AN fitting for the suction line sticks down quite far so I used a tight 90 degree fitting on it to keep things close to the gearbox. I made a bracket that's under the left hand CV joint to hold the suction hose and keep it out of the CV joint area.

I realized the pictures I posted do not show the completed lines. This one from under the car with the gearbox installed shows how I routed the suction line to the pump. The 8AN fitting for the suction line sticks down quite far so I used a tight 90 degree fitting on it to keep things close to the gearbox. I made a bracket that's under the left hand CV joint to hold the suction hose and keep it out of the CV joint area.

Trending Topics
#9

I finally installed a MUCH BIGGER transmission oil cooler. I was not overly thrilled about running lines to the front of the car, so I decided to put the heat exchanger where the front diff used to be. I used a Deraile 51678 heat exchanger which is about the biggest that will fit in the available space. I wanted a Mocal unit that the Deraile copied, I could not get the Mocal in time. The Mocal is a far better heat exchanger, the Deraile unit is pop riveted together, so I'll replace it with a Mocal when I can.
I installed the heat exchanger by making up some brackets that bolt to the front diagonal braces and to the front subframe where the front diff attaches. It is a tight fit. I used 120 degree 8AN fitting on the heat exchanger to angle the hoses down the tunnel. I also installed two 4" moped radiator fans on the back side of the heat exchanger.

This picture is looking in from the driver's side where the driveshaft used to be.

I ran a pair of 8AN lines through the tunnel, and added a pair of dry break fittings at the transmission end so I can remove the transmission (or the heat exchanger) without making a huge mess. The dry break fittings are protected behind the black stamped steel transmission mount extension. I did make brackets for these fittings so they aren't banging around. The stray electrical connector is for the oil temperature into the transmission.

The plumbing on the transmission is much simpler, as I no longer have the woefully inadequate heat exchanger there. I ran the pump output line and the return to the transmission up over the curved transmission support to keep them away from the cardan shaft drive. Having the hoses run like this is important as it creates a point where the hoses are higher than the oil level in the gearbox. If this is not done there is a possibility of all the oil in the cooler running back into the gearbox, which would raise the level much higher than is desirable.
A couple brackets keep the suction line away from the left side driveshaft. The suction is plumbed into the gearbox under the limited slip diff and should be pulling the hottest oil.

I mounted the heat exchanger so that it receives airflow from the naca ducts on the undertray. I had to cut the small outer naca ducts more than I anticipated.

So, how did all this work?
Last time out with the tiny side-mounted heat exchanger I saw trans oil temps of 245F after 3 sessions of 20 minutes. The oil temp increased after each session, something like 220F then 230F then 245F. To compare temperatures, highway driving gives about 180F for gearbox temperature.
With the new cooler setup the highest temp I saw for oil into the gearbox was 185F. This was after the fifth 20 minute session on one of the hottest days of the year. I did not use the heat exchanger fans while on track, it was not necessary as the naca ducts seem to give plenty of airflow.
As soon as I pulled off track (not driving fast anymore) the oil temperature started to increase and that's when I turned on the fans, while I was doing a casual drive around the pits for a cool down. Based on this I an sure the ducts are providing plenty of air as long as the speed is fairly high (50 mph?). Running the fans afterwards kept the temperature around 185. I have a temperature gauge on the oil out of and in to the trans so I can see what the heat exchanger is doing.
I also wired up a time delay so I can leave the trans pump and fans running after I shut the car off to further cool the trans. The timer shuts the system off after 20 minutes.
Although I would prefer a GT2 type built-in trans pump and cooler that was not in the budget. I am really happy with how this turned out!
I installed the heat exchanger by making up some brackets that bolt to the front diagonal braces and to the front subframe where the front diff attaches. It is a tight fit. I used 120 degree 8AN fitting on the heat exchanger to angle the hoses down the tunnel. I also installed two 4" moped radiator fans on the back side of the heat exchanger.

This picture is looking in from the driver's side where the driveshaft used to be.

I ran a pair of 8AN lines through the tunnel, and added a pair of dry break fittings at the transmission end so I can remove the transmission (or the heat exchanger) without making a huge mess. The dry break fittings are protected behind the black stamped steel transmission mount extension. I did make brackets for these fittings so they aren't banging around. The stray electrical connector is for the oil temperature into the transmission.

The plumbing on the transmission is much simpler, as I no longer have the woefully inadequate heat exchanger there. I ran the pump output line and the return to the transmission up over the curved transmission support to keep them away from the cardan shaft drive. Having the hoses run like this is important as it creates a point where the hoses are higher than the oil level in the gearbox. If this is not done there is a possibility of all the oil in the cooler running back into the gearbox, which would raise the level much higher than is desirable.
A couple brackets keep the suction line away from the left side driveshaft. The suction is plumbed into the gearbox under the limited slip diff and should be pulling the hottest oil.

