Hi Performance Bearings for the 928
#1
Addict
Rennlist Member
Rennlist Member
Thread Starter

Previously I posted about these bearings as a upgrade to the Porsche 928 OEM design bearings. There was lots to like but I had some concerns and they were not the most optimal they could be. That is because they were not around the 140 degree amount of grooving that is seen as optimal at least in most hi performance engines where they are chasing every HP. Obviously this type of grooving requires some highly skilled machining.
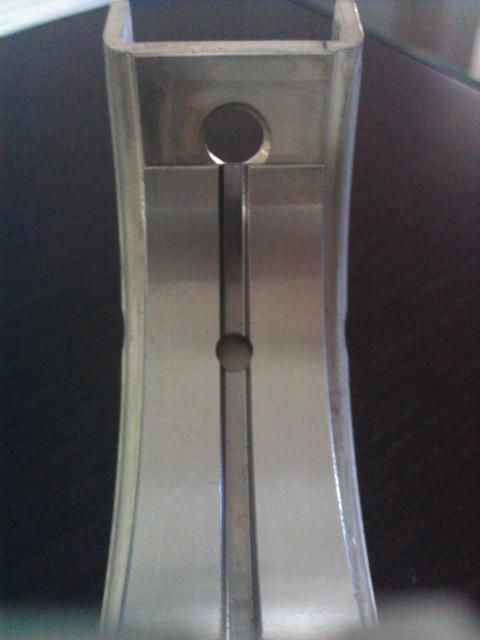
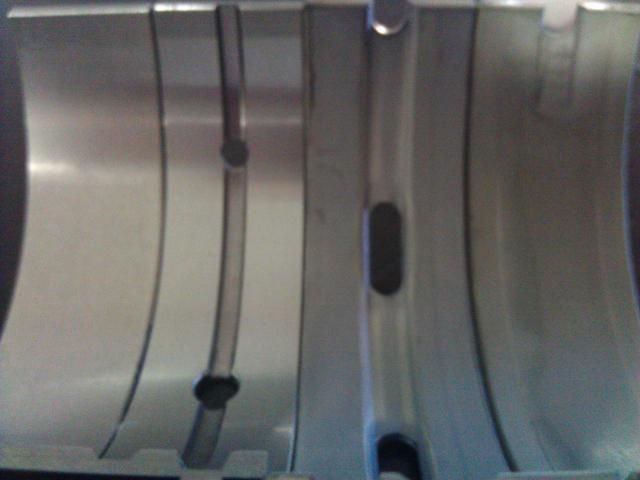
Below is some Nascar bearings, some have more grooving than others. These are not the most optimal as they have the retaining tabs removing surface area from the running surface.
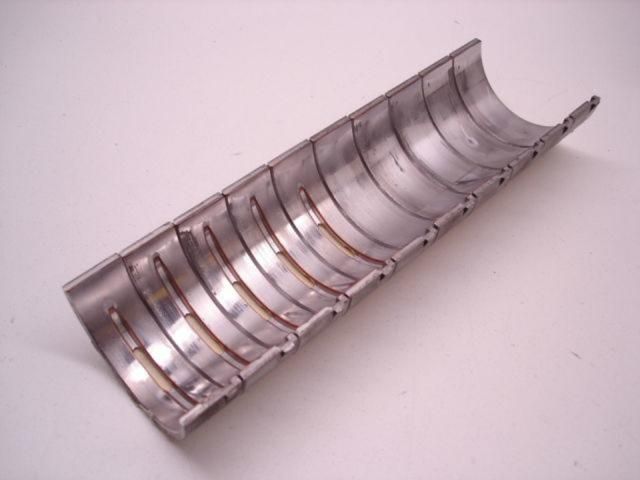
This is a stroke of luck, the new race style bearings fit neatly into the 928 bearings. You will also note that the bearing surface is not impaired by the retaining tab.

Side by side with the upper 928 bearings, note the 928 bearings don't have much use on them but look at the wear pattern. Also it should be noted that the amount of "load surface area" is probably greater on the new bearings. These bearings are very hard, they are race bearings and I was told by an engine builder that he uses them in his 1400 HP builds and they wear extremely well.

A closer look at the retaining tab area of the bearing, you can see the recess creates high pressure and wear. This equals high friction. More on that a bit later.

Here's two front nose bearings, notice how the main bearing journal must be climbing up the wall of the bearing where the grooving is.
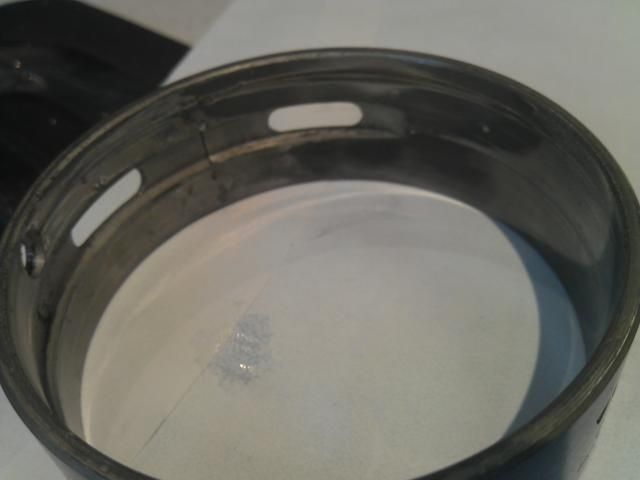
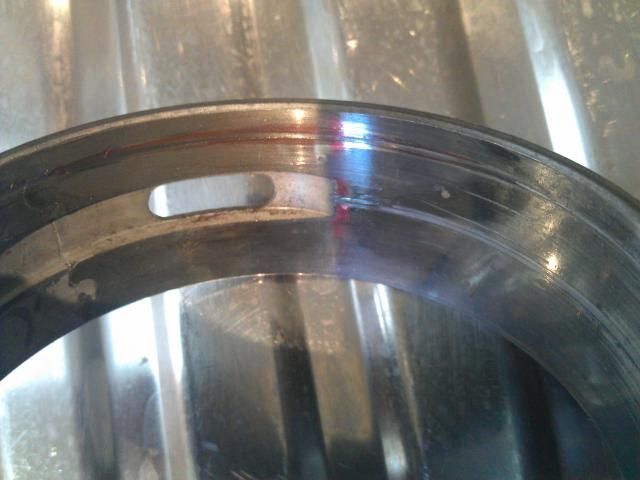
So now it becomes pretty easy to see that by having the grooving you add to wear and friction. Mahle have a very interesting graph. A 2% HP gain by having 40 degrees less grooving. A massive 15% over 360 degree grooved bearings. Now that seems a lot and it isn't my claim but Mahle's.
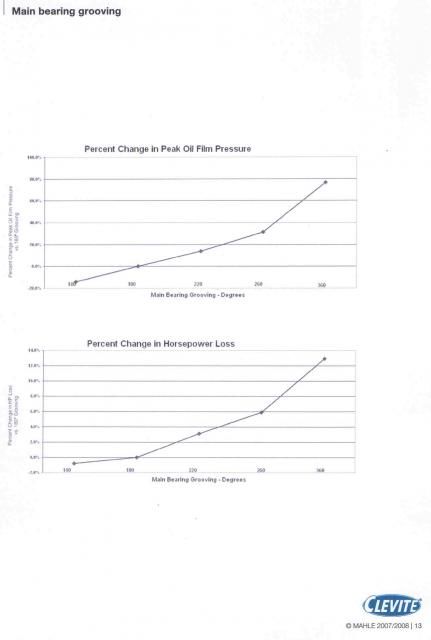
The grooving is much wider in this bearing candidate than my first try, it is approx 4.5 mm at the base and 5 mm at the surface of the bearing. There is obviously a small reduction of the main journal diameter, So there will be some marginal benefit with the higher revs than the factory rev limit. There is much information regarding the changes to the grooving can make. King bearings have some excellent products and most of their bearings don't have the locating tab recess in the bearings surface.

