Lobster bends
#18
Three Wheelin'
Join Date: Jul 2002
Location: Connersville IN
Posts: 1,807
Likes: 0
Received 0 Likes
on
0 Posts

I sold a intake pipe for a K-27 on here years ago that I pie cut like that. I love TIG welding but not enough for that! BTW I run a 330A miller tig, it's huge and a bit old but steady as a rock and the torch stays cool!
#20
Professional Hoon
Rennlist Member
Rennlist Member
Thread Starter
Join Date: Jan 2010
Location: Melbourne, Australia
Posts: 7,090
Likes: 0
Received 4 Likes
on
4 Posts

Still pretty 
Thanks, I'm sure you could go to a proper fab shop and get them to make you one?
Cheers mate, Appreciate it
. Just practice on off cuts. These days you can find small TIGS (probably pricey) that are small that do aluminium with pulse.
Remember you need Pure Argon to TIG weld Stainless Steel and Aluminium
People where doing it before the trend came along haha! Im running a Lincoln Electric precision 375. Tip stays cool also!
I have a small TIG and it's the worst when the tip gets hot. You feel it though thte gloves and it gets uncomfortable.
You have to! time consuming though. Good luck with the Apprenticeship


Remember you need Pure Argon to TIG weld Stainless Steel and Aluminium
I have a small TIG and it's the worst when the tip gets hot. You feel it though thte gloves and it gets uncomfortable.
You have to! time consuming though. Good luck with the Apprenticeship
#22
Addict
Rennlist Member
Rennlist Member

When you do a thru weld with tig, you need to back purge the backside of the weld. In this case it would be the id. Tape over the ends of the pipe .put a small hose of argon in the lowest point and punch a hole in the highest point on the other end. Argon will fill the pipe and displace the air. The vent hole should be big enough so that you get flow thru the pipe and NOT pressurize the pipe. You'll get a very clean id this way. Have fun.Tig is like art.
#23
Nordschleife Master

When you do a thru weld with tig, you need to back purge the backside of the weld. In this case it would be the id. Tape over the ends of the pipe .put a small hose of argon in the lowest point and punch a hole in the highest point on the other end. Argon will fill the pipe and displace the air. The vent hole should be big enough so that you get flow thru the pipe and NOT pressurize the pipe. You'll get a very clean id this way. Have fun.Tig is like art.
#25
Drifting
Join Date: Aug 2009
Location: Bangkok, Thailand, Milpitas, CA & Weeki Wachee, FL
Posts: 2,239
Likes: 0
Received 2 Likes
on
1 Post

Paul:
I am going to try to post a link via the phone, hope it works. This is the welder we use at work. I know it takes the fun and art out of it, but if you are **** like me, you will love these welds. Video is using 1/4" tubing, but we have chucks good for up to 4" 304 SS tubing. Seams are perfect every time. I have never looked for a price used, but this would be handy if you were in the business.
http://m.youtube.com/#/watch?v=xdeN1jtgHr8&desktop_uri=%2Fwatch%3Fv%3DxdeN1jtgHr8
I am going to try to post a link via the phone, hope it works. This is the welder we use at work. I know it takes the fun and art out of it, but if you are **** like me, you will love these welds. Video is using 1/4" tubing, but we have chucks good for up to 4" 304 SS tubing. Seams are perfect every time. I have never looked for a price used, but this would be handy if you were in the business.
http://m.youtube.com/#/watch?v=xdeN1jtgHr8&desktop_uri=%2Fwatch%3Fv%3DxdeN1jtgHr8
#27
Professional Hoon
Rennlist Member
Rennlist Member
Thread Starter
Join Date: Jan 2010
Location: Melbourne, Australia
Posts: 7,090
Likes: 0
Received 4 Likes
on
4 Posts

Eric,
Pretty neat machine i have to say. Useless for me as we don't really do much with pipes. And they're usually all funny sizes if we do.
I have a picture a friend took of some lobster pipes. The welds are so straight it looks like a machine did it.
Pretty neat machine i have to say. Useless for me as we don't really do much with pipes. And they're usually all funny sizes if we do.
I have a picture a friend took of some lobster pipes. The welds are so straight it looks like a machine did it.
#28

You should definately back purge with argon if it's pre-turbo. You don't want something breaking loose from high heat and going into the turbo 
Here is my crossover pipe

Here is my crossover pipe

#29
Professional Hoon
Rennlist Member
Rennlist Member
Thread Starter
Join Date: Jan 2010
Location: Melbourne, Australia
Posts: 7,090
Likes: 0
Received 4 Likes
on
4 Posts

Got any inside images?
