Anyone here polished their plastic headlights before?
#31

i can't say i am 100% sure; it is the oem X97 shifter. bought it off a really kind older gentleman on kijiji. my buddy sent me the link the other day so i just grabbed it.
i figure i can just mask off areas with tape, start at approx 1000grit (maybe 800) -> 2000grit and then finish off with metal polish. and then use some leather restore stuff for the leather bits.
i figure i can just mask off areas with tape, start at approx 1000grit (maybe 800) -> 2000grit and then finish off with metal polish. and then use some leather restore stuff for the leather bits.
#32

Looks like solid aluminum. Don't quote me 
If you can take it apart, remove the leather, lightly sand out the scratches with sandpaper, buy this
http://www.caswellcanada.ca/shop/pro...&cat=95&page=1
It would look awesome highly polished. Very time consuming!

If you can take it apart, remove the leather, lightly sand out the scratches with sandpaper, buy this
http://www.caswellcanada.ca/shop/pro...&cat=95&page=1
It would look awesome highly polished. Very time consuming!
#33

My **** was this style (but in black leather)
http://www.suncoastparts.com/product..._Code=996knobs
I polished it using a dremel. I cut up 400, 800, 1000, 1500 grit sandpaper into small disks and used the dremel to sand the brushed almunimum to a shine. I then switched to a dremel polishing wheel with a polishing compound. Finally used a metal polish.
I am very happy with the results. It becomes dull after a few months, but 2 minutes with a metal polish (like Mothers etc.) brings back the shine.
- I used electrical tape to mask off the leather. Electrical tape is flexible enough to follow the edges well. But be careful since it is easy to sand through the tape
- I taped the back of the sand paper with duct tape before cutting the disks. That made them a little more rigid and much more durable.
- Another tip is to sand the edges of each sanding disk against a sheet of course sandpaper using the dremel (i.e. after the disk is installed ). That way you end up with a perfectly round disk
- Probably didn't have to start as low as 400 grit but I had it handy
- In hindsight it might have been easier to just sand by hand. But with the dremel it was pretty easy to be precise
#34

this is awesome. thank you kgoertz. the elec. tape idea is brilliant, will use elec tape on bottom layer and then throw some masking tape on top. i may just do the shift **** by hand as its a very small surface area.... otherwise dremel tool/electrinc screwdriver method.
Yes. I did both my shift **** and e-brake handle. I had originally thought the top portion of the **** was plastic (like the horseshoe base) until I scratched it and found out that it was actually brushed aluminum.
My **** was this style (but in black leather)
http://www.suncoastparts.com/product..._Code=996knobs
I polished it using a dremel. I cut up 400, 800, 1000, 1500 grit sandpaper into small disks and used the dremel to sand the brushed almunimum to a shine. I then switched to a dremel polishing wheel with a polishing compound. Finally used a metal polish.
I am very happy with the results. It becomes dull after a few months, but 2 minutes with a metal polish (like Mothers etc.) brings back the shine.
My **** was this style (but in black leather)
http://www.suncoastparts.com/product..._Code=996knobs
I polished it using a dremel. I cut up 400, 800, 1000, 1500 grit sandpaper into small disks and used the dremel to sand the brushed almunimum to a shine. I then switched to a dremel polishing wheel with a polishing compound. Finally used a metal polish.
I am very happy with the results. It becomes dull after a few months, but 2 minutes with a metal polish (like Mothers etc.) brings back the shine.
- I used electrical tape to mask off the leather. Electrical tape is flexible enough to follow the edges well. But be careful since it is easy to sand through the tape
- I taped the back of the sand paper with duct tape before cutting the disks. That made them a little more rigid and much more durable.
- Another tip is to sand the edges of each sanding disk against a sheet of course sandpaper using the dremel (i.e. after the disk is installed ). That way you end up with a perfectly round disk
- Probably didn't have to start as low as 400 grit but I had it handy
- In hindsight it might have been easier to just sand by hand. But with the dremel it was pretty easy to be precise
#35

