I'm f*cked - You're not going to believe this
#32
Nordschleife Master

I would not attempt to weld this piece I am afraid.
Location is horrid for welding! Plus with the block being alusil in this spot....
I would recommend that you JB Weld it as well.
Location is horrid for welding! Plus with the block being alusil in this spot....
I would recommend that you JB Weld it as well.
#33
Three Wheelin'

If you can get it to a good welder, have him weld one of these to the block-
http://www.summitracing.com/parts/EA...8ERL/?rtype=10
try to not weld on the hex so you can use a backup wrench in the future
Then you use an A.N. cap on it- seals on the taper- takes very little to tighten it,
don't over do it.
http://www.summitracing.com/parts/EA...8ERL/?rtype=10
http://www.summitracing.com/parts/EA...8ERL/?rtype=10
try to not weld on the hex so you can use a backup wrench in the future
Then you use an A.N. cap on it- seals on the taper- takes very little to tighten it,
don't over do it.
http://www.summitracing.com/parts/EA...8ERL/?rtype=10
Last edited by Jim Devine; 03-17-2011 at 02:01 AM. Reason: added cap
#34
Rennlist Member

I would go for the least invasive procedure first, that being JB Weld. It's strong stuff, as long as it can withstand the heat you should be good to go. You can always try welding later if the JB Weld fails. My underlying approach in these cases is to make sure that whatever I do doesn't make the situation worse...
#35
Rest in Peace
Rennlist Member
Rennlist Member
Join Date: May 2006
Location: Bird lover in Sharpsburg
Posts: 9,903
Likes: 0
Received 2 Likes
on
2 Posts

I would go for the least invasive procedure first, that being JB Weld. It's strong stuff, as long as it can withstand the heat you should be good to go. You can always try welding later if the JB Weld fails. My underlying approach in these cases is to make sure that whatever I do doesn't make the situation worse...
If it were my motor, I would pull it, put it on a really good engine stand and take it to a welder that was at least as good as Joe Norman.
George's 928 is one of the better examples that I have seen, why half *** a repair now?
#36
Rennlist Member

You put JB Weld in that hole you may never get it clean enough to get a good weld.
If it were my motor, I would pull it, put it on a really good engine stand and take it to a welder that was at least as good as Joe Norman.
George's 928 is one of the better examples that I have seen, why half *** a repair now?
If it were my motor, I would pull it, put it on a really good engine stand and take it to a welder that was at least as good as Joe Norman.
George's 928 is one of the better examples that I have seen, why half *** a repair now?
#37
Vegas, Baby!
Rennlist Member
Rennlist Member



There is a way to fix this without it being welded, and do a proper job. Use a polymethylmethacrylate composite, it's used on airplanes where drilling or riviting would lessen the strength of the joined parts.
It's called Equilox by Center Forge.
I could and would weld it, with GTAW wA/C current, and pure Argon as a shielding gas. Silica Bronze filler rod. This is the right way to weld it, and forget about it.
George, ask some of the aircraft mechanics if they have Equilox, at the base. They should have. It's nasty stuff. You need stout rubber gloves, and a respirator. You'll tear the base metal before this stuff fails.
P.S. Thanks Greg!
It's called Equilox by Center Forge.
I could and would weld it, with GTAW wA/C current, and pure Argon as a shielding gas. Silica Bronze filler rod. This is the right way to weld it, and forget about it.
George, ask some of the aircraft mechanics if they have Equilox, at the base. They should have. It's nasty stuff. You need stout rubber gloves, and a respirator. You'll tear the base metal before this stuff fails.
P.S. Thanks Greg!
Last edited by polecat702; 03-17-2011 at 02:55 AM. Reason: add a post scrip
#38
Nordschleife Master

JB Weld is the way to go ... 