Below is a link to King Bearings It is well worth the read;
http://kingracebearings.com/wp-conte...e-bearings.pdf
Basically they ran conventional bearings vs new design bearings against each other in the same engine. Then they weighed and measured them.
The results were, ……………...Conventionall groove….Hi Performance groove
Thickness reduction in microns ..63 microns……………..41 microns……………..
Weight reduction in miii grams…29 mg………………..…….19 mg……………………
You will need the whole test procedure if you require more info which is in the link.
Also there is this video which is interesting.
I'm certainly looking forward to using these bearings, they don't have a massive range like Mahle Clevite but will suit many hi performance rods like these that I intend to use. The tighter you run your clearances, the better the standard required for all the parts. The machining of the crank, the tolerance of the bearings. The stability of the bearing housing. You will note for the folks who haven't seen these rods, the saw tooth pattern on the bearing caps on the rod on the left. This is to stop fretting or walking which would alter tight tolerances to the point there may be a failure.
Another King Bearing video,
I have decided not to run the forced pin oiling, I am designed an advanced oil squirting system that will spray multiple jets of oil at the piston and thus also the small end. this will help as these are piston guided rods and by not having the dowel hole in the rod bearing I won't be taking any oil away from the rod bearing either. Again it goes to the same principle as the main bearing grooving.
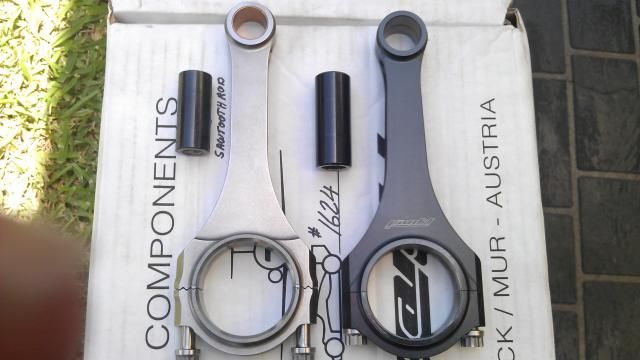
So the cost of this conversion will be under a $1000. Probably well under, I was quoted between $300 to $400 for the line bore of the Porsche bearings. I have a new Porsche thrust bearing which is required as I am using the Porsche thrust faces but not the slipper faces. There is some cost to notch the Porsche thrust bearing to accept the new bearing and there is also a cost to notch the front main bearing because it uses a one piece bearing in my block. So I suspect the actual modification cost is around $500 plus parts. The new bearings are cheaper than the Porsche 928 bearings, I guess that doesn't surprise anybody though does it. So there is some cost offset there.
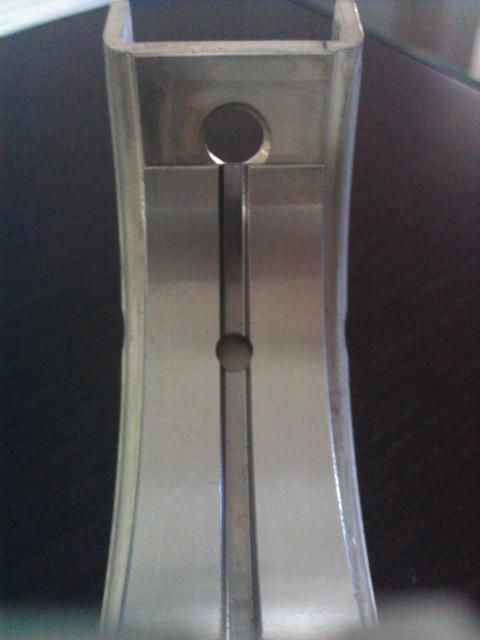
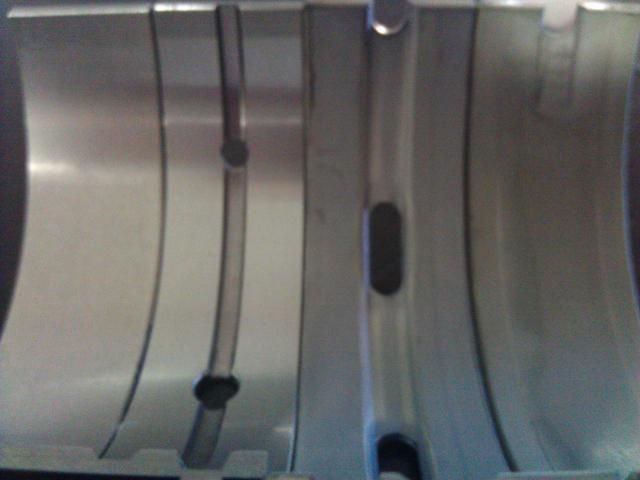
Below is some Nascar bearings, some have more grooving than others. These are not the most optimal as they have the retaining tabs removing surface area from the running surface.
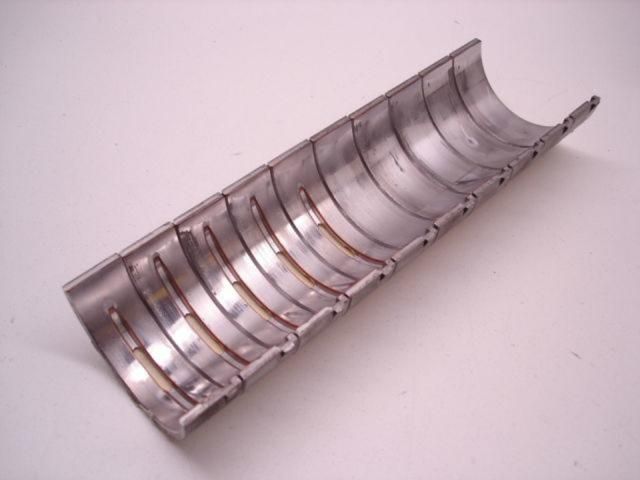
This is a stroke of luck, the new race style bearings fit neatly into the 928 bearings. You will also note that the bearing surface is not impaired by the retaining tab.

Side by side with the upper 928 bearings, note the 928 bearings don't have much use on them but look at the wear pattern. Also it should be noted that the amount of "load surface area" is probably greater on the new bearings. These bearings are very hard, they are race bearings and I was told by an engine builder that he uses them in his 1400 HP builds and they wear extremely well.

A closer look at the retaining tab area of the bearing, you can see the recess creates high pressure and wear. This equals high friction. More on that a bit later.

Here's two front nose bearings, notice how the main bearing journal must be climbing up the wall of the bearing where the grooving is.
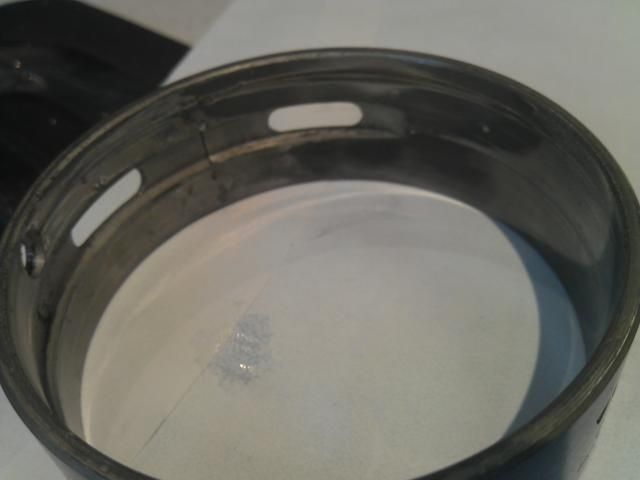
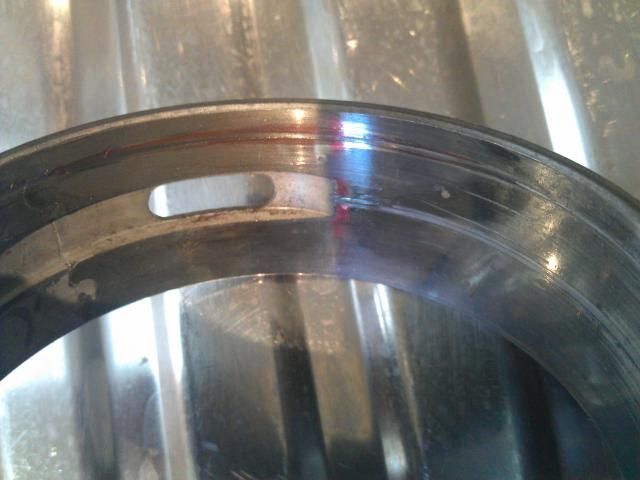
So now it becomes pretty easy to see that by having the grooving you add to wear and friction. Mahle have a very interesting graph. A 2% HP gain by having 40 degrees less grooving. A massive 15% over 360 degree grooved bearings. Now that seems a lot and it isn't my claim but Mahle's.
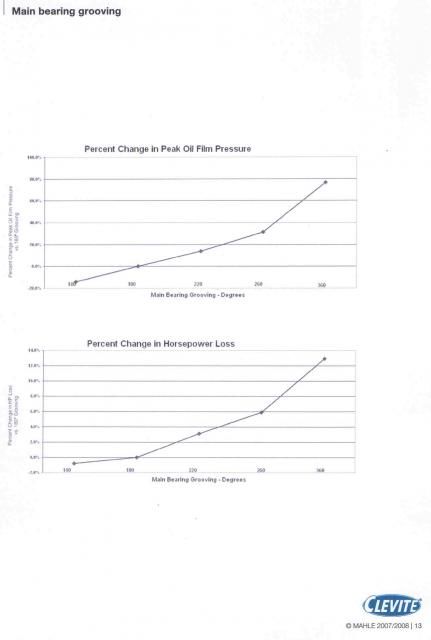
The grooving is much wider in this bearing candidate than my first try, it is approx 4.5 mm at the base and 5 mm at the surface of the bearing. There is obviously a small reduction of the main journal diameter, So there will be some marginal benefit with the higher revs than the factory rev limit. There is much information regarding the changes to the grooving can make. King bearings have some excellent products and most of their bearings don't have the locating tab recess in the bearings surface.