#30
Professional Hoon
Rennlist Member
Rennlist Member
Thread Starter
Join Date: Jan 2010
Location: Melbourne, Australia
Posts: 7,090
Likes: 0
Received 4 Likes
on
4 Posts

I did another piece today in some free time after work.
I took step by step pictures so you can see the effort put into it.
I set up my bandsaw a ~6 degree and rotate the tube 180 degree each cut to get the angle i want.
This is what it looks like after it's cut
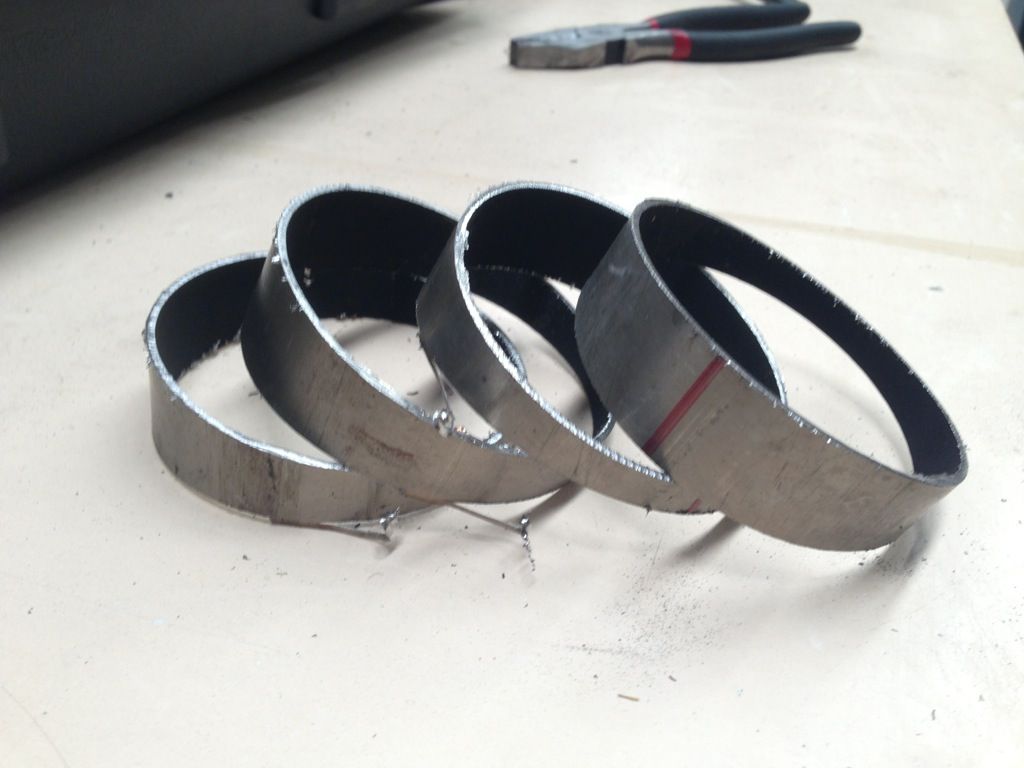
Cleaned up the edges with a bench grinder and washed it in thinners (or a dirt and grease remover)
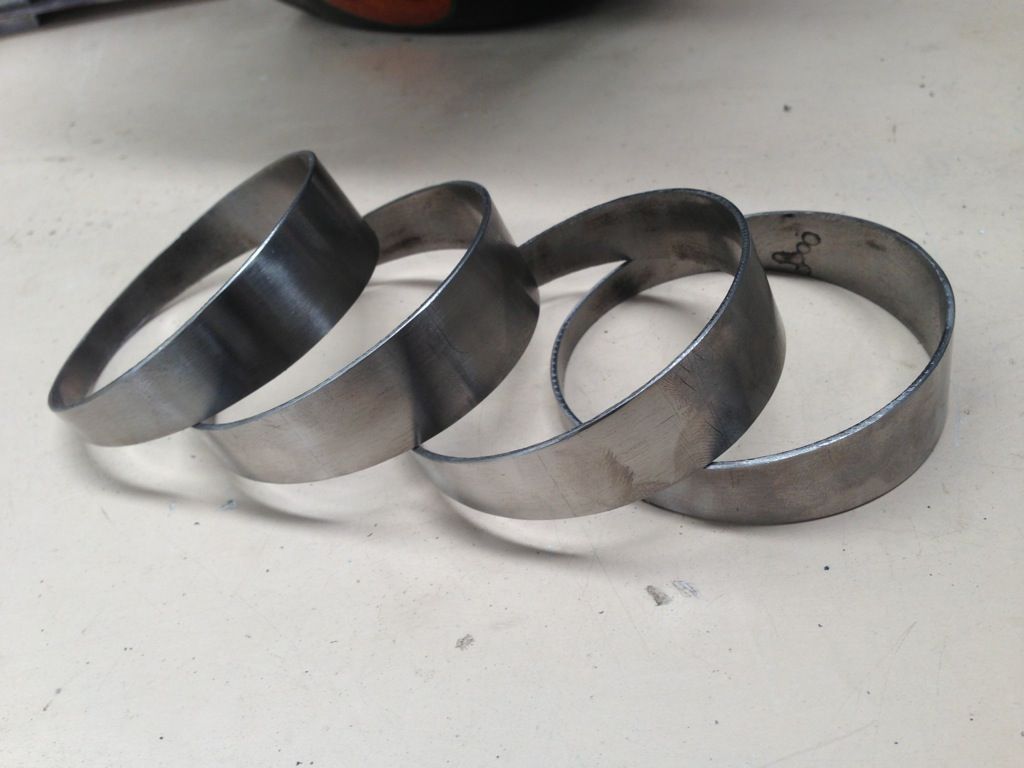
Clamped them together with a vice and vice grips
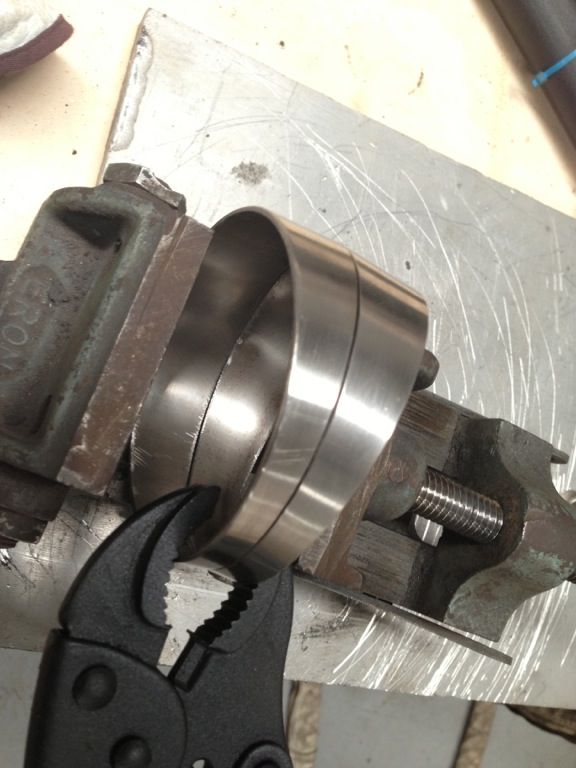
Tacked them into place (i tired to tack them all together