quick update.
lol i thought this would have taken an hour LMAO boy am i annoyed (as all these projects go).
as some of you know i have my 997.2 conversion in the works and before i am going to install the 997.2 front LED, i couldnt help but notice and get annoyed by a little bit of cloudiness and some scratches (a few deep ones) in the passenger LED (got the light from ebay).
for those of you with deep scratches 800 grit is useless imo, u can go polishing for days and days, i would recemmend you goto home depot and for safety, buy some 600 grit, 400, and even 200 grit sandpaper and a few sanding blocks.
luckily i i had some 600 and 150 (yikes) grit left over from my honda projects from yesteryear (lol literally decade old sandpaper) and i got really fed up with the amount of time it was taking and used 150 (on a sanding block) to speed things up. before going 150 i did spend a good time using 600 on a sanding block but it wasnt doing much at all for the scratches.
you do get a little scared going that coarse at 150 but the remaining tidbits of the tough scratches were easily removed, and i went back to went back to giving a VERY thorough 600 -> 800 -> 1000 sanding.
going to finish off with 2000 grit apply the compound and then show you guys the results.
lol i thought this would have taken an hour LMAO boy am i annoyed (as all these projects go).
as some of you know i have my 997.2 conversion in the works and before i am going to install the 997.2 front LED, i couldnt help but notice and get annoyed by a little bit of cloudiness and some scratches (a few deep ones) in the passenger LED (got the light from ebay).
for those of you with deep scratches 800 grit is useless imo, u can go polishing for days and days, i would recemmend you goto home depot and for safety, buy some 600 grit, 400, and even 200 grit sandpaper and a few sanding blocks.
luckily i i had some 600 and 150 (yikes) grit left over from my honda projects from yesteryear (lol literally decade old sandpaper) and i got really fed up with the amount of time it was taking and used 150 (on a sanding block) to speed things up. before going 150 i did spend a good time using 600 on a sanding block but it wasnt doing much at all for the scratches.
you do get a little scared going that coarse at 150 but the remaining tidbits of the tough scratches were easily removed, and i went back to went back to giving a VERY thorough 600 -> 800 -> 1000 sanding.
going to finish off with 2000 grit apply the compound and then show you guys the results.
#37

600 grit sanding - cloudy

800 grit sanding - cloudy but getting more clear

1000 grit sanding - a few passes

2000 grit - 2nd pass of wet sanding, took a pic right away without wiping it off

applied the headlight polish via my simonize oribital buffer, the attached 3m kit would have taken wayyyy too long just not fast enough imo.
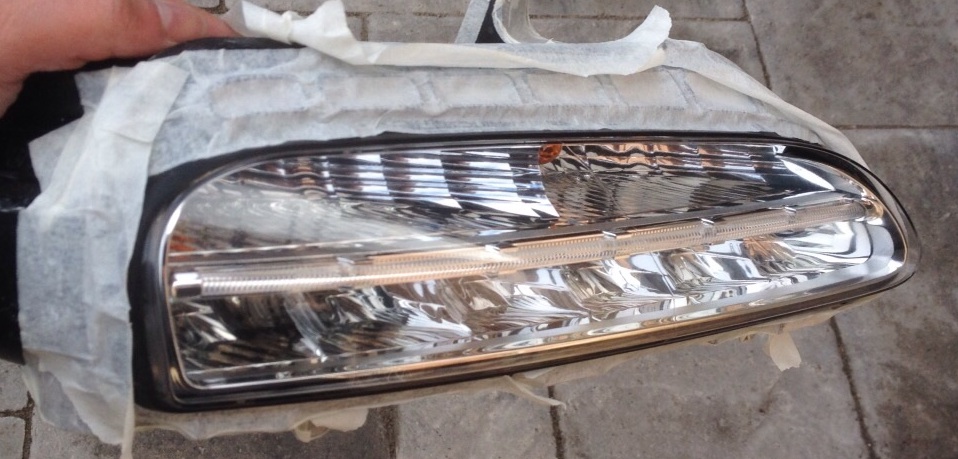
2nd pass of headlight polish on passenger lens. looking really really sharp again.

threw on some headlight polish on the driver led, this lens was mint condition and is 3 years newer then the passenger led.

old and new lens are pretty much the same condition/quality now.

i'll have my body shop throw a 2 coats of clear before the lenses get mounted and ill have the lenses 3M'd like the rest of the front end shortly after.
THANKS OP for bringing this to my attention. this was bothering me for so long and i never knew these things could be fixed... for a while i even considered buying another LED.

