Battery-area surprise!
#76

50019b, this is just amazing. I stumbled onto this thread and have been reading, mouth open, for the last 40 minutes. Incredible work and generosity for sharing.
You need to rename this thread, "1,472 Things I did to my car after the battery box surprise!"
Soon as you get bored making your car perfect, I'll swap you for mine.
You need to rename this thread, "1,472 Things I did to my car after the battery box surprise!"
Soon as you get bored making your car perfect, I'll swap you for mine.
#77
Thread Starter
RL Community Team
Rennlist Member
Rennlist Member
Joined: May 2004
Posts: 3,332
Likes: 165
From: Toronto

I took all the parts off that I could and included them in my pile of parts that I took to a plating shop. Although there were myriad items that really did benefit from this, I kind of questioned my sanity by doing everything I could. As it is, I paid for two lots (not cheap) whereas I probably could have just done all the significant items in one lot. It struck me once I put the front spoiler back on just how hard it is to see those foglight fasteners!
50019b, this is just amazing. I stumbled onto this thread and have been reading, mouth open, for the last 40 minutes. Incredible work and generosity for sharing.
You need to rename this thread, "1,472 Things I did to my car after the battery box surprise!"
Soon as you get bored making your car perfect, I'll swap you for mine.
You need to rename this thread, "1,472 Things I did to my car after the battery box surprise!"
Soon as you get bored making your car perfect, I'll swap you for mine.
Certainly many things are going well with this project, but the wheels are a notable mistake and perhaps someone might make better choices than I did on their own project based on what they learn from my results.
Plus, it's therapeutic for me...
#78
#80

I thought I had taken care of some battery tray rust a few years ago, 500_19 has prompted me to take another look at my battery tray. Well, it looks as though I'll be cutting out some metal and welding in some new pieces - Rust never sleeps!!
Don't think you might be safe because you have a dry state car, mine has spent it's whole life in Socal and AZ, everyone needs to take a close look at this area, externally mine didn't look that bad at all. Once I started cutting, my heart sank.
Don't think you might be safe because you have a dry state car, mine has spent it's whole life in Socal and AZ, everyone needs to take a close look at this area, externally mine didn't look that bad at all. Once I started cutting, my heart sank.
#82
Thread Starter
RL Community Team
Rennlist Member
Rennlist Member
Joined: May 2004
Posts: 3,332
Likes: 165
From: Toronto

Ha ha! Speaking of 930s... I don't know if you saw this thread yet, but this makes everything I have ever done look like an absolute hack job (even my 944 project... which I formerly thought was great...)
https://rennlist.com/forums/911-turb...ion-at-9m.html
I think Ed nailed it... it all depends on what has happened in the past vis-a-vis battery acid boil overs. My car was a southern car too, and it is very rust-free otherwise (no rusty bolts on the underside etc).
I am sorry to hear you found the tin worm, but I guarantee you will feel really good about the car once you have taken care of it. Just try not to end up in while-you're-in-there purgatory too!!
https://rennlist.com/forums/911-turb...ion-at-9m.html
I thought I had taken care of some battery tray rust a few years ago, 500_19 has prompted me to take another look at my battery tray. Well, it looks as though I'll be cutting out some metal and welding in some new pieces - Rust never sleeps!!
Don't think you might be safe because you have a dry state car, mine has spent it's whole life in Socal and AZ, everyone needs to take a close look at this area, externally mine didn't look that bad at all. Once I started cutting, my heart sank.
Don't think you might be safe because you have a dry state car, mine has spent it's whole life in Socal and AZ, everyone needs to take a close look at this area, externally mine didn't look that bad at all. Once I started cutting, my heart sank.
I am sorry to hear you found the tin worm, but I guarantee you will feel really good about the car once you have taken care of it. Just try not to end up in while-you're-in-there purgatory too!!
#83
Thread Starter
RL Community Team
Rennlist Member
Rennlist Member
Joined: May 2004
Posts: 3,332
Likes: 165
From: Toronto