Below is a link to King Bearings It is well worth the read;
http://kingracebearings.com/wp-conte...e-bearings.pdf
Basically they ran conventional bearings vs new design bearings against each other in the same engine. Then they weighed and measured them.
The results were, ……………...Conventionall groove….Hi Performance groove
Thickness reduction in microns ..63 microns……………..41 microns……………..
Weight reduction in miii grams…29 mg………………..…….19 mg……………………
You will need the whole test procedure if you require more info which is in the link.
Also there is this video which is interesting.
I'm certainly looking forward to using these bearings, they don't have a massive range like Mahle Clevite but will suit many hi performance rods like these that I intend to use. The tighter you run your clearances, the better the standard required for all the parts. The machining of the crank, the tolerance of the bearings. The stability of the bearing housing. You will note for the folks who haven't seen these rods, the saw tooth pattern on the bearing caps on the rod on the left. This is to stop fretting or walking which would alter tight tolerances to the point there may be a failure.
Another King Bearing video,
I have decided not to run the forced pin oiling, I am designed an advanced oil squirting system that will spray multiple jets of oil at the piston and thus also the small end. this will help as these are piston guided rods and by not having the dowel hole in the rod bearing I won't be taking any oil away from the rod bearing either. Again it goes to the same principle as the main bearing grooving.
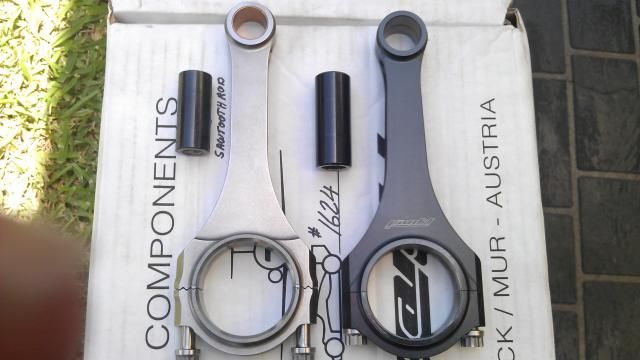
So the cost of this conversion will be under a $1000. Probably well under, I was quoted between $300 to $400 for the line bore of the Porsche bearings. I have a new Porsche thrust bearing which is required as I am using the Porsche thrust faces but not the slipper faces. There is some cost to notch the Porsche thrust bearing to accept the new bearing and there is also a cost to notch the front main bearing because it uses a one piece bearing in my block. So I suspect the actual modification cost is around $500 plus parts. The new bearings are cheaper than the Porsche 928 bearings, I guess that doesn't surprise anybody though does it. So there is some cost offset there.
#2
Nordschleife Master

Fascinating.
Can you clarify which are rod bearings and which are main? Are these available off-the-shelf and, if so, what are the part numbers?
Can you clarify which are rod bearings and which are main? Are these available off-the-shelf and, if so, what are the part numbers?
#3
Drifting

Very interesting as always but what about:
"This is a stroke of luck, the new race style bearings fit neatly into the 928 bearings."
You aren't using them this way, right?
And what Glen asked above please.
Matt
"This is a stroke of luck, the new race style bearings fit neatly into the 928 bearings."
You aren't using them this way, right?
And what Glen asked above please.
Matt
#4
Chronic Tool Dropper
Lifetime Rennlist
Member
Lifetime Rennlist
Member

For those reading along, added clarity for the HP claims-- The percentage claims are not actual percents of engine horsepower, but percentage of horsepower lost to friction. Great stuff, by the way.
#5
Addict
Rennlist Member
Rennlist Member
Thread Starter

Hello Matt and Glen,
The bearings that have grooves in them are the mains, the King rod bearings are without any grooving. I suspect King are working through their catalogs to update the spec on their parts. I recently (This year) bought rod bearing for the 928 which were from their XP race series. Now these bearings are not directly a swap in. The recess for the tab needs widening and then you would carefully line up the bearings to ensure correct fitment/alignment. Please remember for those who may not be aware, the tabs are a alignment tool not what holds the bearing, the crush holds the bearing. I may be able to post pics of the Toyota bearings in situ if I get time later in the day. As mentioned I was disappointed that these Toyota bearings did have the recess in the bearing surface. I suspect they are working through old stock.
For those who are not aware I am building 4 engines, I have standard mains in two of the engines and the strokers will have slightly reduced main journal size. For one engine I am getting custom Carrillo rods, this engine will be a "Mini Stroker" If you search my threads you will see I wanted to do something like that back in 2006 or thereabouts. Unfortunately I had a car accident which put paid to that till now. Those rods are going to be for the Honda/IRL sized bearings.
So the concept is to offset grind the factory crank (something which has been done with the 944/968 series engines) and achieve a crank rod journal size of approx 48 mm or 1.888" The rods will be conventional and crank guided. The rod housing size is an interesting one, the size I could use is 2.008" This fits bearings for both 48 mm and 47 mm journals.
This way if there is a big blow up, you can clean the crank up with a grind and go to the smaller size of 47 mm still using the same rods. The length of these bearings is 20.11 mm and 16.64 mm respectively. The part no.s (King/Clevite) for those bearings which also fit into the Pankl rods above are;
CR4033XP/CB1780H to achieve 48 mm in the smaller 2.008" housing. The bearings that achieve the 47 mm journal are only available in Clevite CB1664H. The King bearings mentioned here are what I will be using in the Pankl saw tooth rods for the 4V stroker.
If I went the larger bore route, i.e 2.015" you have the choice of bearings with a length of 21.36 mm which is Clevite CB1665HND. No King equivalent.
CB1663H has a length of 20.12 mm and King have a bearing which is CR8028XP
These will be the bearings in the 2V stroker, it has less load and doesn't need the saw tooth caps on the con rods. I may get the custom Carrillo rods in this size due to the extra bearing length.
King is also working on coated bearings with HM Elliot, it was explained to me that bearing coating is quite complicated to do correctly, something I wasn't aware of. Given these are very hard bearings I will get them in a coated version to protect the crank. I will try to write more later.
#6
Addict
Rennlist Member
Rennlist Member
Thread Starter

Hi Dr Bob, I was trying to find my article on the friction study that Cosworth F1 did. They used a friction rig to analyse the friction in their F1 engines. I suspect what Mahle means may the main bearing friction only, not general friction. I haven't read their complete writings on this topic just recently, maybe I have to refresh myself on that one.
There has been some concerns expressed to me privately that there will not be enough oil getting to the rod bearings. Now that may well be the reason Porsche put so much grooving. My engine is not a standard wet sump engine, it will have a advanced dry sump. So the quality of the oil getting to the bearings, both mains and rods will be much better. Just about all the hi performance engines being built by the big OEMs, i.e Porsche with the GT3, GM with most of the Corvette engines, BMW M series engines and performance AMG engines all have dry sumps. These engines can then employ better more efficient designs.
The other issue I didn't mention was the fact that I am currently designing my new cranks, (the crank maker has agreed to use my design) is that these narrower new main bearings which are about 21 mm + in length. This allows the use of bigger radii on the mains. I am going to go for approx 4 mm which is very large, these bigger radii reduce the stresses where cranks often break. The same can be achieved on the rods given I am making the crank to the same spacing as a factory crank. That is the rod journals will be 54 mm+ wide and not the standard original stroker width of 1.90"/48.26 mm. With the reduced length of the bearings this creates more room for the large radii. I will try to post some pics of the Nascar crank I have which has large radii compared to the 928 crank. Not that there is a problem with the standard crank but it is very bulky and gets its substantial strength from its beefiness. My cranks will be very light in weight so they need to utilise a very good design.
#7
Former Sponsor