I mounted the heat exchanger so that it receives airflow from the naca ducts on the undertray. I had to cut the small outer naca ducts more than I anticipated.

So, how did all this work?
Last time out with the tiny side-mounted heat exchanger I saw trans oil temps of 245F after 3 sessions of 20 minutes. The oil temp increased after each session, something like 220F then 230F then 245F. To compare temperatures, highway driving gives about 180F for gearbox temperature.
With the new cooler setup the highest temp I saw for oil into the gearbox was 185F. This was after the fifth 20 minute session on one of the hottest days of the year. I did not use the heat exchanger fans while on track, it was not necessary as the naca ducts seem to give plenty of airflow.
As soon as I pulled off track (not driving fast anymore) the oil temperature started to increase and that's when I turned on the fans, while I was doing a casual drive around the pits for a cool down. Based on this I an sure the ducts are providing plenty of air as long as the speed is fairly high (50 mph?). Running the fans afterwards kept the temperature around 185. I have a temperature gauge on the oil out of and in to the trans so I can see what the heat exchanger is doing.
I also wired up a time delay so I can leave the trans pump and fans running after I shut the car off to further cool the trans. The timer shuts the system off after 20 minutes.
Although I would prefer a GT2 type built-in trans pump and cooler that was not in the budget. I am really happy with how this turned out!
#10

So, how did all this work?
Last time out with the tiny side-mounted heat exchanger I saw trans oil temps of 245F after 3 sessions of 20 minutes. The oil temp increased after each session, something like 220F then 230F then 245F. To compare temperatures, highway driving gives about 180F for gearbox temperature.
With the new cooler setup the highest temp I saw for oil into the gearbox was 185F. This was after the fifth 20 minute session on one of the hottest days of the year. I did not use the heat exchanger fans while on track, it was not necessary as the naca ducts seem to give plenty of airflow.
As soon as I pulled off track (not driving fast anymore) the oil temperature started to increase and that's when I turned on the fans, while I was doing a casual drive around the pits for a cool down. Based on this I an sure the ducts are providing plenty of air as long as the speed is fairly high (50 mph?). Running the fans afterwards kept the temperature around 185. I have a temperature gauge on the oil out of and in to the trans so I can see what the heat exchanger is doing.
I also wired up a time delay so I can leave the trans pump and fans running after I shut the car off to further cool the trans. The timer shuts the system off after 20 minutes.
Although I would prefer a GT2 type built-in trans pump and cooler that was not in the budget. I am really happy with how this turned out!
Last time out with the tiny side-mounted heat exchanger I saw trans oil temps of 245F after 3 sessions of 20 minutes. The oil temp increased after each session, something like 220F then 230F then 245F. To compare temperatures, highway driving gives about 180F for gearbox temperature.
With the new cooler setup the highest temp I saw for oil into the gearbox was 185F. This was after the fifth 20 minute session on one of the hottest days of the year. I did not use the heat exchanger fans while on track, it was not necessary as the naca ducts seem to give plenty of airflow.
As soon as I pulled off track (not driving fast anymore) the oil temperature started to increase and that's when I turned on the fans, while I was doing a casual drive around the pits for a cool down. Based on this I an sure the ducts are providing plenty of air as long as the speed is fairly high (50 mph?). Running the fans afterwards kept the temperature around 185. I have a temperature gauge on the oil out of and in to the trans so I can see what the heat exchanger is doing.
I also wired up a time delay so I can leave the trans pump and fans running after I shut the car off to further cool the trans. The timer shuts the system off after 20 minutes.
Although I would prefer a GT2 type built-in trans pump and cooler that was not in the budget. I am really happy with how this turned out!
You pay for one rebuild... you'll do anything you can to prevent another!!
#12

I had the gearbox rebuilt at California Motorsport. I had the 996 Cup oil spray tube added internally, it looks like this.

The 6AN fitting to supply the 6Cup tube is welded to the gearbox next to the cardan shaft drive. In an actual Cup/GT2/GT3 gearbox the fitting is on the side of the gearbox.

The 6AN fitting to supply the 6Cup tube is welded to the gearbox next to the cardan shaft drive. In an actual Cup/GT2/GT3 gearbox the fitting is on the side of the gearbox.

The following users liked this post:
paopao (08-03-2022)
#14

I finally installed a MUCH BIGGER transmission oil cooler. I was not overly thrilled about running lines to the front of the car, so I decided to put the heat exchanger where the front diff used to be. I used a Deraile 51678 heat exchanger which is about the biggest that will fit in the available space. I wanted a Mocal unit that the Deraile copied, I could not get the Mocal in time. The Mocal is a far better heat exchanger, the Deraile unit is pop riveted together, so I'll replace it with a Mocal when I can.
I installed the heat exchanger by making up some brackets that bolt to the front diagonal braces and to the front subframe where the front diff attaches. It is a tight fit. I used 120 degree 8AN fitting on the heat exchanger to angle the hoses down the tunnel. I also installed two 4" moped radiator fans on the back side of the heat exchanger.

