'87 S4 Timing Death
#226
Inventor
Rennlist Member
Rennlist Member

You should know this, correct? I hope you are not just hoping the stock system will work with the additional belt generated by radical cams or running at higher than stock rpm?
#227
Former Sponsor

Relative to the roller/rollers or lack of under the crank gear.
Most early cars had a plastic guide which in the majority of cases has crumbled and disappeared. Not to be replaced because it has been NLA for many years.
From 83 to 87 and 90 to 95 a single roller was used.
In 88 and 89 a double roller was used.
What was the theory behind the single to double and back to single?
Most early cars had a plastic guide which in the majority of cases has crumbled and disappeared. Not to be replaced because it has been NLA for many years.
From 83 to 87 and 90 to 95 a single roller was used.
In 88 and 89 a double roller was used.
What was the theory behind the single to double and back to single?
Porsche was trying to control the "slack" on the belt on the oil pump side of the engine by running a second roller very close to the belt.
(Note that this would obviously have have helped keep the belt from jumping on the crank drive gear, like what I'm assuming happened to the OP.)
The problem with this is that the "second roller" ended up rubbing on the belt way more than they anticipated...and that second roller sometimes made lots of objectionable noise.....even given the tension on the belt with the stock tensioner.
Ken found this out. The fact that his tensioner runs the belt much looser translates into any roller making noise.
His solution....simply remove the roller/rollers completely.
And that's why he is never going to tell anyone to add the roller back in....he knows that it (the single roller) is going to spin like crazy and make noise/burn up.
#228
Inventor
Rennlist Member
Rennlist Member

Porsche was trying to control the "slack" on the belt on the oil pump side of the engine by running a second roller very close to the belt.
The problem with this is that the "second roller" ended up rubbing on the belt way more than they anticipated...and that second roller sometimes made lots of objectionable noise.....even given the tension on the belt with the stock tensioner.
The problem with this is that the "second roller" ended up rubbing on the belt way more than they anticipated...and that second roller sometimes made lots of objectionable noise.....even given the tension on the belt with the stock tensioner.
People pay you money for advice? Amazing.
Um, no.

Contrast this with the stock pre-tensioner system which substantially runs on wishful thinking.
#229
Rennlist Member

I don't recall (maybe I missed it) Ken's instructions recommending removal of the roller(s). I remember lots of folks, including Ken, suggesting that they could be left off. Others said there's no good reason to leave it off, which made sense, so I put it back on, but no one that I recall said it SHOULD be left off.
#231
Chronic Tool Dropper
Lifetime Rennlist
Member
Lifetime Rennlist
Member

Ken, thanks for the link to the Gates info page.
The bearings in the factory lower rollers are tiny, resulting in a very high bearing speed relative to crankshaft speed when there is contact. The ones I've replaced on my car have been worn-noisy, even though they fit up with clearance when first installed. They should only be spinning when the belt "grows" around the crank gear, so my worn/noisy bearings are a clue that there is growth there under certain circumstances.
Before reading this last volley of posts this morning, I was (weakly) brainstorming what it would take to use either larger bearings, or a plastic belt guide that would wrap around the belt on the crank gear.
Adding larger bearings underneath where the factory console sits is not an easy option. The pins that the little console slides on are in the way. The install method would need to be console/mounting bracket first, secure, then the bearings/rollers would go on. I'd find a larger diameter and wider bearing so it wouldn't need the roller cover. I only have one engine block to experiment on, and it's in-service right now.
The next option, which I think Roger mentioned, might be a plastic guide "shoe" that would sit clear of the belt by a few thousandths with the belt fit at normal tension. The leading edge of that would need careful attention, as it's where any slack would cause first contact between belt and the plastic guide. It would also need to consider the "normal" dynamics (read: flapping) that can happen in that section, so the back of the belt could survive contact with no cutting.
Looks a lot like a 3D printer project, in HDPE.
Note that the engine layout with the oil pump drive relatively close to the crank undoubtedly gained consideration for belt management; the short span there would likely give higher frequency but lower amplitude vibrations with the same excitation. Higher frequency means more wear with the same amplitude, vs higher amplitude which risks instant fail if the amplitude/displacement exceeds any large fraction of the tooth depth.
The bearings in the factory lower rollers are tiny, resulting in a very high bearing speed relative to crankshaft speed when there is contact. The ones I've replaced on my car have been worn-noisy, even though they fit up with clearance when first installed. They should only be spinning when the belt "grows" around the crank gear, so my worn/noisy bearings are a clue that there is growth there under certain circumstances.
Before reading this last volley of posts this morning, I was (weakly) brainstorming what it would take to use either larger bearings, or a plastic belt guide that would wrap around the belt on the crank gear.
Adding larger bearings underneath where the factory console sits is not an easy option. The pins that the little console slides on are in the way. The install method would need to be console/mounting bracket first, secure, then the bearings/rollers would go on. I'd find a larger diameter and wider bearing so it wouldn't need the roller cover. I only have one engine block to experiment on, and it's in-service right now.
The next option, which I think Roger mentioned, might be a plastic guide "shoe" that would sit clear of the belt by a few thousandths with the belt fit at normal tension. The leading edge of that would need careful attention, as it's where any slack would cause first contact between belt and the plastic guide. It would also need to consider the "normal" dynamics (read: flapping) that can happen in that section, so the back of the belt could survive contact with no cutting.
Looks a lot like a 3D printer project, in HDPE.
Note that the engine layout with the oil pump drive relatively close to the crank undoubtedly gained consideration for belt management; the short span there would likely give higher frequency but lower amplitude vibrations with the same excitation. Higher frequency means more wear with the same amplitude, vs higher amplitude which risks instant fail if the amplitude/displacement exceeds any large fraction of the tooth depth.
#232
Basic Sponsor
Rennlist
Site Sponsor
Rennlist
Site Sponsor