Previously I posted about these bearings as a upgrade to the Porsche 928 OEM design bearings. There was lots to like but I had some concerns and they were not the most optimal they could be. That is because they were not around the 140 degree amount of grooving that is seen as optimal at least in most hi performance engines where they are chasing every HP. Obviously this type of grooving requires some highly skilled machining.
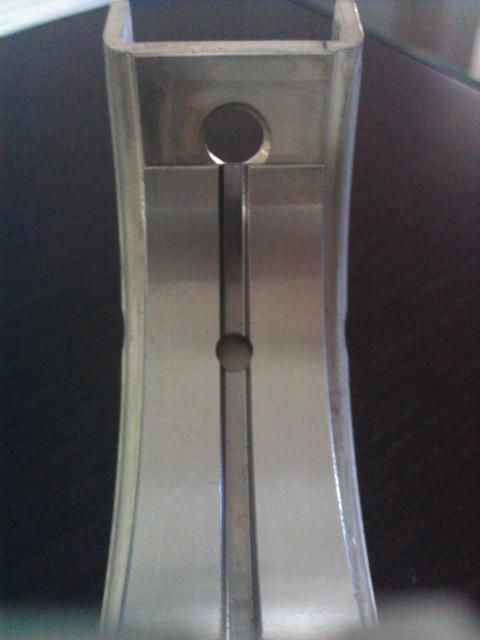
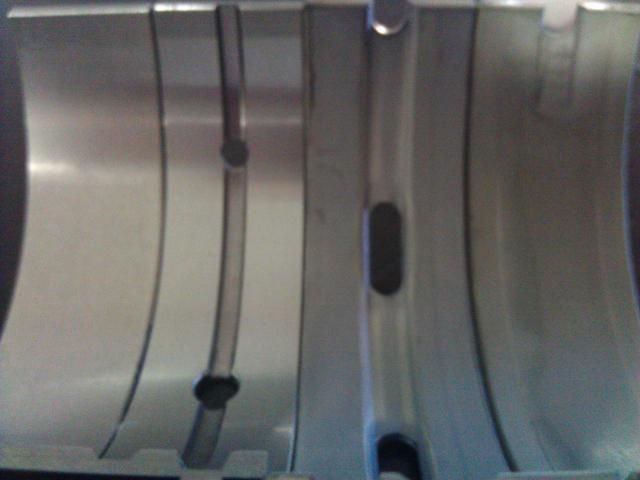
Below is some Nascar bearings, some have more grooving than others. These are not the most optimal as they have the retaining tabs removing surface area from the running surface.
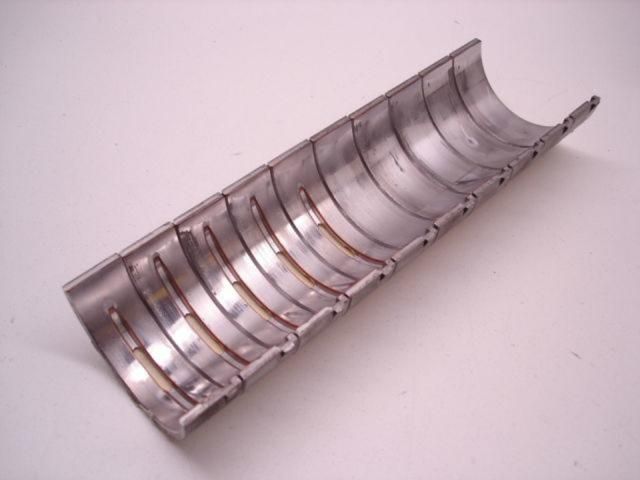
This is a stroke of luck, the new race style bearings fit neatly into the 928 bearings. You will also note that the bearing surface is not impaired by the retaining tab.

Side by side with the upper 928 bearings, note the 928 bearings don't have much use on them but look at the wear pattern. Also it should be noted that the amount of "load surface area" is probably greater on the new bearings. These bearings are very hard, they are race bearings and I was told by an engine builder that he uses them in his 1400 HP builds and they wear extremely well.

A closer look at the retaining tab area of the bearing, you can see the recess creates high pressure and wear. This equals high friction. More on that a bit later.

Here's two front nose bearings, notice how the main bearing journal must be climbing up the wall of the bearing where the grooving is.
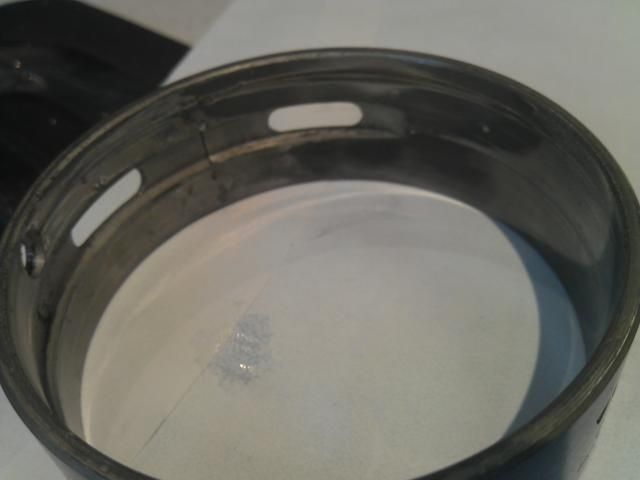
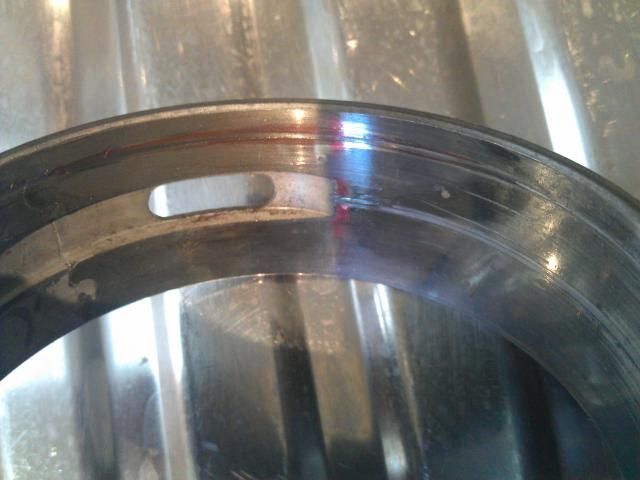
So now it becomes pretty easy to see that by having the grooving you add to wear and friction. Mahle have a very interesting graph. A 2% HP gain by having 40 degrees less grooving. A massive 15% over 360 degree grooved bearings. Now that seems a lot and it isn't my claim but Mahle's.
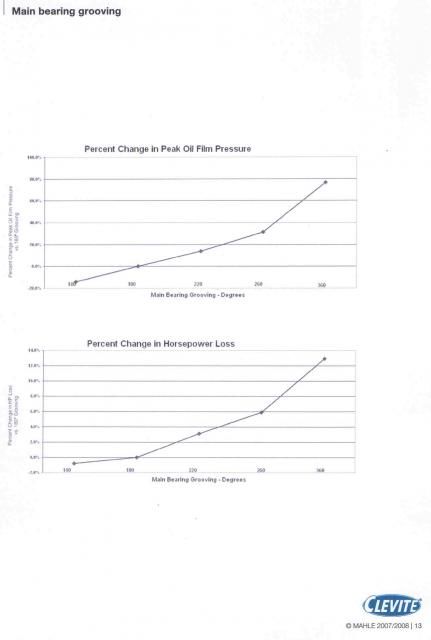
The grooving is much wider in this bearing candidate than my first try, it is approx 4.5 mm at the base and 5 mm at the surface of the bearing. There is obviously a small reduction of the main journal diameter, So there will be some marginal benefit with the higher revs than the factory rev limit. There is much information regarding the changes to the grooving can make. King bearings have some excellent products and most of their bearings don't have the locating tab recess in the bearings surface.