800 grit sanding - cloudy but getting more clear

1000 grit sanding - a few passes

2000 grit - 2nd pass of wet sanding, took a pic right away without wiping it off

applied the headlight polish via my simonize oribital buffer, the attached 3m kit would have taken wayyyy too long just not fast enough imo.
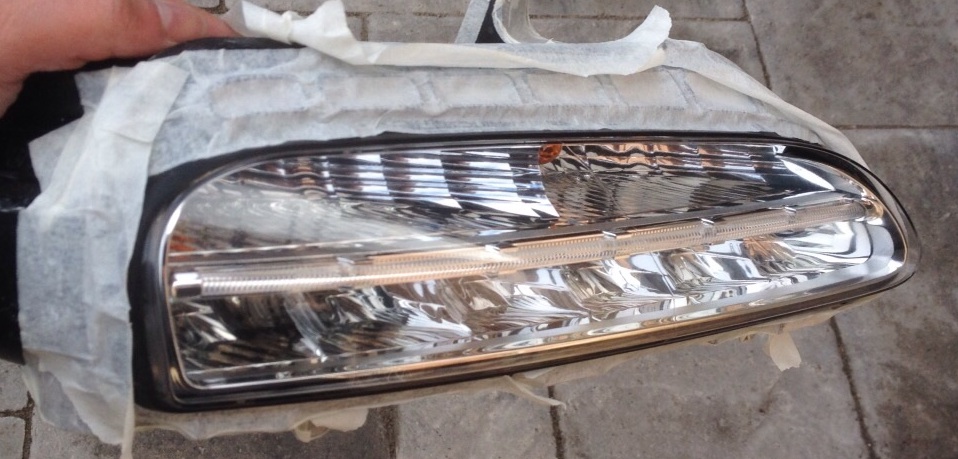
2nd pass of headlight polish on passenger lens. looking really really sharp again.

threw on some headlight polish on the driver led, this lens was mint condition and is 3 years newer then the passenger led.

old and new lens are pretty much the same condition/quality now.

i'll have my body shop throw a 2 coats of clear before the lenses get mounted and ill have the lenses 3M'd like the rest of the front end shortly after.
THANKS OP for bringing this to my attention. this was bothering me for so long and i never knew these things could be fixed... for a while i even considered buying another LED.
Last edited by myw; 03-30-2015 at 10:09 PM.
#38

thank you well noted. i'll have this done sometime soon as well.
#40

Nice job Myw!
I've also been working on my headlights and have one finished. It isn't quite perfect though. When viewed at the right angle I can still see a few scratches. It isn't really a huge problem since the Lamin-x that I applied also shows scratches when looking very closely at the right angle.
I only started with 800 grit so it could just be that I didn't go low enough. But I'm finding it really hard to see the scratches when sanding to know if they have been removed. Did you find any tricks for this?
I found polishing aluminum to be much easier since it is pretty easy to see the scratches from the previous grit. For plastic it looks like the only solution is to just spend more time sanding each layer than it really needs. But that is pretty time consuming.
I've also been working on my headlights and have one finished. It isn't quite perfect though. When viewed at the right angle I can still see a few scratches. It isn't really a huge problem since the Lamin-x that I applied also shows scratches when looking very closely at the right angle.
I only started with 800 grit so it could just be that I didn't go low enough. But I'm finding it really hard to see the scratches when sanding to know if they have been removed. Did you find any tricks for this?
I found polishing aluminum to be much easier since it is pretty easy to see the scratches from the previous grit. For plastic it looks like the only solution is to just spend more time sanding each layer than it really needs. But that is pretty time consuming.
#41