first. probably better off tacking one and welding it one by one)
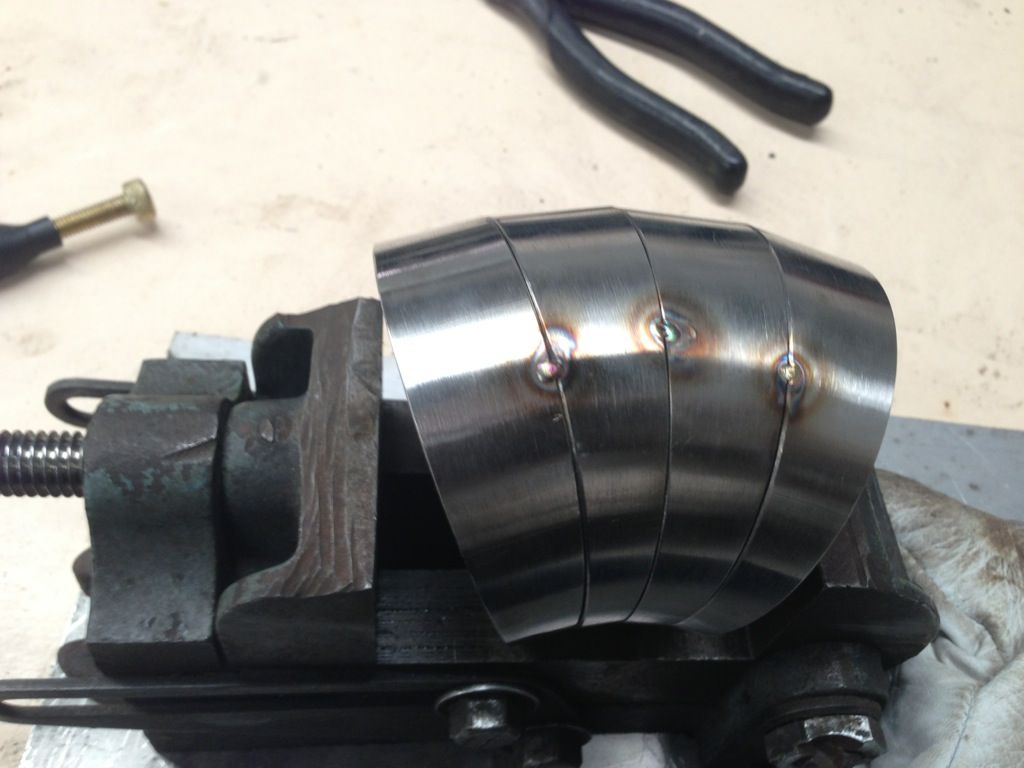
Finished (you can see on the left middle run, that it's larger. That is because it had a small gap so i needed to use filler wire)
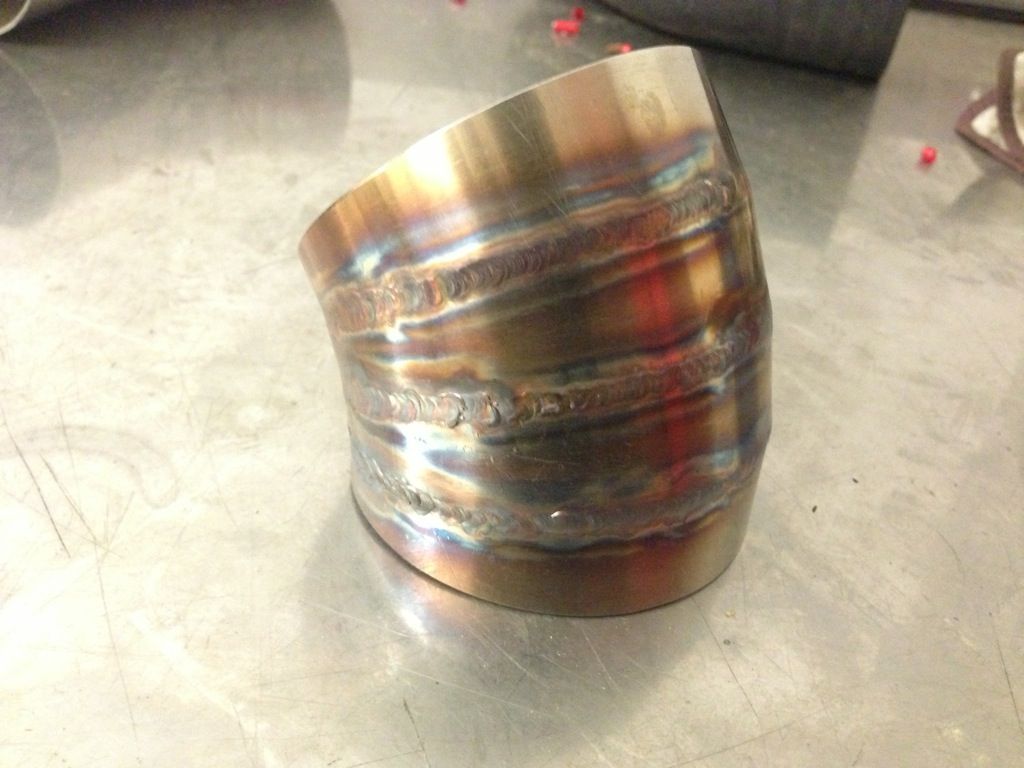
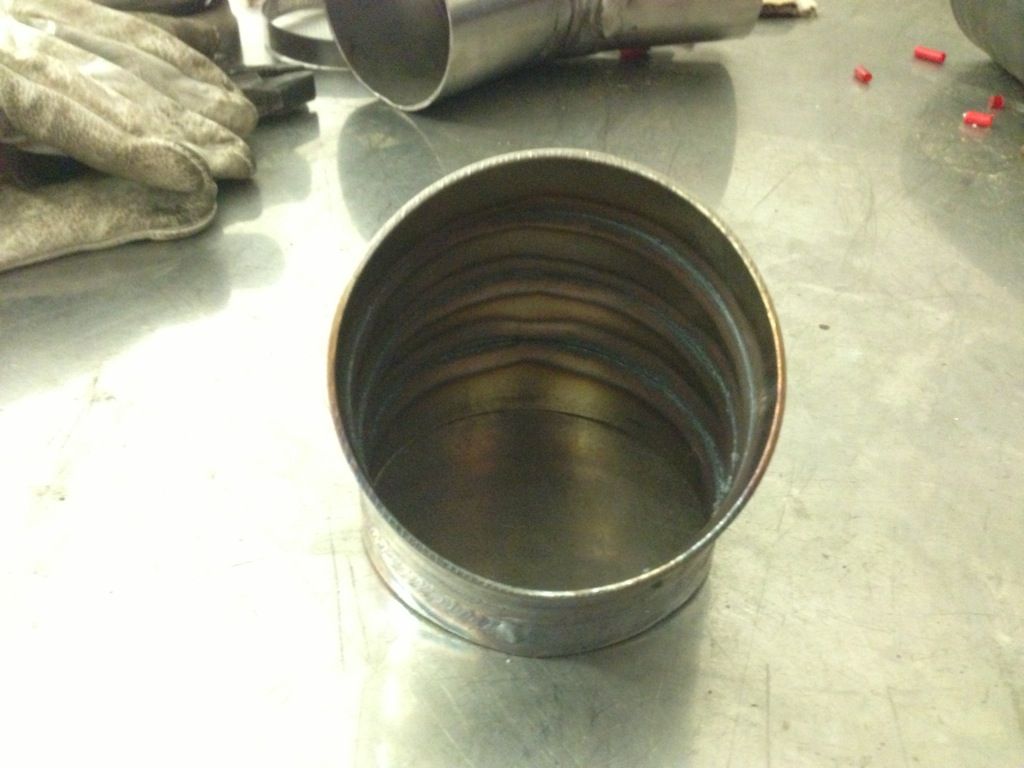
I took step by step pictures so you can see the effort put into it.