I am about 60% done with the wheels… Two are totally done, and I am working on the third.
I took the opportunity to disassemble the steering rack, inspect parts for wear and then fix/clean as necessary. I am finding that overall I have a lot to be happy about with this car, and the steering rack condition can be added to that list. The pressure block was pristine with no detectable wear (oftentimes these seem to develop a ridge from the rack, due to low grease levels and perhaps dirt I suppose). The rack and pinion looked perfect as did the bearings. So, I just had to clean everything up, re-pack the bearings and re-assemble. The rack feels very “tight” and smooth on the bench:


I have a new set of “turbo” ties rods that will go on, but I am going to install the rack into the car first, and then add the tie rods after. The only reason for this is that I am working alone and the rack is a weird item to manage on your own (I have a plan though – shouldn’t be a big deal, but leaving the weight of the rods off will be helpful).
I have also been putting the front-end bodywork back together and am almost done there. A key part of any suspension pan replacement is dealing with the turn indicator lenses!
I find that the plastic lenses respond very well to the types of polish one uses on paint. I used my trusty Sure Finish polish with a micro fiber towel and simply polished them by hand. I tried to capture the before and after in pictures. However, it is very difficult to see the difference in the photo, whereas in real life, it is night and day. The "before lens" is on the left, and the polished one is on the right in each picture:



The lenses basically look new now.
I took the opportunity to disassemble the steering rack, inspect parts for wear and then fix/clean as necessary. I am finding that overall I have a lot to be happy about with this car, and the steering rack condition can be added to that list. The pressure block was pristine with no detectable wear (oftentimes these seem to develop a ridge from the rack, due to low grease levels and perhaps dirt I suppose). The rack and pinion looked perfect as did the bearings. So, I just had to clean everything up, re-pack the bearings and re-assemble. The rack feels very “tight” and smooth on the bench:


I have a new set of “turbo” ties rods that will go on, but I am going to install the rack into the car first, and then add the tie rods after. The only reason for this is that I am working alone and the rack is a weird item to manage on your own (I have a plan though – shouldn’t be a big deal, but leaving the weight of the rods off will be helpful).
I have also been putting the front-end bodywork back together and am almost done there. A key part of any suspension pan replacement is dealing with the turn indicator lenses!




The lenses basically look new now.
Last edited by 500; 12-10-2010 at 07:37 PM. Reason: typos...
#85
Thread Starter
RL Community Team
Rennlist Member
Rennlist Member
Joined: May 2004
Posts: 3,332
Likes: 165
From: Toronto

The progress of this project has slipped into a very funny state. I am so busy that I tend to cram in little bits of work at all sorts of odd times. For example, I'll wake up at 5 am and do 30 minutes of work. This is horribly inefficient as I find I usually spend 10 or so minutes just figuring out what to do. Another result of all this is that I tend to jump around - tackling any particular job that looks doable.
As such, it's not a lot of fun the way taking a few hours on a Saturday afternoon to really "get into" the job at hand. Literally, I will spend 10 minutes on sanding a wheel or something, and then have to stop.
But it shows me clearly how inexorable little steps become, as the car is getting there. Those that read this from the start may recall that this all began with me wanting to change my spring plate bushings. Well, this morning, while my wife was out running a few errands with my little guy, I managed to do one side.
In keeping with my preference for a stock ride, I went with ER rubber for the back as well. The difficulty with replacing spring plate bushings is that the operating principle is that the outer and inner boundaries remain static. On the OE bushings, the inner surface was bonded (somehow) to the spring plate tube, and the outer was just compressed tightly in place. It is a clever design, as at some point, the outer can slip, prevent bushing tears. But the idea is that the bushing does not slip under normal conditions, rather the rubber twists and the suspension moves. So, the issue is how to bond replacements. The consensus is "super glue" (aka alpha cyanoacrylate cement). It has always sounded a little doubtful to me, but apparently it does work...
Anyway, I found what I believe is the best ACC-derivative product out there, Loctite 380 "Black Max". If price is any indication, then this stuff should rock:

Actually, it is a very simple job. I had previously coated the inside of the torsion tube with the rust preventative (it looked great in there, just wanted to be extra-cautious. To prep the bushings I sanded the inner surfaces with P600. I also chased the threads in the chassis as they had some paint in them.