The rollers are available new in single and double versions - About $250 each.
I also carry the bearings for a lot less money.
I also carry the bearings for a lot less money.
__________________

Does it have the "Do It Yourself" manual transmission, or the superior "Fully Equipped by Porsche" Automatic Transmission?
George Layton March 2014
928 Owners are ".....a secret sect of quietly assured Porsche pragmatists who in near anonymity appreciate the prodigious, easy going prowess of the 928."

Does it have the "Do It Yourself" manual transmission, or the superior "Fully Equipped by Porsche" Automatic Transmission?

928 Owners are ".....a secret sect of quietly assured Porsche pragmatists who in near anonymity appreciate the prodigious, easy going prowess of the 928."

#233

I don't recall (maybe I missed it) Ken's instructions recommending removal of the roller(s). I remember lots of folks, including Ken, suggesting that they could be left off. Others said there's no good reason to leave it off, which made sense, so I put it back on, but no one that I recall said it SHOULD be left off.
But the thing we all need to know is if we install a PKensioner, will our engines get that same, nice shiny "new" look? Unlike that old, crusty " before" look ??
My engine wants one real bad but I think it first needs to get over some self esteem issues.
#234
Inventor
Rennlist Member
Rennlist Member

They should only be spinning when the belt "grows" around the crank gear, so my worn/noisy bearings are a clue that there is growth there under certain circumstances.
The next option, which I think Roger mentioned, might be a plastic guide "shoe" that would sit clear of the belt by a few thousandths with the belt fit at normal tension. The leading edge of that would need careful attention, as it's where any slack would cause first contact between belt and the plastic guide.
Looks a lot like a 3D printer project, in HDPE.
The next option, which I think Roger mentioned, might be a plastic guide "shoe" that would sit clear of the belt by a few thousandths with the belt fit at normal tension. The leading edge of that would need careful attention, as it's where any slack would cause first contact between belt and the plastic guide.
Looks a lot like a 3D printer project, in HDPE.
Since the belt should never touch the slide (or rollers) with a PKT perhaps a micro-switch or something as basic as a delicate wire could be put on the slider as a tension warning.
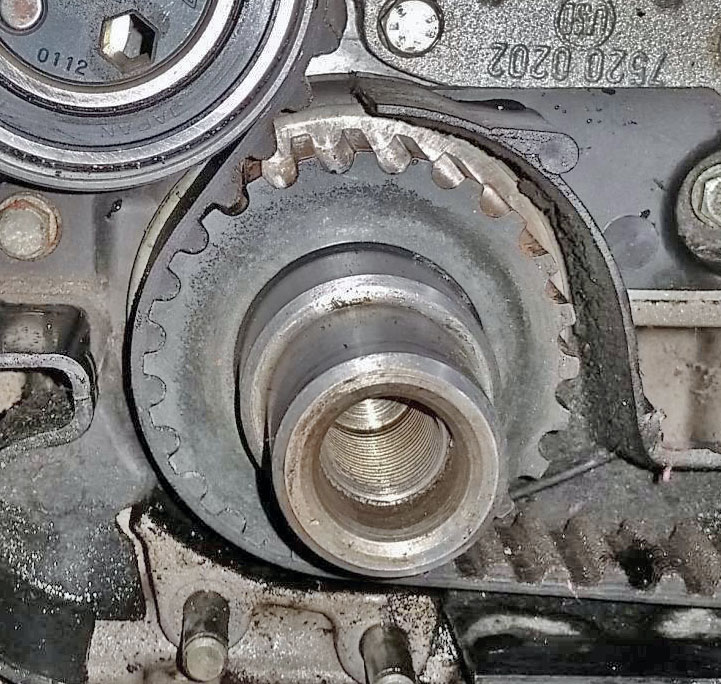
#235
Captain Obvious
Super User
Super User

Ectually, I'm the perfect case study. I bought a S4 with a good belt, in proper tension with a stock tensioner. I had a bearing failure at high speed on a water pump which cocked the pump shaft up about 12deg and was able to identify the problem by the warning light, note the temp start to rise, then shut the engine down and coast to a stop without catastrophic engine damage. New WP, new belt, new tension roller and I was back on the road in a few days.