I set up my bandsaw a ~6 degree and rotate the tube 180 degree each cut to get the angle i want.
This is what it looks like after it's cut
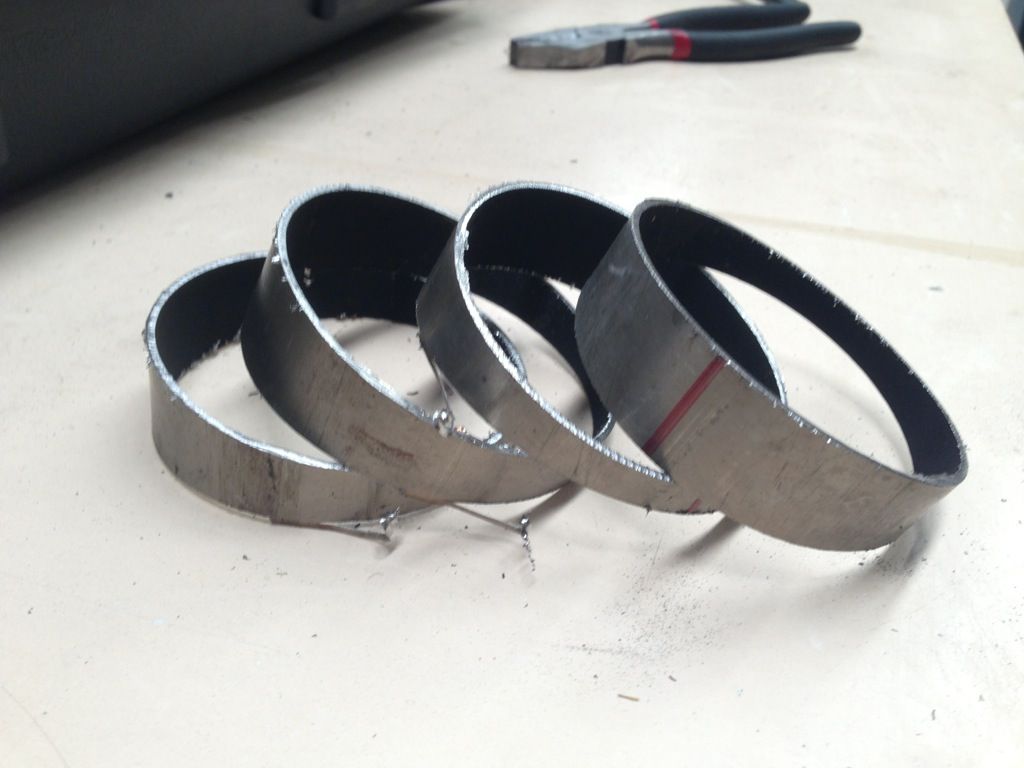
