Crank position sender pin assignments
#1

I rebuilt my engine management harness a couple of years ago and whilst removing such the male connector on the CPS literally crumbled away leaving the pins still engaged in the harness plug with nothing around them. The unit was working perfectly OK but I failed to make a note of the assignments within the male plug. The wiring diagram suggests the screen is on pin 3. The remaining cores are yellow and black but there is no indication on the wiring diagram which core goes to pins 1 and 2 respectively.
I have a new male 3 pin junior powertimer plug that I want to fit and thus have a working spare CPS as it were.
Much appreciate if anyone can advise the correct pin assignments or post a photo of the cores under the weather boot. I suspect yellow will be pin 1 but...?
Thanks in anticipation
I have a new male 3 pin junior powertimer plug that I want to fit and thus have a working spare CPS as it were.
Much appreciate if anyone can advise the correct pin assignments or post a photo of the cores under the weather boot. I suspect yellow will be pin 1 but...?
Thanks in anticipation
Last edited by FredR; 06-29-2022 at 02:23 PM.
#3

The layout of the cores suggests yellow would be on pin 1 and black on pin two- will default to that if no one has a firm input.
Cheers
Fred
#4

For a variable reluctor sensor like the one used as a CPS on the 928, polarity does matter. It changes whether the reliable signal location is on the rising or falling edge of the wave form and whether missing teeth are interpreted as a single spike (desirable) or a double spike (undesirable). Either way can work, but one will be reliable and the other may cause sync loss or inconsistent timing.
I haven't looked at the wiring diagram, but it sounds like you have, and it is surprising to hear that there is no wire color identified.
However, the ECU pinout definitely shows which wire is high and which is low. So, you can easily use a multimeter to identify which is which at the CPS plug end. And then use a standard Bosch CPS pinout to determine which pin is high and which is low. The CPS should have the pins numbered on the connector housing.
EZK Pin 23: Speed sender +
EZK Pin 24: Speed sender shield
EZK Pin 6: Speed Sender -
And attached is a Bosch CPS specification document.
I will be removing my intake in a few weeks and can confirm the wiring if you can wait that long.
I haven't looked at the wiring diagram, but it sounds like you have, and it is surprising to hear that there is no wire color identified.
However, the ECU pinout definitely shows which wire is high and which is low. So, you can easily use a multimeter to identify which is which at the CPS plug end. And then use a standard Bosch CPS pinout to determine which pin is high and which is low. The CPS should have the pins numbered on the connector housing.
EZK Pin 23: Speed sender +
EZK Pin 24: Speed sender shield
EZK Pin 6: Speed Sender -
And attached is a Bosch CPS specification document.
I will be removing my intake in a few weeks and can confirm the wiring if you can wait that long.
Last edited by Bulvot; 06-30-2022 at 08:17 AM.
#5