with 800 grit, i would do 10-20 wet sand passes, then wipe the lens dry with a microfibre cloth and look carefully.... then remind yourself of those trouble areas.
over time the scratches do get tiny bit smaller so it makes it tougher to see, the water and sanded plastic does not help re visibility so the water+wipe method is a must imo. otherwise you can be be polishing blindly for hours on end.
dropping off the LEDs for clearcoating today. going to also see get the 997.2 silver grills clearcoated as well (hate it when they chip)
over time the scratches do get tiny bit smaller so it makes it tougher to see, the water and sanded plastic does not help re visibility so the water+wipe method is a must imo. otherwise you can be be polishing blindly for hours on end.
dropping off the LEDs for clearcoating today. going to also see get the 997.2 silver grills clearcoated as well (hate it when they chip)
#42

Something interesting I found with my sand blasted/pitted headlights, I prepped them with the 3'000, 4'000, 5'000 plastic polishing fabric sheets I bought in 1986 at EAA Oshkosh, they are made by a company called Micro-Mesh, and were intended to be used for aircraft Plexiglas windshields.
I knocked down any burrs from the pitting with the fabric and sanding block, wet sanding of course.
I thought about trying to sand out the pitting but that would have taken way too much effort so I didn't bother.
I then applied the thick XPEL headlight protection film on the headlights, this is where I was astounded that the sand blasted pitting disappeared as the adhesive glue flowed into the pitting under the heat I was applying with a heat gun to conform the film to the curvature of the headlight lens.
Be careful not to overheat else you risk distort the film or the headlight lens, or both!!
My headlights now looked brand new after the film was applied two years ago.
I knocked down any burrs from the pitting with the fabric and sanding block, wet sanding of course.
I thought about trying to sand out the pitting but that would have taken way too much effort so I didn't bother.
I then applied the thick XPEL headlight protection film on the headlights, this is where I was astounded that the sand blasted pitting disappeared as the adhesive glue flowed into the pitting under the heat I was applying with a heat gun to conform the film to the curvature of the headlight lens.
Be careful not to overheat else you risk distort the film or the headlight lens, or both!!
My headlights now looked brand new after the film was applied two years ago.
#44

I just finished my second headlight today and am finally (mostly) happy with the results. It was definitely harder than I had expected and I wish I originally had the knowledge that I have now. So I thought it was worth sharing 
For the first headlight I sanded by hand starting with 800 grit. I believe I used 800, 1000, 1500 and 2000 grit sandpaper but I didn't use a sanding block. I did the work inside with indirect sunlight and then applied pre-cut Lamin-X film. I wasn't really happy with the results though since I could still see some fine scratches when looking closely and at the right angle. Similar to swirls in paint when looking under bright lights.
It was a lot of work. The headlight looks great overall and most people wouldn't notice the light scratches. But not as good as I'd like.
For the second headlight I used the Simonize kit which consisted of 3 inch (?) sanding disks and polish. The discs were 800, 1000 and 2000 grit. I worked outside on this one which made it much easier to see the scratches left by previous grits. But the problem (IMO) is that all of the sanding was done with a machine with the same pattern which makes it really hard to know when you have sanded enough especially between the 800 and 1000 grit. I finished with the included polish.
There were still scratches though and I wasn't happy. In hindsight it was probably because I hadn't polished long enough. I had some new clear-coat spray cans handy so I tried to clearcoat to see if that would fill in the scratches. It did. But the clearcoat finish wasn't ideal so I waited a few days for it to harden before polishing it smooth.
That was a mistake. I should have waited a week. Most of the headlight was fine and looked great, but the clearcoat had cracked slightly in a few areas. I assume that I hadn't waited long enough.
So I started trying to correct the cracks but eventually gave up and went back to sanding from scratch. But this time I had the technique down.
Probably still took about 3 hours to sand and polish but I wasn't in a hurry.
My steps were
I then applied the Lamin-X film. It still looks pretty cloudy in a few places but that will clear. It took over 2 weeks for the first one to clear.
I'm actually not that happy with the Lamin-X film though. It isn't quite big enough and the washer cut-out is larger than the washer. So part of the headlight is still exposed to the sun. I will be applying headlight protector to those areas. It is also pretty tricky to install mostly because the 996 headlight is so large and an irregular shape. It probably took 1/2 hour to install and a bunch of attempts to align it properly.
I like the clearcoat idea though. If I have to do this again I will sand by hand and take it to a body shop for a quick clearcoat. Or use a rattle can again but wait at least a week before attempting to polish. I'd probably still use the Lamin-X even if the fit wasn't perfect since the car is my DD. On a show-car I would stick with just a clear coat.
Picture is before I applied the Lamin-x. Hopefully I never have to do this again on this car.