If you buy ER bushings now, you will get a set of extra-long M10 bolts to help press the whole thing in. Mine must have been one the last sets before this enhancement. So, instead of doing what the cool kids do and get longer bolts, I instead chose to first only glue the inner bushing. then I used the standard bolts with the spring plate cover to press it it. THEN I glued the outer bushing on, and repeated the pressing operation with the standard bolts. Easy-peasy as my little guy would say.
1) Glue the inner half on:

2) Just after pressing it on:

3) That rust-colored stuff on the upper right boss is just the copper anti-sieze I use... I have now glued the outer on:

4) Starting to press it on:

Ta-da. The lower left bolt (and spacer) will be added later after the glue has fully cured.

This is how it looked before, just for interest:

Of course, I only got one side done...
20 min job.
As such, it's not a lot of fun the way taking a few hours on a Saturday afternoon to really "get into" the job at hand. Literally, I will spend 10 minutes on sanding a wheel or something, and then have to stop.
But it shows me clearly how inexorable little steps become, as the car is getting there. Those that read this from the start may recall that this all began with me wanting to change my spring plate bushings. Well, this morning, while my wife was out running a few errands with my little guy, I managed to do one side.
In keeping with my preference for a stock ride, I went with ER rubber for the back as well. The difficulty with replacing spring plate bushings is that the operating principle is that the outer and inner boundaries remain static. On the OE bushings, the inner surface was bonded (somehow) to the spring plate tube, and the outer was just compressed tightly in place. It is a clever design, as at some point, the outer can slip, prevent bushing tears. But the idea is that the bushing does not slip under normal conditions, rather the rubber twists and the suspension moves. So, the issue is how to bond replacements. The consensus is "super glue" (aka alpha cyanoacrylate cement). It has always sounded a little doubtful to me, but apparently it does work...
Anyway, I found what I believe is the best ACC-derivative product out there, Loctite 380 "Black Max". If price is any indication, then this stuff should rock:

Actually, it is a very simple job. I had previously coated the inside of the torsion tube with the rust preventative (it looked great in there, just wanted to be extra-cautious. To prep the bushings I sanded the inner surfaces with P600. I also chased the threads in the chassis as they had some paint in them.

If you buy ER bushings now, you will get a set of extra-long M10 bolts to help press the whole thing in. Mine must have been one the last sets before this enhancement. So, instead of doing what the cool kids do and get longer bolts, I instead chose to first only glue the inner bushing. then I used the standard bolts with the spring plate cover to press it it. THEN I glued the outer bushing on, and repeated the pressing operation with the standard bolts. Easy-peasy as my little guy would say.
1) Glue the inner half on:

2) Just after pressing it on:

3) That rust-colored stuff on the upper right boss is just the copper anti-sieze I use... I have now glued the outer on:

4) Starting to press it on:

Ta-da. The lower left bolt (and spacer) will be added later after the glue has fully cured.