For a variable reluctor sensor like the one used as a CPS on the 928, polarity does matter. It changes whether the reliable signal location is on the rising or falling edge of the wave form and whether missing teeth are interpreted as a single spike (desirable) or a double spike (undesirable). Either way can work, but one will be reliable and the other may cause sync loss or inconsistent timing.
I haven't looked at the wiring diagram, but it sounds like you have, and it is surprising to hear that there is no wire color identified.
However, the ECU pinout definitely shows which wire is high and which is low. So, you can easily use a multimeter to identify which is which at the CPS plug end. And then use a standard Bosch CPS pinout to determine which pin is high and which is low. The CPS should have the pins numbered on the connector housing.
EZK Pin 23: Speed sender +
EZK Pin 24: Speed sender shield
EZK Pin 6: Speed Sender -
And attached is a Bosch CPS specification document.
I will be removing my intake in a few weeks and can confirm the wiring if you can wait that long.
I haven't looked at the wiring diagram, but it sounds like you have, and it is surprising to hear that there is no wire color identified.
However, the ECU pinout definitely shows which wire is high and which is low. So, you can easily use a multimeter to identify which is which at the CPS plug end. And then use a standard Bosch CPS pinout to determine which pin is high and which is low. The CPS should have the pins numbered on the connector housing.
EZK Pin 23: Speed sender +
EZK Pin 24: Speed sender shield
EZK Pin 6: Speed Sender -
And attached is a Bosch CPS specification document.
I will be removing my intake in a few weeks and can confirm the wiring if you can wait that long.
The wiring diagram is colour coded correctly so no problem there and the harness has a white core and a brown core so I assumed that the brown is the earth as per general wiring convention. Had Bosch followed the convention within the CPS and used the same colours I would not be confused but of course no such logical rationale. I suspect the yellow core is positive and black the earth but...?
What I do not understand is how to differentiate between the earth and the plus signal on the CPS using a multimeter- doubtless it will be simple but not on my elecronics pay grade scale!
The new junior powertimer male connector has the pin numbers identified so no problem there, shield is pin 3.
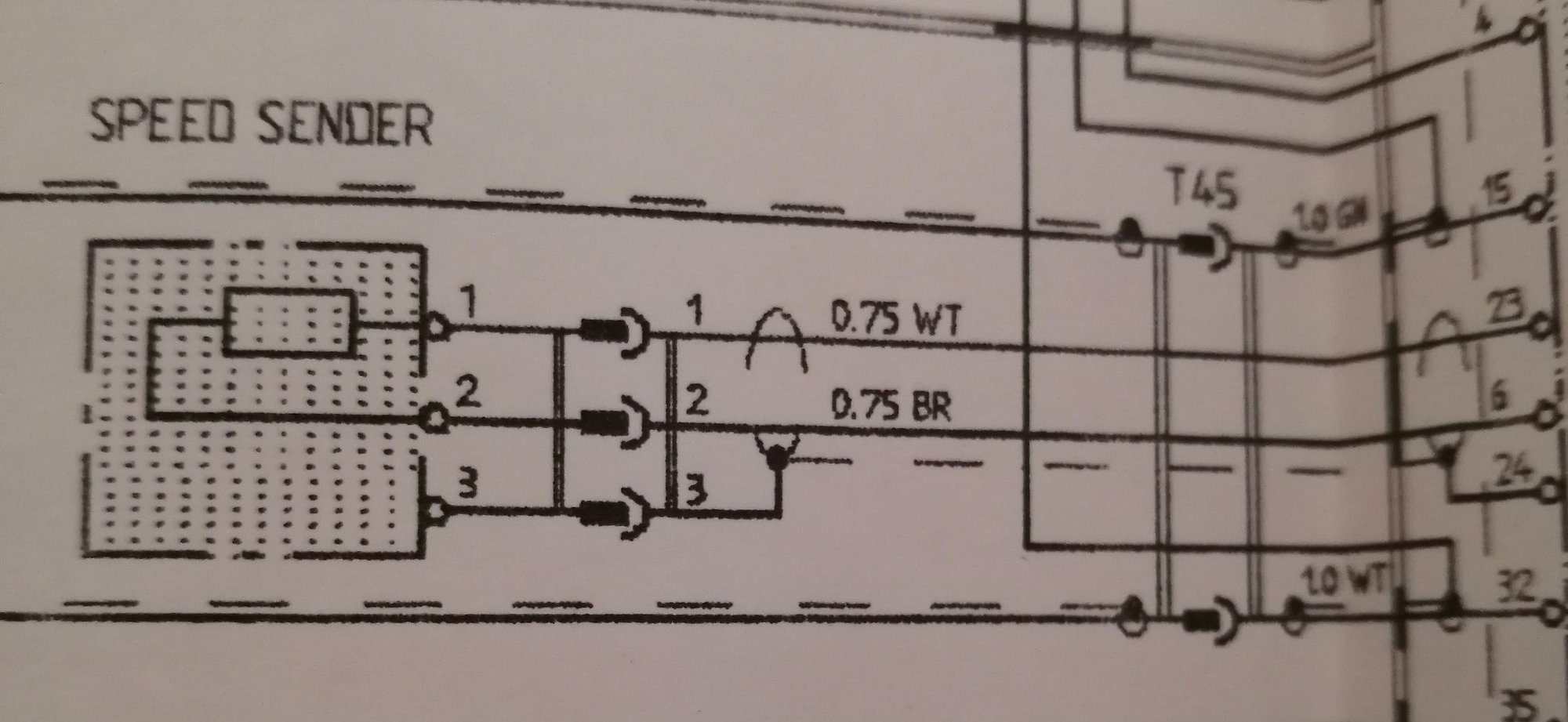
#6

The most sure way to determine the high and low side wires is to use an oscilloscope and observe the signal as the trigger wheel spins. Which, I know, is not an easy test to perform on a spare uninstalled CPS.
Check out page 3 of this document, the LED light test method:
https://www.pim-engineering.com/tied...%20Sensors.pdf
I didn't read it in details, but maybe it will work for you.
Check out page 3 of this document, the LED light test method:
https://www.pim-engineering.com/tied...%20Sensors.pdf
I didn't read it in details, but maybe it will work for you.
#7

The most sure way to determine the high and low side wires is to use an oscilloscope and observe the signal as the trigger wheel spins. Which, I know, is not an easy test to perform on a spare uninstalled CPS.
Check out page 3 of this document, the LED light test method:
https://www.pim-engineering.com/tied...%20Sensors.pdf
I didn't read it in details, but maybe it will work for you.
Check out page 3 of this document, the LED light test method:
https://www.pim-engineering.com/tied...%20Sensors.pdf
I didn't read it in details, but maybe it will work for you.
The documentation makes interesting reading and copies are now in my 928 soft data library- many thanks for sharing. Whether I can rig the LED test and make sense of it remains to be seen.
Trending Topics
#8

I read the document in more depth. The LED approach sounds correct. You'll want a standard 5v (or lower voltage, if available) LED (the kind that's very small and has two leads attached to it). Available online from lots of places, or your local electronics supplier. The instructions in the document are pretty straight forward.
#9