For the first headlight I sanded by hand starting with 800 grit. I believe I used 800, 1000, 1500 and 2000 grit sandpaper but I didn't use a sanding block. I did the work inside with indirect sunlight and then applied pre-cut Lamin-X film. I wasn't really happy with the results though since I could still see some fine scratches when looking closely and at the right angle. Similar to swirls in paint when looking under bright lights.
It was a lot of work. The headlight looks great overall and most people wouldn't notice the light scratches. But not as good as I'd like.
For the second headlight I used the Simonize kit which consisted of 3 inch (?) sanding disks and polish. The discs were 800, 1000 and 2000 grit. I worked outside on this one which made it much easier to see the scratches left by previous grits. But the problem (IMO) is that all of the sanding was done with a machine with the same pattern which makes it really hard to know when you have sanded enough especially between the 800 and 1000 grit. I finished with the included polish.
There were still scratches though and I wasn't happy. In hindsight it was probably because I hadn't polished long enough. I had some new clear-coat spray cans handy so I tried to clearcoat to see if that would fill in the scratches. It did. But the clearcoat finish wasn't ideal so I waited a few days for it to harden before polishing it smooth.
That was a mistake. I should have waited a week. Most of the headlight was fine and looked great, but the clearcoat had cracked slightly in a few areas. I assume that I hadn't waited long enough.
So I started trying to correct the cracks but eventually gave up and went back to sanding from scratch. But this time I had the technique down.
Probably still took about 3 hours to sand and polish but I wasn't in a hurry.
My steps were
- Remove the headlight from the car and mount on a portable work table. Remove the headlight washer by forcing ~20psi through the headlight washer tube. Actually the first time I tried to pry it up and broke the tabs. I can report that fixing the headlight washer cover with Goop works well
- Use a sanding pad to apply even force (instead of just holding the paper). My sanding pad was a foam polishing pad with a plastic handle that I wrapped the paper around. The foam allowed for pretty constant pressure while still providing a fairly large surface area to reduce the effort.
- Sanding by hand using 1/3 sheets of wet/dry paper. Wet sanding only
- After each sanding, wipe the plastic with a wet towel and then wipe dry. Then inspect in sunlight and find any scratches in the perpendicular direction. Cleaning between each sanding was critical to see if any scratches were missed.
- Switch directions for each grit. I used ~2 sheets of 1/3 paper for each grit for one headlight.
- I started with 800 grit. It was enough for most of the light although I did drop to 400 for a few deeper scratches.
- Followed by 1000, 1500, 2000 and 2500 grit. Cleaning the headlight between each and and marking any remaining scratches to fix with a dry erase marker. The scratches were much easier with bright sunlight.
- I then switched to Meguiars plastic polish. I tried polishing by hand using a polishing pad but quickly gave up. Then switched to my dual action orbital polisher with at least 15 passes. Definitely better but still scratches. I switched to a circular polisher/sander using the same pad with with a high RPM checking constantly to make sure I wasn't overheating it. No problems with heat. The polish removed the last scratches from the 2500 grit, but it took quite a bit longer than I had expected to get them all.
- I cleaned the headlights and inspected in the sunlight several times when polishing.
I then applied the Lamin-X film. It still looks pretty cloudy in a few places but that will clear. It took over 2 weeks for the first one to clear.
I'm actually not that happy with the Lamin-X film though. It isn't quite big enough and the washer cut-out is larger than the washer. So part of the headlight is still exposed to the sun. I will be applying headlight protector to those areas. It is also pretty tricky to install mostly because the 996 headlight is so large and an irregular shape. It probably took 1/2 hour to install and a bunch of attempts to align it properly.
I like the clearcoat idea though. If I have to do this again I will sand by hand and take it to a body shop for a quick clearcoat. Or use a rattle can again but wait at least a week before attempting to polish. I'd probably still use the Lamin-X even if the fit wasn't perfect since the car is my DD. On a show-car I would stick with just a clear coat.
Picture is before I applied the Lamin-x. Hopefully I never have to do this again on this car.
#45