This picture is looking in from the driver's side where the driveshaft used to be.

I ran a pair of 8AN lines through the tunnel, and added a pair of dry break fittings at the transmission end so I can remove the transmission (or the heat exchanger) without making a huge mess. The dry break fittings are protected behind the black stamped steel transmission mount extension. I did make brackets for these fittings so they aren't banging around. The stray electrical connector is for the oil temperature into the transmission.

The plumbing on the transmission is much simpler, as I no longer have the woefully inadequate heat exchanger there. I ran the pump output line and the return to the transmission up over the curved transmission support to keep them away from the cardan shaft drive. Having the hoses run like this is important as it creates a point where the hoses are higher than the oil level in the gearbox. If this is not done there is a possibility of all the oil in the cooler running back into the gearbox, which would raise the level much higher than is desirable.
A couple brackets keep the suction line away from the left side driveshaft. The suction is plumbed into the gearbox under the limited slip diff and should be pulling the hottest oil.

I mounted the heat exchanger so that it receives airflow from the naca ducts on the undertray. I had to cut the small outer naca ducts more than I anticipated.

So, how did all this work?
Last time out with the tiny side-mounted heat exchanger I saw trans oil temps of 245F after 3 sessions of 20 minutes. The oil temp increased after each session, something like 220F then 230F then 245F. To compare temperatures, highway driving gives about 180F for gearbox temperature.
With the new cooler setup the highest temp I saw for oil into the gearbox was 185F. This was after the fifth 20 minute session on one of the hottest days of the year. I did not use the heat exchanger fans while on track, it was not necessary as the naca ducts seem to give plenty of airflow.
As soon as I pulled off track (not driving fast anymore) the oil temperature started to increase and that's when I turned on the fans, while I was doing a casual drive around the pits for a cool down. Based on this I an sure the ducts are providing plenty of air as long as the speed is fairly high (50 mph?). Running the fans afterwards kept the temperature around 185. I have a temperature gauge on the oil out of and in to the trans so I can see what the heat exchanger is doing.
I also wired up a time delay so I can leave the trans pump and fans running after I shut the car off to further cool the trans. The timer shuts the system off after 20 minutes.
Although I would prefer a GT2 type built-in trans pump and cooler that was not in the budget. I am really happy with how this turned out!
I installed the heat exchanger by making up some brackets that bolt to the front diagonal braces and to the front subframe where the front diff attaches. It is a tight fit. I used 120 degree 8AN fitting on the heat exchanger to angle the hoses down the tunnel. I also installed two 4" moped radiator fans on the back side of the heat exchanger.

This picture is looking in from the driver's side where the driveshaft used to be.

I ran a pair of 8AN lines through the tunnel, and added a pair of dry break fittings at the transmission end so I can remove the transmission (or the heat exchanger) without making a huge mess. The dry break fittings are protected behind the black stamped steel transmission mount extension. I did make brackets for these fittings so they aren't banging around. The stray electrical connector is for the oil temperature into the transmission.

The plumbing on the transmission is much simpler, as I no longer have the woefully inadequate heat exchanger there. I ran the pump output line and the return to the transmission up over the curved transmission support to keep them away from the cardan shaft drive. Having the hoses run like this is important as it creates a point where the hoses are higher than the oil level in the gearbox. If this is not done there is a possibility of all the oil in the cooler running back into the gearbox, which would raise the level much higher than is desirable.
A couple brackets keep the suction line away from the left side driveshaft. The suction is plumbed into the gearbox under the limited slip diff and should be pulling the hottest oil.

I mounted the heat exchanger so that it receives airflow from the naca ducts on the undertray. I had to cut the small outer naca ducts more than I anticipated.

So, how did all this work?
Last time out with the tiny side-mounted heat exchanger I saw trans oil temps of 245F after 3 sessions of 20 minutes. The oil temp increased after each session, something like 220F then 230F then 245F. To compare temperatures, highway driving gives about 180F for gearbox temperature.
With the new cooler setup the highest temp I saw for oil into the gearbox was 185F. This was after the fifth 20 minute session on one of the hottest days of the year. I did not use the heat exchanger fans while on track, it was not necessary as the naca ducts seem to give plenty of airflow.
As soon as I pulled off track (not driving fast anymore) the oil temperature started to increase and that's when I turned on the fans, while I was doing a casual drive around the pits for a cool down. Based on this I an sure the ducts are providing plenty of air as long as the speed is fairly high (50 mph?). Running the fans afterwards kept the temperature around 185. I have a temperature gauge on the oil out of and in to the trans so I can see what the heat exchanger is doing.
I also wired up a time delay so I can leave the trans pump and fans running after I shut the car off to further cool the trans. The timer shuts the system off after 20 minutes.
Although I would prefer a GT2 type built-in trans pump and cooler that was not in the budget. I am really happy with how this turned out!
Anyway, very nice set up you crafted. It's nice to see clever engineering. Congrats.
#15