Below is a link to King Bearings It is well worth the read;
http://kingracebearings.com/wp-conte...e-bearings.pdf
Basically they ran conventional bearings vs new design bearings against each other in the same engine. Then they weighed and measured them.
The results were, ……………...Conventionall groove….Hi Performance groove
Thickness reduction in microns ..63 microns……………..41 microns……………..
Weight reduction in miii grams…29 mg………………..…….19 mg……………………
You will need the whole test procedure if you require more info which is in the link.
Also there is this video which is interesting.
http://youtu.be/dPhLADi-VFM
I'm certainly looking forward to using these bearings, they don't have a massive range like Mahle Clevite but will suit many hi performance rods like these that I intend to use. The tighter you run your clearances, the better the standard required for all the parts. The machining of the crank, the tolerance of the bearings. The stability of the bearing housing. You will note for the folks who haven't seen these rods, the saw tooth pattern on the bearing caps on the rod on the left. This is to stop fretting or walking which would alter tight tolerances to the point there may be a failure.
Another King Bearing video,
http://youtu.be/_pSQhdgFum8
I have decided not to run the forced pin oiling, I am designed an advanced oil squirting system that will spray multiple jets of oil at the piston and thus also the small end. this will help as these are piston guided rods and by not having the dowel hole in the rod bearing I won't be taking any oil away from the rod bearing either. Again it goes to the same principle as the main bearing grooving.
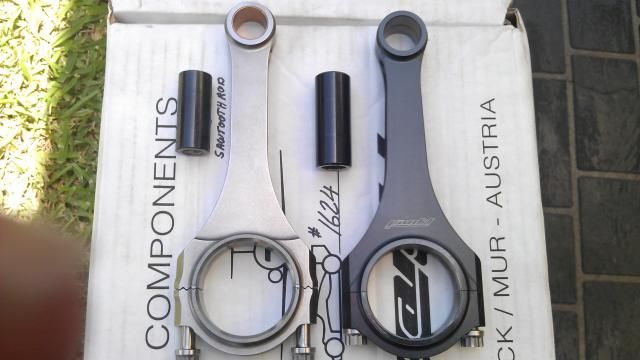
So the cost of this conversion will be under a $1000. Probably well under, I was quoted between $300 to $400 for the line bore of the Porsche bearings. I have a new Porsche thrust bearing which is required as I am using the Porsche thrust faces but not the slipper faces. There is some cost to notch the Porsche thrust bearing to accept the new bearing and there is also a cost to notch the front main bearing because it uses a one piece bearing in my block. So I suspect the actual modification cost is around $500 plus parts. The new bearings are cheaper than the Porsche 928 bearings, I guess that doesn't surprise anybody though does it. So there is some cost offset there.
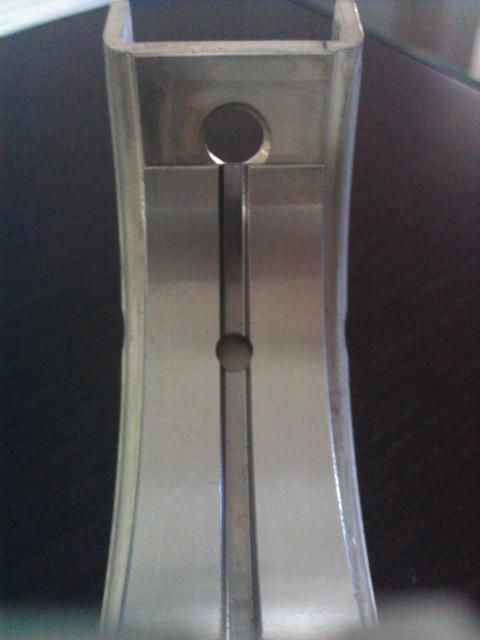
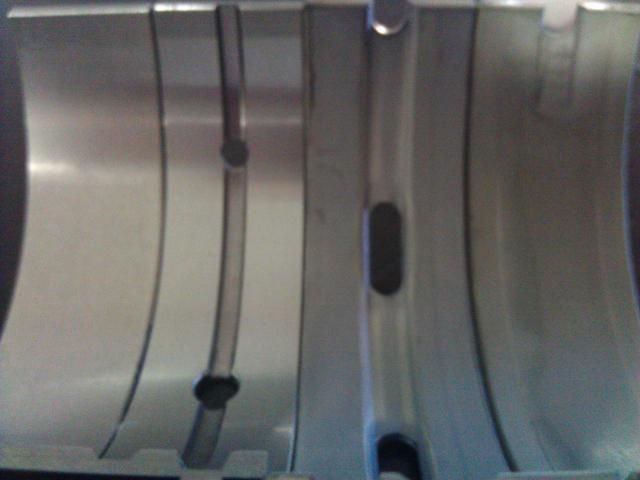
Below is some Nascar bearings, some have more grooving than others. These are not the most optimal as they have the retaining tabs removing surface area from the running surface.
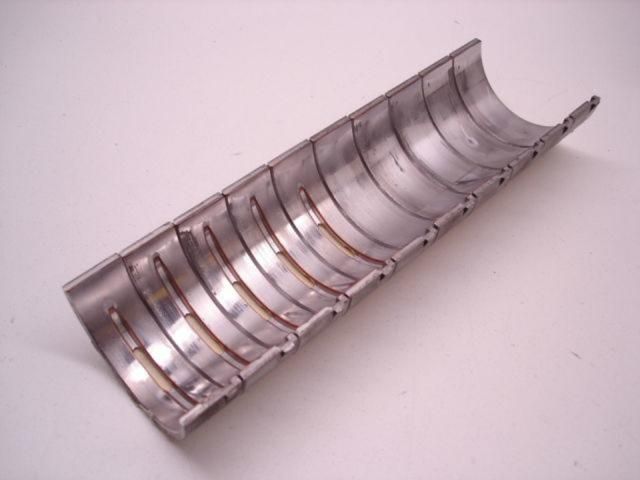
This is a stroke of luck, the new race style bearings fit neatly into the 928 bearings. You will also note that the bearing surface is not impaired by the retaining tab.

Side by side with the upper 928 bearings, note the 928 bearings don't have much use on them but look at the wear pattern. Also it should be noted that the amount of "load surface area" is probably greater on the new bearings. These bearings are very hard, they are race bearings and I was told by an engine builder that he uses them in his 1400 HP builds and they wear extremely well.

A closer look at the retaining tab area of the bearing, you can see the recess creates high pressure and wear. This equals high friction. More on that a bit later.

Here's two front nose bearings, notice how the main bearing journal must be climbing up the wall of the bearing where the grooving is.
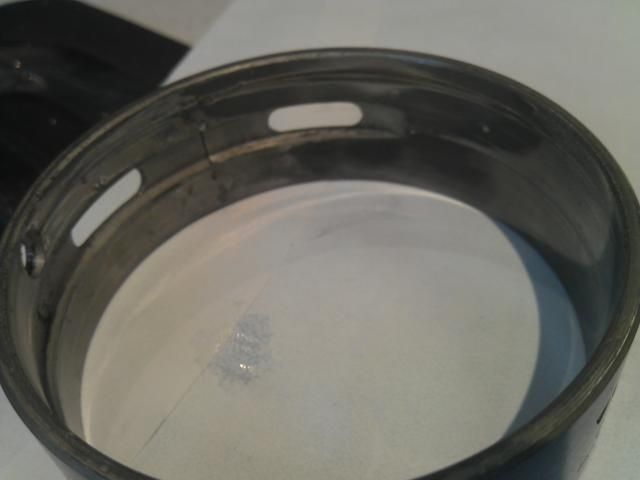
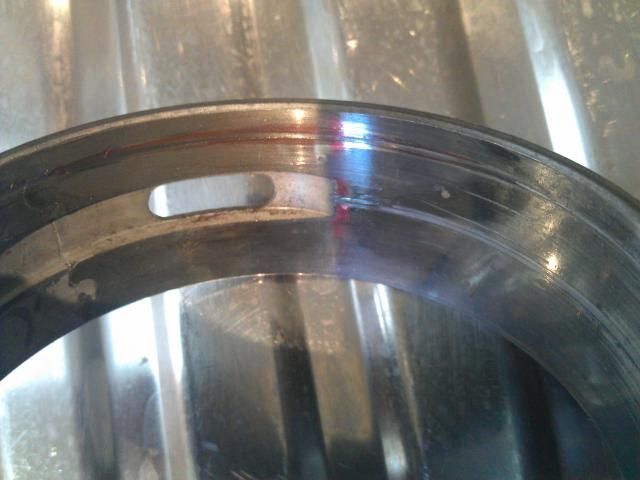
So now it becomes pretty easy to see that by having the grooving you add to wear and friction. Mahle have a very interesting graph. A 2% HP gain by having 40 degrees less grooving. A massive 15% over 360 degree grooved bearings. Now that seems a lot and it isn't my claim but Mahle's.
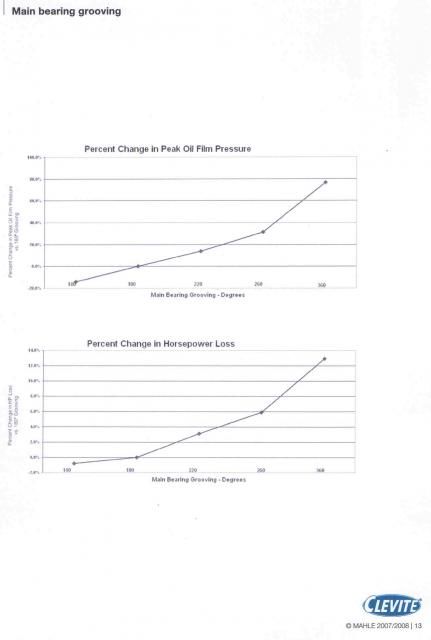
The grooving is much wider in this bearing candidate than my first try, it is approx 4.5 mm at the base and 5 mm at the surface of the bearing. There is obviously a small reduction of the main journal diameter, So there will be some marginal benefit with the higher revs than the factory rev limit. There is much information regarding the changes to the grooving can make. King bearings have some excellent products and most of their bearings don't have the locating tab recess in the bearings surface.