#236
Captain Obvious
Super User
Super User

Spring. More info - http://members.rennlist.com/porken/G...tensioners.pdf
If... the belt is pre-stretched properly and all of the comparatively crude and lightweight components are in good condition. And the water pump doesn't wear out, etc.
It may have helped this time, but not another? It is the tensioner/damper's job to keep the belt on the crank gear. It can't do that if it is out of range.
This failure, to me, is akin to running the factory tensioner with the belt loose. The lower roller(s) are a vestigal band-aid from an unmanaged system, but it does not hurt to keep them. I personally won't be reinstalling them.
If... the belt is pre-stretched properly and all of the comparatively crude and lightweight components are in good condition. And the water pump doesn't wear out, etc.
It may have helped this time, but not another? It is the tensioner/damper's job to keep the belt on the crank gear. It can't do that if it is out of range.
This failure, to me, is akin to running the factory tensioner with the belt loose. The lower roller(s) are a vestigal band-aid from an unmanaged system, but it does not hurt to keep them. I personally won't be reinstalling them.
You keep using words like belt management and inadequate as a campaign slogan to push your product. The OE setup manages the belt as intended and does the job that is designed for. What inadequate really is, is the deletion of the belt warning system with your product. If there was one, the PO would have known the belt was loose. But since this system was completely eliminated, here we are today.....
The fact the Audi tensioner was at full extent and cause the belt to slip, makes your design a faliure. Perhaps a different tensioner with a longer stroke would be in order. And/or one that puts a bit more force on the belt so under NO CIRCUMSTANCES can it be pulled off by hand. Maybe a limit switch that triggers the light when the tensioner can not go any further.....and so on. BUT instead, just created a hype when the "black" version was released (many thought it will have a warning system) but all it did was include stronger bolts.
#237
Rennlist Member

Did we decide his problem was not at startup? As far as I know we have no evidence that there was anything wrong (other than possible belt wear issues) prior to the failure on startup. The stock tension warning system doesn't do anything for several minutes after start-up.
The factory system would have triggered the belt warning light and gave a fighting chance for the PO to react.
You keep using words like belt management and inadequate as a campaign slogan to push your product. The OE setup manages the belt as intended and does the job that is designed for. What inadequate really is, is the deletion of the belt warning system with your product. If there was one, the PO would have known the belt was loose. But since this system was completely eliminated, here we are today.....
The fact the Audi tensioner was at full extent and cause the belt to slip, makes your design a faliure. Perhaps a different tensioner with a longer stroke would be in order. And/or one that puts a bit more force on the belt so under NO CIRCUMSTANCES can it be pulled off by hand. Maybe a limit switch that triggers the light when the tensioner can not go any further.....and so on. BUT instead, just created a hype when the "black" version was released (many thought it will have a warning system) but all it did was include stronger bolts.
You keep using words like belt management and inadequate as a campaign slogan to push your product. The OE setup manages the belt as intended and does the job that is designed for. What inadequate really is, is the deletion of the belt warning system with your product. If there was one, the PO would have known the belt was loose. But since this system was completely eliminated, here we are today.....
The fact the Audi tensioner was at full extent and cause the belt to slip, makes your design a faliure. Perhaps a different tensioner with a longer stroke would be in order. And/or one that puts a bit more force on the belt so under NO CIRCUMSTANCES can it be pulled off by hand. Maybe a limit switch that triggers the light when the tensioner can not go any further.....and so on. BUT instead, just created a hype when the "black" version was released (many thought it will have a warning system) but all it did was include stronger bolts.
#238
Captain Obvious
Super User
Super User

Did we decide his problem was not at startup? As far as I know we have no evidence that there was anything wrong (other than possible belt wear issues) prior to the failure on startup. The stock tension warning system doesn't do anything for several minutes after start-up.
#239
Rennlist Member
#240
Former Sponsor

The stock tensioner isn't going to fail....unless it falls off the front of the engine.
You keep (conveniently) skipping over this point.
You can rationalize what you built all you want...how you think it works better as the engine warms up. How you think it better controls the belt.
But the reality is that the OP wouldn't have a pile of scrap metal if he had installed the original tensioner.