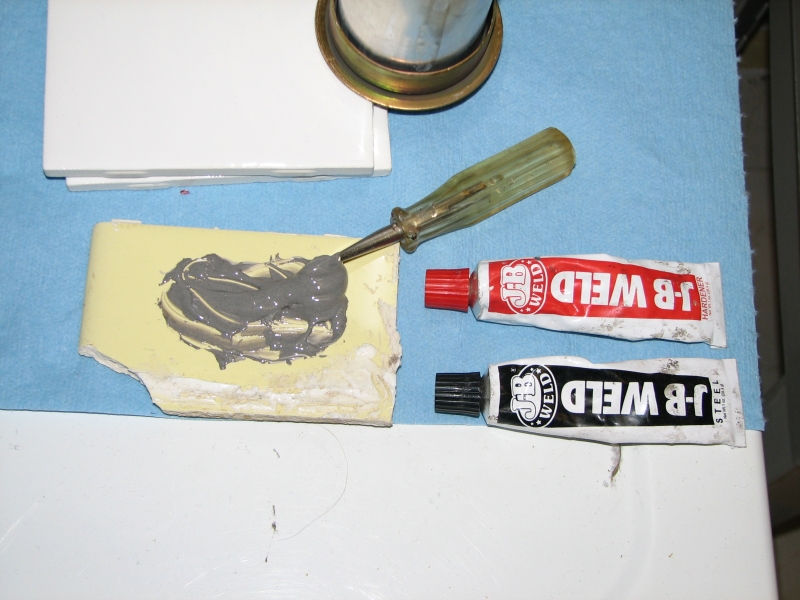


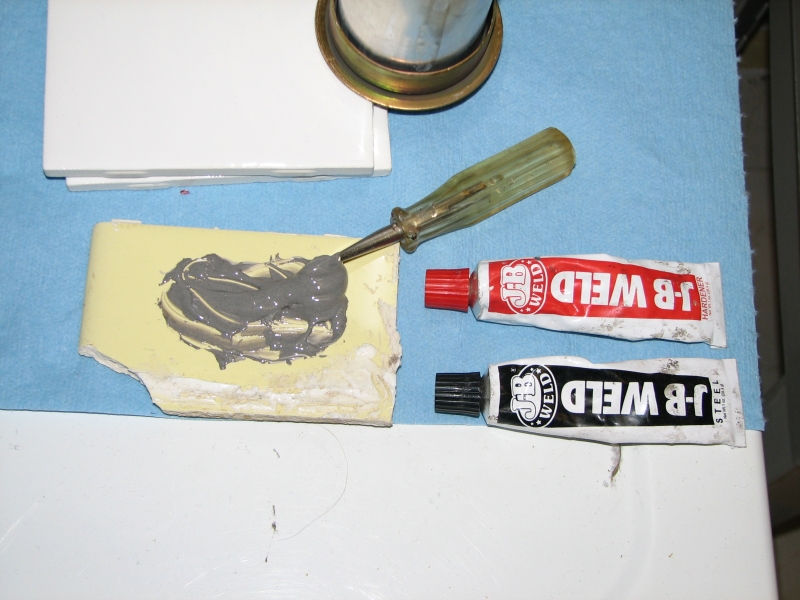

#39
Rennlist Member

................... Use a polymethylmethacrylate composite, it's used on airplanes where drilling or riviting would lessen the strength of the joined parts.
It's called Equilox by Center Forge. ........................George, ask some of the aircraft mechanics if they have Equilox, at the base. They should have. It's nasty stuff. You need stout rubber gloves, and a respirator. You'll tear the base metal before this stuff fails.
It's called Equilox by Center Forge. ........................George, ask some of the aircraft mechanics if they have Equilox, at the base. They should have. It's nasty stuff. You need stout rubber gloves, and a respirator. You'll tear the base metal before this stuff fails.
#40
Rennlist Member
#41
Rennlist Member
Thread Starter

Is this the company ?? ... http://www.centaurforge.com/Equilox/products/73/
Thanks for all the inputs and expertise... I plan on consulting the best local welder I can find to see what he thinks. Lots of considerations and pros/cons for each method... will keep you posted.
A DE weekend at VIR starts tomorrow, maybe it'll get my mind off it for a while.
#42
Three Wheelin'