Below is a link to King Bearings It is well worth the read;
http://kingracebearings.com/wp-conte...e-bearings.pdf
Basically they ran conventional bearings vs new design bearings against each other in the same engine. Then they weighed and measured them.
The results were, ……………...Conventionall groove….Hi Performance groove
Thickness reduction in microns ..63 microns……………..41 microns……………..
Weight reduction in miii grams…29 mg………………..…….19 mg……………………
You will need the whole test procedure if you require more info which is in the link.
Also there is this video which is interesting.
http://youtu.be/dPhLADi-VFM
I'm certainly looking forward to using these bearings, they don't have a massive range like Mahle Clevite but will suit many hi performance rods like these that I intend to use. The tighter you run your clearances, the better the standard required for all the parts. The machining of the crank, the tolerance of the bearings. The stability of the bearing housing. You will note for the folks who haven't seen these rods, the saw tooth pattern on the bearing caps on the rod on the left. This is to stop fretting or walking which would alter tight tolerances to the point there may be a failure.
Another King Bearing video,
http://youtu.be/_pSQhdgFum8
I have decided not to run the forced pin oiling, I am designed an advanced oil squirting system that will spray multiple jets of oil at the piston and thus also the small end. this will help as these are piston guided rods and by not having the dowel hole in the rod bearing I won't be taking any oil away from the rod bearing either. Again it goes to the same principle as the main bearing grooving.
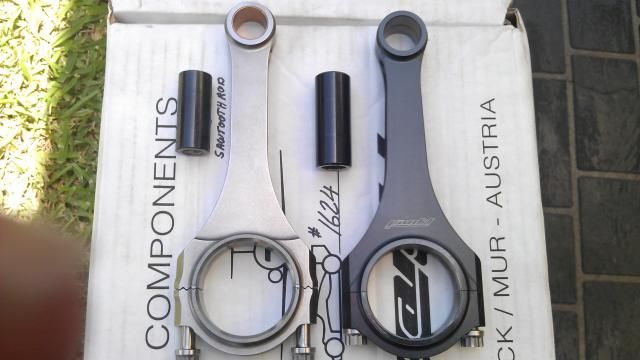
So the cost of this conversion will be under a $1000. Probably well under, I was quoted between $300 to $400 for the line bore of the Porsche bearings. I have a new Porsche thrust bearing which is required as I am using the Porsche thrust faces but not the slipper faces. There is some cost to notch the Porsche thrust bearing to accept the new bearing and there is also a cost to notch the front main bearing because it uses a one piece bearing in my block. So I suspect the actual modification cost is around $500 plus parts. The new bearings are cheaper than the Porsche 928 bearings, I guess that doesn't surprise anybody though does it. So there is some cost offset there.
But it would seem, to me, that installing a harder main bearing with a steel backing into the "soft" stock Porsche main bearing would just pound out the soft stock Porsche main bearings, as soon as the crankshaft has any distortion/harmonics.
Trending Topics
#8
Addict
Rennlist Member
Rennlist Member
Thread Starter

I'm very confused about what your goals are and what you are doing.
But it would seem, to me, that installing a harder main bearing with a steel backing into the "soft" stock Porsche main bearing would just pound out the soft stock Porsche main bearings, as soon as the crankshaft has any distortion/harmonics.
But it would seem, to me, that installing a harder main bearing with a steel backing into the "soft" stock Porsche main bearing would just pound out the soft stock Porsche main bearings, as soon as the crankshaft has any distortion/harmonics.
The Porsche bearings are being used as spacer bearings, just like people do for the small block chevy with the 350 cranks in 400 blocks etc.
There is basically no soft bearing material used, the Porsche 928 bearings get lined bored. This was the cost I mentioned that I got quoted of between $300 to $400. So to clarify, I will use old 928 bearings in 4 of the mains and a new thrust bearing. These bearings are then bored to the O.D of the new design bearings and then these bearings fit into the steel shells of the 928 bearings. There is no bearing material left except for the thrust faces of the thrust bearing. It just happen to be a coincidence that the tab recess is placed in the correct location for this mod. Now when the shells are bored I may have to "touch up the recess" to ensure correct fit. I can't comment on the necessity to do that just yet.
The goals are less bearing wear, less friction and heat. The bearing speed will be slightly reduced. This should slightly lower friction if and it should help create better hydrodynamic lubrication. The change between hydrodynamic lubrication and mixed lubrication is where the gains are. This cannot be achieved properly with a excessively grooved bearing, at best it will be "mixed" lubrication
if you haven't read the attached article by King Bearings I suggest it is worth your time. It has actual testing of what a better designed bearing on their engine dyno test rig can produce. it is not exactly what I am doing but I am incorporating some of their changes.
#9
Former Sponsor

The Porsche bearings are being used as spacer bearings, just like people do for the small block chevy with the 350 cranks in 400 blocks etc.
There is basically no soft bearing material used, the Porsche 928 bearings get lined bored. This was the cost I mentioned that I got quoted of between $300 to $400. So to clarify, I will use old 928 bearings in 4 of the mains and a new thrust bearing. These bearings are then bored to the O.D of the new design bearings and then these bearings fit into the steel shells of the 928 bearings. There is no bearing material left except for the thrust faces of the thrust bearing. It just happen to be a coincidence that the tab recess is placed in the correct location for this mod. Now when the shells are bored I may have to "touch up the recess" to ensure correct fit. I can't comment on the necessity to do that just yet.
The goals are less bearing wear, less friction and heat. The bearing speed will be slightly reduced. This should slightly lower friction if and it should help create better hydrodynamic lubrication. The change between hydrodynamic lubrication and mixed lubrication is where the gains are. This cannot be achieved properly with a excessively grooved bearing, at best it will be "mixed" lubrication
if you haven't read the attached article by King Bearings I suggest it is worth your time. It has actual testing of what a better designed bearing on their engine dyno test rig can produce. it is not exactly what I am doing but I am incorporating some of their changes.
There is basically no soft bearing material used, the Porsche 928 bearings get lined bored. This was the cost I mentioned that I got quoted of between $300 to $400. So to clarify, I will use old 928 bearings in 4 of the mains and a new thrust bearing. These bearings are then bored to the O.D of the new design bearings and then these bearings fit into the steel shells of the 928 bearings. There is no bearing material left except for the thrust faces of the thrust bearing. It just happen to be a coincidence that the tab recess is placed in the correct location for this mod. Now when the shells are bored I may have to "touch up the recess" to ensure correct fit. I can't comment on the necessity to do that just yet.
The goals are less bearing wear, less friction and heat. The bearing speed will be slightly reduced. This should slightly lower friction if and it should help create better hydrodynamic lubrication. The change between hydrodynamic lubrication and mixed lubrication is where the gains are. This cannot be achieved properly with a excessively grooved bearing, at best it will be "mixed" lubrication
if you haven't read the attached article by King Bearings I suggest it is worth your time. It has actual testing of what a better designed bearing on their engine dyno test rig can produce. it is not exactly what I am doing but I am incorporating some of their changes.
Your picture of the stock main bearing and the new main bearing mislead me.
It's so great that you are thinking outside the box and traveling down a different road.
Obvious in the picture of the "Nascar" main bearings, that there are two distinct different lengths of the oil grooves. If the bearings are actually pictured in order, I'd have to assume that #1 main and #5 main have the "shorter" grooves, because they are supplying oil to only one rod bearing, each. The three "longer" grooves are presumably longer because these main bearing feed oil to two rod journals.
Makes total sense, if you think about each rod journal and corresponding "oil feed system" being its own small scale "oil pump", which is the theory that most oiling experts believe.
Of course, Nascar engine guys are notoriously secretive....so whenever a picture gets published, you have to question if what you are looking at is something that worked, or something that did not work...and a couple of those lower un-grooved bearings, in the rear of the picture, don't look like they were too happy!
If you talk to very many experts about crankshaft oiling (if you can get them to talk to you), the entire oiling of an engine becomes a really interesting topic.
What works in one engine, doesn't work in another engine....mostly because of the differences in crankshaft distortion and how that distortion affects the oil feeding (they say that what we consider to be a solid chunk of rigid steel becomes more like a piece of rubber, when an engine is running, at high loads and high rpms.)
It actually gets more involved than that.....what works with one crankshaft design, in one engine may not work with a different crankshaft design in the same engine....that being completely dependent upon how that "piece of rubber" flexes and affects the oil feed.
And, if that is not enough....what works for one RPM range, may not work in the same engine with the same crankshaft, in a different rpm range.....again, totally dependent upon how "that piece of rubber" flexes and how that flex affects the oiling at the different rpm ranges.
Very frustrating stuff, for most professional engine builders.
To figure out what actually "works" becomes an "experiment" to try different combinations to see what works. (That's how the Nascar guys figured out how long to make those different length oil grooves, within the same engine.)
Sounds like you've got a really interesting project ahead of you. Should keep you thinking, for quite some time. Good luck....and more importantly....have fun!
#10
Addict
Rennlist Member
Rennlist Member
Thread Starter