This is how it looked before, just for interest:

Of course, I only got one side done...
20 min job.
Last edited by 500; 12-12-2010 at 09:20 AM. Reason: typos...
#88
Thread Starter
RL Community Team
Rennlist Member
Rennlist Member
Joined: May 2004
Posts: 3,332
Likes: 165
From: Toronto

The hard oil lines…
Those pricey hard oil lines often fall afoul of poor jacking/lifting practices and get crushed. Mine were no exception. One line was partially crushed at both the front and rear, the other was crushed “only” at the rear. In all cases, they were not fully crushed, but it certainly is not an ideal situation. Also of concern, one of the lines showed extensive signs of someone having tried to un-crush it with a pair of sharp-toothed pliers. There were significant, deep-looking gouges.
I was able to reverse the crushing by heating the lines gently with a MAPP torch while pressurizing the lines with compressed air (I used 75 psi). It is important to note that you want to first make sure the inside of the lines are very clean.
I found a plastic plumbing cap that I drilled and tapped for an air connector. It was a tight fit around the oil line end. I capped the other end with another cap, some hose and some clamps… just whatever works to seal it off. A little air leakage is fine, as long as it holds decent pressure.
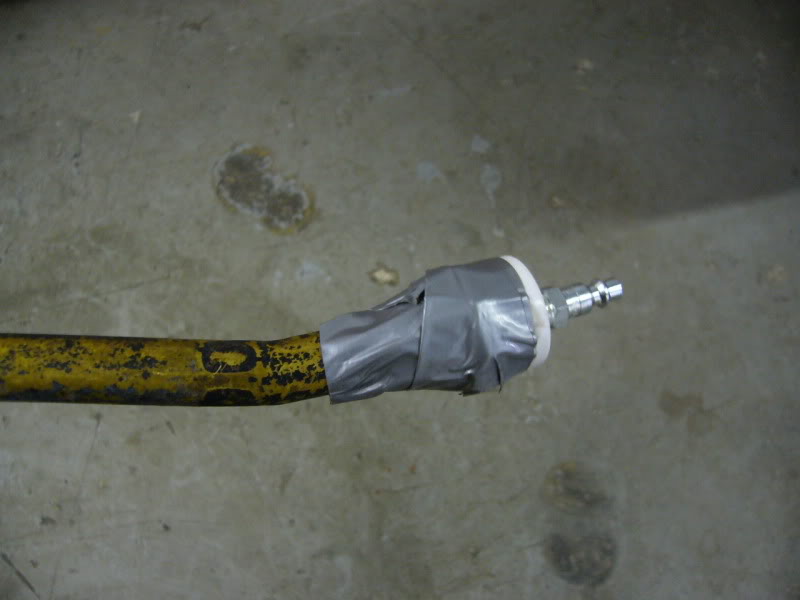

I did not have my camera with me when I repaired the bad spots, so I only can show how this worked with the least-bad damage. Here is the dent in the tube before:

The heating is not hard, just make sure you move the flame constantly and keep a keen eye on things. When the tubing gets pliable enough, the dent will gradually push back out.

Here is that same location after:

Once the dents were repaired, I considered what to do about the gouge marks from the pliers. On the one hand, they had held 75 psi air pressure, but on the other hand, I was concerned about them acting as a stress riser over the long haul (OK, probably too conservative of a bent there). Anyway, what I decided to do was silver-braze a few sections of split copper tubing along the length of tube with the mauling. I suppose it looks a little ghetto, and I’m sure someone might assume that it is actually a repair for a broken tube, but I think I will feel better knowing it is solid:

To finish the tubes I glass-bead blasted them and then painted them with some of my left-over Glasurit clear! Let’s see how that holds up!

I over-wrapped the rubber protection pieces with high temperature silicone wrap (good for 400ºF) to freshen things up a bit. I stripped and powder-coated the original clamps while I was at it:

Next up was popping the lines up onto the car. It went smoothly, I temporarily attached the thermostat to help align everything. Now it is ready for the rocker trim to go back on. Then I can move over to the driver’s side and do the bushings and rocker trim there. It will be nice to have those long rocker trims out of the basement and back onto the car as I always worry a tiny bit about things like that lying around, waiting for some accident to happen (even though they are well wrapped up)!
Those pricey hard oil lines often fall afoul of poor jacking/lifting practices and get crushed. Mine were no exception. One line was partially crushed at both the front and rear, the other was crushed “only” at the rear. In all cases, they were not fully crushed, but it certainly is not an ideal situation. Also of concern, one of the lines showed extensive signs of someone having tried to un-crush it with a pair of sharp-toothed pliers. There were significant, deep-looking gouges.
I was able to reverse the crushing by heating the lines gently with a MAPP torch while pressurizing the lines with compressed air (I used 75 psi). It is important to note that you want to first make sure the inside of the lines are very clean.
I found a plastic plumbing cap that I drilled and tapped for an air connector. It was a tight fit around the oil line end. I capped the other end with another cap, some hose and some clamps… just whatever works to seal it off. A little air leakage is fine, as long as it holds decent pressure.
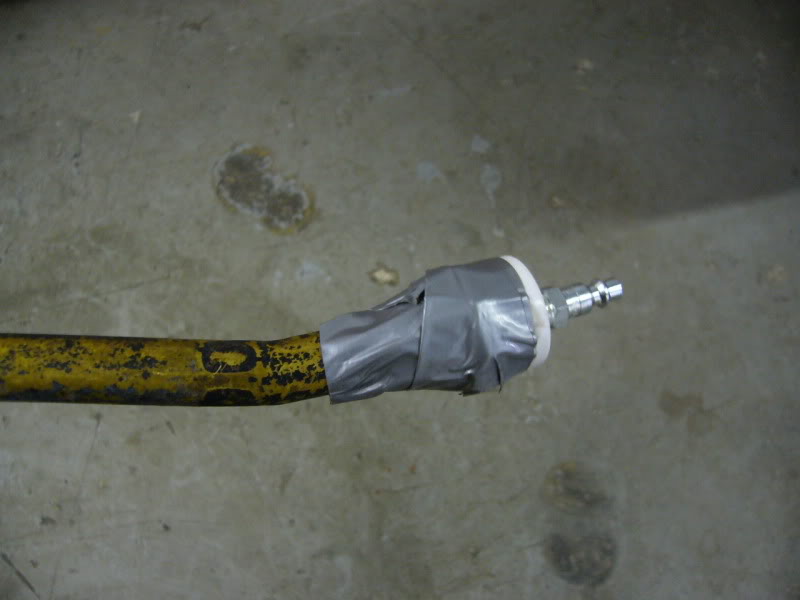

I did not have my camera with me when I repaired the bad spots, so I only can show how this worked with the least-bad damage. Here is the dent in the tube before:

The heating is not hard, just make sure you move the flame constantly and keep a keen eye on things. When the tubing gets pliable enough, the dent will gradually push back out.

Here is that same location after:

Once the dents were repaired, I considered what to do about the gouge marks from the pliers. On the one hand, they had held 75 psi air pressure, but on the other hand, I was concerned about them acting as a stress riser over the long haul (OK, probably too conservative of a bent there). Anyway, what I decided to do was silver-braze a few sections of split copper tubing along the length of tube with the mauling. I suppose it looks a little ghetto, and I’m sure someone might assume that it is actually a repair for a broken tube, but I think I will feel better knowing it is solid:

To finish the tubes I glass-bead blasted them and then painted them with some of my left-over Glasurit clear! Let’s see how that holds up!

I over-wrapped the rubber protection pieces with high temperature silicone wrap (good for 400ºF) to freshen things up a bit. I stripped and powder-coated the original clamps while I was at it:

Next up was popping the lines up onto the car. It went smoothly, I temporarily attached the thermostat to help align everything. Now it is ready for the rocker trim to go back on. Then I can move over to the driver’s side and do the bushings and rocker trim there. It will be nice to have those long rocker trims out of the basement and back onto the car as I always worry a tiny bit about things like that lying around, waiting for some accident to happen (even though they are well wrapped up)!

#90
Thread Starter
RL Community Team
Rennlist Member
Rennlist Member
Joined: May 2004
Posts: 3,332
Likes: 165
From: Toronto