Cleaned up the edges with a bench grinder and washed it in thinners (or a dirt and grease remover)
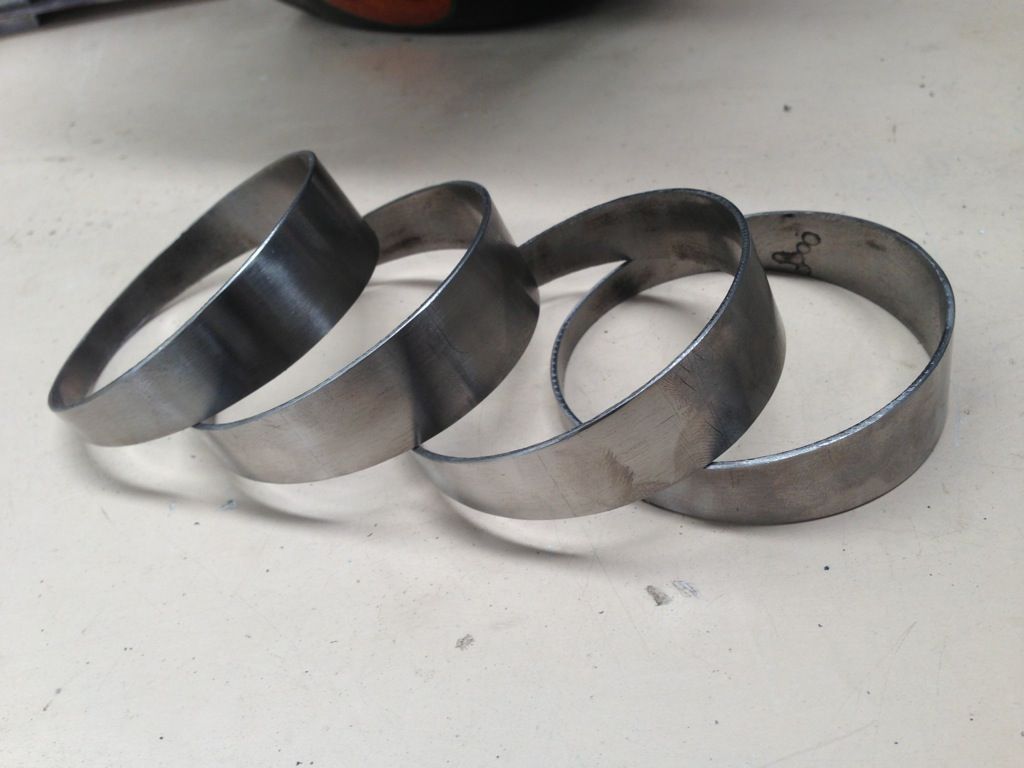
Clamped them together with a vice and vice grips
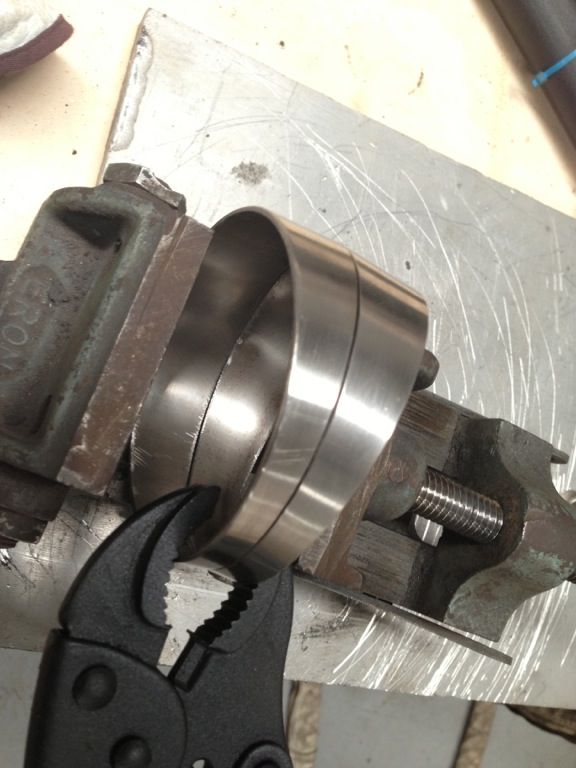