Thanks for sharing that @theprf; unfortunately don't think this is one I can DIY in my garage.
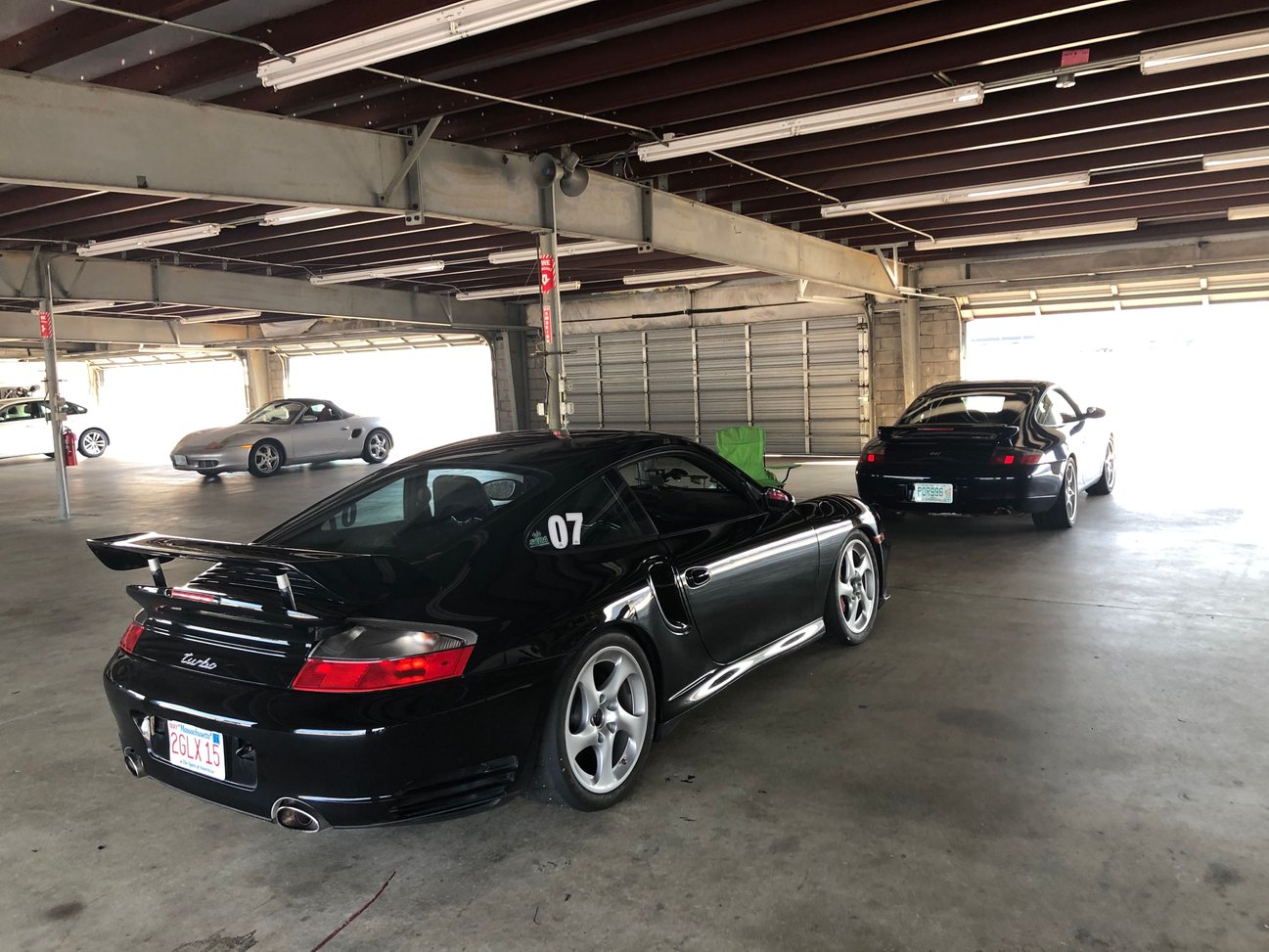
The hottest trans temp I saw was 190F after 20 minutes. Oil went to 241F, water to 190-ish. I didn't have my OBD datalogger because my in-dash oil temp gauge decided not to work which left me relying on the Cobb Accessport to display oil temp. Since the Cobb uses the OBD2 port I can't plug in the datalogger. Note to self, fix the oil temperature gauge!
The following 2 users liked this post by theprf:
17ram2500 (08-07-2022),
TheDeckMan (08-06-2022)