I read the document in more depth. The LED approach sounds correct. You'll want a standard 5v (or lower voltage, if available) LED (the kind that's very small and has two leads attached to it). Available online from lots of places, or your local electronics supplier. The instructions in the document are pretty straight forward.
#10

I read the document in more depth. The LED approach sounds correct. You'll want a standard 5v (or lower voltage, if available) LED (the kind that's very small and has two leads attached to it). Available online from lots of places, or your local electronics supplier. The instructions in the document are pretty straight forward.
I then took a 1/4 inch socket driver to use as a lump of steel, held the black wire to the casing of the LED torch to form the circuit and sort of rapidly brought the socket tool axially into the sensor head- the LED array flickered. Initially I thought I had cracked it but then I noticed if I pulled the tool away from sensor head rapidly it also flickered- bugger!
After some experimenting I found that by progressively changing the speed of approach to the sensor I could get consistent results and more importantly if I pulled the tool awway from the sensor head at approximately the same velocity I approached it the LED's did not flicker so it would seem one has to use a critical approach velocity to make this test work and get consistent results.
Kudos to Mr Bulvot!
Hopefully if I get hold of the other 928's allegedly knackered sensor tomorrow I can verify my findings by physical inspection. ]
I also assume that because I was seeing the LEDs illuminate in this manner it de-facto confirms that my spare CPS unit is in fact viable.
I have reported previously that when I did my harness revamp the male connectors seemed to crumble whereas the female connectors, although replaced, still appeared in good nick. We see this on the Hall sender [I temporarily hard wired the connections and that works fine according to ST2], I installed new knock sensors but the old ones still looked viable and I have a couple of male connectors lying around to revamp those as viable spares for my parts bin.
Last edited by FredR; 07-01-2022 at 11:56 AM.
#11

Outstanding! That's great.
I have found the variable reluctor sensors do have a finite lifespan and will eventually fail internally even if there is nothing observably wrong with them. Keeping an old one as a spare is a good strategy in case nothing else is available, but I would strongly prefer putting in a new one whenever possible. I've had a couple of them fail in other vehicles. The sensors were in very good shape and appeared to have nothing wrong with them. But, electrically did not meet the specifications and the vehicles' computers refused to proceed without them. In one case it affected starting/running, in the other vehicle it prevented shifting (automated manual transmission and it couldn't detect output shaft speed).
Great finding, though, and good to know that there is a way to determine correct wiring.
I have found the variable reluctor sensors do have a finite lifespan and will eventually fail internally even if there is nothing observably wrong with them. Keeping an old one as a spare is a good strategy in case nothing else is available, but I would strongly prefer putting in a new one whenever possible. I've had a couple of them fail in other vehicles. The sensors were in very good shape and appeared to have nothing wrong with them. But, electrically did not meet the specifications and the vehicles' computers refused to proceed without them. In one case it affected starting/running, in the other vehicle it prevented shifting (automated manual transmission and it couldn't detect output shaft speed).
Great finding, though, and good to know that there is a way to determine correct wiring.
#12

Outstanding! That's great.
I have found the variable reluctor sensors do have a finite lifespan and will eventually fail internally even if there is nothing observably wrong with them. Keeping an old one as a spare is a good strategy in case nothing else is available, but I would strongly prefer putting in a new one whenever possible. I've had a couple of them fail in other vehicles. The sensors were in very good shape and appeared to have nothing wrong with them. But, electrically did not meet the specifications and the vehicles' computers refused to proceed without them. In one case it affected starting/running, in the other vehicle it prevented shifting (automated manual transmission and it couldn't detect output shaft speed).
Great finding, though, and good to know that there is a way to determine correct wiring.
I have found the variable reluctor sensors do have a finite lifespan and will eventually fail internally even if there is nothing observably wrong with them. Keeping an old one as a spare is a good strategy in case nothing else is available, but I would strongly prefer putting in a new one whenever possible. I've had a couple of them fail in other vehicles. The sensors were in very good shape and appeared to have nothing wrong with them. But, electrically did not meet the specifications and the vehicles' computers refused to proceed without them. In one case it affected starting/running, in the other vehicle it prevented shifting (automated manual transmission and it couldn't detect output shaft speed).
Great finding, though, and good to know that there is a way to determine correct wiring.
#13

That makes perfect sense. I know someone who did the same thing with a crumbling knock sensor plug. Put a new plug on it and it works just fine (confirmed with SharkTuner). No sense in pulling the entire intake to resolve a small issue like that if it otherwise works fine. However, if the part is already out anyway, and a new one is available... 

#14

That makes perfect sense. I know someone who did the same thing with a crumbling knock sensor plug. Put a new plug on it and it works just fine (confirmed with SharkTuner). No sense in pulling the entire intake to resolve a small issue like that if it otherwise works fine. However, if the part is already out anyway, and a new one is available... 