Tacked them into place (i tired to tack them all together first. probably better off tacking one and welding it one by one)
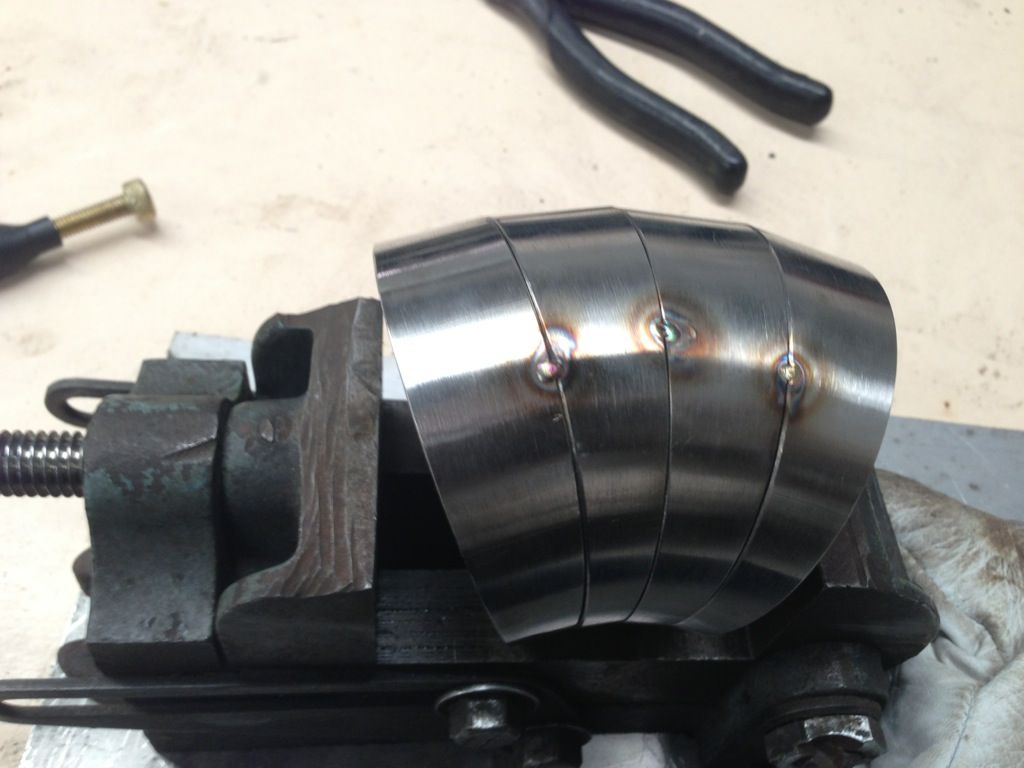
Finished (you can see on the left middle