Greg you are spot on regarding Nascar guys being secretive, those bearings would be quite old and the current bearings may not look like those in the picture, so I do not regard those bearings as the "Holy Grail" but just one approach.
The other issue we should consider is that the journals on Nascar cranks are quite small. The mains are 2" and the rods are 1.85" and have roughly 7 mm of overlap for their roughly 82 mm stroke cranks. There is different approaches to the design of the cranks and in a article I read and recounted here on Rennlist various main bearings have different loadings and that may influence what they are doing with the grooving too. Of course not everything they try will work, nor will what I do be optimal.
However my cranks will not be pushed to the same limits as a Nascar crank for the simple reason those cranks have less material or mass to do their work. The Winberg crank I have from memory was 16.5 kgs. Most likely I will be in the 21 to 22 kgs range. So if I have the same power, I hopefully have more material to resist bending forces.
The "rubber" issue you mention is one reason that piston guided rods are basically exclusively used in top end racing. When I contacted a well known British engine part manufacturer, I was advised when I queried how familiar they were with piston guided setups, they replied. "For the top teams, i.e British touring cars, World rally and British Superbikes etc, they are all piston guided."
The advantage is when the bending occurs it doesn't make the big ends rub against each other and against the crank cheeks. Again the narrower bearings have less chance of being "pinched". The piston guided setup under normal conditions will have less friction due to inherent design advantage of have less rubbing surfaces. Mercedes and Ferrari implement piston guided setups in some of their street engines.
I will try to post more later, there is a very interesting article, I believe it is a British Superbike crankshaft study, it's by Riccardo in the UK and it deals with flexing and vibration. Riccardo are responsible for many advanced engines like the one used in the McLaren etc.
If you think about it, bearing design has had to improve due to the thinner oils being used in modern engines. The critical separation of the crank or rod bearings against the crankshaft is now smaller due to the thinner oil so the inherent design of the bearing has to improve to carry the same or greater loads with that thinner oil.
The other issue we should consider is that the journals on Nascar cranks are quite small. The mains are 2" and the rods are 1.85" and have roughly 7 mm of overlap for their roughly 82 mm stroke cranks. There is different approaches to the design of the cranks and in a article I read and recounted here on Rennlist various main bearings have different loadings and that may influence what they are doing with the grooving too. Of course not everything they try will work, nor will what I do be optimal.
However my cranks will not be pushed to the same limits as a Nascar crank for the simple reason those cranks have less material or mass to do their work. The Winberg crank I have from memory was 16.5 kgs. Most likely I will be in the 21 to 22 kgs range. So if I have the same power, I hopefully have more material to resist bending forces.
The "rubber" issue you mention is one reason that piston guided rods are basically exclusively used in top end racing. When I contacted a well known British engine part manufacturer, I was advised when I queried how familiar they were with piston guided setups, they replied. "For the top teams, i.e British touring cars, World rally and British Superbikes etc, they are all piston guided."
The advantage is when the bending occurs it doesn't make the big ends rub against each other and against the crank cheeks. Again the narrower bearings have less chance of being "pinched". The piston guided setup under normal conditions will have less friction due to inherent design advantage of have less rubbing surfaces. Mercedes and Ferrari implement piston guided setups in some of their street engines.
I will try to post more later, there is a very interesting article, I believe it is a British Superbike crankshaft study, it's by Riccardo in the UK and it deals with flexing and vibration. Riccardo are responsible for many advanced engines like the one used in the McLaren etc.
If you think about it, bearing design has had to improve due to the thinner oils being used in modern engines. The critical separation of the crank or rod bearings against the crankshaft is now smaller due to the thinner oil so the inherent design of the bearing has to improve to carry the same or greater loads with that thinner oil.
I see. When you said that the new main bearing fit into the stock 928 main bearing....I made the bad assumption that the stock main bearing was still the same stock internal size and that it had not been machined to remove all of the soft bearing material, to allow the new bearing to fit inside of it.
Your picture of the stock main bearing and the new main bearing mislead me.
It's so great that you are thinking outside the box and traveling down a different road.
Obvious in the picture of the "Nascar" main bearings, that there are two distinct different lengths of the oil grooves. If the bearings are actually pictured in order, I'd have to assume that #1 main and #5 main have the "shorter" grooves, because they are supplying oil to only one rod bearing, each. The three "longer" grooves are presumably longer because these main bearing feed oil to two rod journals.
Makes total sense, if you think about each rod journal and corresponding "oil feed system" being its own small scale "oil pump", which is the theory that most oiling experts believe.
Of course, Nascar engine guys are notoriously secretive....so whenever a picture gets published, you have to question if what you are looking at is something that worked, or something that did not work...and a couple of those lower un-grooved bearings, in the rear of the picture, don't look like they were too happy!
If you talk to very many experts about crankshaft oiling (if you can get them to talk to you), the entire oiling of an engine becomes a really interesting topic.
What works in one engine, doesn't work in another engine....mostly because of the differences in crankshaft distortion and how that distortion affects the oil feeding (they say that what we consider to be a solid chunk of rigid steel becomes more like a piece of rubber, when an engine is running, at high loads and high rpms.)
It actually gets more involved than that.....what works with one crankshaft design, in one engine may not work with a different crankshaft design in the same engine....that being completely dependent upon how that "piece of rubber" flexes and affects the oil feed.
And, if that is not enough....what works for one RPM range, may not work in the same engine with the same crankshaft, in a different rpm range.....again, totally dependent upon how "that piece of rubber" flexes and how that flex affects the oiling at the different rpm ranges.
Very frustrating stuff, for most professional engine builders.
To figure out what actually "works" becomes an "experiment" to try different combinations to see what works. (That's how the Nascar guys figured out how long to make those different length oil grooves, within the same engine.)
Sounds like you've got a really interesting project ahead of you. Should keep you thinking, for quite some time. Good luck....and more importantly....have fun!
Your picture of the stock main bearing and the new main bearing mislead me.
It's so great that you are thinking outside the box and traveling down a different road.
Obvious in the picture of the "Nascar" main bearings, that there are two distinct different lengths of the oil grooves. If the bearings are actually pictured in order, I'd have to assume that #1 main and #5 main have the "shorter" grooves, because they are supplying oil to only one rod bearing, each. The three "longer" grooves are presumably longer because these main bearing feed oil to two rod journals.
Makes total sense, if you think about each rod journal and corresponding "oil feed system" being its own small scale "oil pump", which is the theory that most oiling experts believe.
Of course, Nascar engine guys are notoriously secretive....so whenever a picture gets published, you have to question if what you are looking at is something that worked, or something that did not work...and a couple of those lower un-grooved bearings, in the rear of the picture, don't look like they were too happy!
If you talk to very many experts about crankshaft oiling (if you can get them to talk to you), the entire oiling of an engine becomes a really interesting topic.
What works in one engine, doesn't work in another engine....mostly because of the differences in crankshaft distortion and how that distortion affects the oil feeding (they say that what we consider to be a solid chunk of rigid steel becomes more like a piece of rubber, when an engine is running, at high loads and high rpms.)
It actually gets more involved than that.....what works with one crankshaft design, in one engine may not work with a different crankshaft design in the same engine....that being completely dependent upon how that "piece of rubber" flexes and affects the oil feed.
And, if that is not enough....what works for one RPM range, may not work in the same engine with the same crankshaft, in a different rpm range.....again, totally dependent upon how "that piece of rubber" flexes and how that flex affects the oiling at the different rpm ranges.
Very frustrating stuff, for most professional engine builders.
To figure out what actually "works" becomes an "experiment" to try different combinations to see what works. (That's how the Nascar guys figured out how long to make those different length oil grooves, within the same engine.)
Sounds like you've got a really interesting project ahead of you. Should keep you thinking, for quite some time. Good luck....and more importantly....have fun!
#11
Former Sponsor