looks great and nice write up too.
dont forget that if you get it clear coated very likely they will re-sand it back down to 800/1000. they will need to coarse it up a bit otherwise there is a chance the clearcoat wont stick.
dont forget that if you get it clear coated very likely they will re-sand it back down to 800/1000. they will need to coarse it up a bit otherwise there is a chance the clearcoat wont stick.
I just finished my second headlight today and am finally (mostly) happy with the results. It was definitely harder than I had expected and I wish I originally had the knowledge that I have now. So I thought it was worth sharing 
For the first headlight I sanded by hand starting with 800 grit. I believe I used 800, 1000, 1500 and 2000 grit sandpaper but I didn't use a sanding block. I did the work inside with indirect sunlight and then applied pre-cut Lamin-X film. I wasn't really happy with the results though since I could still see some fine scratches when looking closely and at the right angle. Similar to swirls in paint when looking under bright lights.
It was a lot of work. The headlight looks great overall and most people wouldn't notice the light scratches. But not as good as I'd like.
For the second headlight I used the Simonize kit which consisted of 3 inch (?) sanding disks and polish. The discs were 800, 1000 and 2000 grit. I worked outside on this one which made it much easier to see the scratches left by previous grits. But the problem (IMO) is that all of the sanding was done with a machine with the same pattern which makes it really hard to know when you have sanded enough especially between the 800 and 1000 grit. I finished with the included polish.
There were still scratches though and I wasn't happy. In hindsight it was probably because I hadn't polished long enough. I had some new clear-coat spray cans handy so I tried to clearcoat to see if that would fill in the scratches. It did. But the clearcoat finish wasn't ideal so I waited a few days for it to harden before polishing it smooth.
That was a mistake. I should have waited a week. Most of the headlight was fine and looked great, but the clearcoat had cracked slightly in a few areas. I assume that I hadn't waited long enough.
So I started trying to correct the cracks but eventually gave up and went back to sanding from scratch. But this time I had the technique down.
Probably still took about 3 hours to sand and polish but I wasn't in a hurry.
My steps were
I then applied the Lamin-X film. It still looks pretty cloudy in a few places but that will clear. It took over 2 weeks for the first one to clear.
I'm actually not that happy with the Lamin-X film though. It isn't quite big enough and the washer cut-out is larger than the washer. So part of the headlight is still exposed to the sun. I will be applying headlight protector to those areas. It is also pretty tricky to install mostly because the 996 headlight is so large and an irregular shape. It probably took 1/2 hour to install and a bunch of attempts to align it properly.
I like the clearcoat idea though. If I have to do this again I will sand by hand and take it to a body shop for a quick clearcoat. Or use a rattle can again but wait at least a week before attempting to polish. I'd probably still use the Lamin-X even if the fit wasn't perfect since the car is my DD. On a show-car I would stick with just a clear coat.
Picture is before I applied the Lamin-x. Hopefully I never have to do this again on this car.