run, that it's larger. That is because it had a small gap so i needed to use filler wire)
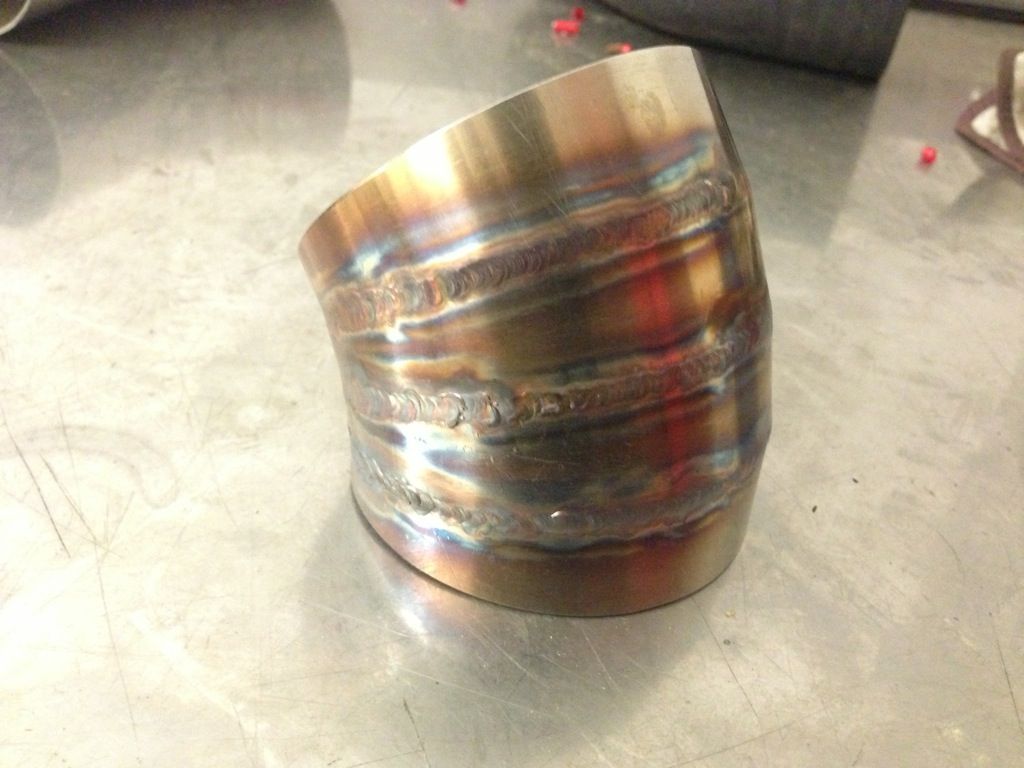
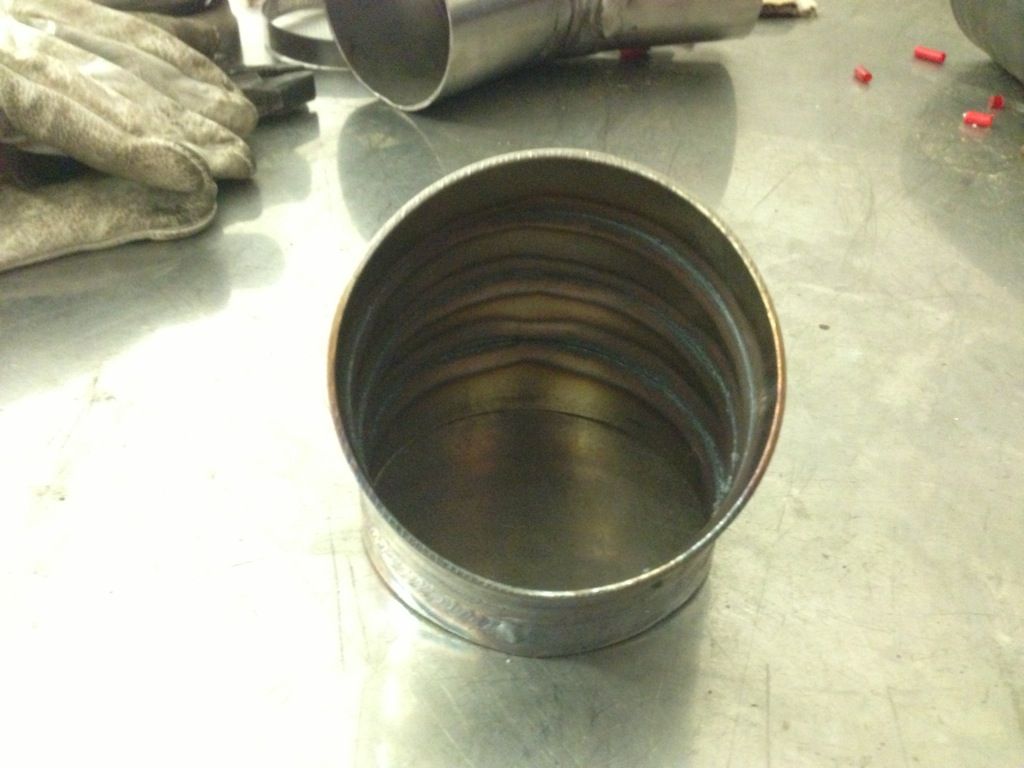
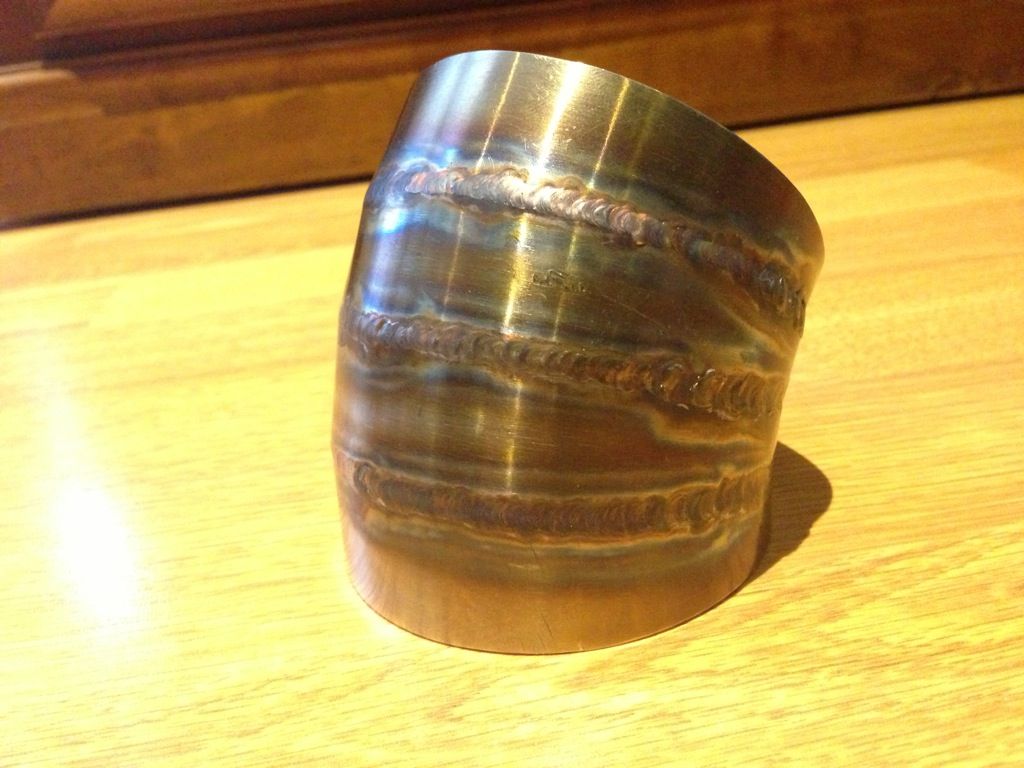