Greg you are spot on regarding Nascar guys being secretive, those bearings would be quite old and the current bearings may not look like those in the picture, so I do not regard those bearings as the "Holy Grail" but just one approach.
The other issue we should consider is that the journals on Nascar cranks are quite small. The mains are 2" and the rods are 1.85" and have roughly 7 mm of overlap for their roughly 82 mm stroke cranks. There is different approaches to the design of the cranks and in a article I read and recounted here on Rennlist various main bearings have different loadings and that may influence what they are doing with the grooving too. Of course not everything they try will work, nor will what I do be optimal.
However my cranks will not be pushed to the same limits as a Nascar crank for the simple reason those cranks have less material or mass to do their work. The Winberg crank I have from memory was 16.5 kgs. Most likely I will be in the 21 to 22 kgs range. So if I have the same power, I hopefully have more material to resist bending forces.
The "rubber" issue you mention is one reason that piston guided rods are basically exclusively used in top end racing. When I contacted a well known British engine part manufacturer, I was advised when I queried how familiar they were with piston guided setups, they replied. "For the top teams, i.e British touring cars, World rally and British Superbikes etc, they are all piston guided."
The advantage is when the bending occurs it doesn't make the big ends rub against each other and against the crank cheeks. Again the narrower bearings have less chance of being "pinched". The piston guided setup under normal conditions will have less friction due to inherent design advantage of have less rubbing surfaces. Mercedes and Ferrari implement piston guided setups in some of their street engines.
I will try to post more later, there is a very interesting article, I believe it is a British Superbike crankshaft study, it's by Riccardo in the UK and it deals with flexing and vibration. Riccardo are responsible for many advanced engines like the one used in the McLaren etc.
If you think about it, bearing design has had to improve due to the thinner oils being used in modern engines. The critical separation of the crank or rod bearings against the crankshaft is now smaller due to the thinner oil so the inherent design of the bearing has to improve to carry the same or greater loads with that thinner oil.
The other issue we should consider is that the journals on Nascar cranks are quite small. The mains are 2" and the rods are 1.85" and have roughly 7 mm of overlap for their roughly 82 mm stroke cranks. There is different approaches to the design of the cranks and in a article I read and recounted here on Rennlist various main bearings have different loadings and that may influence what they are doing with the grooving too. Of course not everything they try will work, nor will what I do be optimal.
However my cranks will not be pushed to the same limits as a Nascar crank for the simple reason those cranks have less material or mass to do their work. The Winberg crank I have from memory was 16.5 kgs. Most likely I will be in the 21 to 22 kgs range. So if I have the same power, I hopefully have more material to resist bending forces.
The "rubber" issue you mention is one reason that piston guided rods are basically exclusively used in top end racing. When I contacted a well known British engine part manufacturer, I was advised when I queried how familiar they were with piston guided setups, they replied. "For the top teams, i.e British touring cars, World rally and British Superbikes etc, they are all piston guided."
The advantage is when the bending occurs it doesn't make the big ends rub against each other and against the crank cheeks. Again the narrower bearings have less chance of being "pinched". The piston guided setup under normal conditions will have less friction due to inherent design advantage of have less rubbing surfaces. Mercedes and Ferrari implement piston guided setups in some of their street engines.
I will try to post more later, there is a very interesting article, I believe it is a British Superbike crankshaft study, it's by Riccardo in the UK and it deals with flexing and vibration. Riccardo are responsible for many advanced engines like the one used in the McLaren etc.
If you think about it, bearing design has had to improve due to the thinner oils being used in modern engines. The critical separation of the crank or rod bearings against the crankshaft is now smaller due to the thinner oil so the inherent design of the bearing has to improve to carry the same or greater loads with that thinner oil.
I agree that the picture of the main bearings is probably very old....it has been many years since I've seen a set of "Nascar" bearings that were not coated.
The point I was trying to make is that amazing few things that happen inside race engines actually will work on a "street" engine.
Take piston guided rods, for instance: On a crank guided rod, the clearance between the crank and the rod does more than just guide the rod....it controls the amount of oil that is "lost" from the rod bearings. Obviously, without some sort of resistance at the very end of an oiling system, there will be no or significantly reduced pressure. The rod side clearance provides this resistance and ensures that there will be oil pressure at lower rpms....this is one of the factors that I take into account in every engine I design and build.
This is not as important of a factor in a pure high rpm race engine that never idles....the shear volume of the oil delivered will make up for the loss of resistance. However, it will require a really interesting oil pump arrangement to provide enough oil pressure at idle and lower rpms for a piston guided rod.
My current generation of cranks have reduced rod journal dimensions....to both slow down the bearing speed and to allow me to select from a larger selection of higher quality rod bearings. I'm still using stock 928 main bearing dimensions, to keep the overlap on the longer stroke crankshafts within "tolerable" specifications. Even with this, I felt I had to make significant changes to the crankshaft design to make the crankshafts stiffer and stronger....especially for the longer stroke crankshafts.
My current cranks are approximately 5 pounds lighter that an equivalent stock stroke or stroker crankshaft, even with the increased stiffness.
It gets really interesting to remove much more material....the shear weight of the rods and pistons requires a certain amount of counterweight, in order to be able to balance the crankshaft. Obviously, a titanium rod and a super lightweight piston would reduce this requirement, but this puts the costs of constucting an engine even higher than they already are....and the costs are already way beyond most people's budgets.
The other factor in reducing the weight of a crankshaft is the relatively long 928 crankshaft. The distance from the main bearing to the rod journal is large...and this requires a certain amount of metal, just to connect the two.
I enjoy your ideas and new approach. Everything I post regarding the subject is not meant to be critical, but simply "food for thought".
#13
Rennlist Member
Join Date: Feb 2011
Location: Mostly in my workshop located in Sweden.
Posts: 2,232
Received 464 Likes
on
249 Posts

I hope you understand that I'm not trying to dissuade you from following the course you have chosen and you are taking what I'm saying as just a pure theoretical discussion.
I agree that the picture of the main bearings is probably very old....it has been many years since I've seen a set of "Nascar" bearings that were not coated.
The point I was trying to make is that amazing few things that happen inside race engines actually will work on a "street" engine.
Take piston guided rods, for instance: On a crank guided rod, the clearance between the crank and the rod does more than just guide the rod....it controls the amount of oil that is "lost" from the rod bearings. Obviously, without some sort of resistance at the very end of an oiling system, there will be no or significantly reduced pressure. The rod side clearance provides this resistance and ensures that there will be oil pressure at lower rpms....this is one of the factors that I take into account in every engine I design and build.
This is not as important of a factor in a pure high rpm race engine that never idles....the shear volume of the oil delivered will make up for the loss of resistance. However, it will require a really interesting oil pump arrangement to provide enough oil pressure at idle and lower rpms for a piston guided rod.
My current generation of cranks have reduced rod journal dimensions....to both slow down the bearing speed and to allow me to select from a larger selection of higher quality rod bearings. I'm still using stock 928 main bearing dimensions, to keep the overlap on the longer stroke crankshafts within "tolerable" specifications. Even with this, I felt I had to make significant changes to the crankshaft design to make the crankshafts stiffer and stronger....especially for the longer stroke crankshafts.
My current cranks are approximately 5 pounds lighter that an equivalent stock stroke or stroker crankshaft, even with the increased stiffness.
It gets really interesting to remove much more material....the shear weight of the rods and pistons requires a certain amount of counterweight, in order to be able to balance the crankshaft. Obviously, a titanium rod and a super lightweight piston would reduce this requirement, but this puts the costs of constucting an engine even higher than they already are....and the costs are already way beyond most people's budgets.
The other factor in reducing the weight of a crankshaft is the relatively long 928 crankshaft. The distance from the main bearing to the rod journal is large...and this requires a certain amount of metal, just to connect the two.
I enjoy your ideas and new approach. Everything I post regarding the subject is not meant to be critical, but simply "food for thought".
I agree that the picture of the main bearings is probably very old....it has been many years since I've seen a set of "Nascar" bearings that were not coated.
The point I was trying to make is that amazing few things that happen inside race engines actually will work on a "street" engine.
Take piston guided rods, for instance: On a crank guided rod, the clearance between the crank and the rod does more than just guide the rod....it controls the amount of oil that is "lost" from the rod bearings. Obviously, without some sort of resistance at the very end of an oiling system, there will be no or significantly reduced pressure. The rod side clearance provides this resistance and ensures that there will be oil pressure at lower rpms....this is one of the factors that I take into account in every engine I design and build.
This is not as important of a factor in a pure high rpm race engine that never idles....the shear volume of the oil delivered will make up for the loss of resistance. However, it will require a really interesting oil pump arrangement to provide enough oil pressure at idle and lower rpms for a piston guided rod.
My current generation of cranks have reduced rod journal dimensions....to both slow down the bearing speed and to allow me to select from a larger selection of higher quality rod bearings. I'm still using stock 928 main bearing dimensions, to keep the overlap on the longer stroke crankshafts within "tolerable" specifications. Even with this, I felt I had to make significant changes to the crankshaft design to make the crankshafts stiffer and stronger....especially for the longer stroke crankshafts.
My current cranks are approximately 5 pounds lighter that an equivalent stock stroke or stroker crankshaft, even with the increased stiffness.
It gets really interesting to remove much more material....the shear weight of the rods and pistons requires a certain amount of counterweight, in order to be able to balance the crankshaft. Obviously, a titanium rod and a super lightweight piston would reduce this requirement, but this puts the costs of constucting an engine even higher than they already are....and the costs are already way beyond most people's budgets.
The other factor in reducing the weight of a crankshaft is the relatively long 928 crankshaft. The distance from the main bearing to the rod journal is large...and this requires a certain amount of metal, just to connect the two.
I enjoy your ideas and new approach. Everything I post regarding the subject is not meant to be critical, but simply "food for thought".
Åke
#14
Rennlist Member
Join Date: Feb 2011
Location: Mostly in my workshop located in Sweden.
Posts: 2,232
Received 464 Likes
on
249 Posts
#15
Rennlist Member

Yes Ake
That happened back in june I was able to buy a couple of sets before the closure, unfortunately the bearings that they supplied are so much better then the stock Glyco units , have tested them thoroughly on the race track.
That happened back in june I was able to buy a couple of sets before the closure, unfortunately the bearings that they supplied are so much better then the stock Glyco units , have tested them thoroughly on the race track.