In the Nuke here where I work we use Devcon products to repair pump bowls and impellers. After repairs are done on an impeller, I've seen the machinists having to use angle grinders to re-shape - its that hard.
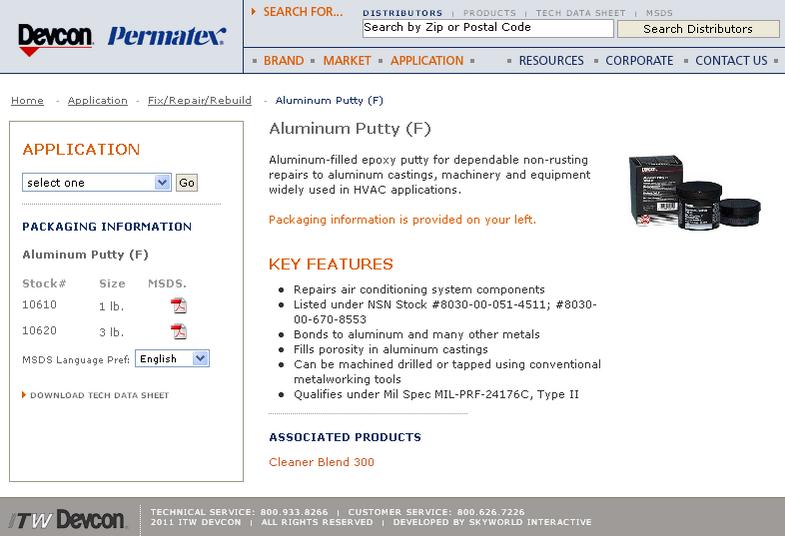
#43
Rennlist Member

George,
Here are pictures of my broken plug and repair. Pictures of broken piece aren't very clear, but you can see similar to your broken drain. Interestingly, the first Frenzy I went to in 2002, Marc Thomas of Devek fame was there, talked about this and he said it is not that uncommon.
I had 2 welders come and look at welding it, both did not think they had enough room to get a good weld all the way around the drain and didn't want to try and maybe make things worse.
Broken block:

This is what it looks like repaired 9 years later with JB Weld repair:


Of course, I don't pull that bolt out when doing WP replacement, just pull the driver side drain. Good luck in the repair, don't despair, it can be fixed in situ. Then when you need to refresh the whole engine after 300K miles or so, if it needs it, you can pull the engine and fix it properly, at least that is what I am thinking with mine.
Here are pictures of my broken plug and repair. Pictures of broken piece aren't very clear, but you can see similar to your broken drain. Interestingly, the first Frenzy I went to in 2002, Marc Thomas of Devek fame was there, talked about this and he said it is not that uncommon.
I had 2 welders come and look at welding it, both did not think they had enough room to get a good weld all the way around the drain and didn't want to try and maybe make things worse.
Broken block:

This is what it looks like repaired 9 years later with JB Weld repair:


Of course, I don't pull that bolt out when doing WP replacement, just pull the driver side drain. Good luck in the repair, don't despair, it can be fixed in situ. Then when you need to refresh the whole engine after 300K miles or so, if it needs it, you can pull the engine and fix it properly, at least that is what I am thinking with mine.
#44
Rest in Peace
Rennlist Member
Rennlist Member
Join Date: May 2006
Location: Bird lover in Sharpsburg
Posts: 9,903
Likes: 0
Received 2 Likes
on
2 Posts

In the Nuke here where I work we use Devcon products to repair pump bowls and impellers. After repairs are done on an impeller, I've seen the machinists having to use angle grinders to re-shape - its that hard.
Attachment 521209
Attachment 521209
#45

I know Mark and someone else have already said this, but it is very important to be patient and use the the regular JB weld, not the quick stuff. Also equally important is your surface prep. Make sure you are applying to a rough and very clean surface and JB weld is magical stuff.