For the first headlight I sanded by hand starting with 800 grit. I believe I used 800, 1000, 1500 and 2000 grit sandpaper but I didn't use a sanding block. I did the work inside with indirect sunlight and then applied pre-cut Lamin-X film. I wasn't really happy with the results though since I could still see some fine scratches when looking closely and at the right angle. Similar to swirls in paint when looking under bright lights.
It was a lot of work. The headlight looks great overall and most people wouldn't notice the light scratches. But not as good as I'd like.
For the second headlight I used the Simonize kit which consisted of 3 inch (?) sanding disks and polish. The discs were 800, 1000 and 2000 grit. I worked outside on this one which made it much easier to see the scratches left by previous grits. But the problem (IMO) is that all of the sanding was done with a machine with the same pattern which makes it really hard to know when you have sanded enough especially between the 800 and 1000 grit. I finished with the included polish.
There were still scratches though and I wasn't happy. In hindsight it was probably because I hadn't polished long enough. I had some new clear-coat spray cans handy so I tried to clearcoat to see if that would fill in the scratches. It did. But the clearcoat finish wasn't ideal so I waited a few days for it to harden before polishing it smooth.
That was a mistake. I should have waited a week. Most of the headlight was fine and looked great, but the clearcoat had cracked slightly in a few areas. I assume that I hadn't waited long enough.
So I started trying to correct the cracks but eventually gave up and went back to sanding from scratch. But this time I had the technique down.
Probably still took about 3 hours to sand and polish but I wasn't in a hurry.
My steps were
- Remove the headlight from the car and mount on a portable work table. Remove the headlight washer by forcing ~20psi through the headlight washer tube. Actually the first time I tried to pry it up and broke the tabs. I can report that fixing the headlight washer cover with Goop works well
- Use a sanding pad to apply even force (instead of just holding the paper). My sanding pad was a foam polishing pad with a plastic handle that I wrapped the paper around. The foam allowed for pretty constant pressure while still providing a fairly large surface area to reduce the effort.
- Sanding by hand using 1/3 sheets of wet/dry paper. Wet sanding only
- After each sanding, wipe the plastic with a wet towel and then wipe dry. Then inspect in sunlight and find any scratches in the perpendicular direction. Cleaning between each sanding was critical to see if any scratches were missed.
- Switch directions for each grit. I used ~2 sheets of 1/3 paper for each grit for one headlight.
- I started with 800 grit. It was enough for most of the light although I did drop to 400 for a few deeper scratches.
- Followed by 1000, 1500, 2000 and 2500 grit. Cleaning the headlight between each and and marking any remaining scratches to fix with a dry erase marker. The scratches were much easier with bright sunlight.
- I then switched to Meguiars plastic polish. I tried polishing by hand using a polishing pad but quickly gave up. Then switched to my dual action orbital polisher with at least 15 passes. Definitely better but still scratches. I switched to a circular polisher/sander using the same pad with with a high RPM checking constantly to make sure I wasn't overheating it. No problems with heat. The polish removed the last scratches from the 2500 grit, but it took quite a bit longer than I had expected to get them all.
- I cleaned the headlights and inspected in the sunlight several times when polishing.
I then applied the Lamin-X film. It still looks pretty cloudy in a few places but that will clear. It took over 2 weeks for the first one to clear.
I'm actually not that happy with the Lamin-X film though. It isn't quite big enough and the washer cut-out is larger than the washer. So part of the headlight is still exposed to the sun. I will be applying headlight protector to those areas. It is also pretty tricky to install mostly because the 996 headlight is so large and an irregular shape. It probably took 1/2 hour to install and a bunch of attempts to align it properly.
I like the clearcoat idea though. If I have to do this again I will sand by hand and take it to a body shop for a quick clearcoat. Or use a rattle can again but wait at least a week before attempting to polish. I'd probably still use the Lamin-X even if the fit wasn't perfect since the car is my DD. On a show-car I would stick with just a clear coat.
Picture is before I applied the Lamin-x. Hopefully I never have to do this again on this car.